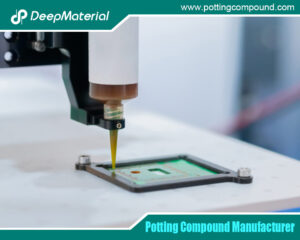

Silicone Potting Compound for Electronics
- Electronic Potting Material Manufacturer
- July 9, 2025
- Automotive potting material manufacturers, Benefits of Potting Electronics, Ceramic Potting Compound, Ceramic Potting Compound Manufacturer, china electronic potting silicone supplier, circuit board potting compound, conformal coating for electronics, conformal coating for pcb, conformal coating material, conformal coating silicone, conformal coating waterproof, Connector Potting Compound, Connector Potting Process, custom automated electronics potting, electrical potting compound, epoxy potting compound, polyurethane potting compound, potting compound for electronics, potting compound for pcb, potting compound vs epoxy, Silicone Potting Compound, silicone potting compound for electronics, silicone potting compound for electronics factory, silicone potting compound for electronics manufacturer, silicone potting compound for electronics market, silicone potting compound for electronics supplier, UV curing potting compound, waterproof potting compound
Silicone Potting Compound for Electronics
In the rapidly evolving world of electronics, ensuring the reliability, durability, and performance of electronic components is paramount. One critical solution that has gained widespread adoption in the industry is the use of silicone potting compounds. These versatile materials serve as protective encapsulants, safeguarding sensitive electronic assemblies from environmental stressors, mechanical damage, and electrical failures. This article explores the role of silicone potting compounds in electronics, delving into their properties, benefits, applications, types, and best practices for implementation.
What is a Silicone Potting Compound?
A silicone potting compound is a two-part or single-part material used to encapsulate or encase electronic components within a protective layer. Typically composed of a silicone resin and a curing agent, these compounds are applied in a liquid form and cure to form a solid, flexible, or semi-rigid barrier. The primary purpose of potting is to shield electronic assemblies from environmental factors such as moisture, dust, chemicals, and extreme temperatures, while also providing mechanical support and electrical insulation.
Silicone potting compounds are particularly favored in electronics due to their unique combination of flexibility, thermal stability, and dielectric properties. Unlike other potting materials like epoxy or polyurethane, silicone compounds offer superior elasticity and resistance to thermal cycling, making them ideal for applications where components are exposed to fluctuating temperatures or mechanical stress.
Why Use Silicone Potting Compounds in Electronics?
The use of silicone potting compounds in electronics is driven by their ability to enhance the longevity and reliability of electronic devices. Below are some of the key reasons why silicone is a preferred choice for potting applications:
- Environmental Protection
Electronics are often exposed to harsh environmental conditions, including humidity, water, dust, and corrosive chemicals. Silicone potting compounds create a hermetic seal around components, preventing ingress of moisture and contaminants that could lead to corrosion, short circuits, or component failure.
- Thermal Stability
Silicone potting compounds exhibit excellent thermal stability, maintaining their properties across a wide temperature range, typically from -50°C to 200°C or higher. This makes them suitable for electronics used in extreme environments, such as automotive, aerospace, and industrial applications.
- Electrical Insulation
With high dielectric strength, silicone potting compounds provide excellent electrical insulation, reducing the risk of electrical arcing or short circuits. This is particularly important for high-voltage applications or densely packed circuit boards.
- Mechanical Protection
Silicone’s inherent flexibility and vibration-dampening properties protect delicate components from mechanical shock, vibration, and impact. This is critical in applications like automotive electronics, where components are subjected to constant movement and stress.
- Chemical Resistance
Silicone potting compounds resist a wide range of chemicals, including oils, solvents, and acids, ensuring that encapsulated electronics remain protected in chemically aggressive environments.
- Ease of Application
Silicone potting compounds are available in various formulations, including low-viscosity options that flow easily into complex assemblies and high-viscosity options for more controlled applications. They can be cured at room temperature or with heat, offering flexibility in manufacturing processes.
Applications of Silicone Potting Compounds in Electronics
Silicone potting compounds are used across a diverse range of industries and applications due to their versatility. Some of the most common applications include:
- Automotive Electronics
Modern vehicles rely heavily on electronic control units (ECUs), sensors, and wiring harnesses. Silicone potting compounds protect these components from heat, moisture, and vibration, ensuring reliable performance in harsh automotive environments.
- Aerospace and Defense
In aerospace and defense applications, electronics must withstand extreme temperatures, high altitudes, and mechanical stress. Silicone potting compounds are used to encapsulate avionics, radar systems, and communication devices, providing robust protection against environmental challenges.
- Consumer Electronics
From smartphones to wearable devices, consumer electronics benefit from silicone potting for protection against water, dust, and drops. Silicone’s flexibility ensures that delicate components like circuit boards and connectors remain secure during everyday use.
- Industrial Electronics
Industrial control systems, sensors, and power supplies are often exposed to dust, chemicals, and temperature fluctuations. Silicone potting compounds enhance the durability of these components, reducing maintenance costs and downtime.
- LED Lighting
LEDs generate significant heat, and their longevity depends on effective thermal management. Silicone potting compounds are used to encapsulate LED modules, providing thermal conductivity and protection from moisture and UV exposure.
- Renewable Energy Systems
Solar inverters, wind turbine controllers, and battery management systems in renewable energy applications rely on silicone potting to ensure reliable operation in outdoor environments exposed to weather extremes.
Types of Silicone Potting Compounds
Silicone potting compounds are available in various formulations, each tailored to specific application requirements. The main types include:
- Addition-Cure Silicones
Addition-cure silicones, also known as platinum-cure silicones, cure through a chemical reaction between a base and a curing agent, typically catalyzed by platinum. These compounds offer excellent thermal stability, low shrinkage, and high purity, making them ideal for sensitive electronics. However, they are sensitive to contamination from certain chemicals, such as sulfur or amines, which can inhibit curing.
- Condensation-Cure Silicones
Condensation-cure silicones cure by reacting with moisture in the air, releasing byproducts like alcohol or acetic acid. These compounds are easier to handle and less sensitive to contamination but may have higher shrinkage and less thermal stability compared to addition-cure silicones.
- Thermally Conductive Silicones
For applications requiring efficient heat dissipation, thermally conductive silicone potting compounds are formulated with fillers like aluminum oxide or boron nitride. These compounds balance thermal conductivity with electrical insulation, making them suitable for power electronics and LEDs.
- Optically Clear Silicones
Optically clear silicone potting compounds are used in applications like LED encapsulation, where transparency is required. These compounds provide UV resistance and clarity while maintaining the protective properties of silicone.
- Flame-Retardant Silicones
For applications requiring compliance with fire safety standards, flame-retardant silicone potting compounds are formulated to meet UL 94 V-0 or similar certifications. These are commonly used in automotive, aerospace, and industrial electronics.
Key Properties of Silicone Potting Compounds
The effectiveness of silicone potting compounds in electronics stems from their unique physical and chemical properties. Below are some of the key characteristics:
- Flexibility and Elongation
Silicone potting compounds remain flexible even after curing, with elongation properties that allow them to absorb mechanical stress without cracking. This is particularly important for components subjected to thermal expansion and contraction.
- Dielectric Strength
With dielectric strengths typically ranging from 15 to 25 kV/mm, silicone potting compounds provide excellent insulation, preventing electrical failures in high-voltage applications.
- Thermal Conductivity
While silicone is not inherently as thermally conductive as some other materials, specialized formulations can achieve thermal conductivity values of 0.5 to 3 W/m·K, sufficient for many electronic applications.
- Low Outgassing
Silicone potting compounds exhibit low outgassing, meaning they release minimal volatile compounds during curing or operation. This is critical for aerospace and vacuum-sealed applications where outgassing could compromise performance.
- Adhesion
Silicone potting compounds can be formulated to adhere well to a variety of substrates, including metals, plastics, and ceramics, ensuring a secure bond in complex assemblies.
Considerations for Using Silicone Potting Compounds
While silicone potting compounds offer numerous advantages, there are several considerations to keep in mind to ensure optimal performance:
- Curing Time and Conditions
The curing process for silicone potting compounds varies depending on the formulation. Addition-cure silicones may require heat to accelerate curing, while condensation-cure silicones rely on ambient moisture. Manufacturers must balance curing time with production schedules to avoid delays.
- Compatibility with Components
Some electronic components, such as certain plastics or coatings, may be incompatible with silicone potting compounds, particularly condensation-cure formulations that release byproducts during curing. Compatibility testing is essential to prevent damage to sensitive components.
- Thermal Management
While silicone potting compounds offer good thermal stability, their thermal conductivity may not be sufficient for high-power applications. In such cases, thermally conductive fillers or alternative materials like epoxy may be considered.
- Cost
Silicone potting compounds are generally more expensive than epoxy or polyurethane alternatives. Manufacturers must weigh the cost against the performance benefits, particularly for high-volume production.
- Reworkability
Unlike some potting materials, silicone compounds are often reworkable, meaning they can be removed for repairs or modifications. However, this process can be labor-intensive and may require specialized tools or solvents.
Best Practices for Applying Silicone Potting Compounds
To maximize the benefits of silicone potting compounds, manufacturers should follow these best practices:
- Surface Preparation: Ensure that all surfaces are clean, dry, and free of contaminants like oils or dust to promote adhesion and prevent curing issues.
- Mixing and Dispensing: For two-part silicones, follow the manufacturer’s mixing ratio precisely to ensure proper curing. Use automated dispensing equipment for consistent application in high-volume production.
- Curing Conditions: Control temperature and humidity during curing to achieve optimal results. For heat-cured silicones, use ovens or heating systems to accelerate the process.
- Testing and Quality Control: Conduct thorough testing to verify the performance of potted assemblies under real-world conditions, including thermal cycling, humidity exposure, and mechanical stress.
- Safety Precautions: Handle silicone potting compounds in well-ventilated areas and follow safety guidelines to avoid skin or respiratory irritation, particularly with condensation-cure silicones that release byproducts.
Challenges and Alternatives
While silicone potting compounds are highly effective, they are not without challenges. Their higher cost and longer curing times compared to epoxy or polyurethane may be a drawback for some applications. Additionally, silicone’s lower thermal conductivity may limit its use in high-power electronics where heat dissipation is critical.
Alternatives to silicone potting compounds include:
- Epoxy Resins: Offer higher mechanical strength and thermal conductivity but are rigid and less resistant to thermal cycling.
- Polyurethane Compounds: Provide good flexibility and chemical resistance but may not match silicone’s thermal stability or dielectric properties.
- Parylene Coatings: Offer conformal coating for lightweight protection but lack the mechanical support provided by potting.
Future Trends in Silicone Potting Compounds
As electronics continue to evolve, so do the demands on potting materials. Emerging trends in silicone potting compounds include:
- Enhanced Thermal Conductivity: New formulations with advanced fillers are improving thermal performance to meet the needs of high-power electronics.
- Eco-Friendly Formulations: Manufacturers are developing silicone compounds with reduced environmental impact, including low-VOC (volatile organic compound) options.
- Smart Potting Materials: Research is underway to create silicone compounds with self-healing or conductive properties for next-generation electronics.
Conclusion
Silicone potting compounds play a vital role in protecting and enhancing the performance of electronic components across industries. Their unique combination of flexibility, thermal stability, electrical insulation, and environmental resistance makes them an ideal choice for a wide range of applications, from automotive and aerospace to consumer electronics and renewable energy systems. By understanding the properties, types, and best practices for using silicone potting compounds, manufacturers can ensure the reliability and longevity of their electronic products in even the most challenging environments. As technology advances, silicone potting compounds will continue to evolve, offering innovative solutions to meet the demands of tomorrow’s electronics.
For more about choosing the top silicone potting compound for electronics, you can pay a visit to DeepMaterial at https://www.pottingcompound.com/ for more info.
Recent Posts
- The Conformal Coating for Electronics
- Conformal Coating Spray
- UV Curing Potting Compound
- The Ultimate Guide to Electrical Potting Compound and Market Application
- The Top Polyurethane Potting Compound
- Advanced Epoxy Potting Compound for Superior Electronic Protection
- Waterproof Potting Compound: A Comprehensive Guide
- Silicone Potting Compound for Electronics
- Potting Compound vs. Epoxy: A Comprehensive Comparison
- Potting Compound for PCB
Tags
Related Posts
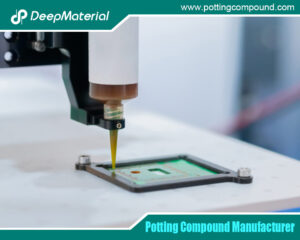
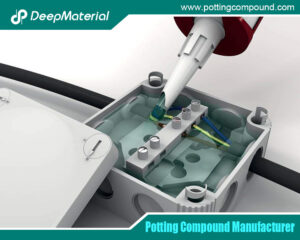
Conformal Coating Spray
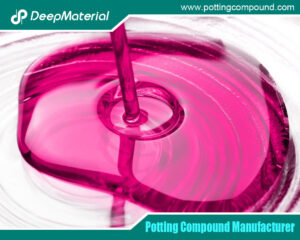
UV Curing Potting Compound
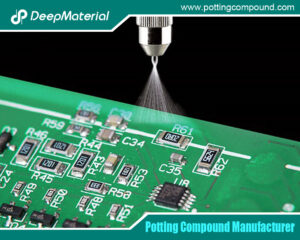
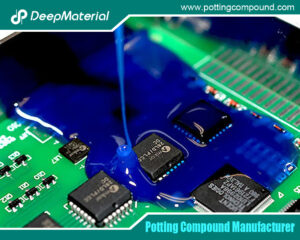
The Top Polyurethane Potting Compound
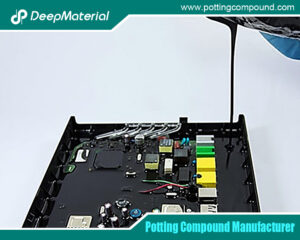