Acrylic Conformal Coating
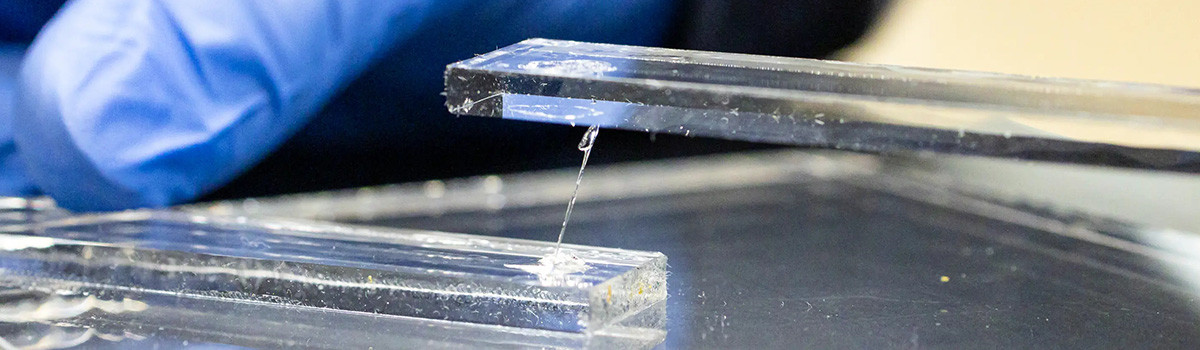
Acrylic conformal coatings protect electronic components, safeguarding them from environmental factors like moisture, dust, chemicals, and temperature extremes. These coatings are widely used in aerospace, automotive, consumer electronics, and telecommunications industries to enhance the reliability and longevity of sensitive electronic devices. Below are essential questions covering various aspects of acrylic conformal coatings, providing insights into their applications, benefits, selection criteria, and more.
Table of Contents
ToggleWhat is the acrylic conformal coating?
Acrylic conformal coating is a protective coating used in electronic applications to safeguard printed circuit boards (PCBs) and other sensitive electronic components from environmental factors such as moisture, dust, chemicals, and temperature extremes. It is applied thinly and evenly over the PCB’s surface to form a protective layer that conforms to the contours of the components.
Composed primarily of acrylic resin dissolved in a solvent, acrylic conformal coatings offer several advantages over other conformal coatings. One main advantage is their quick drying time, which helps expedite the manufacturing process. Additionally, acrylic coatings typically exhibit good adhesion to various substrates, including metals, plastics, and ceramics. They also provide excellent electrical insulation properties, ensuring the coated components remain electrically isolated and protected from short circuits.
Acrylic conformal coatings are available in various formulations to meet specific application requirements. Some formulations offer enhanced resistance to chemicals or high temperatures, while others provide improved flexibility or UV stability. This versatility makes acrylic coatings suitable for various industries, including automotive, aerospace, medical devices, and consumer electronics.
Application methods for acrylic conformal coatings include spraying, dipping, brushing, or selective coating using automated equipment. Regardless of the application method, proper surface preparation is essential to ensure optimal adhesion and performance of the layer. This may involve cleaning the PCB thoroughly to remove contaminants or residues before applying the coating.
Once applied, acrylic conformal coatings form a transparent protective barrier that helps extend the lifespan of electronic components and increase their reliability in harsh operating environments. Additionally, they offer ease of rework and repair, as they can be removed using solvents or mechanical means if necessary.
Acrylic conformal coating provides:
- Adequate protection for electronic assemblies.
- Offering benefits such as quick drying.
- Good adhesion.
- Electrical insulation.
- Versatility in formulation.
Its ability to safeguard PCBs against environmental hazards makes it an essential component in manufacturing reliable electronic devices.
How does acrylic conformal coating protect electronic components?
Acrylic conformal coating is a protective layer applied to electronic components to safeguard them against environmental hazards like moisture, dust, chemicals, and mechanical stress. Here’s how acrylic conformal coating works to protect electronic components:
- Moisture Barrier: One of the primary functions of acrylic conformal coating is to create a moisture barrier around the electronic components. Moisture can cause corrosion and short circuits in electronic circuits, leading to malfunction or failure. The acrylic coating forms a tight seal over the surface of the components, preventing moisture ingress and thus extending the lifespan of the device.
- Chemical Resistance: Acrylic coatings resist various chemicals, including solvents, oils, and cleaning agents. This chemical resistance protects the electronic components from damage or degradation when exposed to harsh environments or during cleaning processes.
- Insulation: Acrylic conformal coatings provide electrical insulation to the components they cover. This insulation prevents electrical shorts and arcing, which can occur due to the accumulation of conductive contaminants or moisture. Acrylic coatings ensure the reliable operation of electronic devices by maintaining proper insulation.
- Dust and Particle Protection: The conformal coating forms a smooth, uniform layer over the surface of the components, preventing the accumulation of dust, dirt, or other particles. Dust and debris can compromise the performance of electronic devices by obstructing airflow, causing overheating, or creating short circuits. Acrylic coatings mitigate these risks by sealing off vulnerable areas.
- Mechanical Protection: Acrylic conformal coatings also offer mechanical protection by providing a barrier against physical damage, such as scratches, abrasions, or impact. This protection is particularly crucial in applications where electronic components are subjected to handling, assembly, or transportation.
- UV Resistance: Some acrylic conformal coatings are formulated to resist ultraviolet (UV) radiation, which can degrade unprotected electronic components exposed to sunlight or UV-emitting sources over time. UV-resistant coatings help maintain the integrity and functionality of the components in outdoor or high-exposure environments.
Acrylic conformal coatings serve as a versatile and effective solution for protecting electronic components by forming a durable, moisture-resistant, chemically inert, electrically insulating, and mechanically robust barrier. This enhances the reliability and longevity of electronic devices in various operating conditions.
What are the primary applications of acrylic conformal coatings?
Acrylic conformal coatings find a wide array of applications across industries where protecting sensitive electronic components from environmental factors is paramount. Here are some primary applications:
- Electronics Industry: Acrylic conformal coatings are extensively used in the electronics industry to protect printed circuit boards (PCBs) from moisture, dust, chemicals, and other environmental contaminants. These coatings provide a protective barrier against corrosion and electrical shorts, extending the lifespan and reliability of electronic devices. They are commonly applied to PCBs in consumer electronics, automotive electronics, aerospace electronics, and industrial control systems.
- Automotive Electronics: With the increasing complexity of automotive electronic systems, the demand for reliable protection against harsh operating conditions is critical. Acrylic conformal coatings are applied to electronic control units (ECUs), sensors, and other components to safeguard them from temperature variations, vibrations, and exposure to chemicals such as fuels and lubricants.
- Aerospace and Defense: In aerospace and defense applications, where equipment operates in extreme conditions, including high altitudes, temperature variations, and exposure to moisture and chemicals, acrylic conformal coatings play a vital role in protecting electronic assemblies. They are used to coat avionics systems, navigation equipment, communication devices, and military-grade electronics, ensuring optimal performance and longevity in challenging environments.
- Medical Devices: Acrylic conformal coatings are utilized in medical devices to protect sensitive electronic components from bodily fluids, sterilization processes, and environmental contaminants. These coatings are critical for ensuring the reliability and safety of medical equipment such as patient monitors, diagnostic devices, and implantable devices.
- LED Lighting: In LED lighting applications, acrylic conformal coatings are applied to LED drivers and control circuitry to protect them from moisture, heat, and environmental contaminants. This protection is essential for maintaining the efficiency and longevity of LED lighting systems, especially in outdoor and industrial settings.
- Renewable Energy Systems: Acrylic conformal coatings are also used in renewable energy systems, such as solar inverters and wind turbine controllers, to protect electronic components from weather-related damage and ensure continuous operation in outdoor environments.
Acrylic conformal coatings serve as a critical protective layer in various industries. They safeguard electronic components and assemblies from a wide range of environmental challenges, thereby enhancing reliability, longevity, and performance.
What are the critical properties of acrylic conformal coatings?
Acrylic conformal coatings are widely used in electronic applications for protecting printed circuit boards (PCBs) and other sensitive electronic components from environmental factors such as moisture, dust, chemicals, and temperature variations. These coatings offer several fundamental properties that make them desirable for such applications:
- Dielectric Strength: Acrylic conformal coatings exhibit excellent dielectric strength, ensuring they can insulate electronic components effectively. This property is crucial for preventing electrical short circuits and maintaining the integrity of the circuitry.
- Moisture Resistance: Acrylic coatings provide a high level of moisture resistance, shielding electronic components from humidity and moisture ingress. This property is vital for maintaining the functionality and reliability of electronic devices, especially in harsh or outdoor environments.
- Chemical Resistance: Acrylic conformal coatings resist various chemicals, including solvents, fuels, and oils. This resistance helps protect PCBs and electronic components from corrosion and chemical damage, extending their lifespan and reliability.
- Flexibility: Acrylic coatings are known for their flexibility, allowing them to conform to the contours of PCBs and electronic assemblies. This property enables uniform coverage and ensures the coating adheres well to the substrate, even on complex or irregular surfaces.
- UV Stability: Many acrylic conformal coatings possess UV stability, meaning they can withstand prolonged exposure to ultraviolet (UV) radiation without degrading or becoming brittle. This property is essential for outdoor applications where exposure to sunlight is a concern.
- Ease of Application and Removal: Acrylic coatings are generally easy to apply using spraying, dipping, or brushing methods. They also offer good reworkability, allowing for straightforward removal and reapplication during PCB assembly or repair processes.
- Fast Curing Time: Acrylic conformal coatings typically have fast curing times, facilitating efficient production processes and reducing manufacturing lead times. Fast curing also helps minimize the risk of contamination during the coating process.
- Low Toxicity and Environmental Impact: Acrylic coatings are often preferred for their low toxicity and minimal environmental impact compared to some alternative coating materials, making them more environmentally friendly options for electronic applications.
Acrylic conformal coatings offer a combination of dielectric strength, moisture and chemical resistance, flexibility, UV stability, ease of application, and environmental considerations, making them well-suited for protecting electronic components in various demanding environments.
How does acrylic conformal coating differ from other types of conformal coatings?
Acrylic conformal coating is commonly used in electronics manufacturing to protect printed circuit boards (PCBs) and other electronic components from environmental factors such as moisture, dust, chemicals, and temperature fluctuations. It primarily differs from different types of conformal coatings, such as silicone, urethane, and epoxy, in its composition, properties, and application methods.
Composition: Acrylic conformal coatings are formulated from acrylic resins, polymer-based materials derived from acrylic acid or its derivatives. These resins provide excellent adhesion to various substrates, including metals, plastics, and ceramics. Acrylic coatings are typically solvent-based, although water-based formulations are also available, offering environmentally friendly options.
Properties: Acrylic conformal coatings offer several advantageous properties, including:
- Transparency: Acrylic coatings are generally transparent, allowing for easy inspection of PCBs after coating application. This property is crucial for troubleshooting and repair processes.
- Fast drying: Acrylic coatings typically dry relatively quickly, reducing production time and increasing throughput in manufacturing processes.
- Good electrical insulation: Acrylic coatings provide effective electrical insulation, helping to prevent short circuits and other electrical failures on PCBs.
- UV stability: Some acrylic formulations offer good resistance to ultraviolet (UV) light, which can benefit applications exposed to sunlight or other UV sources.
Application methods: Acrylic conformal coatings can be applied using various methods, including spray coating, dip coating, brush coating, and selective coating techniques. Spray coating is a popular method due to its efficiency and ability to achieve uniform coverage over complex PCB geometries. Dip coating is another standard method involving immersing PCBs into a bath of the coating material.
Acrylic conformal coatings offer a balance of properties suitable for many electronic applications, including consumer electronics, automotive electronics, aerospace, and industrial equipment. However, specific application requirements, such as environmental exposure, operating conditions, and regulatory standards, must be considered when selecting the appropriate conformal coating type.
What are the advantages of using acrylic conformal coatings?
Acrylic conformal coatings offer several advantages, making them a popular choice for protecting printed circuit boards (PCBs) and electronic components in various industries. These advantages include:
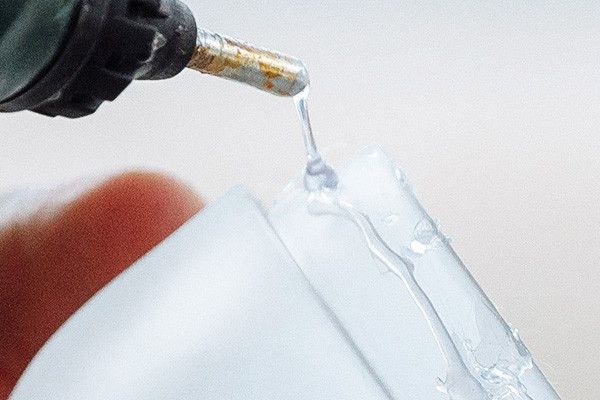
- Transparency: Acrylic coatings are typically transparent, allowing for easy visual inspection of PCBs after coating application. This transparency is crucial for quality control, troubleshooting, and maintenance purposes, as it enables technicians to detect defects or anomalies on the PCB surface.
- Fast curing: Acrylic conformal coatings generally cure relatively quickly compared to other coatings. Fast curing times reduce production cycle times, increase manufacturing throughput, and enable rapid assembly of electronic devices, ultimately leading to cost savings and improved efficiency.
- Good adhesion: Acrylic coatings exhibit excellent adhesion to various substrates, including metals, plastics, and ceramics. This strong adhesion ensures reliable protection for PCBs and electronic components, preventing delamination or detachment of the coating over time.
- Electrical insulation: Acrylic conformal coatings provide effective electrical insulation, helping to prevent short circuits and electrical failures on PCBs. Acrylic coatings contribute to the long-term reliability and performance of electronic devices by creating a barrier between conductive traces and environmental contaminants.
- Chemical resistance: Acrylic coatings resist various chemicals, including solvents, oils, and cleaning agents. This chemical resistance helps to protect PCBs and electronic components from damage or corrosion caused by exposure to harsh environmental conditions or contaminants.
- UV stability: Some acrylic formulations feature excellent UV stability, meaning they can withstand prolonged exposure to ultraviolet (UV) light without degrading or yellowing. UV stability is particularly beneficial for outdoor or high-UV environments, where electronic devices may be subjected to sunlight or other UV sources.
- Versatility: Acrylic conformal coatings are available in various formulations to suit different application requirements, such as solvent-based or water-based options, as well as different viscosity levels and curing mechanisms. This versatility allows manufacturers to select the most suitable acrylic coating for their specific needs, whether for high-volume production or specialized applications.
Overall, the advantages of acrylic conformal coatings, including transparency, fast curing, adhesion, electrical insulation, chemical resistance, UV stability, and versatility, make them a preferred choice for protecting electronic assemblies and ensuring their long-term reliability in diverse operating environments.
Are there any limitations or drawbacks associated with acrylic conformal coatings?
Acrylic conformal coatings offer several advantages in protecting electronic components but also have limitations and drawbacks that need consideration.
- Limited Chemical Resistance: Acrylic coatings may not provide sufficient protection against harsh chemicals or solvents. They can degrade or dissolve when exposed to certain chemicals, compromising their protective capabilities. This limitation restricts their use in environments where chemical exposure is expected.
- Thermal Stability: While acrylic coatings offer decent thermal resistance, they may not perform as well as other materials like silicone or polyurethane in extreme temperatures. High temperatures can cause acrylic coatings to soften or degrade, potentially leading to failure in critical applications.
- Mechanical Durability: Acrylic coatings may not offer the same level of mechanical durability as other conformal coatings. They can be relatively soft and prone to scratching or abrasion, which could expose underlying components to damage or environmental hazards.
- Moisture Resistance: Although acrylic coatings provide some moisture protection, they may not be as effective as other materials, such as silicone, in highly humid or wet environments. Prolonged exposure to moisture can lead to delamination or reduced effectiveness in preventing corrosion.
- UV Stability: Acrylic coatings may degrade when exposed to ultraviolet (UV) radiation over time. This limitation makes them less suitable for outdoor applications or environments where exposure to sunlight is frequent unless supplemented with UV stabilizers.
- Application Challenges: Acrylic coatings can be challenging to apply uniformly, especially on complex or three-dimensional surfaces. Achieving consistent coverage without air bubbles or voids may require specialized equipment or expertise, increasing application costs and complexity.
- Limited Thickness Range: Acrylic coatings typically have a relatively limited thickness range compared to other conformal coating materials. This limitation may restrict their effectiveness in providing adequate insulation or protection for specific electronic components, especially in high-voltage applications.
Despite these limitations, acrylic conformal coatings remain a popular choice for many electronic applications due to their affordability, ease of application, and satisfactory performance in less demanding environments. However, carefully considering these drawbacks is essential to ensure that the chosen coating meets the application’s specific requirements and environmental conditions.
What are the different methods of applying acrylic conformal coatings?
Acrylic conformal coatings are widely used in electronics to protect printed circuit boards (PCBs) and electronic components from environmental factors such as moisture, dust, chemicals, and temperature variations. Various methods can be employed to apply acrylic conformal coatings, each with its advantages and considerations:
- Brush Application: This is one of the simplest methods for manually brushing the coating onto the PCB surface. It offers precise control over the application, making it suitable for small-scale or intricate designs. However, it may result in uneven coating thickness and requires skilled labor for consistent results.
- Dipping: In this method, the PCB is submerged in a bath of liquid acrylic coating. The coating adheres to the entire surface, providing uniform coverage. Dipping is efficient for large-scale production but may require additional steps such as draining and curing. It’s crucial to control factors like viscosity and withdrawal speed to achieve the desired coating thickness and uniformity.
- Spraying: Acrylic coatings can be applied using spray equipment, such as airbrushes or automated spray systems. This method offers high throughput and uniform coverage, making it suitable for large volumes of PCBs. Adjusting spray parameters like pressure, nozzle size, and distance from the substrate is essential to ensure consistent coating thickness and quality.
- Selective Coating: Selective coating involves applying the acrylic conformal coating only to specific areas of the PCB, leaving other areas exposed. This can be achieved through various methods like masking, robotic dispensing, or precision spraying. Selective coating is ideal for shielding sensitive components from environmental stress while avoiding coating on areas like connectors or heatsinks.
- Roller Coating: The acrylic coating is applied using a roller, similar to painting walls. This method offers moderate throughput and can be suitable for specific applications where spraying or dipping may not be feasible. However, control is required to control the roller speed and pressure to achieve consistent coating thickness.
Regardless of the method chosen, proper surface preparation, curing, and inspection are essential for ensuring the effectiveness and reliability of acrylic conformal coatings in protecting electronic assemblies. Each application method has its own set of advantages and challenges, and the selection depends on factors like production volume, complexity of the PCB design, and desired coating properties.
How do you ensure proper adhesion of acrylic conformal coatings?
Ensuring proper adhesion of acrylic conformal coatings is crucial for effectively protecting electronic assemblies. Several key steps can be taken to enhance adhesion:
- Surface Preparation: Proper surface preparation is fundamental for promoting adhesion. The substrate should be clean, dry, and free from contaminants such as oils, dust, and residues. Techniques like solvent cleaning, mechanical abrasion, or plasma treatment can achieve a clean and receptive surface.
- Adhesion Promotion: Some substrates may require additional treatments to enhance adhesion. This can include adhesion promoters or primers designed explicitly for acrylic conformal coatings. These materials create a strong bond between the substrate and the coating, improving adhesion reliability.
- Optimizing Coating Formulation: The formulation of the acrylic conformal coating itself plays a significant role in adhesion. Factors such as the choice of monomers, additives, and cross-linking agents can influence adhesion properties. Formulating the coating with appropriate viscosity, surface tension, and compatibility with the substrate material can enhance adhesion.
- Curing Conditions: Proper curing of the acrylic coating is essential for achieving optimal adhesion. Following manufacturer recommendations regarding curing temperature, time, and humidity levels is crucial. Only complete curing can lead to good adhesion and compromised coating performance.
- Testing and Quality Control: Regular testing and quality control measures are essential for ensuring adhesion reliability. Various adhesion testing methods, such as tape tests, crosshatch adhesion tests, or pull-off adhesion tests, can be employed to evaluate the strength of the bond between the coating and the substrate. Performing these tests periodically during production helps identify any adhesion issues early on and allows for corrective actions to be taken.
By diligently implementing these steps, manufacturers can enhance the adhesion of acrylic conformal coatings, thereby improving the reliability and effectiveness of the protective coating on electronic assemblies.
What factors influence the curing time of acrylic conformal coatings?
The curing time of acrylic conformal coatings, used to protect electronic components from environmental factors, is influenced by several key factors:
- Temperature: Curing time is highly dependent on temperature. Higher temperatures generally accelerate the curing process, while lower temperatures slow it down. Most acrylic coatings have a recommended curing temperature range, and deviations from this range can significantly affect curing time.
- Humidity: Acrylic coatings can be moisture-cured, meaning they polymerize in the presence of moisture. Higher humidity levels can accelerate curing, while low humidity can slow it down. However, excessive moisture can lead to improper curing or defects in the coating.
- The thickness of the Coating: Thicker coatings require more time to cure than thinner coatings. This is because the curing process must penetrate through the entire thickness of the coating layer.
- Chemical Composition: The specific formulation of the acrylic coating, including the types and ratios of monomers, oligomers, and additives, can influence curing time. Some formulations may be designed for rapid curing, while others may prioritize other properties, such as flexibility or chemical resistance, which can affect curing kinetics.
- Presence of Catalysts or Accelerators: Certain additives can be incorporated into the coating formulation to accelerate the curing process. These additives may react with functional groups in the acrylic resin to promote cross-linking and polymerization, reducing curing time.
- Substrate Material: The material onto which the coating is applied can impact curing time. Porous or absorbent substrates may affect the solvent evaporation rate or moisture absorption, altering the curing kinetics of the coating.
- Application Method: The method used to apply the coating, such as spraying, dipping, or brushing, can affect curing time. Differences in coating thickness and coverage resulting from different application methods can influence how quickly the coating cures.
- Post-Cure Conditions: Some acrylic coatings may require post-cure processes, such as exposure to elevated temperatures or UV radiation, to achieve optimal properties and performance. The duration and conditions of post-cure can impact the overall curing time of the coating.
By understanding and controlling these factors, manufacturers can optimize the curing process to achieve the desired coating properties and performance for specific applications.
Can acrylic conformal coatings be removed or reworked?
Acrylic conformal coatings are widely used in electronic applications to protect printed circuit boards (PCBs) and other sensitive components from environmental factors such as moisture, dust, chemicals, and temperature extremes. While these coatings provide excellent protection, there are situations where removal or rework may be necessary.
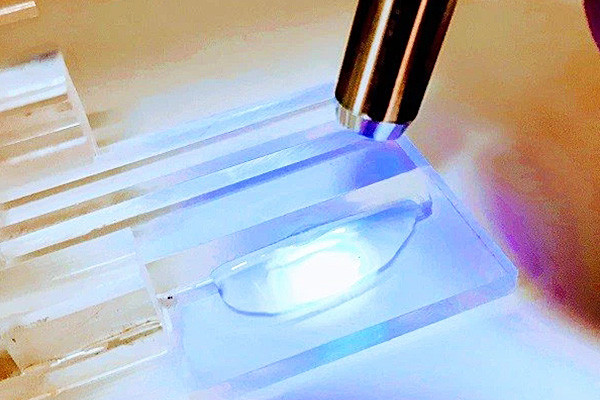
Removing acrylic conformal coatings can be challenging due to their durable nature and strong adhesion to surfaces. However, several methods can be employed for removal or rework:
- Chemical Stripping: Chemical strippers specifically formulated for acrylic coatings can soften and dissolve the coating, making removing it easier. These strippers typically contain solvents such as acetone or methylene chloride. Care must be taken to ensure compatibility with the substrate material and to follow safety guidelines when handling these chemicals.
- Mechanical Abrasion: Mechanical methods such as scraping, sanding, or grinding can physically remove the coating. However, this approach requires caution to avoid damaging the underlying components or substrate.
- Thermal Methods: Heat can soften acrylic coatings, making peeling or scraping easier. Heat guns or infrared heaters can be used for localized heating, but care must be taken to avoid overheating sensitive components.
- Laser Ablation: Laser systems can selectively remove acrylic coatings with precision, leaving underlying components intact. This method suits delicate components and complex geometries but may require specialized equipment.
- Solvent Swelling: Immersing the coated substrate in a solvent that swells the acrylic coating can facilitate its removal. However, this method may only be suitable for some substrates and can be time-consuming.
- Combination Approaches: Often, a combination of methods may be necessary for effective coating removal, especially for thick or stubborn coatings.
Considering the potential impact on the substrate and components during coating removal or rework is essential. Careful planning, proper equipment, and adherence to safety protocols are necessary to ensure successful outcomes and prevent damage to electronic assemblies. Additionally, consulting with coating manufacturers or experts can provide valuable guidance on the most suitable removal methods for specific applications.
Are acrylic conformal coatings suitable for high-temperature applications?
Acrylic conformal coatings are commonly used in electronic applications to protect circuit boards and components from environmental factors such as moisture, dust, chemicals, and debris. However, their suitability for high-temperature applications depends on various factors.
Acrylic coatings typically have a temperature resistance range of -40°C to 125°C (-40°F to 257°F), making them suitable for many standard operating conditions. However, they may not be the best choice for high-temperature applications exceeding this range.
When exposed to elevated temperatures, acrylic coatings can undergo thermal degradation, resulting in softening, loss of adhesion, discoloration, and even complete failure. Thus, acrylic coatings may not provide adequate protection for applications where temperatures regularly exceed the specified range, such as automotive under-hood environments, aerospace systems, or industrial machinery subjected to high-temperature processes.
In such cases, silicone or epoxy conformal coatings are often preferred due to their higher temperature resistance. Silicone coatings can withstand temperatures ranging from -55°C to 200°C (-67°F to 392°F), while epoxy coatings offer even more excellent resistance, with some formulations capable of withstanding temperatures up to 200°C to 250°C (392°F to 482°F).
However, the application’s temperature requirements fall within the operating range of acrylic coatings. In that case, they can offer several advantages, including ease of application, fast curing times, good adhesion to various substrates, and excellent dielectric properties.
Before selecting a conformal coating material, it’s essential to thoroughly assess the environmental conditions, including temperature ranges, humidity levels, chemical exposure, and mechanical stresses. Additionally, considering cost, availability, and compatibility with the specific substrate and manufacturing process is crucial in determining the most suitable coating for a particular application.
While acrylic conformal coatings offer adequate protection for electronics in many standard operating conditions, they may not be suitable for high-temperature applications exceeding their specified temperature range. In such cases, silicone or epoxy coatings should be considered for their superior temperature resistance properties.
How do acrylic conformal coatings resist moisture and environmental contaminants?
Acrylic conformal coatings are widely used in electronic applications to protect printed circuit boards (PCBs) and other sensitive components from moisture and environmental contaminants. These coatings offer several mechanisms to resist such threats.
Firstly, acrylic conformal coatings form a physical barrier over the surface of the PCB, creating a shield against moisture and contaminants. The coating material is typically applied in thin layers that adhere tightly to the substrate, sealing exposed areas such as solder joints, traces, and components. This barrier prevents moisture ingress, which could otherwise lead to corrosion, electrical shorts, or degradation of the electronic components.
Secondly, acrylic coatings possess excellent adhesion properties, ensuring they adhere firmly to the substrate even under harsh environmental conditions. This adhesion helps maintain the integrity of the protective barrier over time, reducing the risk of delamination or cracking that could compromise the coating’s effectiveness.
Additionally, acrylic conformal coatings often contain additives that enhance their resistance to moisture and contaminants. These additives may include hydrophobic compounds, which repel water and prevent it from penetrating the coating. Some formulations also incorporate UV stabilizers to protect against damage from exposure to sunlight, which can degrade the coating over time.
Furthermore, acrylic coatings can be formulated with high dielectric strength, which helps to maintain electrical insulation properties even in humid environments. This property is crucial for electronic devices operating in diverse conditions, where maintaining proper insulation is essential for reliable performance and safety.
Acrylic conformal coatings offer a combination of physical barrier properties, adhesion strength, and chemical resistance to protect electronic components from moisture and environmental contaminants. By forming a durable and reliable shield, these coatings help extend the lifespan and reliability of electronic devices in a wide range of applications.
What testing standards are used to evaluate the performance of acrylic conformal coatings?
Several testing standards are commonly used to evaluate the performance of acrylic conformal coatings, ensuring they meet the necessary quality and reliability requirements. These standards include coating thickness, adhesion, chemical resistance, electrical properties, and thermal endurance. Here are some essential standards:
- Thickness Measurement: ASTM D1003 outlines procedures for measuring the dry film thickness of organic coatings on metal substrates using magnetic and eddy current principles. This standard ensures that the coating meets specified thickness requirements for adequate protection.
- Adhesion Testing: ASTM D3359 provides methods for assessing the adhesion of coatings by conducting tape tests. It evaluates the ability of the coating to adhere to the substrate under stress, ensuring that the coating remains intact and does not peel off prematurely.
- Chemical Resistance: ASTM D1308 evaluates the resistance of coatings to various chemicals by exposing them to specific solutions and assessing any changes in appearance, weight, or other properties. This test helps determine the coating’s ability to withstand common contaminants.
- Electrical Properties: ASTM D257 outlines procedures for measuring electrical insulating materials’ volume and surface resistivity, including conformal coatings. These tests ensure that the coating provides adequate insulation and does not interfere with the electrical performance of electronic components.
- Thermal Endurance: ASTM D522 outlines methods for assessing the flexibility and adhesion of thin films, including conformal coatings, after exposure to elevated temperatures. This test helps evaluate the coating’s ability to withstand thermal cycling and other operational stressors.
- Salt Spray Testing: ASTM B117 is commonly used to assess the corrosion resistance of coatings by subjecting samples to a salt spray environment. While not specific to acrylic conformal coatings, it provides valuable insights into their protective properties against corrosion.
These standards provide a comprehensive framework for evaluating the performance of acrylic conformal coatings, ensuring they meet industry requirements for reliability, durability, and protection of electronic components in various applications. Compliance with these standards helps manufacturers guarantee the quality and consistency of their products.
What are the considerations for selecting the suitable acrylic conformal coating for a specific application?
Selecting the appropriate acrylic conformal coating for a specific application involves considering several factors to ensure optimal performance and compatibility. Here are key considerations:
- Environmental Conditions: Evaluate the operating environment, including temperature extremes, humidity levels, chemical exposure, and potential contaminants. Choose a coating that offers suitable protection against these factors to prevent degradation or malfunction of the coated components.
- Substrate Compatibility: Assess the material composition of the substrates to be coated. Ensure the acrylic coating is compatible with the materials to prevent adhesion issues, delamination, or component damage.
- Application Method: Consider the application method (spraying, brushing, or dipping) and ensure the selected coating can be applied effectively using the chosen method. Some coatings may require specialized equipment or techniques for application.
- Thickness Requirements: Determine the desired thickness of the coating based on the level of protection needed and the application’s specifications. Some acrylic coatings can be applied in varying thicknesses to accommodate different protection levels.
- Curing Method: Understand the curing process of the acrylic coating, whether it requires air drying, heat curing, or UV curing. Ensure the curing method aligns with the manufacturing process and timeframe of the application.
- Electrical Properties: If the coated components are electrical or electronic, consider the electrical insulation properties of the acrylic coating. Choose a coating with appropriate dielectric strength and insulation resistance to prevent electrical failures.
- Regulatory Compliance: Verify that the selected acrylic coating complies with relevant industry standards and regulations such as RoHS (Restriction of Hazardous Substances) and REACH (Registration, Evaluation, Authorization, and Restriction of Chemicals) to ensure safety and environmental compliance.
- Maintenance and Repair: Consider the coated components’ ease of maintenance and repair. Select a coating that allows for easy rework or repair if necessary without compromising the integrity of the coating or underlying substrate.
By carefully considering these factors, you can select the suitable acrylic conformal coating that provides optimal protection and performance for your application.
Can acrylic conformal coatings be customized for specialized requirements?
Acrylic conformal coatings, widely used in electronics manufacturing to protect printed circuit boards (PCBs) from environmental factors, can indeed be customized to meet specialized requirements. These coatings offer numerous advantages, such as moisture and chemical resistance, insulation, and protection against dust and debris. Customization allows for tailoring these properties to specific needs, ensuring optimal performance in diverse applications.
One standard customization is altering the thickness of the coating. Thicker coatings provide increased protection against harsh environments but may affect heat dissipation or interfere with component functionality. Thinner coatings offer lighter weight and less impact on thermal management but may sacrifice some protection. Understanding the balance between safety and functionality is crucial in customization.
Moreover, the composition of acrylic coatings can be adjusted to enhance specific properties. Additives can be incorporated to improve adhesion, flexibility, or UV resistance. For instance, if the application involves outdoor exposure, UV stabilizers can be added to prevent degradation due to sunlight exposure. Similarly, adhesion promoters can be included to ensure strong bonding to various substrates, enhancing the coating’s reliability in challenging conditions.
Furthermore, specialized requirements may demand unique formulations to meet regulatory standards. For instance, coatings used in aerospace or medical devices may need to comply with stringent regulations for safety and environmental impact. Custom formulations can ensure adherence to these standards while maintaining desired performance characteristics.
Color customization is another aspect that can be tailored to meet aesthetic or functional preferences. Different colors may facilitate visual inspection or identification of components on the PCB. Additionally, fluorescence or phosphorescence can be incorporated for applications requiring low-light visibility.
AcrylicAcrylic conformal coatings offer significant customization flexibility to meet specialized requirements. Whether it’s adjusting thickness, modifying composition for specific properties, ensuring regulatory compliance, or incorporating unique visual features, customization allows manufacturers to optimize performance and effectively meet the demands of diverse applications.
How do acrylic conformal coatings impact the electrical properties of coated components?
Acrylic conformal coatings can impact the electrical properties of coated components in several ways, both positively and negatively. Understanding these effects is crucial for ensuring the reliability and functionality of electronic devices. Here are some ways acrylic conformal coatings can influence electrical properties:
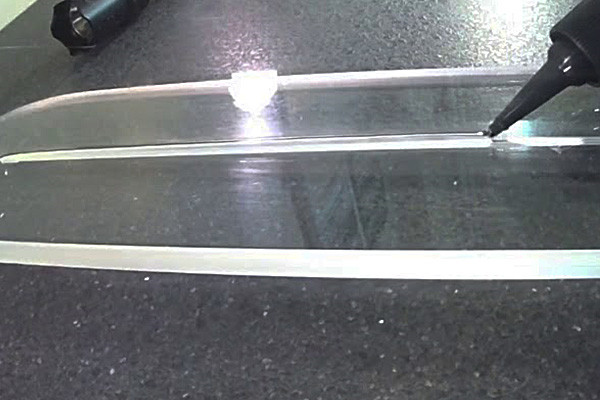
- Insulation:One of the primary functions of conformal coatings is to provide electrical insulation. Acrylic coatings create a barrier between conductive elements on the PCB, preventing electrical leakage or short circuits due to moisture, dust, or other contaminants. This insulation helps maintain proper electrical performance and prevents malfunctions or failures.
- Dielectric Properties:Acrylic coatings typically have good dielectric properties, meaning they can withstand high voltages without conducting electricity. This property is essential for maintaining electrical integrity, especially in high-voltage applications. However, it’s necessary to maintain its dielectric strength to keep the coating intact and free from defects.
- Capacitance:Acrylic coatings can affect the capacitance of components on the PCB. Capacitance is the ability of a system to store electrical energy in an electric field. While acrylic coatings have low capacitance, the coating between conductive traces or components can alter the overall capacitance of the circuit. This effect is typically minimal but may be a consideration in high-frequency or high-precision applications.
- Resistance:Acrylic coatings can introduce resistance to the electrical path. While this resistance is usually low, it can affect the performance of sensitive circuits, especially those requiring precise voltage or current levels. Proper selection of coating thickness and formulation can mitigate any adverse effects on resistance.
- Temperature Stability:Some acrylic coatings may exhibit changes in electrical properties with temperature variations. Thermal expansion and contraction can impact the coating’s integrity and interaction with the underlying components, potentially affecting electrical performance. Choosing coatings with good temperature stability can minimize these effects.
While acrylic conformal coatings provide valuable protection for electronic components, their application can introduce subtle changes to electrical properties. Understanding these effects and selecting appropriate coating materials and application methods are essential for maintaining the desired electrical performance of coated components.
Are there any environmental or regulatory considerations when using acrylic conformal coatings?
When using acrylic conformal coatings, several environmental and regulatory considerations come into play, primarily due to the potential impact of the chemicals involved on human health and the environment. Acrylic conformal coatings are commonly used in electronics manufacturing to protect printed circuit boards (PCBs) from environmental factors such as moisture, dust, and chemicals. However, their application and disposal can pose risks if not managed properly.
- Chemical Composition: Acrylic conformal coatings typically contain volatile organic compounds (VOCs) and other hazardous chemicals. VOCs contribute to air pollution and can have adverse health effects on humans, such as respiratory issues and neurological problems. Regulatory agencies often have limits on VOC emissions, requiring companies to monitor and control their release.
- Air Quality and Emissions: Applying acrylic conformal coatings can release VOCs into the air, impacting indoor and outdoor air quality. Manufacturers must adhere to regulations regarding emissions during application processes to minimize environmental contamination and health risks to workers and nearby communities.
- Waste Management: Proper disposal of waste materials, including unused coating, cleaning solvents, and contaminated materials, is crucial to prevent environmental contamination. Regulatory guidelines govern hazardous waste disposal, necessitating proper labeling, storage, and disposal methods to minimize the risk of pollution and harm to ecosystems.
- Worker Safety: Workers involved in applying and handling acrylic conformal coatings must be trained in safety protocols to reduce exposure to harmful chemicals. This includes proper ventilation, personal protective equipment (PPE), spill cleanup, and emergency response procedures.
- Regulatory Compliance: Various regulatory frameworks, such as REACH (Registration, Evaluation, Authorization, and Restriction of Chemicals) in the European Union and similar regulations in other regions, impose restrictions on the use of certain chemicals and require companies to assess and mitigate the risks associated with their products.
When using acrylic conformal coatings, it is essential to consider the chemical composition, air emissions, waste management, worker safety, and regulatory compliance to minimize adverse impacts on human health and the environment. Adhering to best practices and regulatory requirements ensures the responsible use of these coatings while protecting both people and the planet.
What are some standard troubleshooting issues encountered with acrylic conformal coatings?
Several common troubleshooting issues may arise when working with acrylic conformal coatings in electronics manufacturing. Addressing these issues promptly is crucial to ensure the reliability and effectiveness of the protective coating on printed circuit boards (PCBs). Here are some typical problems and their potential causes:
- Incomplete Coverage: One common issue is inadequate coverage of the PCB surface, leaving areas vulnerable to environmental damage. This problem may occur due to improper application techniques, such as uneven spraying or insufficient coating thickness. It can also result from contaminants on the PCB surface, preventing proper coating adhesion adhesion.
- Blushing or Hazing: Blushing or hazing refers to the formation of a cloudy or milky appearance on the coated surface, which can compromise the aesthetics and functionality of the PCB. This issue often arises when the coating is applied in high humidity or improper temperatures. Moisture trapped within the coating during curing can cause this effect.
- Delamination occurs when the conformal coating separates from the PCB surface, compromising its protective properties. Factors contributing to delamination include inadequate surface preparation, incompatible materials, or improper curing conditions. Insufficient adhesion between the coating and the substrate is typically the root cause.
- Cracking or Peeling: Cracking or peeling of the conformal coating can occur over time, especially when exposed to thermal cycling or mechanical stress. This issue may stem from using a coating with inadequate flexibility for the application requirements, applying the coating too thickly, or subjecting the coated PCB to extreme temperatures or physical strain.
- Electrical Failure: In some cases, applying conformal coatings can lead to unintended electrical problems, such as short circuits or insulation breakdown. These issues may arise from coating material inadvertently bridging conductive paths on the PCB, inadequate coverage around sensitive components, or improper curing causing electrical leakage paths.
Addressing these troubleshooting issues often requires a combination of careful process optimization, adherence to manufacturer recommendations, and thorough quality control measures during application and curing. Proper personnel training and regular equipment maintenance can also help mitigate these challenges and ensure the reliable performance of acrylic conformal coatings in electronics applications.
What future trends are expected in developing and using acrylic conformal coatings?
As technology advances and environmental concerns become increasingly significant, several future trends are expected to shape the development and use of acrylic conformal coatings in electronics manufacturing:
- Environmentally Friendly Formulations: A significant trend in developing acrylic conformal coatings is the formulation of environmentally friendly alternatives with reduced or eliminated volatile organic compounds (VOCs) and hazardous chemicals. Manufacturers are exploring eco-friendly solvent-based formulations or switching to water-based coatings to minimize environmental impact and comply with stricter regulations.
- Enhanced Performance Characteristics: Future acrylic conformal coatings will likely exhibit improved performance characteristics, such as higher resistance to temperature extremes, better chemical resistance, and enhanced mechanical durability. These advancements will cater to the evolving demands of modern electronic devices operating in harsh environments, such as automotive, aerospace, and industrial applications.
- Nanotechnology Integration: Nanotechnology holds promise for enhancing the properties of acrylic conformal coatings by incorporating nanoparticles for improved barrier properties, increased scratch resistance, and better adhesion to diverse substrates. Nanocomposite coatings can offer superior protection against moisture, corrosion, and other environmental factors while maintaining thin film thickness.
- Self-Healing Coatings: Researchers are exploring the development of self-healing acrylic conformal coatings capable of autonomously repairing minor damage or scratches incurred during service life. These coatings utilize microcapsules or molecular-level mechanisms to release healing agents when damage occurs, extending the lifespan of coated electronic components and reducing maintenance requirements.
- Smart Coating Technologies: Integrating innovative functionalities into acrylic conformal coatings is anticipated, allowing for features such as sensing, self-cleaning, or antimicrobial properties. Intelligent coatings can provide additional value by enabling real-time monitoring of environmental conditions or enhancing the longevity and reliability of electronic assemblies.
- Application Innovations: Advanced application technologies, such as selective coating techniques using robotic dispensing or jetting systems, are expected to streamline the coating process, improve accuracy, and reduce material waste. Automated inspection and quality control systems will ensure uniform coating coverage and detect defects.
Future trends in acrylic conformal coatings will focus on achieving higher performance, environmental sustainability, and innovative functionalities to meet the evolving needs of the electronics industry while complying with regulatory requirements.
Conclusion:
Acrylic conformal coatings safeguard electronic components from various environmental stressors, ensuring their reliability and longevity in diverse applications. Understanding their properties, applications, and selection criteria is vital for engineers and manufacturers aiming to enhance the performance and durability of electronic devices. As technology advances, acrylic conformal coatings are likely to evolve further, meeting the growing demands of industries while maintaining compatibility with environmental regulations and emerging trends.
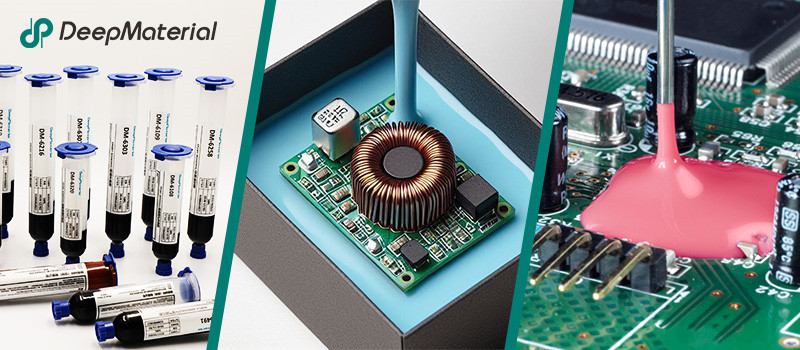
About DeepMaterial
DeepMaterial is a trusted supplier of encapsulant materials that are used in electronics manufacturing worldwide. From chip on board encapsulants such as glob top material to conformal coatings, underfills, low pressure molding, and potting solutions, DeepMaterial offers a full range of circuit board protection materials that effectively protect circuit boards while help reduce costs. More…Deepmaterial is a the manufacturer of epoxy adhesives including hardeners, metalbond, and metal filled resins. Structural, toughened medium viscosity, and non-sag adhesives are also offered. Some adhesives are resistant to thermal shock, chemical, vibration dampening, and impact. Suitable for metals, plastics, wood, and ceramics. Serves electronics, aerospace, automotive, tooling, marine, and construction industries. REACH and RoHS compliant. FDA approved. UL listed. Meets military specifications. We are the one of best adhesive manufacturers in China.
Blogs & News
Potting compounds are at the frontline of electronics assembly, delivering effective protection in challenging environmental conditions while improving mechanical strength and offering high electric insulation. Used within a variety of industries, electrical potting compounds are found within a broad range of consumer electronics, as well as used in applications across the automotive, aerospace, and other industries where electronic assemblies are prevalent.
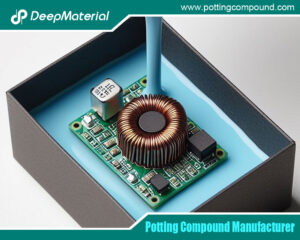
Potting Compound vs. Epoxy: A Comprehensive Comparison
Potting Compound vs. Epoxy: A Comprehensive Comparison In the world of electronics, manufacturing, and material encapsulation, two terms frequently come up: potting compounds and epoxy.
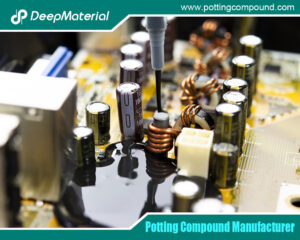
Potting Compound for PCB
Potting Compound for PCB A potting compound is a liquid or semi-liquid material that is poured or injected over a PCB or electronic assembly, then
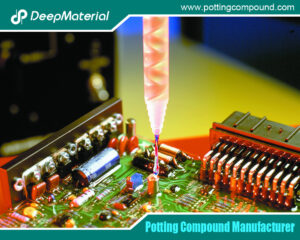
In – depth Analysis of the Curing Characteristics of Electronic Potting Compounds
In – depth Analysis of the Curing Characteristics of Electronic Potting Compounds Electronic potting compounds play a vital role in the electronics industry. They can
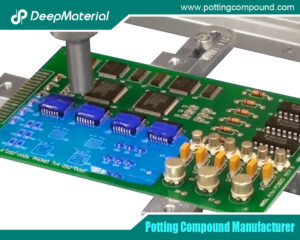
A Comprehensive Analysis of the Environmental Performance of Encapsulating Materials: From Regulations to Practices
A Comprehensive Analysis of the Environmental Performance of Encapsulating Materials: From Regulations to Practices In modern industrial manufacturing, encapsulating materials are widely used in numerous

A Comprehensive Analysis of PCB Encapsulation Quality Inspection: Innovative Application of Non-Destructive Testing Technologies
A Comprehensive Analysis of PCB Encapsulation Quality Inspection: Innovative Application of Non-Destructive Testing Technologies In the field of electronic manufacturing, the encapsulation process of printed
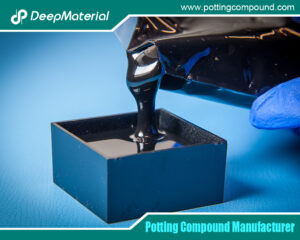
Analysis of the Improvement of the Seismic and Impact Resistance Performance of PCB by Encapsulation
Analysis of the Improvement of the Seismic and Impact Resistance Performance of PCB by Encapsulation During the operation of electronic devices, the PCB (Printed Circuit