Conformal Coating
In the world of electronics, where functionality and durability are paramount, one often encounters the term “Conformal Coating.” This seemingly simple solution holds the power to protect delicate electronic components from harsh environments, ensuring their longevity and reliability. However, delving deeper, one realizes there’s much more to this coating than meets the eye. In this comprehensive blog post, we’ll explore the intricacies of conformal coating, its applications, benefits, and everything in between.
Table of Contents
ToggleWhat Exactly is Conformal Coating and How Does it Work?
Electronic circuitry is covered with a conformal coating layer to protect it from external elements like moisture, dust, chemicals, and temperature changes. This thin film adheres to the contours of the electronic components, providing a barrier against potential damage. Its purpose is to extend the lifespan and reliability of electronics, particularly in harsh operating conditions.
Conformal coating involves various methods, including spraying, dipping, brushing, or selective coating. Each method offers distinct advantages based on the complexity of the circuitry, the desired level of protection, and cost considerations. Regardless of the application method, the coating material must be carefully chosen to assure compatibility with the specific components and environmental factors.
Silicone, acrylic, epoxy, and polyurethane are common materials used for conformal coating due to their excellent protective properties and compatibility with diverse substrates.
Once applied, the conformal coating forms a uniform layer over the electronic assembly, conforming to the shape of the components and creating a protective barrier. This barrier shields the circuitry from moisture, preventing corrosion and short circuits. Additionally, it insulates the components, reducing the risk of electrical arcing and improving reliability.
One key benefit of conformal coating is its ability to enhance the durability of electronics in challenging environments. Whether exposed to extreme temperatures, humidity, or chemical contaminants, coated circuitry is better equipped to withstand harsh conditions without compromising performance. It makes conformal coating indispensable in the automotive, aerospace, medical devices, and industrial automation industries.
Furthermore, conformal coating can also provide mechanical reinforcement to delicate components, reducing the likelihood of damage from vibration or mechanical shock. By encapsulating the circuitry in a protective layer, the coating helps prevent physical stress on the components, contributing to overall reliability and longevity.
However, while conformal coating offers significant advantages in terms of protection and reliability, proper application is crucial to ensure optimal performance. Factors such as coating thickness, curing time, and uniformity must be carefully controlled to avoid such problems as incomplete coverage, uneven coating, or delamination.
Why is Conformal Coating Crucial in Electronic Applications?
In electronic applications, one crucial yet often overlooked aspect is conformal coating. Particularly in harsh settings, this protective layer is essential to the durability and dependability of electronic equipment. Let’s examine the necessity of conformal coating in more detail.
Protection Against Environmental Factors:
- Conformal coatings shield electronic components from environmental factors such as moisture, dust, chemicals, and temperature variations.
- Moisture ingress can lead to corrosion, short circuits, and malfunctions, which conformal coatings effectively mitigate.
Enhanced Durability:
- By encapsulating delicate electronic components, conformal coatings provide an additional layer of durability, safeguarding against physical damage and vibration.
- This durability is vital in applications subjected to rough handling or high-stress environments.
Insulation and Dielectric Properties:
- Conformal coatings possess excellent insulation properties, which are crucial for preventing electrical leakage and short circuits.
- They also offer high dielectric strength, maintaining electrical integrity and preventing signal interference.
Chemical Resistance:
- Many electronic applications encounter exposure to various chemicals, including solvents, fuels, and cleaning agents. Conformal coatings offer resistance against such chemical exposures, ensuring sustained performance.
- Chemical resistance is especially critical in industrial and automotive applications where harsh substances are prevalent.
Facilitating Miniaturization:
- As electronic devices shrink in size, conformal coatings play a pivotal role in enabling miniaturization.
- They allow for closer component spacing by protecting against short circuits in confined spaces, facilitating compact designs without compromising reliability.
Temperature Stability:
- Electronic components are often exposed to various temperatures, from extreme cold to high heat. Conformal coatings provide thermal stability, protecting components from thermal shock and ensuring consistent performance across temperature variations.
Compliance with Regulatory Standards:
- Adherence to regulatory standards regarding environmental protection and safety is mandatory in many industries. They achieve this through their ability to provide a barrier.
What Are the Different Types of Conformal Coating Available?
Conformal coating protects electronic components from environmental factors such as moisture, dust, chemicals, and temperature fluctuations. It forms a protective layer over the circuitry, ensuring longevity and reliability. However, there is more than one-size-fits-all solution for conformal coatings. Different types cater to different needs and specifications. Let’s delve into the various types of conformal coatings available:
1. Acrylic Conformal Coating
Description: Acrylic conformal coatings are widely used for their versatility and cost-effectiveness. They provide excellent moisture and abrasion resistance, making them suitable for various applications.
Advantages:
Good moisture protection.
- Easy to apply and rework.
- Fast drying time.
- UV resistance.
Applications: This product is ideal for consumer electronics, automotive electronics, and LED lighting applications.
2. Silicone Conformal Coating
Description: Silicone conformal coatings offer exceptional flexibility and high-temperature resistance. They maintain their properties over various temperatures, making them suitable for harsh environments.
Advantages:
- Excellent thermal stability.
- High flexibility.
- Chemical resistance.
- Understand extreme temperatures.
Applications: These industries encompass aerospace, automotive, marine, and industrial electronics.
3. Urethane Conformal Coating
Description: Urethane conformal coatings provide superior protection against chemicals, solvents, and abrasion. They offer excellent dielectric properties and mechanical strength.
Advantages:
- Chemical resistance.
- Excellent adhesion.
- Abrasion resistance.
- High dielectric strength.
Applications: These encompass military and aerospace electronics, automotive control systems, and harsh industrial environments.
4. Parylene Conformal Coating
Description: Parylene coatings are deposited as a gas, forming a thin, pinhole-free film. They offer uniform coverage and excellent protection against moisture, chemicals, and temperature extremes.
Advantages:
- Excellent barrier properties.
- Biocompatible and bio-stable.
- Uniform coating thickness.
- Superior dielectric properties.
Applications: These include medical devices, aerospace electronics, and susceptible electronic components.
Choosing the Right Conformal Coating
Selecting the appropriate conformal coating depends on several factors, such as the environmental conditions, operating temperature range, required flexibility, and reworkability. It’s essential to assess these factors carefully to ensure optimal performance and reliability of the coated electronics.
How Does Conformal Coating Shield Electronics from Environmental Stress?
A thin layer of protection called conformal coating is used on electronic circuits. It conforms to the contours of the components, covering them entirely and providing a protective barrier against various environmental factors. This coating can be made from multiple materials such as acrylics, silicones, urethanes, and epoxies, each offering specific advantages for different applications.
Environmental Stressors Confronting Electronics
Electronics are exposed to numerous environmental stressors that can compromise their functionality and reliability:
- Humidity and Moisture:These conditions can cause electrical leakage, short circuits, and corrosion.
- Dust and Debris:Dust and debris accumulation can cause overheating, interference with moving parts, and electrical arcing.
- Chemical Exposure: Contact with chemicals, such as solvents or cleaning agents, can degrade electronic components and cause malfunctions.
- Extremes of temperature:Hot or cold temperatures have the potential to cause thermal expansion and contraction, which could harm components and solder junctions.
- Mechanical Shock and Vibration:Mechanical shock and vibration can loosen connections, dislodge components, and ultimately lead to system failure.
Shielding Electronics with Conformal Coating
The conformal coating serves as a shield against these environmental stressors, offering several key benefits:
- Moisture Barrier:Coating protects against moisture and humidity, preventing corrosion and electrical damage.
- Dust and Debris Protection:It seals components from dust and debris, reducing the risk of overheating and interference.
- Chemical Resistance:Certain coatings resist chemicals, safeguarding electronics from corrosive substances.
- Thermal Management:Coatings can enhance thermal management by providing insulation and dissipating heat, thereby extending component lifespan.
- Shock and Vibration Absorption:Conformal coating absorbs shock and vibration, reducing the likelihood of mechanical failure.
Applications of Conformal Coating
Conformal coating finds applications across various industries:
- Consumer Electronics:Smartphones, tablets, and laptops benefit from conformal coating to enhance durability and reliability.
- Automotive Electronics:Coating protects automotive electronics from moisture, temperature fluctuations, and vibrations.
- Medical Devices:Critical medical equipment relies on conformal coating to ensure consistent performance in challenging environments.
- Aerospace and Defense: Electronics in aerospace and defense systems are shielded from harsh conditions, including high altitude, temperature extremes, and vibrations.
When Should Conformal Coating Be Applied in the Manufacturing Process?
Conformal coating protects electronic components from environmental stresses such as moisture, dust, chemicals, and temperature variations. Applying conformal coating at the right stage of the manufacturing process ensures optimal protection and functionality of electronic assemblies. Here’s a breakdown of when conformal coating should be applied:
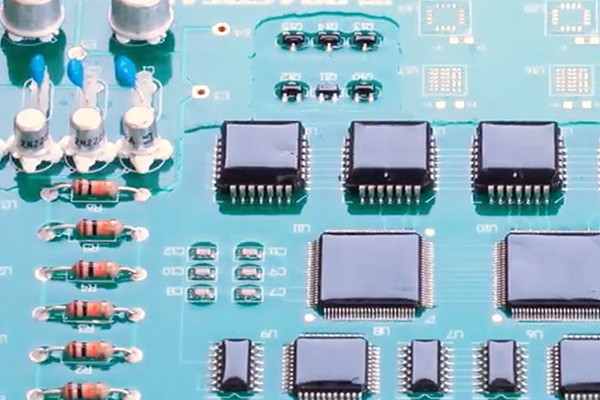
Initial Design Phase Evaluation:
During the initial design phase, engineers should evaluate whether conformal coating is necessary based on the intended application and environmental conditions. Factors such as exposure to humidity, temperature extremes, vibration, and corrosive substances influence this decision.
Component Selection:
Selecting components compatible with the conformal coating is essential. Some components may be sensitive to certain coating materials or application processes. Therefore, choosing components that can withstand the coating process is crucial without compromising their functionality or reliability.
PCB Assembly Stage:
Conformal coating is typically applied after the PCB assembly stage. Once all components are soldered onto the PCB and tested for functionality, the board is ready for conformal coating. Applying the coating at this stage ensures that all sensitive components are adequately protected before the final product assembly.
Before Functional Testing:
Conformal coating should be applied before subjecting the assembled PCB to functional testing. It ensures that the coating does not interfere with the electrical functionality of the components. Conducting functional tests after coating application helps identify any potential issues caused by the coating process.
Before Final Enclosure:
Conformal coating should be applied before the electronic assembly is enclosed in its final housing or casing. This step ensures that all exposed surfaces of the PCB are adequately protected against environmental factors and prevents any potential damage that may occur during the assembly of the final product.
Post-Assembly Inspection:
After applying the conformal coating, a thorough inspection is necessary to ensure uniform coverage and the absence of defects such as bubbles, voids, or insufficient coating thickness.
Periodic Maintenance and Reapplication:
In some cases, periodic maintenance may require the reapplication of conformal coating, especially in harsh operating environments where the coating may degrade over time. Regular inspections help identify areas where the coating needs to be reapplied to ensure continued protection of the electronic components.
Which Industries Rely Heavily on Conformal Coating?
Conformal coating is a vital protective layer for electronic components, safeguarding them against environmental hazards. Several industries heavily depend on conformal coating to ensure the reliability and durability of their electronic devices. Let’s delve into the sectors where conformal coating plays a pivotal role:
- Aerospace and Defense: In the aerospace and defense industries, electronic components face extreme conditions such as high altitude, temperature variations, moisture, and vibration. The conformal coating protects against these environmental stresses, ensuring the optimal performance and longevity of critical systems like avionics, radar, and missile guidance.
- Automotive: The automotive industry relies on conformal coating to protect electronic components from moisture, chemicals, and temperature fluctuations. From engine control units to advanced driver assistance systems (ADAS), the conformal coating helps maintain the reliability and functionality of electronic systems even in harsh operating environments.
- Medical Devices:Medical devices require high reliability and precision in performance. The conformal coating shields electronic components within medical devices from contaminants, sterilization processes, and bodily fluids. It ensures the safety and effectiveness of devices ranging from patient monitors to implantable medical devices.
- Industrial Electronics: Electronic equipment is exposed to dust, humidity, and corrosive chemicals in industrial environments. Conformal coating protects industrial electronics such as control systems, sensors, and power supplies, ensuring uninterrupted operation and minimizing downtime in critical processes.
- Telecommunications: Telecommunication equipment, including routers, switches, and base stations, operates in diverse environmental conditions, including outdoor installations. Conformal coating safeguards the sensitive electronic components from moisture, dust, and temperature fluctuations, ensuring reliable communication networks.
- Consumer Electronics: The conformal coating protects against everyday hazards like spills, humidity, and dust ingress in consumer electronics, such as smartphones, tablets, and wearables. It enhances the durability and reliability of these devices, prolonging their lifespan and ensuring uninterrupted performance.
- Energy and Renewable Resources:In the energy sector, electronic components used in power generation, distribution, and renewable energy systems are often exposed to harsh outdoor conditions. The conformal coating helps protect components such as inverters, solar panels, and wind turbines from moisture, UV radiation, and temperature extremes, ensuring consistent energy production and system reliability.
Can Conformal Coating Enhance the Lifespan of Electronic Devices?
A thin layer of protection known as conformal coating shields electronic circuitry from external elements such as moisture, dust, chemicals, and extreme temperatures. Typically made from materials like silicone, acrylic, or urethane, conformal coatings adhere to the contours of the circuit board, providing a protective barrier without altering its functionality.
Protection Against Environmental Hazards
Electronic devices often operate in harsh environments where moisture and contaminants pose significant threats. Conformal coatings act as a shield, preventing these elements from infiltrating the delicate components of the circuitry. By repelling moisture and contaminants, conformal coatings reduce the risk of corrosion, short circuits, and other damage, extending the device’s lifespan.
Enhanced Reliability
The application of conformal coating enhances the reliability of electronic devices by minimizing the likelihood of electrical failures. By insulating components from external factors that can cause malfunctions, such as humidity or chemical exposure, conformal coatings contribute to the uninterrupted performance of the device over an extended period.
Improved Thermal Management
In addition to protecting against external hazards, conformal coatings can also aid in thermal management. Some coatings possess heat-dissipating properties, which help dissipate heat generated during device operation. By maintaining optimal operating temperatures, conformal coatings prevent overheating-induced failures and ensure the longevity of electronic components.
Increased Durability
During transportation and operation, electronic devices are often subject to mechanical stresses, such as vibration and shock. Conformal coatings offer more defense against these pressures, lowering the possibility of the circuitry sustaining physical harm. This increased durability contributes to the device’s overall longevity, especially in applications where ruggedness is essential.
Facilitating Miniaturization
As electronic devices become increasingly compact, the spacing between components decreases, making them more susceptible to environmental influences. Conformal coatings enable the design and manufacture of smaller, denser electronic assemblies by protecting against moisture, dust, and other contaminants without sacrificing reliability or longevity.
How Does Conformal Coating Protect Against Corrosion and Moisture?
Conformal coating is a thin, protective film typically made from silicone, acrylic, polyurethane, or epoxy. It conforms precisely to the contours of the components it covers, providing a seamless barrier against external threats.
- Protection Against Moisture Ingress:Moisture is a common adversary of electronic devices, causing corrosion, short circuits, and electrical failures. Conformal coating acts as a waterproof barrier, preventing moisture from seeping into sensitive areas of the circuitry, thus ensuring the long-term reliability of the device.
- Corrosion Resistance: Corrosion occurs when metal components react with moisture and oxygen, leading to degradation and failure. Conformal coating creates a protective shield that isolates metal contacts and traces from environmental elements, inhibiting corrosion and extending the lifespan of electronic assemblies.
- Chemical Resistance:In addition to moisture and humidity, electronic devices may encounter various chemicals in their operating environment. Conformal coatings resist acids, solvents, and other corrosive substances, providing an extra defense against chemical damage.
- Temperature and Thermal Stability:Electronic components are subjected to fluctuating temperatures during operation. Conformal coatings are engineered to withstand a wide range of temperatures, ensuring the integrity of the protective layer even in extreme thermal conditions, thus enhancing the device’s reliability.
- Improved Reliability and Performance: By shielding electronic components from moisture, corrosion, and chemical exposure, conformal coating enhances the reliability and performance of electronic devices. Its increased durability translates to fewer malfunctions, reduced downtime, and lower maintenance costs for manufacturers and end-users.
What Challenges Arise During Conformal Coating Application?
Conformal coating is a vital process in protecting electronic assemblies from environmental hazards. However, several challenges can arise during its application, affecting the quality and effectiveness of the protective layer. This article explores these challenges and offers insights into overcoming them for successful conformal coating applications.
Surface Preparation:
One of the primary challenges in conformal coating application is ensuring proper surface preparation. Contaminants such as oils, dust, and residues must be removed from the substrate to promote adhesion and prevent defects like delamination or uneven coating coverage.
Compatibility with Substrates and Components:
Different substrates and components may require specific types of conformal coatings for optimal protection. Ensuring compatibility between the coating material and the substrate is crucial to prevent issues such as chemical reactions, poor adhesion, or damage to sensitive components.
Coating Thickness Control:
Achieving consistent and uniform coating thickness across the entire assembly can be challenging, especially on complex or uneven surfaces. Variations in coating thickness may compromise the protective properties of the layer, leaving vulnerable areas exposed to environmental threats.
Masking and Selective Coating:
Precise masking techniques are essential in applications where certain assembly areas must remain uncoated. Improper masking or inadequate coverage can result in unintended coating of critical components, leading to functionality issues or additional rework.
Curing and Drying:
Conformal coatings’ curing or drying process must be carefully controlled to ensure optimal performance. Inadequate curing time or improper curing conditions can result in incomplete polymerization, poor adhesion, or surface defects, compromising the protective layer’s effectiveness.
Environmental Factors:
Environmental conditions such as temperature, humidity, and airborne contaminants can impact the quality and consistency of conformal coating application. Controlling these factors within the application environment is crucial to minimize potential defects and ensure the integrity of the protective layer.
Quality Assurance and Inspection:
Efficient quality control procedures are necessary to find and fix any flaws or irregularities in the conformal coating application procedure. Comprehensive inspection techniques, such as visual inspection, coating thickness measurement, and electrical testing, help verify the quality and reliability of the coated assemblies.
Are There Environmental Concerns Associated with Conformal Coating?
Conformal coating is vital in electronics manufacturing, protecting against moisture, dust, chemicals, and temperature extremes. While it offers numerous benefits for product longevity and reliability, there are growing concerns about its environmental impact. Let’s delve into the environmental considerations associated with conformal coating:
Volatile Organic Compounds (VOCs):
- Conventional conformal coatings often contain VOCs, harmful air pollutants contributing to smog formation and respiratory issues.
- VOCs can evaporate into the atmosphere during application and curing processes, posing risks to human health and the environment.
Hazardous Substances:
- Some conformal coatings may contain hazardous substances such as lead, cadmium, and chromium, which can leach into soil and water sources if not correctly managed during disposal.
- These substances can accumulate in the environment, potentially causing long-term ecological damage and posing health risks to wildlife and humans.
Energy Consumption:
- Energy-intensive procedures are needed to manufacture and apply conformal coatings, which increases greenhouse gas emissions and contributes to climate change.
- Energy-efficient application methods and the use of eco-friendly formulations can mitigate these concerns.
Waste Generation:
- Excess coating material, packaging waste, and equipment cleaning residues contribute to solid waste generation.
- Improper disposal of waste materials can lead to contamination of landfills and water bodies, necessitating proper recycling or disposal procedures.
Water Pollution:
- Runoff from facilities using conformal coatings can contaminate water sources with chemicals, jeopardizing aquatic ecosystems.
- When opposed to solvent-based formulations, water-based coatings present a more environmentally beneficial option because they lower the possibility of water pollution.
Regulatory Compliance:
- Regulatory bodies impose restrictions on certain chemicals in conformal coatings to minimize environmental and health risks.
- Ensuring environmentally responsible manufacturing procedures requires adherence to rules like REACH (Registration, Evaluation, Authorization, and Restriction of Chemicals) and RoHS (Restriction of Hazardous Substances).
Sustainability Initiatives:
- Manufacturers increasingly focus on developing eco-friendly coatings with reduced VOCs and hazardous substances.
- Adopting renewable materials and sustainable manufacturing processes can significantly reduce the environmental footprint of conformal coating applications.
What Factors Should Be Considered When Selecting a Conformal Coating Material?
Selecting the appropriate conformal coating material is crucial for ensuring electronic components and assemblies’ long-term reliability and performance. With myriad options available, manufacturers must carefully consider various factors to make an informed decision. Here are vital considerations when selecting a conformal coating material:
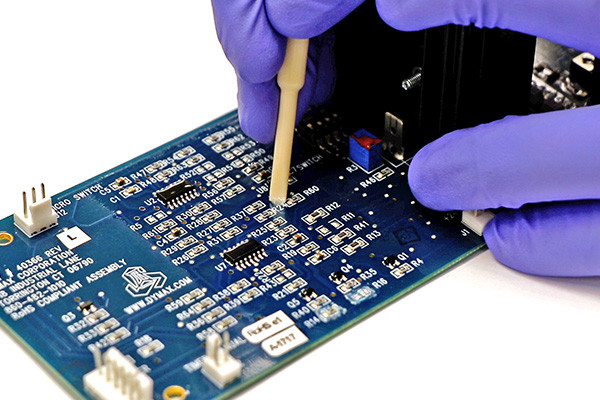
- Compatibility:Assess the compatibility of the coating material with the substrate and components to avoid any adverse reactions that could compromise performance or reliability.
- Environmental Conditions:Consider the operating environment, including temperature extremes, humidity, exposure to chemicals, and other environmental factors, to choose a coating material that offers adequate protection.
- Application Method:Evaluate the preferred application method (spraying, brushing, dipping, etc.) and select a coating material compatible with the chosen method for optimal application efficiency and uniformity.
- Electrical Properties:Determine the application’s electrical insulation requirements and select a coating material with appropriate dielectric properties to prevent electrical shorts or leakage.
- Mechanical Properties:Consider the mechanical stresses, such as thermal cycling, vibration, and mechanical shock, that the coated assembly may encounter, and choose a material with suitable flexibility, adhesion, and durability to withstand these stresses.
- Chemical Resistance:Assess the coating material’s resistance to chemicals, solvents, fuels, and other substances that the assembly may be exposed to during its lifecycle to ensure long-term protection against corrosion and degradation.
- Cure Method:Evaluate the curing requirements of the coating material, including temperature, humidity, and curing time, and ensure compatibility with the manufacturing process and assembly schedule.
- Thickness Requirements: Determine the desired coating thickness based on the level of protection required and select a material that can be applied to reliably and consistently achieve the desired thickness.
By carefully considering these factors, manufacturers can select the most suitable conformal coating material to ensure their electronic assemblies’ reliability, longevity, and performance in various applications and operating environments.
Is Conformal Coating Compatible with Different Electronic Components?
Conformal coating is a protective layer for protecting electronic components from external elements like dampness, dust, chemicals, and mechanical stress. An essential consideration in applying conformal coating is its compatibility with various electronic components. This article explores the compatibility of conformal coating with different electronic components and the factors influencing successful application.
Component Materials
- Semiconductors:Conformal coatings are generally compatible with semiconductor components, including integrated circuits (ICs), transistors, and diodes, as they protect without interfering with electrical conductivity.
- Passive Components:Resistors, capacitors, and inductors are typically compatible with conformal coating, although careful selection of coating material and application method is necessary to avoid affecting component performance.
- Connectors and Terminals:Coatings must be selected and applied carefully to avoid interfering with electrical connections or mechanical mating of connectors and terminals.
Surface Finishes
- Printed Circuit Boards (PCBs):Conformal coatings are compatible with various PCB surface finishes, including solder mask, bare copper, ENIG (Electroless Nickel Immersion Gold), and HASL (Hot Air Solder Leveling), protecting without compromising solderability.
- Surface Mount Devices (SMDs):Compatibility with surface mount devices depends on the coating’s ability to conform to complex geometries and thin profiles without causing bridging or delamination.
- Through-Hole Components:Coatings must adequately cover through-hole components and joints without compromising solder joint reliability or electrical connections.
Environmental Considerations
- Temperature Range:Conformal coatings should withstand the operating temperature range of electronic components to prevent cracking, delamination, or loss of adhesion.
- Chemical Exposure:Compatibility with chemicals encountered in the operating environment, such as solvents, oils, and cleaning agents, is crucial to ensure long-term protection.
- Humidity and Moisture:Coatings must provide effective moisture barrier properties to prevent corrosion and electrical failures in humid or damp environments.
Application Method
- Spraying:Conformal coatings can be applied via spraying methods, which require proper masking to prevent overspray and ensure uniform coverage without pooling or dripping.
- Dipping:Dip coating is another standard method for applying conformal coatings. It requires control over immersion time and withdrawal speed to achieve the desired coating thickness.
- Brushing and Dispensing:For selective coating or touch-up applications, brushing or dispensing methods may be employed, necessitating precise control over application thickness and coverage.
Conformal coating is compatible with various electronic components, provided factors such as component materials, surface finishes, environmental considerations, and application methods are carefully considered. Manufacturers can protect electronic assemblies from ecological hazards by selecting appropriate coating materials and application techniques while maintaining component functionality and reliability.
How Does Conformal Coating Impact the Thermal Performance of Electronics?
Conformal coating is a widely used technique in electronics manufacturing to protect circuit boards. It protects electronic components from outside elements, including dust, dampness, and chemical exposure. While the primary purpose of conformal coating is to provide insulation and corrosion resistance, it also has implications for the thermal performance of electronics. Understanding the impact of conformal coating on thermal management is crucial for optimizing the reliability and efficiency of electronic devices. Here’s an exploration of how conformal coating influences the thermal performance of electronics:
- Heat Dissipation:Conformal coatings can affect the heat dissipation capabilities of electronic components by altering their thermal conductivity and surface properties. Coatings with high thermal conductivity facilitate efficient heat transfer away from heat-generating components, enhancing thermal management and preventing overheating.
- Insulation Properties:Some conformal coatings offer electrical insulation properties, preventing short circuits and electrical failures caused by moisture ingress or contamination. While insulation is essential for protecting sensitive electronic components, it can also inhibit heat dissipation and increase thermal resistance, leading to elevated operating temperatures.
- Coating Thickness:The conformal coating layer’s thickness significantly impacts defining its effect on thermal performance. Thin coatings may provide sufficient protection while minimizing thermal impedance, whereas thick coatings can act as thermal barriers, impeding heat transfer and exacerbating thermal issues.
- Surface Roughness:The surface roughness of conformal coatings can affect their contact with heat sinks or other dissipative elements. Smooth coatings promote better thermal contact and heat transfer, whereas rough or uneven coatings may introduce air gaps or thermal barriers, reducing thermal conductivity and efficiency.
- Material Selection:The choice of conformal coating material influences its thermal properties and performance. Silicone, acrylic, and polyurethane are common coating materials with unique thermal conductivity, dielectric strength, and temperature resistance characteristics. Selecting a coating material with optimal thermal properties is essential for effective thermal management.
- Application Method:The conformal coating, whether spraying, dipping, or brushing, can impact its uniformity, thickness, and adherence to the substrate. Proper application techniques ensure even coverage and minimize defects such as pinholes or voids that could compromise thermal performance.
- Environmental Conditions:Operating environments, such as temperature extremes, humidity levels, and exposure to chemicals or contaminants, can affect the performance of conformal coatings and their ability to withstand thermal stresses. Coatings should be selected based on their compatibility with the anticipated environmental conditions to ensure long-term reliability.
- Testing and Validation:Extensive examination and verification of conformal coatings under simulated operating conditions are essential for assessing their impact on thermal performance. Testing methodologies may include thermal cycling, accelerated aging tests, and thermal conductivity measurements to evaluate heat dissipation efficiency and reliability.
What Are the Steps Involved in the Conformal Coating Process?
Conformal coating protects electronic components from environmental factors such as moisture, dust, chemicals, and temperature extremes. Understanding the steps involved in the conformal coating process is essential for ensuring the reliability and longevity of electronic devices. This exploration outlines the critical stages in the conformal coating process, shedding light on each step’s significance and best practices for implementation.
Surface Preparation:
The first step in the conformal coating process is surface preparation, which involves thoroughly cleaning and inspecting the electronic components. Any contaminants, residues, or oxidation present on the surface must be removed to ensure proper coating adhesion. Techniques such as cleaning with solvents, mechanical abrasion, or plasma treatment may be employed to achieve a clean and uniform surface.
Masking and Taping:
Masking and taping are critical steps in the conformal coating, especially when selective coating is required. Areas that should not be coated, such as connectors, switches, and sensitive components, are masked off using specialized tapes or liquid masking materials. Proper masking ensures the conformal coating is applied only to the designated areas, preventing electrical shorts or interference with component functionality.
Coating Application:
The coating application stage involves applying the conformal coating material to the prepared surfaces using various techniques such as spraying, dipping, brushing, or selective coating. The choice of application method depends on factors such as component geometry, coating material viscosity, and production volume. Achieving a uniform and consistent coating thickness across all surfaces is crucial to protecting against environmental contaminants.
Curing and Drying:
After applying the conformal coating, the next step is curing or drying the coating to achieve the desired film properties. Depending on the coating material used, curing may involve heat, UV, or air drying. Proper curing ensures the coating forms a durable and resilient barrier while maintaining its electrical and mechanical properties.
Post-coating Inspection and Testing:
The final stage in the conformal coating process involves post-coating inspection and testing to ensure the quality and reliability of the coated components. Visual inspection is conducted to detect defects, such as bubbles, runs, or voids in the coating. Additionally, electrical testing, such as insulation resistance and dielectric strength testing, may be performed to verify the integrity of the coating and its insulation properties.
Can Conformal Coating Adapt to Various Substrates and Surface Conditions?
Conformal coating protects electronic components from environmental factors and mechanical stresses. Still, its effectiveness hinges on its ability to adapt to different substrates and surface conditions. This article investigates the versatility of conformal coating in accommodating various substrates and surface conditions, ensuring optimal protection and performance for electronic assemblies.
Substrate Compatibility
- Printed Circuit Boards (PCBs): Conformal coatings are designed to adhere to different types of PCB substrates, including FR-4, flexible PCBs, and ceramic substrates, providing uniform coverage without affecting electrical conductivity.
- Metal Substrates:Coatings must bond effectively to metal substrates such as aluminum, copper, and steel, offering corrosion protection and electrical insulation without compromising thermal dissipation.
- Plastic Substrates:Compatibility with plastic substrates like ABS, polycarbonate, and polyamide requires coatings to exhibit adhesion and flexibility to accommodate thermal expansion and contraction.
Surface Condition Considerations
- Cleanliness:Proper surface cleaning and preparation are essential to ensure adequate adhesion and coverage of conformal coatings, necessitating the removal of contaminants like oils, grease, and flux residues.
- Surface Roughness:Coatings must conform to surface irregularities and roughness variations, requiring the selection of appropriate coating materials and application techniques to achieve uniform coverage.
- Surface Energy:Compatibility with substrates of varying surface energy levels, such as low-energy plastics or high-energy metals, necessitates coatings with tailored adhesion properties to ensure long-term bonding.
Environmental Adaptability
- Temperature Variations:Conformal coatings should maintain adhesion and flexibility across a wide temperature range, from sub-zero to elevated temperatures in industrial or automotive applications.
- Humidity and Moisture:Effective moisture barrier properties are crucial for coatings to prevent ingress of moisture and humidity, protecting sensitive electronic components from corrosion and electrical failures.
- Chemical Exposure:Compatibility with chemicals commonly encountered in operating environments, including solvents, oils, and cleaning agents, ensures long-term protection against chemical degradation and delamination.
Application Methods and Techniques
- Spraying: Spraying methods allow for uniform coating application across large surface areas, with adjustments made for spray pattern, pressure, and nozzle size to accommodate different substrate geometries.
- Dipping:Dip coating offers complete coverage of complex components and assemblies, requiring control over immersion time and withdrawal speed to achieve the desired coating thickness.
- Selective Coating:For targeted protection of specific areas or components, selective coating methods such as masking or robotic dispensing provide precision and control over coating thickness and coverage.
What Innovations Are Shaping the Future of Conformal Coating?
Innovations to enhance performance, sustainability, and efficiency are shaping the future of conformal coating. The demand for advanced conformal coating solutions grows as electronic devices evolve in complexity and functionality. This exploration delves into the innovations driving the evolution of conformal coating processes, elucidating their potential impact on industries and applications.
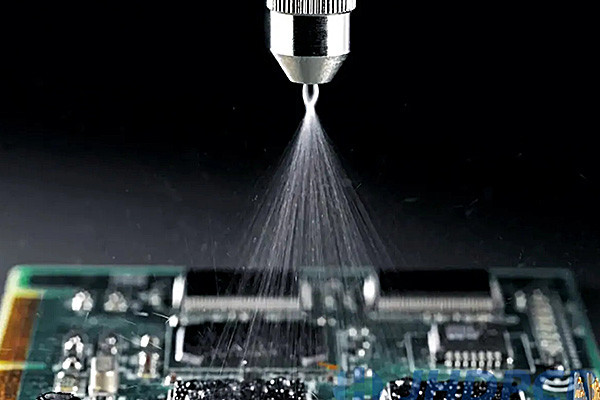
Nanotechnology Advancements:
One key innovation shaping the future of conformal coating is the integration of nanotechnology. Nanocoatings, engineered at the nanoscale, offer superior properties such as enhanced barrier protection, corrosion resistance, and electrical insulation. Manufacturers can develop conformal coatings that provide unparalleled performance while reducing material usage and environmental impact by leveraging nanomaterials such as nanoparticles and nanocomposites.
Self-healing Coatings:
Self-healing coatings represent another frontier in conformal coating innovation, offering the ability to repair damage and extend the lifespan of coated components. These coatings incorporate microcapsules or reactive polymers that can autonomously mend cracks, scratches, or abrasions after exposure to outside stimulants like moisture, light, or heat. By continuously repairing damage, self-healing coatings enhance the durability and reliability of electronic devices, particularly in harsh operating environments.
Functional Coatings for Advanced Applications:
Innovations in functional coatings drive the development of conformal coating solutions tailored to specific applications and industries. Functional coatings may include properties such as antimicrobial, antistatic, or anti-fogging capabilities, addressing emerging healthcare, automotive, and aerospace needs. By incorporating additional functionalities into conformal coatings, manufacturers can enhance coated electronic components’ performance and value proposition.
Green and Sustainable Coating Technologies:
A shift towards green and sustainable coating technologies increasingly influences the future of conformal coating. As the importance of environmental stewardship and regulatory compliance, manufacturers are exploring eco-friendly alternatives to traditional coating materials. Innovations like water-based coatings, bio-based resins, and solvent-free formulations offer reduced environmental impact, improved worker safety, and enhanced sustainability throughout the product lifecycle.
Smart Coating Solutions:
Integrating intelligent technologies into conformal coatings is poised to revolutionize how electronic devices are protected and monitored. Innovative coatings may incorporate sensors, indicators, or responsive materials that provide real-time feedback on coating integrity, environmental conditions, or component performance. By enabling proactive maintenance and condition monitoring, intelligent coating solutions enhance reliability, reduce downtime, and optimize the lifecycle management of coated electronic devices.
How Does Conformal Coating Contribute to Regulatory Compliance in Electronics?
Conformal coating ensures electronic regulatory compliance by protecting against environmental factors and enhancing reliability. This article examines how conformal coating contributes to regulatory compliance in the electronics industry through various mechanisms and considerations.
Environmental Protection
- Moisture Resistance:Conformal coatings create a barrier against moisture ingress, mitigating the risk of corrosion and electrical failures that can lead to non-compliance with safety standards.
- Chemical Resistance:Protection against exposure to chemicals such as solvents and cleaning agents ensures electronic components remain operational and compliant with regulatory requirements.
- Dust and Contaminant Protection:Coatings safeguard sensitive electronics from dust, debris, and contaminants, preventing potential performance degradation or safety hazards.
Insulation and Dielectric Properties
- Electrical Insulation:Conformal coatings insulate electronic components, preventing short circuits and ensuring compliance with safety standards for electrical insulation.
- Dielectric Strength:Coatings with high dielectric strength enhance insulating qualities, lowering the possibility of an electrical malfunction and ensuring compliance with regulatory requirements.
Flame Retardancy and Safety Standards
- Flame Retardant Formulations:Conformal coatings can be formulated with flame retardant additives to meet safety standards for fire resistance and ensure compliance with regulations such as UL 94 and IEC 60695.
- Smoke and Toxic Gas Emissions:Coatings that inhibit smoke and toxic gas emissions during fire events contribute to compliance with environmental and safety regulations, protecting both personnel and equipment.
Conformal coating ensures regulatory compliance in the electronics industry by providing environmental protection, insulation, flame retardancy, and adherence to substance regulations such as RoHS and REACH. By selecting appropriate coating formulations and application methods, Manufacturers can improve the dependability and security of electronic products while meeting stringent regulatory requirements.
What Role Does Thickness Play in Conformal Coating Effectiveness?
Conformal coating is a protective barrier for protecting electronic components from external elements like dampness, dust, and chemical contaminants. Convergent coating layer thickness is a critical factor that significantly influences its effectiveness in providing insulation, corrosion resistance, and mechanical protection. Understanding the role of thickness in conformal coating effectiveness is essential for optimizing the reliability and performance of electronic devices. Here’s an exploration of the importance of thickness in conformal coating effectiveness:
- Barrier Protection:The primary function of conformal coating is to create a barrier between electronic components and external elements, such as moisture, chemicals, and debris. The coating layer’s thickness directly affects its ability to effectively seal the components and prevent ingress of contaminants, reducing the risk of corrosion, short circuits, and electrical failures.
- Dielectric Strength:Conformal coatings with adequate thickness provide insulation against electrical conductivity, preventing leakage currents and short circuits between conductive traces or components. Thicker coatings offer higher dielectric strength, enhancing electrical insulation properties and ensuring reliable performance in high-voltage applications.
- Mechanical Durability:Thicker conformal coatings offer excellent mechanical protection against physical damage, including abrasion, impact, and vibration. The additional thickness adds strength and resilience to the coating, reducing the risk of delamination or cracking when subjected to mechanical stresses during handling, assembly, or operation.
- Conformal Coating Methods:Different application methods, such as spraying, dipping, or brushing, can achieve varying thicknesses of conformal coating layers. The choice of the best coating technique is determined by factors such as the complexity of the assembly, the desired coating thickness, and the uniformity of coverage required to ensure adequate protection.
- Compatibility with Components:While thicker conformal coatings offer superior protection, they may challenge compatibility with tight-tolerance components, connectors, or fine-pitch circuitry. Careful consideration of component spacing, clearances, and coating coverage is necessary to avoid interference or masking of critical features.
- Cost Considerations:Thicker conformal coatings require larger volumes of material, resulting in increased material costs and potentially longer processing times during application and curing. Manufacturers must balance the desired level of protection with cost considerations to optimize the thickness of conformal coatings for specific applications.
- Quality Control:Proper measurement and control of coating thickness are essential to ensure uniform coverage and adherence to specifications. Thickness measurement techniques, such as dry film thickness gauges or optical microscopy, allow manufacturers to monitor coating quality and detect inconsistencies or defects that could compromise effectiveness.
Are There Any Special Considerations for Conformal Coating in Harsh Environments?
Conformal coatings are crucial protective barriers for electronic components, safeguarding them against environmental hazards such as moisture, dust, chemicals, and temperature extremes. However, in harsh environments characterized by extreme temperatures, high humidity, corrosive substances, or mechanical stress, special considerations must be made to ensure the efficacy and longevity of conformal coatings. This exploration delves into the unique challenges of harsh environments and the specific considerations to address when applying conformal coatings in such conditions.
Selection of Coating Material:
Choosing the appropriate coating material is paramount when dealing with harsh environments. Specific environments may require improved chemical resistance, UV stability, or temperature tolerance coatings. Silicone-based coatings, for example, offer excellent flexibility and thermal stability, making them well-suited for applications in extreme temperatures. Similarly, polyurethane coatings provide superior chemical resistance and mechanical protection, ideal for environments exposed to corrosive substances or mechanical stress.
Thickness and Coverage:
In harsh environments, ensuring adequate coating thickness and coverage is crucial for robust protection of electronic components. Thicker coatings can provide better insulation and barrier properties, enhancing resistance to moisture ingress and chemical exposure. However, excessive coating thickness may lead to issues such as increased curing times or difficulty in rework. Achieving uniform coverage across all surfaces, including complex geometries and hard-to-reach areas, is essential to prevent potential weak points in the coating that could compromise protection.
Adhesion and Compatibility:
Adhesion to substrate surfaces and compatibility with other materials in the electronic assembly are critical considerations in harsh environments. Proper surface preparation, including cleaning and surface activation, is essential to promote adhesion and ensure the integrity of the coating bond. Additionally, compatibility between the conformal coating and underlying components, such as solder joints or conformal coating for connectors, must be carefully evaluated to prevent delamination or degradation under harsh conditions.
Testing and Validation:
Rigorous testing and validation are imperative when deploying conformal coatings in harsh environments to assess performance and reliability. Accelerated aging tests, environmental exposure tests, and mechanical stress tests can simulate the harsh conditions that coated components may encounter during their operational lifespan. By subjecting conformal-coated assemblies to these tests, manufacturers can identify potential weaknesses or failure modes and make necessary adjustments to optimize coating performance and durability in harsh environments.
Can Conformal Coating Be Removed or Modified Once Applied?
Conformal coating is crucial in electronic manufacturing, protecting environmental elements, including chemicals, dust, and dampness. However, the question often arises: can conformal coating be removed or modified once applied? This discussion explores the possibilities and limitations of altering or eliminating conformal coatings post-application.
Can Conformal Coating Be Removed?
- Chemical Removal:Conformal coatings can be chemically removed using solvents specifically designed for the type of coating used. Typical solvents include acetone, isopropyl alcohol, and specialized conformal coating removers. These solvents dissolve the coating, allowing it to be wiped or brushed away.
- Mechanical Removal: Mechanical methods such as scraping, sanding, or using abrasive materials can also remove conformal coatings. However, this approach is more aggressive and may damage delicate electronic components if not executed carefully.
Challenges and Considerations
- Residue Removal:Even after removing the primary coating, traces or residues may remain on the surface. Thorough cleaning is essential to eliminate any remnants that could compromise the performance or reliability of the electronic assembly.
- Component Sensitivity:Electronic components may be sensitive to harsh chemicals or mechanical stress. Care must be taken to select removal methods that do not harm the components or their functionality.
Can Conformal Coating Be Modified?
- Reapplication:In some cases, modifying conformal coatings by reapplying a different type or formulation may be possible. This approach requires thoroughly cleaning the existing coating and preparing the surface before applying the new layer.
- Selective Masking:Alternatively, selective masking techniques can modify specific areas of the conformal coating while leaving the rest intact. Masking materials such as tapes or liquid masking agents are applied to protect desired areas during recoating or modification processes.
Conclusion
In conclusion, the realm of conformal coating unveils a fascinating intersection between technology, protection, and innovation. From shielding intricate circuitry to safeguarding against environmental hazards, its significance in the electronics industry cannot be overstated. As we continue to push the boundaries of electronic design, understanding the nuances of conformal coating will undoubtedly remain a critical aspect of ensuring reliability and performance in our increasingly interconnected world.
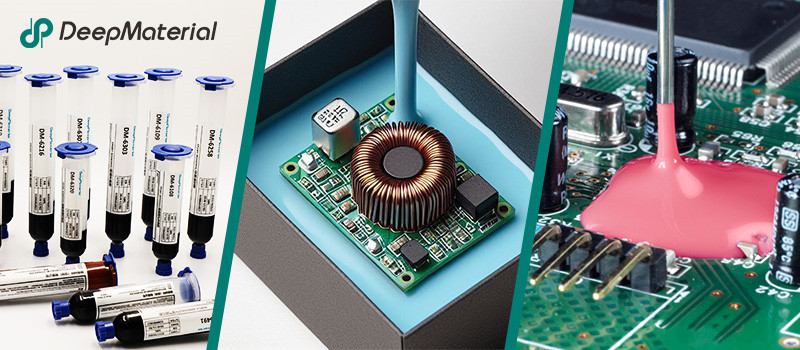
About DeepMaterial
DeepMaterial is a trusted supplier of encapsulant materials that are used in electronics manufacturing worldwide. From chip on board encapsulants such as glob top material to conformal coatings, underfills, low pressure molding, and potting solutions, DeepMaterial offers a full range of circuit board protection materials that effectively protect circuit boards while help reduce costs. More…Deepmaterial is a the manufacturer of epoxy adhesives including hardeners, metalbond, and metal filled resins. Structural, toughened medium viscosity, and non-sag adhesives are also offered. Some adhesives are resistant to thermal shock, chemical, vibration dampening, and impact. Suitable for metals, plastics, wood, and ceramics. Serves electronics, aerospace, automotive, tooling, marine, and construction industries. REACH and RoHS compliant. FDA approved. UL listed. Meets military specifications. We are the one of best adhesive manufacturers in China.
Blogs & News
Potting compounds are at the frontline of electronics assembly, delivering effective protection in challenging environmental conditions while improving mechanical strength and offering high electric insulation. Used within a variety of industries, electrical potting compounds are found within a broad range of consumer electronics, as well as used in applications across the automotive, aerospace, and other industries where electronic assemblies are prevalent.
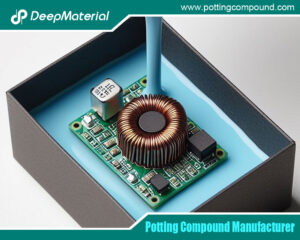
Potting Compound vs. Epoxy: A Comprehensive Comparison
Potting Compound vs. Epoxy: A Comprehensive Comparison In the world of electronics, manufacturing, and material encapsulation, two terms frequently come up: potting compounds and epoxy.
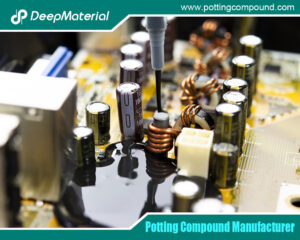
Potting Compound for PCB
Potting Compound for PCB A potting compound is a liquid or semi-liquid material that is poured or injected over a PCB or electronic assembly, then
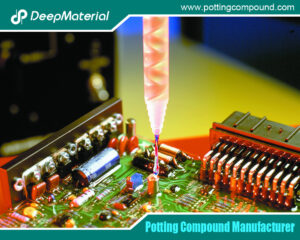
In – depth Analysis of the Curing Characteristics of Electronic Potting Compounds
In – depth Analysis of the Curing Characteristics of Electronic Potting Compounds Electronic potting compounds play a vital role in the electronics industry. They can
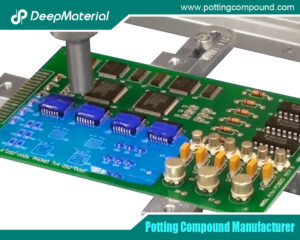
A Comprehensive Analysis of the Environmental Performance of Encapsulating Materials: From Regulations to Practices
A Comprehensive Analysis of the Environmental Performance of Encapsulating Materials: From Regulations to Practices In modern industrial manufacturing, encapsulating materials are widely used in numerous

A Comprehensive Analysis of PCB Encapsulation Quality Inspection: Innovative Application of Non-Destructive Testing Technologies
A Comprehensive Analysis of PCB Encapsulation Quality Inspection: Innovative Application of Non-Destructive Testing Technologies In the field of electronic manufacturing, the encapsulation process of printed
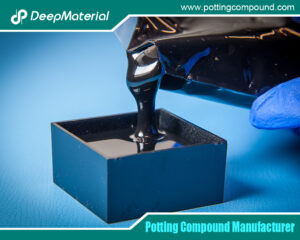
Analysis of the Improvement of the Seismic and Impact Resistance Performance of PCB by Encapsulation
Analysis of the Improvement of the Seismic and Impact Resistance Performance of PCB by Encapsulation During the operation of electronic devices, the PCB (Printed Circuit