How to Measure Conformal Coating Thickness
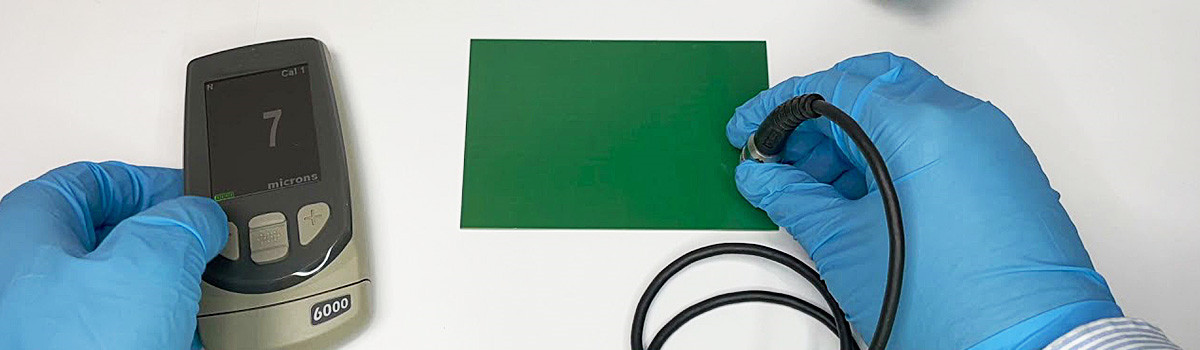
Conformal coating protects electronic components from environmental factors such as moisture, chemicals, and dust. Ensuring the proper thickness of the conformal coating is essential for its effectiveness. Proper measurement techniques are thus indispensable in guaranteeing optimal performance. In this series of questions, we delve into various methods and considerations for measuring conformal coating thickness accurately.
Table of Contents
ToggleEssential knowledge to be aware of:
What is the importance of measuring conformal coating thickness?
Measuring the conformal coating thickness is essential for guaranteeing the dependability and performance of electronic components, especially under challenging conditions like those found in industrial, automotive, aircraft, and marine applications. Here are several vital reasons why measuring conformal coating thickness is essential:
- Protection from Environmental Factors: Electronic components are coated with conformal coatings to shield them from environmental aggressors such as moisture, dust, chemicals, and temperature changes. The thickness of the coating directly impacts its ability to provide adequate protection. Proper thickness ensures that the coated components are shielded adequately against these factors, thus extending their operational lifespan.
- Prevention of Electrical Failures: In electronic assemblies, conductive contaminants or moisture can lead to short circuits or corrosion, resulting in electrical failures. A uniform and adequate conformal coating thickness acts as a barrier, preventing the ingress of contaminants and reducing the likelihood of electrical failures.
- Insulation and Dielectric Strength: Conformal coatings insulate layers between adjacent conductive components on a printed circuit board (PCB). The thickness of the coating affects its dielectric properties, including its insulation resistance and dielectric strength. Measuring and maintaining the proper thickness ensures the coating retains its insulating properties, preventing unintended electrical conduction between components.
- Conformity to Standards and Specifications: Various industry standards and specifications dictate the acceptable thickness range for conformal coatings based on the application and environmental conditions. Measuring the coating thickness ensures compliance with these standards, ensuring product quality and reliability. Non-compliance could lead to rejected products or potential failures in the field.
- Process Control and Quality Assurance: Monitoring conformal coating thickness is essential for manufacturing process control and quality assurance. Manufacturers can detect deviations from the intended thickness range early in production by routinely measuring and checking the thickness. It enables rapid remedial action to ensure consistency and quality.
Measuring conformal coating thickness is crucial for ensuring electronic assemblies’ reliability, functionality, and longevity by protecting against environmental factors, preventing electrical failures, maintaining insulation properties, ensuring compliance with standards, and facilitating process control and quality assurance in manufacturing. By enclosing the connection, you lower the chance of corrosion, short circuits, and other types of damage by constructing a barrier that keeps impurities out.
What are the different types of conformal coating thickness measurement methods?
Conformal coating thickness measurement is crucial in ensuring the reliability and effectiveness of electronic components by protecting them from environmental factors like moisture, dust, and chemicals. Various methods are employed to measure the thickness of conformal coatings accurately. These methods can be broadly categorized into non-contact and contact methods.
Non-contact methods utilize techniques that do not physically touch the coating surface. Standard non-contact methods include:
- Optical Profilometry: This method employs optical principles to measure the thickness of the coating by analyzing the reflected light from the surface. It provides high-resolution measurements and is suitable for various coating materials.
- Laser Scanning Confocal Microscopy (LSCM): LSCM uses a laser beam to scan the coating surface and a confocal microscope to measure the reflected light. It offers high precision and is capable of measuring transparent coatings.
- X-ray Fluorescence (XRF): XRF measures the thickness of conformal coatings by analyzing the characteristic X-rays emitted when the layer is irradiated with X-rays. It is suitable for measuring thick coatings and can also provide information about the composition of the coating material.
Contact methods involve physical contact with the coating surface and typically use probes or sensors to measure the thickness. Standard contact methods include:
- Eddy Current: Eddy current probes generate electromagnetic fields interacting with the coating surface, producing eddy currents. The thickness of the coating affects the impedance of the eddy currents, allowing for thickness measurement.
- Ultrasonic Thickness Measurement: Ultrasonic waves are propagated through the coating, and the time taken to travel through the coating and reflect is measured. This method is effective for measuring thick coatings and can penetrate non-metallic substrates.
- Micrometer or Caliper Measurement: These traditional methods involve directly measuring the coating thickness using mechanical tools such as micrometers or calipers. While simple and cost-effective, they may not be suitable for thin or delicate coatings.
Each method has advantages and limitations, and the choice depends on factors such as coating material, substrate type, required accuracy, and accessibility. Proper selection and calibration of the measurement method are essential to ensure accurate and reliable conformal coating thickness measurements.
How does the thickness of conformal coating affect its protective properties?
Conformal coatings are thin protective layers applied to electronic circuitry to safeguard against environmental factors such as moisture, dust, chemicals, and temperature variations. The thickness of conformal coating plays a critical role in determining its protective properties.
A thicker coating provides better coverage and insulation, effectively sealing the circuitry from external contaminants. This barrier helps prevent corrosion, short circuits, and other forms of damage that can compromise the functionality of electronic devices. Additionally, a thicker coating enhances resistance to mechanical stress, such as vibration or flexing, which can occur during handling or operation.
Moreover, the thickness of the coating influences its dielectric properties. A thicker coating typically has a higher dielectric strength, meaning it can withstand higher voltages without breaking down. This is crucial for protecting sensitive electronic components from electrical interference or breakdown due to voltage spikes.
However, there are also considerations against excessive thickness. While a thicker coating may offer better protection, it can also introduce challenges during application and may negatively impact the performance of the electronic device. Excessive thickness can lead to issues like uneven coating, increased weight, and interference with component functionality or heat dissipation. Additionally, thick coatings may take longer to cure, extending production time and potentially increasing costs.
Furthermore, the thermal conductivity of the conformal coating can be affected by its thickness. Thicker coatings may impede heat dissipation from electronic components, leading to overheating and reduced performance or reliability.
While a thicker conformal coating generally provides enhanced protection against environmental factors and mechanical stress, it is essential to balance thickness and practical considerations such as application feasibility, thermal management, and overall device performance. A carefully optimized thickness ensures optimal protection without compromising other aspects of electronic device functionality and reliability.
What are the common industry standards for conformal coating thickness?
Conformal coating thickness is a critical factor in ensuring the reliability and performance of electronic assemblies, particularly in industries like aerospace, automotive, medical devices, and consumer electronics where protection against environmental factors is essential. While specific requirements may vary based on application and environmental conditions, there are some common industry standards and guidelines for conformal coating thickness.
One widely recognized standard is IPC-A-610, which provides guidance on the acceptability of electronic assemblies. It suggests that conformal coating thickness should typically fall within the range of 25 to 75 micrometers (1 to 3 mils). However, this standard also emphasizes that the coating thickness should be consistent and sufficient to cover and protect all relevant components and features on the assembly.
Another important standard is MIL-I-46058C, although it has been superseded by IPC-CC-830. This military specification outlined requirements for conformal coatings, including thickness. It recommended a minimum thickness of 25 micrometers (1 mil) and a maximum of 125 micrometers (5 mils) for Type AR coatings. However, IPC-CC-830A, the replacement for MIL-I-46058C, doesn’t specify precise thickness values but focuses more on performance and material properties.
The automotive industry often refers to standards such as the International Automotive Task Force (IATF) 16949, which includes guidelines for conformal coating thickness to ensure product quality and reliability in automotive electronic assemblies. These standards typically align with IPC guidelines but may have additional requirements specific to automotive applications.
In medical device manufacturing, adherence to regulations such as ISO 13485 is crucial. While ISO 13485 doesn’t specify conformal coating thickness directly, it emphasizes the importance of process control and documentation to ensure product quality and consistency, which indirectly influences coating thickness.
Overall, while there are common industry standards and guidelines for conformal coating thickness, it’s essential for manufacturers to consider specific application requirements, environmental conditions, and regulatory compliance when determining the appropriate thickness for their electronic assemblies. Regular testing and quality control measures are also necessary to ensure consistent and reliable performance over the product’s lifecycle.
What are the common industry standards for conformal coating thickness?
Conformal coating thickness is a critical factor in ensuring the reliability and performance of electronic assemblies, particularly in industries like aerospace, automotive, medical devices, and consumer electronics, where protection against environmental factors is essential. While specific requirements may vary based on application and environmental conditions, some common industry standards and guidelines exist for conformal coating thickness.
One widely recognized standard is IPC-A-610, which guides the acceptability of electronic assemblies. Conformal coating thickness should typically fall within 25 to 75 micrometers (1 to 3 mils). However, this standard also emphasizes that the coating thickness should be consistent and sufficient to cover and protect all relevant components and features in the assembly.
Another necessary standard is MIL-I-46058C, although IPC-CC-830 has superseded it. This military specification outlined requirements for conformal coatings, including thickness. It recommended a minimum thickness of 25 micrometers (1 mil) and a maximum of 125 micrometers (5 mils) for Type AR coatings. However, IPC-CC-830A, the replacement for MIL-I-46058C, doesn’t specify precise thickness values but focuses more on performance and material properties.
The automotive industry often refers to standards such as the International Automotive Task Force (IATF) 16949, which includes guidelines for conformal coating thickness to ensure product quality and reliability in automotive electronic assemblies. These standards typically align with IPC guidelines but may have additional requirements specific to automotive applications.
Adherence to regulations such as ISO 13485 is crucial in medical device manufacturing. While ISO 13485 doesn’t specify conformal coating thickness directly, it emphasizes the importance of process control and documentation to ensure product quality and consistency, indirectly influencing coating thickness.
While there are common industry standards and guidelines for conformal coating thickness, manufacturers need to consider specific application requirements, environmental conditions, and regulatory compliance when determining the appropriate thickness for their electronic assemblies. Regular testing and quality control measures are also necessary to ensure consistent and reliable performance over the product’s lifecycle.
Can conformal coating thickness be measured non-destructively?
Conformal coating thickness can be measured non-destructively through various techniques, offering valuable insights into the quality and effectiveness of the coating without compromising the integrity of the coated material. Several methods are commonly employed for this purpose:
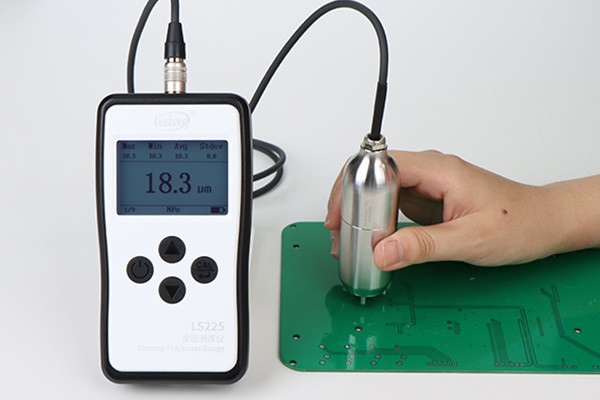
- Eddy Current Testing: This technique utilizes electromagnetic induction to measure variations in electrical conductivity or magnetic permeability caused by changes in coating thickness. Eddy current probes generate a magnetic field that interacts with the conductive substrate beneath the coating. By analyzing changes in the induced currents, the thickness of the coating can be determined.
- Ultrasonic Testing (UT): Ultrasonic waves are transmitted through the coating material, and the time taken to reflect from the substrate is measured. The thickness of the coating is calculated based on the time delay and the sound velocity through the coating material. UT can provide accurate measurements even through relatively thick coatings.
- Optical Coherence Tomography (OCT): This method employs low-coherence interferometry to capture cross-sectional images of the coating. By analyzing the interference patterns of light waves reflected from different layers within the coating, OCT can precisely determine its thickness. It is beneficial for transparent or translucent coatings.
- X-ray Fluorescence (XRF): XRF can measure the thickness of conformal coatings containing heavy elements. When X-rays are directed at the coating, they cause the emission of fluorescent X-rays, which are characteristic of the elements present. By analyzing the intensity of these X-rays, the thickness of the coating can be determined.
- Terahertz Imaging: Terahertz radiation can penetrate many non-metallic materials, including conformal coatings. The thickness of the coating can be inferred by measuring the time delay and intensity of reflected terahertz pulses.
These non-destructive methods offer advantages such as minimal sample preparation, rapid measurement times, and the ability to inspect coatings on complex geometries. However, the choice of technique may depend on factors such as the material composition of the layer, the substrate material, and the desired level of accuracy. Integrating these methods into quality control ensures conformal coatings’ consistent application and performance in various industrial applications.
What are the challenges associated with measuring conformal coating thickness?
Measuring conformal coating thickness presents several challenges owing to the nature of the coatings and the intricacies of the surfaces to which they are applied. Conformal coatings are thin layers of protective material applied to electronic components to safeguard them against environmental factors such as moisture, dust, chemicals, and temperature variations. However, accurately measuring the thickness of these coatings is crucial for ensuring optimal performance and reliability. Here are some challenges associated with measuring conformal coating thickness:
- Transparency and Opacity: Conformal coatings can vary in transparency and opacity, making it difficult to visually assess thickness accurately. This can lead to consistency, mainly if the coating is unevenly applied or contains air pockets.
- Surface Variability: Electronic components often have complex geometries and uneven surfaces. Measuring coating thickness across such surfaces can be challenging due to variations in height, angles, and contours, leading to inaccurate readings.
- Substrate Material: The substrate material plays a significant role in the accuracy of thickness measurements. Different materials have different reflective properties, affecting the performance of measurement techniques such as optical methods.
- Measurement Techniques: Various techniques are employed to measure conformal coating thickness, including optical methods (interferometry and microscopy), eddy current, ultrasonics, and mechanical methods. Each technique has limitations and may not be suitable for all coatings or surfaces.
- Calibration and Standards: Ensuring the accuracy and reliability of measurement equipment through proper calibration is essential. Additionally, the lack of standardized measurement procedures can lead to inconsistencies in results, making it challenging to compare data across different systems or laboratories.
- Cost and Complexity: Some measurement techniques, such as X-ray fluorescence (XRF) or scanning electron microscopy (SEM), can be expensive and require specialized equipment and trained personnel. This can pose challenges for smaller manufacturers or laboratories with limited resources.
Addressing these challenges often involves a combination of careful process control, advanced measurement techniques, standardized procedures, and regular calibration to ensure accurate and consistent results. Additionally, technological advancements may lead to the development of more robust and cost-effective measurement solutions in the future.
What equipment is typically used for measuring conformal coating thickness?
Measuring conformal coating thickness is crucial in ensuring the reliability and performance of electronic components, as it helps maintain consistent protection against environmental factors such as moisture, dust, and chemicals. Several methods and equipment are commonly used for this purpose.
- Digital Thickness Gauges: These gauges utilize non-contact methods such as eddy currents or ultrasonic waves to measure coating thickness. They provide quick and accurate measurements and are suitable for various coating materials. Digital thickness gauges often come with multiple probes or sensors for different substrate materials and coating types.
- Micrometers and Calipers: While more precise than digital thickness gauges, micrometers and calipers are still used for quick, approximate measurements of conformal coating thickness. They are handy for thicker coatings where precision is less critical.
- Cross-Sectional Analysis: This method involves cutting a sample of the coated substrate and examining it under a microscope to measure the thickness of the coating layer. While accurate, this method is destructive and time-consuming, making it less suitable for routine quality control but valuable for in-depth analysis.
- Optical Profilers: Optical profilers use light interference techniques to measure coating thickness with high precision and non-destructively. They provide detailed surface topography information and thickness measurements, making them helpful in characterizing conformal coatings on complex surfaces.
- X-ray Fluorescence (XRF): XRF can measure the thickness of conformal coatings by analyzing the elemental composition of the coating material. While less commonly used than other thickness measurement methods, XRF can provide valuable insights into coating thickness and composition.
- Infrared (IR) Reflectance: IR reflectance techniques analyze the reflection of infrared light from the coated surface to determine coating thickness. This method is beneficial for transparent coatings and can be non-contact, making it suitable for delicate substrates.
- Automated Optical Inspection (AOI): AOI systems equipped with specialized algorithms can measure conformal coating thickness by analyzing images of coated surfaces captured during inspection. While primarily used for defect detection, AOI can provide valuable thickness information.
Each method has advantages and limitations, and the choice of equipment depends on factors such as coating material, substrate type, required accuracy, and cost considerations. Combining multiple techniques may offer comprehensive insights into conformal coating thickness and quality.
How does the substrate material influence conformal coating thickness measurement?
The substrate material plays a significant role in conformal coating thickness measurement due to its influence on the measurement technique, accuracy, and potential challenges encountered during the process. Several factors related to the substrate material affect the measurement of coating thickness:
- Surface Roughness: Substrate materials with rough surfaces can affect the accuracy of specific measurement techniques, such as optical methods or non-contact probes. Irregularities on the substrate surface may cause variations in readings or difficulties in achieving consistent contact between the measurement device and the surface.
- Reflectivity: Substrate materials with different levels of reflectivity can affect optical measurement techniques, such as infrared reflectance or optical profilers. Highly reflective substrates may interfere with light penetration or cause specular reflection, impacting the accuracy of thickness measurements.
- Material Compatibility: Some measurement techniques may be influenced by the material properties of the substrate, such as its conductivity or magnetic permeability. For example, eddy current thickness gauges are sensitive to the electrical conductivity of the substrate material, which can affect their accuracy on conductive substrates.
- Substrate Composition: Variations in substrate composition, such as the presence of metallic additives or composite materials, can introduce complexities in thickness measurement. Different materials may interact differently with measurement signals, affecting the interpretation of results.
- Substrate Thickness: The thickness of the substrate itself can affect the penetration depth or resolution of specific measurement techniques. Thicker substrates may require measurement parameter adjustments to ensure accurate coating thickness determination.
- Substrate Geometry: The shape and geometry of the substrate can influence the accessibility of measurement points and the applicability of specific techniques. Complex or irregular shapes may pose challenges for contact-based measurement methods or require specialized equipment for accurate measurements.
Considering these factors, it’s essential to select measurement techniques and equipment that are compatible with the specific characteristics of the substrate material. Calibration procedures may also need to be adjusted to account for substrate-related variables and ensure reliable thickness measurements in conformal coating applications.
What are the advantages and disadvantages of contact-based measurement methods?
Contact-based measurement methods offer several advantages and disadvantages, depending on the context of their application.
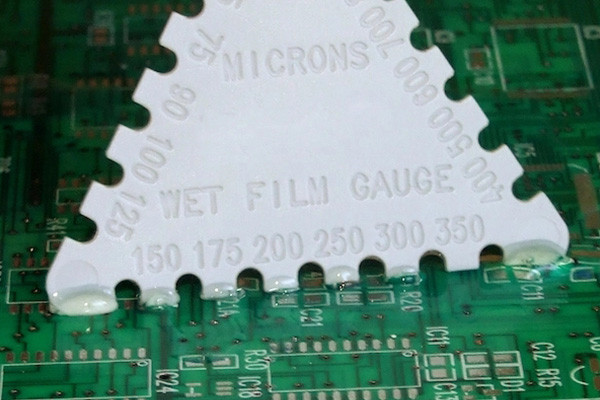
Advantages:
- Accuracy: Contact-based measurements often provide high accuracy because they directly interact with the measured object. This ensures precise data collection, which is critical in engineering, manufacturing, and metrology fields.
- Direct Feedback: These methods offer immediate feedback, allowing real-time adjustments or corrections during measurement. This instantaneous feedback can enhance the efficiency and quality of production processes.
- Broad Applicability: Contact-based measurement tools can be used across various industries and applications, from quality control in manufacturing to medical diagnostics. Their versatility makes them indispensable in many fields.
- Cost-Effectiveness: In some cases, contact-based measurement tools can be more cost-effective than non-contact methods, particularly for tasks requiring high precision, but the expense of non-contact equipment is prohibitive.
Disadvantages:
- Potential Damage: Contact-based methods involve physical interaction with the measured object, which can lead to damage or deformation, especially for delicate or sensitive materials. This limits their use in specific applications where preserving the object’s integrity is paramount.
- Limited Speed: Contact-based measurements may be slower than non-contact methods, mainly when dealing with complex surfaces or large volumes of data. This can impact productivity in time-sensitive environments.
- Surface Effects: Certain materials or surface conditions may interfere with contact-based measurements, leading to inaccuracies or inconsistencies. Surface roughness, lubrication, or contamination can affect the reliability of results.
- Operator Skill Dependency: Contact-based measurement techniques often require skilled operators to ensure accurate readings. Improper handling or calibration can introduce errors, necessitating training, and expertise, which can add to operational costs.
- Restricted Accessibility: Some objects or areas may be challenging to access with contact-based probes or sensors, limiting their applicability in specific scenarios, such as measuring internal features or components within complex assemblies.
While contact-based measurement methods offer high accuracy and versatility, they also pose challenges related to potential damage, speed limitations, surface effects, operator skill dependency, and accessibility constraints. Understanding these advantages and disadvantages is crucial for selecting the most suitable measurement approach for specific applications.
How does the ambient environment affect conformal coating thickness measurement?
Conformal coating thickness measurement is critical to ensuring the reliability and performance of electronic components, especially in industries like aerospace, automotive, and electronics manufacturing. The ambient environment plays a significant role in this measurement process, influencing factors such as coating application, drying/curing, and subsequent measurement accuracy.
- Temperature and Humidity: Ambient temperature and humidity levels can affect the viscosity of the conformal coating material during application. Higher temperatures can lower viscosity, potentially leading to thinner coating application if not adequately controlled. Conversely, lower temperatures can increase viscosity, resulting in thicker coatings. Similarly, humidity can affect drying or curing times, impacting coating thickness measurement.
- Airflow and Contaminants: Airflow in the ambient environment can influence the application of the coating material and its subsequent drying/curing process. High airflow may cause uneven coating thickness due to material displacement, while contaminants in the air could lead to imperfections or irregularities in the coating layer. Both factors can affect the accuracy of thickness measurements.
- Substrate Material and Surface Condition: The substrate material and its surface condition can interact with the conformal coating material differently based on environmental conditions. For example, variations in temperature and humidity can cause substrate expansion or contraction, potentially affecting coating adhesion and thickness uniformity.
- Measurement Technique Sensitivity: The method used for thickness measurement (e.g., optical, ultrasonic, mechanical) may be sensitive to environmental conditions. For instance, ambient lighting conditions could influence optical measurement techniques, while ultrasonic methods might be affected by temperature variations that alter the speed of sound in the material.
- Calibration and Standardization: Environmental factors can impact the calibration and standardization of thickness measurement equipment. Changes in ambient conditions may necessitate recalibration to ensure accurate readings, wildly if the environment significantly deviates from the conditions under which the equipment was calibrated.
The ambient environment plays a crucial role in conformal coating thickness measurement due to its influence on coating application, drying/curing processes, substrate characteristics, measurement technique sensitivity, and equipment calibration. Understanding and controlling these environmental factors are essential for achieving accurate and reliable thickness measurements in electronic component manufacturing.
Are there any considerations specific to measuring conformal coating thickness on irregular surfaces?
Measuring conformal coating thickness on irregular surfaces presents unique challenges that require careful consideration to ensure accurate results. Here are some key considerations:
- Surface Variation: Irregular surfaces may have varying levels of roughness or curvature, making it difficult to obtain consistent measurements. Selecting a measurement technique that can accommodate these variations and provide reliable data across the entire surface is essential.
- Measurement Technique: Traditional measurement techniques like contact-based methods (e.g., micrometers) may not be suitable for irregular surfaces due to the inability to maintain consistent contact across the entire surface. Non-contact methods such as optical profilometry or laser scanning offer better adaptability to surface irregularities.
- Calibration: Calibration is crucial to ensure the accuracy of measurements, especially on irregular surfaces where variations can significantly affect results. Calibration should be performed using standards with similar surface characteristics to those measured to account for differences in reflectivity, roughness, and curvature.
- Data Interpretation: The interpretation of measurement data becomes more complex on irregular surfaces. Software algorithms must be adapted for surface variations and provide meaningful insights into coating thickness distribution. Statistical analysis can help identify trends and outliers in the data.
- Accessibility: Accessibility to all irregular surface areas may be challenging, particularly in intricate or confined spaces. Consideration should be given to selecting measurement equipment and techniques that allow adequate access to the entire surface without compromising accuracy.
- Reproducibility: Reproducibility of measurements is essential for quality control and process optimization. Standardized procedures should be developed and followed consistently to ensure repeatable results, even on irregular surfaces.
- Environmental Factors: Environmental conditions such as temperature, humidity, and ambient lighting can impact measurement accuracy, particularly for non-contact methods. Controlling these factors or compensating for their effects during measurements is essential for reliable results.
Measuring conformal coating thickness on irregular surfaces requires a tailored approach for surface variation, appropriate measurement techniques, meticulous calibration, thorough data interpretation, accessibility considerations, attention to reproducibility, and control of environmental factors. By addressing these considerations, manufacturers can ensure accurate and reliable measurements for quality assurance purposes.
What are the key parameters to consider when selecting a measurement method for conformal coating thickness?
When selecting a measurement method for conformal coating thickness, several vital parameters need to be considered to ensure accurate and reliable results:
- Accuracy: The measurement method should provide accurate results within the desired tolerance level. This requires calibration and verification against known standards to ensure precision.
- Resolution: The method should offer sufficient resolution to detect slight variations in coating thickness, especially for thin films or when precise control is required.
- Non-destructiveness: Non-destructive measurement methods are preferred to avoid damaging the coated substrate. Optical or eddy current methods are commonly used for non-destructive measurement.
- Substrate Material: Consider the substrate’s coated material, as some measurement techniques may be better suited for specific materials. For example, magnetic induction methods may not be suitable for non-metallic substrates.
- Coating Material: Different measurement techniques may be ideal for particular types of conformal coatings, such as acrylics, silicones, or urethanes. Ensure the selected method is compatible with the coating material.
- Surface Profile: The surface profile of the substrate can affect measurement accuracy. Techniques that can accommodate irregular surfaces or roughness variations are advantageous.
- Speed: Consider the required measurement speed for the specific application. Some methods offer rapid measurements suitable for high-throughput production environments, while others may be slower but more accurate.
- Operator Skill: The complexity of the measurement method and the skill required to operate it should be considered. Choose a method that aligns with the available expertise of operators.
- Environmental Conditions: Ensure the measurement method can operate effectively in the environmental conditions present in the production environment, including temperature, humidity, and cleanliness.
- Cost: Evaluate the equipment, maintenance, and operation costs associated with each measurement method. Balancing cost with performance requirements is essential for selecting the most cost-effective solution.
By carefully considering these parameters, manufacturers can select the most suitable measurement method for conformal coating thickness, ensuring quality control and compliance with specifications in various production environments.
How can automated measurement systems improve efficiency in conformal coating thickness measurement?
Automated measurement systems offer significant advantages in conformal coating thickness measurement, enhancing efficiency through precision, speed, and consistency. These systems utilize advanced technology to streamline the measurement process, providing several key benefits:
- Accuracy and Precision: Automated measurement systems employ sophisticated sensors and algorithms to ensure precise coating thickness measurements. These systems can achieve consistently accurate results by eliminating human error and variability, which is crucial for meeting quality standards and ensuring product reliability.
- Speed: Automated systems can measure coating thickness much faster than manual methods. With rapid scanning capabilities, these systems can swiftly assess multiple areas of a PCB or component, significantly reducing inspection time and increasing throughput in production lines. This speed enables manufacturers to optimize their workflow and effectively meet tight deadlines.
- Data Analysis: Automated systems often come equipped with software that captures thickness measurements and facilitates data analysis and interpretation. This capability allows for real-time monitoring of coating quality, identification of trends or anomalies, and prompt corrective action if deviations from specifications are detected. Analytical insights these systems provide contribute to process optimization and continuous improvement efforts.
- Non-destructive Testing: Many automated measurement systems utilize non-destructive testing techniques, such as eddy current or ultrasonic measurement methods. These techniques allow for the assessment of coating thickness without causing damage to the substrate or the coating itself. Non-destructive testing is precious in industries where preserving the integrity of the product is essential, such as aerospace or electronics manufacturing.
- Integration with Production Systems: Automated measurement systems can be seamlessly integrated into existing production lines, interfacing with other manufacturing equipment and control systems. This integration enables automated feedback loops, where measurement data can inform real-time adjustments to coating application processes, ensuring consistent quality and minimizing material waste.
Automated measurement systems offer a comprehensive solution for improving conformal coating thickness measurement efficiency. By combining accuracy, speed, data analysis capabilities, non-destructive testing methods, and integration with production systems, these systems enable manufacturers to enhance product quality, increase throughput, and optimize their manufacturing processes.
Can conformal coating thickness be accurately measured on transparent substrates?
Conformal coating thickness measurement on transparent substrates presents unique challenges due to the inherent optical properties of the substrate and coating material. Traditional methods like optical microscopy or profilometry struggle to accurately measure transparent coatings without interference from substrate reflections or refraction effects. However, several techniques can be employed to overcome these challenges and achieve accurate measurements.
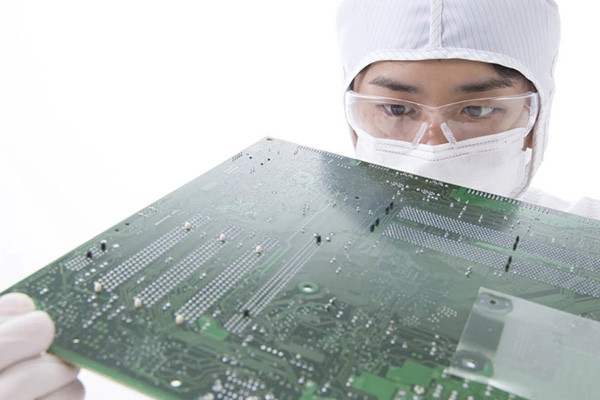
One approach is spectroscopic ellipsometry, which utilizes the interaction of polarized light with the coating to determine its thickness and optical properties. Ellipsometry can provide precise coating thickness measurements on transparent substrates with minimal interference from substrate effects by analyzing the changes in the polarization state of light reflected from the substrate-coating interface.
Another method is interferometry, mainly white light or coherence scanning interferometry (CSI). These techniques use interference patterns generated by light reflection from the substrate-coating interface to determine coating thickness. By analyzing the interference fringes, interferometry can measure the thickness of transparent coatings with high precision, regardless of substrate transparency.
Furthermore, optical coherence tomography (OCT) can be employed for non-destructive and high-resolution imaging of coating thickness on transparent substrates. OCT utilizes low-coherence interferometry to capture cross-sectional images of the coating-substrate interface, enabling accurate coating thickness measurement even on optically transparent substrates.
Alternatively, confocal microscopy offers another solution for measuring coating thickness on transparent substrates. Confocal microscopy can generate high-resolution images and precisely measure coating thickness while minimizing interference from substrate effects by selectively focusing on different depths within the coating.
While measuring conformal coating thickness on transparent substrates poses challenges, various techniques such as spectroscopic ellipsometry, interferometry, optical coherence tomography, and confocal microscopy offer practical solutions for achieving accurate measurements with high precision and minimal substrate interference. These methods are essential for ensuring the quality and reliability of conformal coatings in various transparent substrate applications.
What are the consequences of inadequate conformal coating thickness?
Conformal coating is a protective layer applied to electronic circuit boards to safeguard them against environmental factors such as moisture, dust, chemicals, and temperature fluctuations. The thickness of this coating is critical for its effectiveness in providing protection. Inadequate conformal coating thickness can lead to several consequences:
- Insufficient Protection: The primary purpose of conformal coating is to provide a barrier between sensitive electronic components and external environmental factors. If the coating thickness is inadequate, it may not effectively shield the components from moisture, dust, or other contaminants. This can result in reduced reliability and lifespan of the electronics.
- Corrosion and Oxidation: Without adequate thickness, the coating may fail to prevent moisture ingress, leading to corrosion of metal components on the circuit board. Corrosion can cause electrical shorts, degraded performance, and, ultimately, device failure. Oxidation of exposed metal traces can also occur, leading to poor electrical connectivity and signal integrity issues.
- Electrical Failures: Incomplete coverage due to insufficient coating thickness can result in electrical shorts or leakage currents between adjacent conductive traces. These shorts can lead to malfunctions, intermittent failures, or permanent damage to the circuitry. Additionally, inadequate insulation can compromise the dielectric properties of the coating, affecting the electrical performance of the device.
- Reduced Reliability: Electronic devices operating in harsh environments, such as automotive or aerospace applications, rely heavily on conformal coatings to ensure reliability. Inadequate thickness compromises this reliability, increasing the risk of premature failures and costly maintenance or recalls.
- Environmental Compliance Issues: Many industries have regulations regarding the environmental impact of electronic devices, including restrictions on hazardous substances. Inadequate conformal coating thickness may lead to non-compliance with these regulations, potentially resulting in legal consequences, fines, or damage to the brand’s reputation.
- Impact on Warranty: Manufacturers often provide electronic product warranties, guaranteeing performance and reliability within specified conditions. Inadequate conformal coating thickness can void these warranties if failures occur due to environmental damage that could have been prevented with proper coating.
Inadequate conformal coating thickness can compromise electronic devices’ reliability, performance, and longevity, leading to various operational issues, safety concerns, and financial implications for manufacturers and end-users alike. Thus, ensuring proper coating thickness is crucial in maintaining the integrity and functionality of electronic assemblies.
How can one ensure calibration accuracy in conformal coating thickness measurement equipment?
Ensuring calibration accuracy in conformal coating thickness measurement equipment is crucial for maintaining quality control and consistency in electronic manufacturing processes. Here are some steps to ensure calibration accuracy:
- Regular Calibration Checks: Establish a schedule for regular calibration checks based on the manufacturer’s recommendations and industry standards. This frequency may vary depending on usage patterns, but typically, it’s done annually or semi-annually.
- Use Certified Standards: Utilize certified coating thickness standards that are traceable to national or international standards. These standards provide known reference points for calibration and verification.
- Calibration Procedure Standardization: Develop a standardized calibration procedure that outlines step-by-step instructions for calibrating the equipment. This ensures consistency and minimizes errors in the calibration process.
- Qualified Personnel: Assign trained and qualified personnel to perform calibration procedures. Proper training ensures that technicians understand the calibration process and can execute it accurately.
- Documentation and Records: Maintain detailed records of calibration activities, including dates, results, and any adjustments made during calibration. Documentation provides a history of equipment performance and helps identify trends or issues.
- External Calibration Services: Consider utilizing external calibration services provided by accredited laboratories. These services offer independent verification and ensure compliance with relevant standards.
- Environmental Controls: Control ecological factors such as temperature and humidity during calibration to minimize potential sources of error. Fluctuations in environmental conditions can impact measurement accuracy.
- Instrument Care and Maintenance: Keep the measurement equipment clean and properly maintained to ensure optimal performance. Regularly inspect equipment for wear or damage that could affect calibration accuracy.
- Verification Checks: Conduct periodic verification checks between calibrations to ensure the equipment performs within acceptable tolerances. This provides additional assurance of measurement accuracy between formal calibration intervals.
- Stay informed about updates or revisions to calibration standards and best practices in conformal coating thickness measurement. Keeping abreast of industry developments ensures that calibration procedures remain current and effective.
By following these steps, manufacturers can maintain calibration accuracy in conformal coating thickness measurement equipment, ensuring consistent quality and reliability in electronic manufacturing processes.
What role does operator skill play in accurate conformal coating thickness measurement?
Operator skill plays a significant role in ensuring accurate conformal coating thickness measurement. While the equipment itself may be precise, the operator’s proficiency in using the equipment correctly and interpreting the results accurately is paramount. Here’s how operator skill influences measurement accuracy:
- Proper Equipment Setup:Skilled operators know how to set up the equipment correctly, including calibrating it to the appropriate standards and ensuring that environmental conditions are conducive to accurate measurements. They understand the importance of proper alignment and configuration to minimize errors.
- Technique and Consistency:Operators with experience develop reliable techniques for consistently applying the measurement probe or sensor to the coated surface. Consistent technique reduces variability in measurements and improves overall accuracy. They know how to maintain a steady hand and apply consistent pressure during measurements.
- Interpretation of Results:Skilled operators can accurately interpret the measurements obtained from the equipment. They understand the significance of deviations from the target thickness and can identify potential issues such as uneven coating, voids, or excessive thickness. Their ability to distinguish between acceptable variations and defects ensures that appropriate action can be taken to maintain quality standards.
- Troubleshooting and Problem-Solving:In cases where measurements deviate from expected values, skilled operators can troubleshoot potential causes and take corrective actions. Whether it’s adjusting equipment settings, investigating process parameters, or identifying defects in the coating process, their problem-solving skills are essential for maintaining accuracy and preventing quality issues.
- Training and Continuous Improvement:Training and skill development are crucial for operators to stay updated on the latest techniques, equipment advancements, and industry best practices. Regular training sessions ensure that operators remain proficient in using the measurement equipment effectively and accurately.
- Documentation and Reporting:Skilled operators understand the importance of documenting measurement results accurately and comprehensively. They maintain detailed records of measurements, including any relevant observations or deviations from specifications. Clear and thorough documentation facilitates traceability and enables effective communication with stakeholders.
Operator skill directly impacts the accuracy of conformal coating thickness measurement by influencing equipment setup, measurement technique, result interpretation, troubleshooting ability, training, and documentation practices. Investing in operator training and skill development is essential for ensuring consistent and reliable measurement results in electronic manufacturing processes.
Are there any emerging technologies for measuring conformal coating thickness?
Conformal coating thickness measurement is crucial in electronics manufacturing industries, where a conformal coating protects circuit boards from environmental factors like moisture, dust, and chemicals. Traditional methods, such as manual inspection or destructive testing, are time-consuming and can damage the board. Emerging technologies offer non-destructive, precise, and efficient solutions for measuring conformal coating thickness.
- Optical Coherence Tomography (OCT): Originally developed for medical imaging, OCT now finds applications in industrial settings, including electronics manufacturing. It works by sending light waves into the coating material and measuring the time the reflections return. This provides high-resolution, cross-sectional images of the coating thickness without contact, enabling precise measurements.
- Terahertz Imaging: Terahertz waves can penetrate non-conductive materials like polymers and coatings, making them suitable for measuring conformal coating thickness. Terahertz imaging systems generate images based on the time delay and intensity of reflected terahertz waves, allowing for non-contact and non-destructive thickness measurement with high resolution.
- Eddy Current Testing: Eddy current testing utilizes electromagnetic induction to detect changes in the conductivity or thickness of non-conductive coatings. This method can determine coating thickness without physical contact by measuring the impedance changes induced by eddy currents, making it suitable for delicate electronic components.
- Ultrasonic Testing: Ultrasonic waves can measure coating thickness by analyzing the time that sound waves propagate through the coating and reflect. Advanced ultrasonic techniques, such as multi-frequency and phased array systems, enhance accuracy and resolution for conformal coating thickness measurement.
- Laser Scanning Confocal Microscopy (LSCM): LSCM offers high-resolution, three-dimensional imaging capabilities, enabling precise measurement of conformal coating thickness with sub-micron accuracy. By scanning the surface with a focused laser beam and analyzing the reflected light, LSCM provides detailed thickness profiles without damaging the coating or substrate.
These emerging technologies are revolutionizing conformal coating thickness measurement by offering non-destructive, precise, and efficient solutions, ultimately improving quality control and reliability in electronics manufacturing processes. As these technologies continue to advance, they are likely to become more accessible and integrated into industrial workflows, further enhancing efficiency and accuracy in coating thickness measurement.
How do I interpret the results obtained from conformal coating thickness measurement?
Interpreting conformal coating thickness measurement results is crucial for ensuring product quality and reliability in electronics manufacturing. Here’s a guide to interpreting these results:
- Compliance with Specifications: Compare the measured thickness with the requirements outlined in product specifications or industry standards. Ensure that the measured thickness falls within the acceptable range to meet the desired level of protection and performance.
- Uniformity Across the Surface: Examine the coating thickness distribution across the entire surface of the component or circuit board. Consistent thickness ensures uniform protection against environmental factors. Deviations or unevenness in thickness may indicate issues with the coating process, such as improper application or substrate preparation.
- Localized Thickness Variations: Identify localized areas with significantly thicker or thinner coatings. These variations could result from process irregularities, substrate features, or coating defects. Investigate the root causes of these variations to address potential quality issues and ensure uniform protection across the entire surface.
- Impact on Functionality: Consider the functional implications of the measured coating thickness. Thicker coatings may provide enhanced protection but can also lead to interference with component functionality, especially in high-frequency applications. Thinner coatings may compromise protection but can be advantageous for heat dissipation or component clearance.
- Correlation with Performance: Evaluate the correlation between coating thickness and product performance, such as reliability, durability, and resistance to environmental stressors. Conduct performance testing to assess how variations in coating thickness affect product functionality and longevity under real-world conditions.
- Feedback for Process Optimization: Use the thickness measurement results as feedback to optimize the conformal coating process. Adjust process parameters, such as spray pressure, nozzle distance, or curing conditions, to achieve the desired thickness uniformity and consistency.
- Documentation and Traceability: Document the measurement results and relevant parameters such as measurement location, date, and equipment used. Establish traceability to track changes over time and ensure consistency in quality control practices.
By carefully interpreting conformal coating thickness measurement results, manufacturers can identify potential issues, optimize processes, and ensure that electronic components receive adequate protection against environmental hazards while maintaining optimal functionality and performance.
What are the best practices for maintaining consistency in conformal coating thickness measurement?
Consistency in conformal coating thickness measurement is critical for ensuring product quality and reliability in electronics manufacturing. Here are some best practices to achieve this:
- Standard Operating Procedures (SOPs): Develop comprehensive SOPs for conformal coating application and thickness measurement. Clearly outline the steps for coating application, measurement techniques, equipment calibration, and data recording procedures.
- Training and Certification: Ensure that coating application and measurement personnel are adequately trained and certified. Training should cover proper equipment handling, adherence to SOPs, and recognition of common issues affecting coating thickness.
- Calibration and Maintenance of Equipment: Regularly calibrate and maintain coating thickness measurement equipment to ensure accuracy and reliability. This includes verifying calibration standards, performing routine maintenance, and promptly addressing equipment malfunctions.
- Quality Control Checks: Implement regular quality control checks throughout the coating process to verify consistency. This may involve conducting spot checks during coating application, inspecting coated samples at various stages, and verifying thickness measurements against predetermined standards.
- Utilize Automated Measurement Systems: Consider utilizing automated measurement systems to improve consistency and accuracy in coating thickness measurement. These systems can reduce human error, provide real-time data analysis, and enhance efficiency.
- Environmental Controls: Maintain consistent ecological conditions (e.g., temperature, humidity) during coating application and measurement to minimize variability in results. Fluctuations in environmental factors can impact coating viscosity and drying rates, affecting thickness uniformity.
- Data Analysis and Trend Monitoring: Regularly analyze coating thickness data and monitor trends over time to identify deviations or inconsistencies. Implement corrective actions as necessary to address root causes and prevent issues from recurrence.
- Documentation and Traceability: Maintain detailed records of coating application and thickness measurement data, including batch information, process parameters, and inspection results. This documentation enables traceability and facilitates troubleshooting in case of quality issues.
- Continuous Improvement: Foster a culture of constant improvement by actively seeking feedback, conducting regular reviews of processes, and implementing corrective actions to address identified areas for enhancement.
By adhering to these best practices, manufacturers can enhance consistency in conformal coating thickness measurement, improving product quality, reliability, and customer satisfaction.
Conclusion:
Accurate measurement of conformal coating thickness is imperative for maintaining the integrity and reliability of electronic assemblies. Professionals can ensure optimal performance and longevity of coated components by understanding various measurement methods, equipment considerations, and industry standards. Continuous improvement in measurement techniques will further enhance the effectiveness of conformal coating applications in safeguarding electronic devices against environmental stresses.
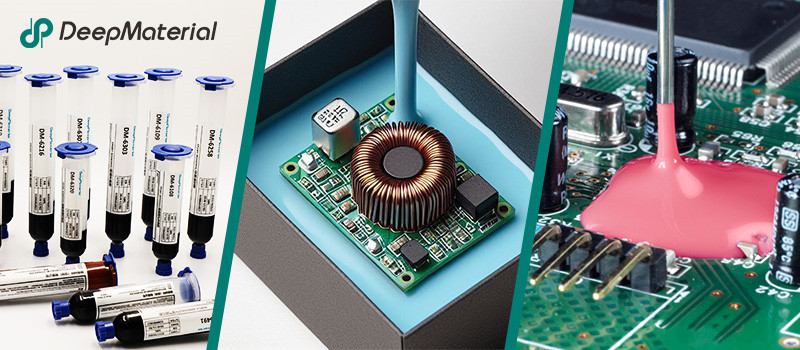
About DeepMaterial
DeepMaterial is a trusted supplier of encapsulant materials that are used in electronics manufacturing worldwide. From chip on board encapsulants such as glob top material to conformal coatings, underfills, low pressure molding, and potting solutions, DeepMaterial offers a full range of circuit board protection materials that effectively protect circuit boards while help reduce costs. More…Deepmaterial is a the manufacturer of epoxy adhesives including hardeners, metalbond, and metal filled resins. Structural, toughened medium viscosity, and non-sag adhesives are also offered. Some adhesives are resistant to thermal shock, chemical, vibration dampening, and impact. Suitable for metals, plastics, wood, and ceramics. Serves electronics, aerospace, automotive, tooling, marine, and construction industries. REACH and RoHS compliant. FDA approved. UL listed. Meets military specifications. We are the one of best adhesive manufacturers in China.
Blogs & News
Potting compounds are at the frontline of electronics assembly, delivering effective protection in challenging environmental conditions while improving mechanical strength and offering high electric insulation. Used within a variety of industries, electrical potting compounds are found within a broad range of consumer electronics, as well as used in applications across the automotive, aerospace, and other industries where electronic assemblies are prevalent.
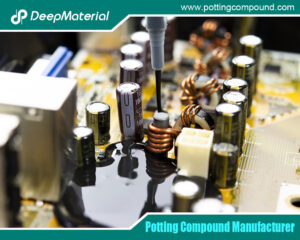
Potting Compound for PCB
Potting Compound for PCB A potting compound is a liquid or semi-liquid material that is poured or injected over a PCB or electronic assembly, then
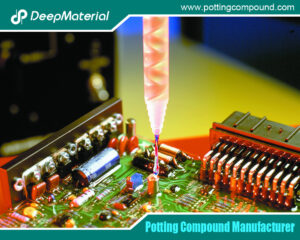
In – depth Analysis of the Curing Characteristics of Electronic Potting Compounds
In – depth Analysis of the Curing Characteristics of Electronic Potting Compounds Electronic potting compounds play a vital role in the electronics industry. They can
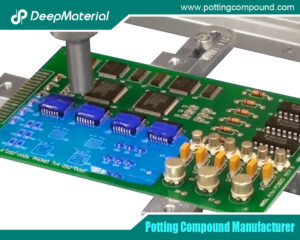
A Comprehensive Analysis of the Environmental Performance of Encapsulating Materials: From Regulations to Practices
A Comprehensive Analysis of the Environmental Performance of Encapsulating Materials: From Regulations to Practices In modern industrial manufacturing, encapsulating materials are widely used in numerous

A Comprehensive Analysis of PCB Encapsulation Quality Inspection: Innovative Application of Non-Destructive Testing Technologies
A Comprehensive Analysis of PCB Encapsulation Quality Inspection: Innovative Application of Non-Destructive Testing Technologies In the field of electronic manufacturing, the encapsulation process of printed
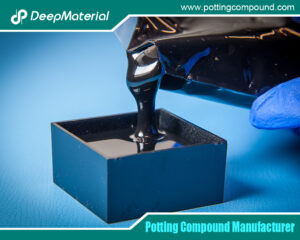
Analysis of the Improvement of the Seismic and Impact Resistance Performance of PCB by Encapsulation
Analysis of the Improvement of the Seismic and Impact Resistance Performance of PCB by Encapsulation During the operation of electronic devices, the PCB (Printed Circuit
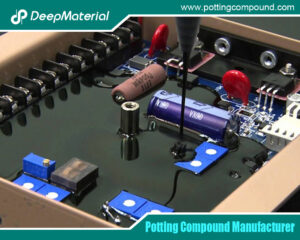
A Comprehensive Guide to Evaluating the Reliability of Encapsulation Materials for Encapsulated PCBs
A Comprehensive Guide to Evaluating the Reliability of Encapsulation Materials for Encapsulated PCBs In modern electronic devices, the printed circuit board (PCB) plays a central