Transparent Potting Compound
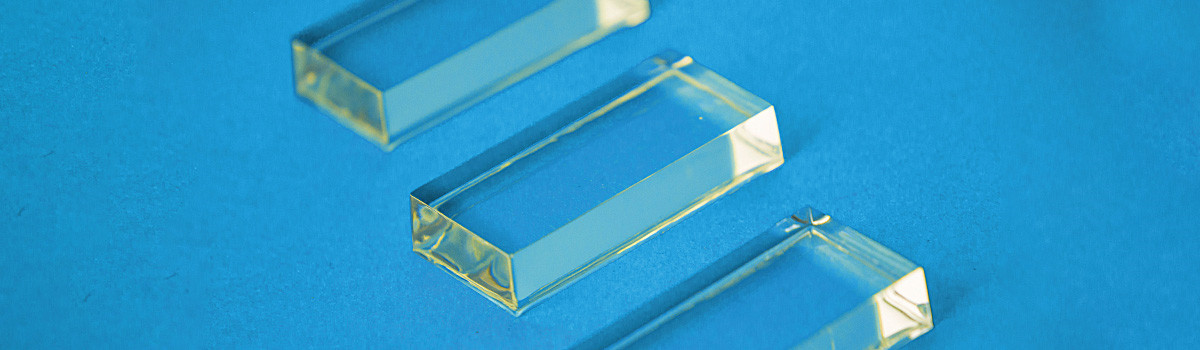
Transparent potting compounds are vital materials used in various industries for encapsulating and protecting electronic components. These compounds provide insulation, environmental protection, and mechanical support while allowing visibility to the components they encase. This category delves into the diverse aspects of transparent potting compounds, including their composition, applications, benefits, and considerations for selection.
Table of Contents
ToggleWhat is a transparent potting compound?
A transparent potting compound, also known as clear potting compound or transparent encapsulant, is a material used in electronics and other industries to encapsulate or protect sensitive components or assemblies. It is formulated to provide excellent protection while maintaining transparency, allowing for visual inspection of the encapsulated parts.
These compounds are typically made from synthetic resins, such as epoxy, silicone, or polyurethane, blended with additives to achieve the desired properties. The primary purpose of a transparent potting compound is to provide insulation, mechanical support, and environmental protection to delicate electronic components, such as circuit boards, sensors, LEDs, and other assemblies.
One critical characteristic of transparent potting compounds is their clarity, which allows for easy inspection of the encapsulated components without compromising their performance. This transparency is achieved through careful formulation and selection of raw materials to minimize the presence of impurities or additives that could cloud or obscure the material.
Transparent potting compounds offer several advantages over traditional opaque potting materials. First and foremost, they allow for visual inspection of components, which can be crucial for quality control, troubleshooting, and maintenance. Additionally, their optical clarity makes them suitable for applications where aesthetics are essential, such as in consumer electronics or decorative lighting.
In addition to transparency, these compounds provide excellent electrical insulation properties, thermal stability, and resistance to moisture, chemicals, and mechanical stress. This ensures the long-term reliability and performance of the encapsulated components, even in harsh operating environments.
Transparent potting compounds are available in various formulations to suit different application requirements, including cure times, thermal conductivity, flexibility, and adhesion properties. Depending on the application’s specific needs, they can be applied using multiple methods, such as casting, potting, or molding.
Overall, transparent potting compounds play a crucial role in protecting and enhancing the reliability of electronic and electromechanical devices while allowing for easy inspection and maintenance, making them indispensable in a wide range of industries.
How are transparent potting compounds different from opaque ones?
Transparent and opaque potting compounds serve similar purposes in protecting and insulating electronic components but differ significantly in their optical properties and applications.
Optical Properties: The most obvious difference lies in their optical properties. Transparent potting compounds are optically clear, allowing light to pass through with minimal distortion or obstruction. This clarity enables visual inspection of encapsulated components, making them suitable for applications where aesthetics or monitoring of internal components are essential. On the other hand, opaque potting compounds block light transmission entirely, rendering encapsulated components invisible from the outside.
Aesthetics and Design: Transparent potting compounds are often preferred in applications where the appearance of the final product matters, such as consumer electronics or decorative lighting. Their ability to maintain transparency ensures that the encapsulated components remain visible, contributing to the device’s overall aesthetics. On the other hand, opaque potting compounds are more commonly used in applications where visual appearance is not a concern, such as industrial machinery or automotive electronics.
Inspection and Maintenance: Transparent potting compounds allow visual inspection of encapsulated components without disassembly. This facilitates troubleshooting, quality control, and maintenance tasks, as technicians can quickly identify issues or anomalies within the encapsulated assembly. In contrast, opaque potting compounds necessitate removing or destroying the encapsulation material to inspect or access the internal components.
Applications: While both potting compounds provide protection and insulation, their specific applications differ. Transparent potting compounds are favored in applications where optical clarity is essential, such as LED lighting, optical sensors, or display panels. Opaque potting compounds are more commonly used in applications where visual inspection is unnecessary, and factors like cost-effectiveness, mechanical strength, or chemical resistance take precedence.
In summary, the primary difference between transparent and opaque potting compounds lies in their optical properties and the specific applications they cater to. Transparent compounds offer optical clarity and visual inspection capabilities, making them suitable for aesthetically sensitive applications. In contrast, opaque compounds prioritize functionality and protection in applications where transparency is not a concern.
What are the primary components of transparent potting compounds?
Transparent potting compounds are used extensively in electronics and electrical applications to encapsulate and protect sensitive components from environmental factors such as moisture, dust, and mechanical stresses. These compounds typically consist of several primary components carefully formulated to provide the desired properties:
Resins: Resins form the primary matrix of the potting compound, providing the bulk of its mechanical and chemical properties. Epoxy resins are commonly used due to their excellent adhesion, chemical resistance, and mechanical strength. Silicones are also famous for their flexibility and high-temperature resistance. The choice of resin depends on the application’s specific requirements, such as temperature range, flexibility, and clarity.
Hardener/Curing Agent: Potting compounds typically require a hardener or curing agent to initiate the cross-linking reaction with the resin, forming a solid, durable material. Common curing agents for epoxy resins include amines and anhydrides, while platinum-based catalysts are often used in silicone formulations. The ratio of resin to hardener is critical and must be carefully controlled to ensure proper curing and optimal material properties.
Fillers are added to potting compounds to modify their properties and improve performance. In transparent formulations, fillers are chosen for their ability to maintain optical clarity while enhancing mechanical strength, thermal conductivity, or other desired characteristics. Joint fillers include silica, glass beads, and various nano-scale materials.
Modifiers/Additives: Additional additives may be incorporated into potting compounds to impart specific properties or enhance performance. These may include UV stabilizers to prevent yellowing or degradation from prolonged exposure to sunlight, flame retardants to improve fire resistance, and adhesion promoters to ensure strong bonding to substrate surfaces.
Solvents: Some potting compounds may contain solvents to adjust viscosity for more accessible applications or to aid in the dispersion of fillers and additives. However, solvent-based formulations are becoming less common due to environmental and health concerns associated with volatile organic compounds (VOCs).
Degassing Agents: To minimize the presence of air bubbles within the cured material, degassing agents may be added to the potting compound formulation. These agents help to release trapped gases during curing, ensuring uniform and void-free encapsulation.
By carefully selecting and balancing these primary components, manufacturers can tailor transparent potting compounds to meet the specific requirements of diverse applications, ranging from delicate electronic assemblies to rugged outdoor environments.
What are the critical properties of transparent potting compounds?
Transparent potting compounds possess several fundamental properties that make them suitable for a variety of applications where optical clarity and protection of sensitive components are paramount:
Optical Clarity: The most crucial property of transparent potting compounds is their ability to maintain optical clarity. They allow light to pass through with minimal distortion, enabling visual inspection of encapsulated components without compromising their transparency. This property is essential for applications such as LED lighting, optical sensors, and displays.
Electrical Insulation: Transparent potting compounds provide excellent electrical insulation, protecting encapsulated electronic components from electrical hazards and preventing short circuits. This property is vital for maintaining the reliability and safety of electronic devices, especially in high-voltage applications.
Mechanical Strength: These compounds offer robust mechanical strength, providing structural support and protection to encapsulated components against mechanical stresses, vibrations, and impacts. This property ensures the longevity and durability of the encapsulated assembly, even in harsh operating environments.
Chemical Resistance: Transparent potting compounds resist various chemicals, including solvents, oils, and corrosive substances. This property protects encapsulated components from chemical damage and ensures the integrity of the encapsulation material over time.
Thermal Stability: These compounds maintain their properties and structural integrity over a wide temperature range, from extreme cold to high heat. They offer excellent thermal stability, efficiently dissipating heat to prevent overheating encapsulated components and ensuring reliable performance in demanding thermal environments.
Adhesion: Transparent potting compounds adhere well to various substrates, including metals, plastics, and ceramics, ensuring secure encapsulation and preventing moisture ingress or delamination. Proper adhesion is crucial for maintaining the effectiveness of the encapsulation and preventing premature failure of the encapsulated assembly.
Overall, the combination of optical clarity, electrical insulation, mechanical strength, chemical resistance, thermal stability, and adhesion makes transparent potting compounds indispensable for protecting and enhancing the reliability of sensitive electronic components in a wide range of applications.
How are transparent potting compounds applied in electronic manufacturing?
Transparent potting compounds play a crucial role in electronic manufacturing by providing protection and insulation for delicate components while maintaining optical clarity. The application process involves several key steps to ensure proper encapsulation and optimal performance:
Preparation of Components: Electronic components are cleaned and prepared to remove contaminants that could compromise adhesion or clarity before potting. This step is essential for ensuring a solid bond between the potting compound and the components’ surfaces.
Mixing: The potting compound is prepared by thoroughly mixing the resin, hardener, fillers, and additives according to the manufacturer’s instructions. Careful attention is paid to the mixing ratio to ensure proper curing and consistent material properties.
Encapsulation: The mixed potting compound is carefully poured or dispensed over the electronic components, ensuring complete coverage and encapsulation. Automated dispensing equipment may be used for precision and consistency, especially in high-volume manufacturing environments.
Degassing: To minimize the presence of air bubbles within the potting compound, the assembly may be subjected to a degassing process. This involves applying vacuum pressure to remove trapped air and ensure a uniform, void-free encapsulation.
Curing: Once encapsulated, the assembly can heal at the appropriate temperature and humidity conditions. Curing times vary depending on the specific formulation of the potting compound but typically range from several hours to overnight. The resin reacts with the hardener during curing, forming a solid, durable material.
Quality Control: After curing, the encapsulated assembly undergoes rigorous quality control checks to ensure that the potting compound has been adequately adhered to, no defects such as air bubbles or voids, and optical clarity is maintained. Samples may be subjected to mechanical, thermal, and environmental testing to verify performance under various conditions.
Finishing: Once validated, the encapsulated components may undergo additional finishing processes, such as trimming excess material or labeling, before being integrated into the final product.
Overall, transparent potting compounds offer reliable protection for electronic components while preserving optical clarity, making them indispensable in various electronic manufacturing applications, from consumer electronics to automotive and aerospace industries.
What industries commonly use transparent potting compounds?
Transparent potting compounds find applications across various industries where the protection and encapsulation of electronic components are critical while maintaining optical clarity is desirable. Some of the industries commonly utilizing transparent potting compounds include:
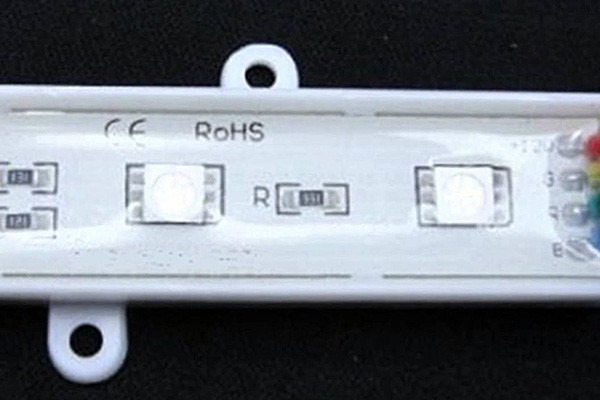
Electronics and Semiconductor: In the electronics industry, transparent potting compounds are extensively used for encapsulating sensitive electronic components such as integrated circuits (ICs), sensors, and LEDs. These compounds provide protection against moisture, dust, and mechanical stresses while allowing for visual inspection of the components.
Automotive: Transparent potting compounds play a vital role in automotive electronics, encapsulating control modules, sensors, and connectors. They offer protection against temperature fluctuations, vibration, and exposure to fluids while ensuring optical clarity for sensors and displays.
Aerospace and Aviation: The aerospace industry relies on transparent potting compounds to protect avionics systems, flight control modules, and communication equipment from harsh environmental conditions encountered during flight. These compounds provide excellent thermal stability, chemical resistance, and resistance to altitude-induced pressure changes.
Medical Devices: Transparent potting compounds are utilized in medical devices such as implantable sensors, diagnostic equipment, and monitoring devices. They provide biocompatibility, stabilizability, and optical clarity, making them suitable for applications where the visibility of internal components is essential.
Renewable Energy: In the renewable energy sector, transparent potting compounds encapsulate photovoltaic cells and modules, protecting them from moisture, UV radiation, and mechanical damage. These compounds help prolong the lifespan and enhance the performance of solar panels in outdoor environments.
Optoelectronics and Fiber Optics: Transparent potting compounds are employed in optoelectronic devices, fiber optic connectors, and optical switches to protect delicate optical components from contamination and mechanical stress. They ensure minimal signal loss and maintain optical clarity in critical optical systems.
Consumer Electronics: Transparent potting compounds are found in various consumer electronic devices such as smartphones, tablets, and wearable gadgets. They protect sensitive components against impact, moisture, and dust while allowing for aesthetic design elements like sleek, transparent casings.
Overall, transparent potting compounds offer versatile solutions for a wide range of industries where electronic components’ protection, insulation, and optical clarity are paramount.
What are the advantages of using transparent potting compounds?
Transparent potting compounds offer several advantages across various industries where the protection and encapsulation of electronic components are crucial:
Optical Clarity: One of the primary advantages of transparent potting compounds is their ability to maintain optical clarity even after encapsulation. This allows for visual inspection of components, alignment of optical elements, and operation of displays or indicators without compromising performance.
Protection: Transparent potting compounds protect electronic components against environmental factors such as moisture, dust, chemicals, and mechanical shocks. They create a barrier shielding sensitive components from damage, extending their lifespan and improving reliability.
Insulation: Potting compounds effectively insulate electronic components from electrical hazards such as short circuits, arc flashes, and electrical interference. Encapsulating conductive traces and components prevents unintended contact and improves the safety of electronic assemblies.
Mechanical Stability: Potting compounds enhance the mechanical stability of electronic assemblies by providing structural support and damping vibrations. This helps reduce the risk of damage due to mechanical stresses during handling, transportation, and operation, leading to more robust and reliable products.
Chemical Resistance: Many transparent potting compounds exhibit high chemical resistance, making them suitable for applications where exposure to harsh chemicals or solvents is expected. They can withstand prolonged exposure to various chemicals without degrading or losing their protective properties.
Thermal Management: Some transparent potting compounds offer excellent thermal conductivity, allowing for efficient heat dissipation generated by electronic components. These compounds help maintain optimal operating temperatures and prevent overheating-related failures by facilitating heat transfer away from critical components.
Ease of Application: Transparent potting compounds are available in formulations that are easy to handle and apply using various methods such as casting, potting, or encapsulation. They can be tailored to suit specific application requirements regarding viscosity, cure time, and pot life, making them versatile and convenient for manufacturing processes.
Overall, transparent potting compounds offer a combination of optical clarity, protection, insulation, and mechanical stability, making them indispensable for a wide range of electronic applications across industries. Their ability to enhance electronic assemblies’ reliability and performance contributes to advancing technology and innovation.
Are there any disadvantages or limitations to using transparent potting compounds?
While transparent potting compounds offer numerous benefits, they also have certain disadvantages and limitations that should be considered:
Cost: Transparent potting compounds can be more expensive than opaque alternatives due to the additional processing required to maintain optical clarity. The cost of materials, processing equipment, and quality control may contribute to higher overall manufacturing costs.
UV Stability: Some transparent potting compounds may exhibit limited resistance to ultraviolet (UV) radiation, leading to yellowing or degradation over time when exposed to sunlight or other UV sources. This can affect optical clarity and compromise the appearance and performance of encapsulated components.
Complexity of Formulation: Achieving and maintaining optical clarity in potting compounds requires precise formulation and processing techniques. Balancing transparency with other desirable properties, such as mechanical strength, thermal conductivity, and chemical resistance, can be challenging and may require specialized expertise.
Curing Time: Transparent potting compounds often have longer curing times than opaque formulations, especially when using epoxy resins. This extended curing time can increase production cycle times and may require additional equipment or processes to accelerate curing, such as elevated temperatures or UV curing systems.
Limited Selection: The range of transparent potting compounds available on the market may be more limited than opaque options. This can restrict the choices available to manufacturers, particularly for applications with specific performance requirements or regulatory compliance needs.
Difficulty in Repairs: Once electronic components are encapsulated with transparent potting compounds, repairing or replacing individual parts without damaging surrounding materials can be challenging. This can pose logistical challenges and increase costs in situations where repairs or upgrades are necessary.
Environmental Impact: Some transparent potting compounds contain chemicals or additives that may have ecological implications during manufacturing, use, and disposal. Careful consideration of the environmental footprint of potting compounds is essential to minimize negative impacts and ensure sustainability.
Overall, while transparent potting compounds offer unique optical clarity and protection advantages for electronic components, manufacturers must weigh these benefits against the associated costs, technical challenges, and limitations to determine the most suitable encapsulation solution for their specific application requirements.
How do transparent potting compounds protect electronic components?
Transparent potting compounds protect electronic components from various environmental factors, mechanical stresses, and electrical hazards. They provide a robust barrier around sensitive components, ensuring long-term reliability and performance. Here’s how transparent potting compounds protect electronic components:
Encapsulation: Transparent potting compounds completely encapsulate electronic components, forming a protective barrier that shields them from moisture, dust, dirt, and other contaminants. This encapsulation prevents corrosion, oxidation, and other forms of degradation that can compromise the functionality and lifespan of electronic devices.
Mechanical Protection: Potting compounds provide mechanical support and stability to electronic assemblies, reducing the risk of damage from vibration, shock, or physical impact. By encapsulating fragile components such as wires, connectors, and solder joints, potting compounds help distribute mechanical stresses evenly and prevent fatigue failure.
Insulation: Transparent potting compounds offer excellent electrical insulation properties, preventing short circuits and electrical leakage in electronic assemblies. By encapsulating conductive traces and components, potting compounds minimize the risk of electrical malfunctions and ensure the device’s and its users’ safety.
Thermal Management: Some transparent potting compounds have high thermal conductivity, allowing them to dissipate heat efficiently from electronic components. By transferring heat away from heat-generating components such as transistors, diodes, and power modules, potting compounds help maintain optimal operating temperatures and prevent overheating-related failures.
Chemical Resistance: Many transparent potting compounds resist chemicals, solvents, oils, and other harsh substances commonly encountered in industrial, automotive, and aerospace environments. This chemical resistance protects electronic components from corrosion and degradation, even in challenging operating conditions.
UV Stability: Transparent potting compounds with UV stabilizers can protect electronic components from the harmful effects of ultraviolet radiation, including yellowing, discoloration, and degradation. This UV stability ensures encapsulated components maintain their optical clarity and performance over time, particularly in outdoor or high-exposure environments.
Overall, transparent potting compounds provide comprehensive protection for electronic components, safeguarding them against environmental, mechanical, electrical, and chemical hazards. Their ability to encapsulate, insulate, dissipate heat, and resist degradation makes them indispensable for ensuring the reliability and longevity of electronic devices in various industries.
Can transparent potting compounds withstand harsh environmental conditions?
Transparent potting compounds are specifically engineered materials designed to encapsulate and protect electronic components, circuitry, or delicate devices from various environmental factors while remaining optically clear. Their ability to withstand harsh environmental conditions depends on several factors, including the compound’s composition, curing method, and intended application.
One primary consideration in assessing a potting compound’s durability is its resistance to temperature extremes. High-quality transparent potting compounds are formulated to maintain structural integrity and optical clarity across various temperatures, from extreme cold to intense heat. This thermal stability ensures that encapsulated components remain protected even in environments with significant temperature fluctuations, such as automotive engine compartments or outdoor electronic displays.
Furthermore, these compounds often exhibit excellent resistance to moisture and humidity. By forming a tight, waterproof seal around sensitive electronics, they prevent moisture ingress that could lead to corrosion, short circuits, or electrical failures. This moisture resistance is crucial for outdoor applications, marine environments, or any setting where exposure to water is a concern.
Transparent potting compounds also offer exceptional chemical resistance, shielding enclosed components from corrosive substances such as solvents, oils, fuels, and acids. This feature is particularly valuable in industrial settings, where electronic equipment may encounter harsh chemicals during operation or maintenance procedures.
UV resistance is another important consideration, especially for outdoor applications exposed to sunlight. Premium transparent potting compounds are engineered to resist yellowing, clouding, or degradation when exposed to UV radiation over extended periods, ensuring long-term optical clarity and performance.
Additionally, these compounds may be formulated to meet specific industry standards for flame retardancy, electrical insulation, and mechanical shock absorption, further enhancing their suitability for demanding environments.
In summary, transparent potting compounds can withstand harsh environmental conditions, protecting against temperature extremes, moisture, chemicals, UV radiation, and other detrimental factors. Their advanced formulations and tailored properties make them indispensable for safeguarding sensitive electronics in various applications, from automotive and aerospace to marine and outdoor signage.
What factors should be considered when selecting a transparent potting compound?
When selecting a transparent potting compound, several crucial factors should be considered to ensure optimal performance and compatibility with the intended application:
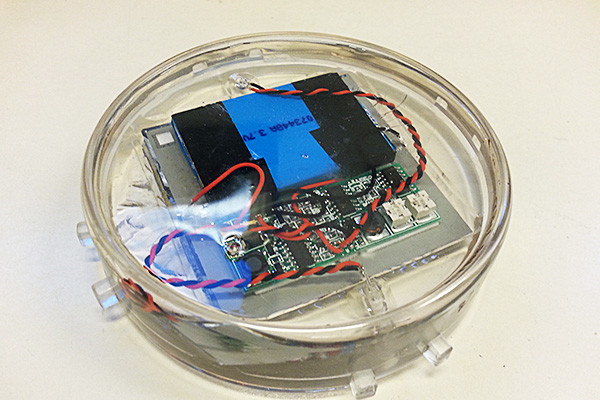
Optical Clarity: The primary requirement for transparent potting compounds is maintaining optical clarity after curing. Ensure the compound does not introduce haze, yellowing, or cloudiness that could impair visibility or performance.
Chemical Compatibility: Evaluate the compound’s resistance to chemicals commonly encountered in the application environment. Consider exposure to solvents, fuels, oils, acids, and other potentially corrosive substances to prevent degradation or failure of encapsulated components.
Temperature Resistance: Determine the temperature range the potting compound will be exposed to during operation and storage. Select a suitable temperature-resistant compound to maintain its structural integrity and optical clarity under these conditions.
Moisture Resistance: Assess the compound’s ability to prevent moisture ingress, which can lead to corrosion, electrical shorts, or component failure. Look for compounds with high moisture resistance to protect sensitive electronics in humid or wet environments.
UV Stability: For outdoor applications or settings with exposure to sunlight, choose a potting compound with excellent UV stability. This prevents yellowing, discoloration, or degradation of the material over time, ensuring long-term optical clarity and performance.
Mechanical Properties: Consider the compound’s mechanical properties, such as flexibility, hardness, and impact resistance. These properties should match the application’s requirements to provide adequate protection against vibrations, shocks, and mechanical stresses.
Curing Method: Evaluate the curing method required for the potting compound, whether it’s room temperature curing, heat curing, or UV curing. Ensure the chosen method aligns with the manufacturing process and equipment available.
Regulatory Compliance: Confirm that the selected potting compound complies with relevant industry standards and regulations, such as UL, RoHS, REACH, or specific certifications required for the application.
By carefully considering these factors and selecting a transparent potting compound that meets the application’s specific requirements, manufacturers can ensure reliable protection and performance for their electronic components in various environments.
How do temperature and UV exposure affect transparent potting compounds?
Temperature and UV exposure can significantly impact the performance and durability of transparent potting compounds, potentially affecting their optical clarity, mechanical properties, and overall effectiveness in protecting encapsulated components.
Temperature Effects:
Temperature extremes can influence the physical and chemical properties of transparent potting compounds:
Thermal Expansion: When exposed to temperature fluctuations, transparent potting compounds may undergo thermal expansion or contraction. If the compound’s coefficient of thermal expansion (CTE) differs significantly from that of the encapsulated components or substrate, it can lead to mechanical stress, delamination, or cracking.
Viscosity Changes: Temperature variations can alter the viscosity of potting compounds, affecting their flow characteristics during application and curing. High temperatures may lower viscosity, leading to excessive flow and potential voids, while low temperatures can increase viscosity, making dispensing and filling challenging.
Curing Properties: The curing process of transparent potting compounds is often temperature-dependent. Temperature deviations from the recommended curing conditions can impact the cure rate, final hardness, and adhesion properties of the material, potentially compromising its effectiveness as an encapsulant.
UV Exposure Effects:
UV radiation can degrade the chemical structure of transparent potting compounds, leading to several detrimental effects:
Yellowing and Discoloration: Prolonged exposure to UV radiation can cause transparent potting compounds to yellow or discolor over time. This diminishes optical clarity and indicates chemical degradation of the material, potentially compromising its mechanical and protective properties.
Reduced Mechanical Strength: UV-induced degradation can weaken the molecular bonds within the potting compound, reducing its mechanical strength, flexibility, and impact resistance. It can increase the susceptibility of encapsulated components to mechanical damage or failure under stress.
Loss of Transparency: UV exposure may cause the material to become cloudy, hazy, or opaque, diminishing its transparency and impairing the visibility of enclosed components or displays.
To mitigate the effects of temperature and UV exposure on transparent potting compounds, manufacturers may formulate materials with additives such as UV stabilizers, thermal stabilizers, and antioxidants to enhance their resistance to environmental factors. Additionally, proper design considerations, application techniques, and environmental controls can help minimize the impact of temperature and UV exposure on the performance and longevity of potting compounds.
Are there different curing methods for transparent potting compounds?
Yes, transparent potting compounds can be cured using various methods, each offering distinct advantages and suitability for different applications. The choice of curing method depends on factors such as the material’s composition, the requirements of the application, and the available manufacturing processes. Some standard curing methods for transparent potting compounds include:
Room Temperature Curing: Room temperature curing, also known as ambient temperature curing, involves allowing the potting compound to cure naturally at room temperature without needing external heat sources or specialized equipment. This method is convenient and energy-efficient, suitable for applications where elevated temperatures may be impractical or detrimental to sensitive components. However, room temperature curing may result in longer curing times compared to accelerated curing methods.
Heat Curing: Heat curing involves subjecting the potting compound to elevated temperatures to accelerate the process. This method typically requires ovens or curing chambers to maintain precise temperature control throughout the curing cycle. Heat curing offers faster cure times than room temperature, allowing for increased production throughput and shorter cycle times. It also facilitates the achievement of higher mechanical strength and improved adhesion properties in the cured material.
UV Curing: UV curing utilizes ultraviolet (UV) radiation to initiate and accelerate the curing reaction of photopolymerizable potting compounds. These compounds contain photoinitiators that react upon exposure to UV light, causing the material to cure rapidly and effectively. UV curing offers near-instantaneous cure times, making it ideal for high-speed manufacturing processes and applications requiring rapid turnaround. It also allows for precise control over curing depth and reduces energy consumption by eliminating the need for prolonged heating cycles.
Moisture Curing: Some potting compounds cure in the presence of moisture from the surrounding environment or by incorporating moisture-reactive additives into the formulation. Moisture curing offers convenience and versatility, eliminating the need for external heat sources or UV radiation. However, careful control of environmental conditions is required to ensure consistent curing performance, and it may be sensitive to variations in humidity levels.
By offering a range of curing methods, transparent potting compounds can accommodate diverse manufacturing requirements and application scenarios, providing manufacturers with flexibility and versatility in encapsulating electronic components and devices.
Can transparent potting compounds be customized for specific applications?
Yes, transparent potting compounds can be customized to meet various applications’ specific requirements and challenges, offering tailored solutions that address factors such as environmental conditions, performance criteria, and manufacturing processes. Customization options for transparent potting compounds encompass a range of aspects, including:
Chemical Composition: Manufacturers can adjust the formulation of transparent potting compounds to enhance properties such as thermal stability, UV resistance, chemical resistance, and mechanical strength. They can optimize the material’s performance for the intended application environment by selecting appropriate resin systems, additives, and modifiers.
Optical Clarity: Transparent potting compounds can be formulated to achieve different levels of optical clarity, ranging from optically clear to lightly tinted or diffused. This customization allows flexibility in matching the application’s aesthetic requirements and functional specifications, such as maintaining the visibility of indicators or displays.
Curing Characteristics: Customization of curing characteristics, including cure speed, temperature, and depth, enables transparent potting compounds to align with specific manufacturing processes and production schedules. Manufacturers can choose curing methods such as room temperature, heat, or UV curing based on the application’s requirements and constraints.
Adhesion Properties: Transparent potting compounds can be tailored to exhibit optimal adhesion to various substrates, including metals, plastics, ceramics, and glass. Customized adhesion promoters or surface treatments can be incorporated into the formulation to ensure strong bonding and reliable encapsulation of electronic components.
Regulatory Compliance: Transparent potting compounds can be customized to meet industry-specific regulatory standards and certifications, such as UL, RoHS, REACH, and FDA compliance. Manufacturers can select raw materials and additives that are approved for use in specific applications, ensuring regulatory compliance and product safety.
Overall, the ability to customize transparent potting compounds enables manufacturers to address diverse applications’ unique challenges and performance requirements, ranging from consumer electronics and automotive systems to aerospace and medical devices. By collaborating with material suppliers or leveraging in-house formulation expertise, manufacturers can develop bespoke solutions that deliver optimal performance, reliability, and durability in their target markets.
What are some examples of innovative applications of transparent potting compounds?
Innovative applications of transparent potting compounds demonstrate their versatility and ability to address unique challenges across various industries. Some examples include:
LED Lighting: Transparent potting compounds are extensively used in LED lighting applications to encapsulate LED modules, strips, and drivers. By providing optical clarity, thermal management, and protection against moisture and environmental factors, these compounds produce high-performance, long-lasting LED fixtures for architectural, automotive, and signage lighting.
Flexible Electronics: Transparent potting compounds are crucial in encapsulating flexible and stretchable electronics, including wearable devices, flexible displays, and intelligent textiles. These compounds offer flexibility, conformability, and durability, allowing electronic components to bend, stretch, and conform to curved surfaces without compromising functionality or reliability.
Solar Photovoltaics: In solar photovoltaic (PV) applications, transparent potting compounds encapsulate and protect photovoltaic cells and modules from moisture, UV radiation, and mechanical stress. By enhancing durability, weather resistance, and optical transmission, these compounds contribute to the efficiency and longevity of solar panels in terrestrial and space-based applications.
Automotive Electronics: Transparent potting compounds are employed in automotive electronics to protect control modules, sensors, and connectors from harsh operating conditions, including temperature extremes, vibration, and exposure to automotive fluids. These compounds enhance reliability, corrosion resistance, and thermal management, ensuring the performance and longevity of critical vehicle electronic systems.
Medical Devices: In medical device manufacturing, transparent potting compounds encapsulate electronic components and sensors in devices such as implantable medical devices, wearable health monitors, and diagnostic equipment. These compounds offer biocompatibility, stabilizability, and chemical resistance, meeting stringent regulatory requirements and ensuring patient safety in healthcare settings.
These examples highlight the diverse range of applications where transparent potting compounds contribute to innovation, performance, and reliability across lighting, electronics, renewable energy, automotive, and healthcare industries. By leveraging the unique properties of transparent potting compounds, manufacturers can develop innovative solutions that address evolving market needs and technological advancements.
How do transparent potting compounds contribute to product reliability?
Transparent potting compounds enhance product reliability across various industries by providing robust protection, mechanical support, and environmental resistance to encapsulated electronic components. Here’s how transparent potting compounds contribute to product reliability:
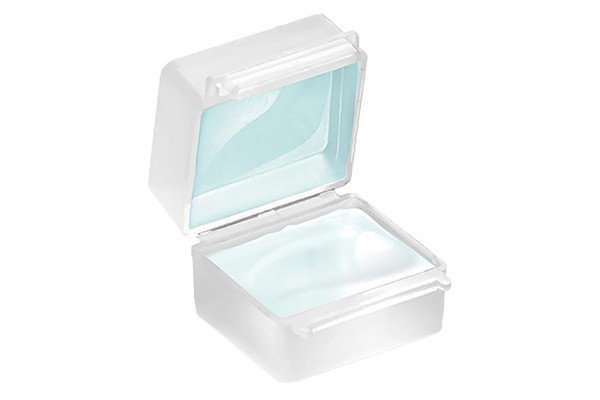
Environmental Protection: Transparent potting compounds create a protective barrier around electronic components, shielding them from moisture, dust, chemicals, and other environmental contaminants. This prevents corrosion, electrical shorts, and component degradation, ensuring consistent performance and longevity of the encapsulated devices, even in harsh operating conditions.
Mechanical Stability: By encapsulating electronic components in a solid, stable matrix, transparent potting compounds provide mechanical support and vibration damping, reducing the risk of physical damage or failure due to mechanical stress, shock, or impact. This enhances the structural integrity of the devices and minimizes the likelihood of component detachment or displacement during operation.
Thermal Management: Transparent potting compounds with high thermal conductivity help dissipate heat generated by electronic components, improving thermal management and preventing overheating. By maintaining optimal operating temperatures, these compounds prolong the lifespan of sensitive electronic devices and mitigate the risk of thermal-induced failures, such as thermal runaway or solder joint fatigue.
UV and Light Stability: UV-stable transparent potting compounds resist yellowing, discoloration, or degradation when exposed to sunlight or other sources of UV radiation. This preserves optical clarity, maintains the visibility of indicators or displays, and prevents performance degradation over time, contributing to the reliability and aesthetics of the encapsulated devices, especially in outdoor or light-sensitive applications.
Chemical Resistance: Transparent potting compounds with excellent chemical resistance protect encapsulated components from exposure to corrosive substances such as solvents, fuels, oils, and cleaning agents. This prevents chemical damage, degradation of materials, and performance deterioration, ensuring reliable operation and longevity of the devices in chemically challenging environments.
Overall, transparent potting compounds enhance product reliability by providing comprehensive protection, mechanical stability, thermal management, and resistance to environmental factors, chemicals, and UV radiation. Their use significantly reduces the risk of component failure, extends the lifespan of electronic devices, and enhances overall performance and customer satisfaction.
Are there any safety considerations associated with handling transparent potting compounds?
Yes, several safety considerations are associated with handling transparent potting compounds, primarily related to their chemical composition, handling procedures, and potential health hazards. It’s essential for personnel working with these materials to be aware of these considerations and follow appropriate safety measures to minimize risks. Some key safety considerations include:
Chemical Exposure: Transparent potting compounds may contain chemicals such as epoxy resins, hardeners, solvents, and additives, which can be hazardous if mishandled or exposed to skin, eyes, or mucous membranes. Direct contact with uncured or partially cured compounds can cause skin irritation, allergic reactions, or chemical burns. Inhalation of vapors or airborne particles may irritate the respiratory system or cause respiratory sensitization. Proper personal protective equipment (PPE), including gloves, safety goggles, and respiratory protection, should be worn when handling these materials to prevent chemical exposure.
Ventilation: Adequate ventilation is essential when working with transparent potting compounds to minimize exposure to airborne contaminants and reduce the risk of inhalation hazards. Workspaces should be well-ventilated, preferably with local exhaust ventilation or fume extraction systems, to remove vapors and airborne particles generated during mixing, dispensing, and curing processes.
Curing Reactions: During the curing process, transparent potting compounds may release heat and emit volatile organic compounds (VOCs) or other hazardous by-products. Curing should be conducted in well-ventilated areas, away from ignition sources or open flames, to prevent overheating, fire hazards, or the accumulation of flammable vapors.
Storage and Handling: Transparent potting compounds should be stored and handled according to manufacturer recommendations to maintain product integrity and minimize risks. Proper storage conditions, including temperature and humidity control, can prevent material degradation and ensure consistent performance. Containers should be tightly sealed, labeled correctly, and stored away from incompatible materials, heat sources, or direct sunlight.
Waste Disposal: Proper disposal of waste materials, including unused or expired potting compounds, mixing containers, and cleanup materials, is essential to prevent environmental contamination and comply with regulations. Waste disposal procedures should adhere to local rules and guidelines for handling hazardous chemicals and waste streams.
By addressing these safety considerations and implementing appropriate controls, organizations can minimize the risks of handling transparent potting compounds and ensure a safe working environment for the personnel involved. Training, hazard communication, and regular risk assessments are essential components of a comprehensive safety program for handling these materials.
What role do transparent potting compounds play in waterproofing electronic devices?
Transparent potting compounds are crucial in waterproofing electronic devices by providing a protective barrier that seals out moisture, liquids, and other environmental contaminants. Waterproofing is essential for electronic devices that may be exposed to water, humidity, or harsh environmental conditions, as moisture ingress can lead to corrosion, electrical shorts, and component failure. Here’s how transparent potting compounds contribute to waterproofing electronic devices:
Sealing and Encapsulation: Transparent potting compounds encapsulate electronic components, circuitry, and connectors, forming a watertight seal that protects them from moisture intrusion. The compound fills gaps, crevices, and voids within the device, ensuring complete coverage and sealing out water and other liquids.
Prevention of Corrosion: Moisture is a leading cause of corrosion in electronic devices. It can react with metal contacts, solder joints, and other conductive elements, leading to degradation and failure over time. Transparent potting compounds prevent moisture ingress, inhibiting corrosion and extending the device’s lifespan.
Enhanced Environmental Resistance: In addition to waterproofing, transparent potting compounds resist various environmental factors, including humidity, temperature extremes, chemicals, and UV radiation. This comprehensive protection ensures electronic devices remain reliable and functional in diverse operating environments, such as outdoor, automotive, marine, or industrial settings.
Maintaining Optical Clarity: Transparent potting compounds are optically clear, allowing for the visibility of indicators, displays, or LEDs on the device’s exterior. It maintains aesthetics and functionality while providing waterproofing, making these compounds suitable for applications where both optical clarity and environmental protection are critical.
Flexible Formulations: Some transparent potting compounds offer flexibility and conformability, allowing them to accommodate thermal expansion, mechanical stress, and movement within the device without compromising the seal or waterproofing properties. This flexibility ensures reliability and durability even in dynamic or rugged environments.
Overall, transparent potting compounds are essential for waterproofing electronic devices. They offer reliable protection against moisture and environmental contaminants while maintaining optical clarity and functionality. Their use enables the development of waterproof electronic devices suitable for various applications, from consumer electronics and wearables to automotive and industrial systems.
How do transparent potting compounds impact the aesthetics of electronic products?
Transparent potting compounds can significantly impact the aesthetics of electronic products, influencing their appearance, design flexibility, and overall visual appeal. Here’s how transparent potting compounds affect the aesthetics of electronic products:
Optical Clarity: One of the most notable aesthetic benefits of transparent potting compounds is their ability to maintain optical clarity. These compounds allow for the visibility of internal components, indicators, displays, and LEDs, providing a sleek and modern appearance to electronic products. The transparency of the potting compound enhances the visibility of intricate designs and adds a sense of sophistication to the product.
Sleek Design Integration: Transparent potting compounds enable seamless integration of electronic components into the product’s overall design. These compounds allow designers to create elegant, minimalist designs that highlight the technology within by encapsulating and protecting sensitive electronics without obscuring their visibility. This integration enhances the product’s aesthetic appeal and user experience.
Enhanced Product Finish: Transparent potting compounds can improve electronic products’ overall finish and aesthetics by providing a smooth, glossy surface. It enhances the tactile experience for users and contributes to the product’s perceived quality. Additionally, choosing potting compounds with different levels of transparency or tinting allows designers to achieve specific aesthetic effects, such as diffused lighting or color matching.
Customization and Branding: Transparent potting compounds offer opportunities for customization and branding. Manufacturers can incorporate logos, branding elements, or decorative features directly into the encapsulation material. This branding enhances brand recognition and adds a personalized touch to electronic products, contributing to their visual identity and marketability.
Durability and Longevity: By protecting internal components from environmental factors and mechanical damage, transparent potting compounds contribute to the long-term aesthetics of electronic products. Ensuring that components remain intact, free from corrosion or degradation, maintains the product’s appearance and functionality over time, preserving its aesthetic appeal and user satisfaction.
Transparent potting compounds play a multifaceted role in enhancing the aesthetics of electronic products. They offer optical clarity, design integration, product finish, customization options, and long-term durability. Their use allows designers to create visually stunning and technologically advanced products that captivate consumers and stand out in the marketplace.
What are the future trends in the development of transparent potting compounds?
The development of transparent potting compounds is continuously evolving to meet emerging challenges, technological advancements, and market demands. Several future trends are expected to shape the development of transparent potting compounds:
Advanced Materials: Future trends in transparent potting compounds will likely involve using advanced materials with enhanced properties, such as higher thermal conductivity, improved UV stability, and superior mechanical strength. Nanocomposite materials, incorporating nanoparticles or nanofillers, may be explored to achieve exceptional performance and tailored properties for specific applications.
Environmental Sustainability: As sustainability becomes increasingly crucial in material development, future transparent potting compounds are expected to focus on eco-friendly formulations with reduced environmental impact. This includes using renewable raw materials, bio-based resins, and recyclable or biodegradable additives, aligning with sustainability goals and regulatory requirements.
Miniaturization and Integration: With the trend towards miniaturization and integration of electronic devices, future transparent potting compounds must accommodate smaller form factors, intricate designs, and densely packed components. This may involve developing ultra-thin coatings, low-viscosity formulations, or conformal encapsulation techniques to ensure reliable protection without compromising performance or aesthetics.
Innovative and Functional Materials: Future transparent potting compounds may incorporate innovative or functional materials with additional functionalities, such as self-healing properties, sensing capabilities, or conductive properties for electromagnetic interference (EMI) shielding. These materials could enable innovative applications in intelligent electronics, IoT devices, and wearable technology, enhancing functionality and performance.
Customization and Tailored Solutions: The demand for customized solutions tailored to specific applications will drive future developments in transparent potting compounds. Manufacturers may offer customizable formulations, allowing customers to select desired properties, such as optical clarity, flexibility, or chemical resistance, to meet their applications’ unique requirements.
Digitalization and Industry 4.0: Digitalization and Industry 4.0 technologies may influence the development of transparent potting compounds through digital design, simulation, and manufacturing processes. Predictive modeling, virtual prototyping, and additive manufacturing techniques could streamline material development, accelerate innovation, and optimize performance.
Overall, the future of transparent potting compounds is characterized by advancements in materials science, sustainability, functionality, customization, and digitalization, driven by the evolving needs of electronic device manufacturers and the pursuit of technological excellence.
Conclusion: Transparent potting compounds are indispensable materials for safeguarding electronic components while offering clarity and protection. Understanding their composition, properties, and applications is crucial for industries seeking reliable encapsulation solutions. As technology advances, the evolution of transparent potting compounds continues to enhance product durability, performance, and aesthetic appeal, paving the way for innovative applications across diverse sectors.
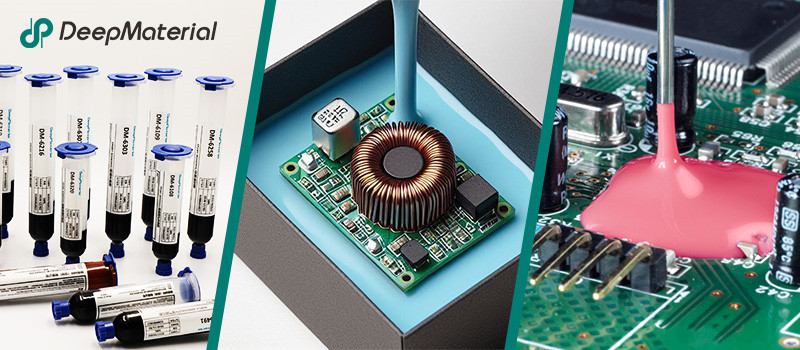
About DeepMaterial
DeepMaterial is a trusted supplier of encapsulant materials that are used in electronics manufacturing worldwide. From chip on board encapsulants such as glob top material to conformal coatings, underfills, low pressure molding, and potting solutions, DeepMaterial offers a full range of circuit board protection materials that effectively protect circuit boards while help reduce costs. More…Deepmaterial is a the manufacturer of epoxy adhesives including hardeners, metalbond, and metal filled resins. Structural, toughened medium viscosity, and non-sag adhesives are also offered. Some adhesives are resistant to thermal shock, chemical, vibration dampening, and impact. Suitable for metals, plastics, wood, and ceramics. Serves electronics, aerospace, automotive, tooling, marine, and construction industries. REACH and RoHS compliant. FDA approved. UL listed. Meets military specifications. We are the one of best adhesive manufacturers in China.
Blogs & News
Potting compounds are at the frontline of electronics assembly, delivering effective protection in challenging environmental conditions while improving mechanical strength and offering high electric insulation. Used within a variety of industries, electrical potting compounds are found within a broad range of consumer electronics, as well as used in applications across the automotive, aerospace, and other industries where electronic assemblies are prevalent.
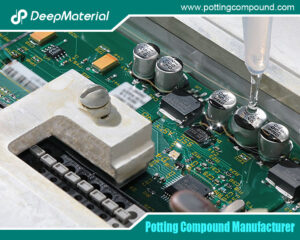
Silicone Potting Compound for Electronics
Silicone Potting Compound for Electronics In the rapidly evolving world of electronics, ensuring the reliability, durability, and performance of electronic components is paramount. One critical
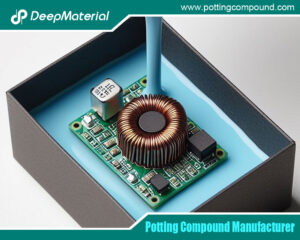
Potting Compound vs. Epoxy: A Comprehensive Comparison
Potting Compound vs. Epoxy: A Comprehensive Comparison In the world of electronics, manufacturing, and material encapsulation, two terms frequently come up: potting compounds and epoxy.
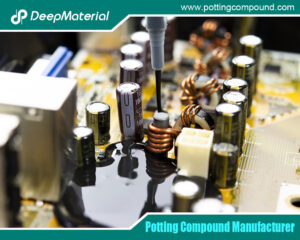
Potting Compound for PCB
Potting Compound for PCB A potting compound is a liquid or semi-liquid material that is poured or injected over a PCB or electronic assembly, then
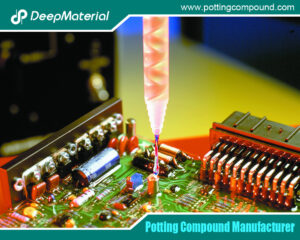
In – depth Analysis of the Curing Characteristics of Electronic Potting Compounds
In – depth Analysis of the Curing Characteristics of Electronic Potting Compounds Electronic potting compounds play a vital role in the electronics industry. They can
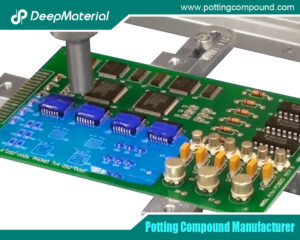
A Comprehensive Analysis of the Environmental Performance of Encapsulating Materials: From Regulations to Practices
A Comprehensive Analysis of the Environmental Performance of Encapsulating Materials: From Regulations to Practices In modern industrial manufacturing, encapsulating materials are widely used in numerous

A Comprehensive Analysis of PCB Encapsulation Quality Inspection: Innovative Application of Non-Destructive Testing Technologies
A Comprehensive Analysis of PCB Encapsulation Quality Inspection: Innovative Application of Non-Destructive Testing Technologies In the field of electronic manufacturing, the encapsulation process of printed