PCB Conformal Coating
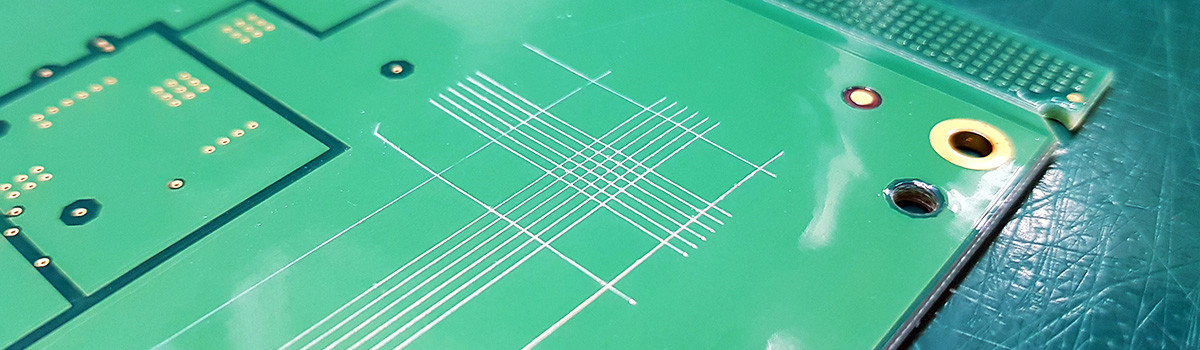
Table of Contents
TogglePCB conformal coating is a critical process in electronics manufacturing that protects printed circuit boards (PCBs) from environmental factors such as moisture, dust, chemicals, and temperature extremes. Conformal coatings are:
- Thin layers of protective material are applied to the surface of PCBs.
- Providing insulation.
- Corrosion resistance.
- Increased reliability to electronic assemblies.
This category explores various aspects of PCB conformal coating, including types of coatings, application methods, benefits, considerations, and best practices.
What is PCB conformal coating, and why is it necessary?
PCB conformal coating is a protective layer applied to printed circuit boards (PCBs) to safeguard them from environmental factors such as moisture, dust, chemicals, and temperature variations. This coating forms a thin film over the PCB’s surface, conforming to its contours and components, hence the term “conformal.”
The importance of PCB conformal coating lies in its ability to enhance the reliability, longevity, and performance of electronic devices and systems. Here’s why it’s significant:
- Environmental Protection: PCBs are often deployed in harsh environments where they can be exposed to moisture, dust, and other contaminants. Conformal coating acts as a barrier, preventing these substances from reaching sensitive components and causing corrosion, short circuits, or other forms of damage.
- Chemical Resistance: In industrial or automotive applications, PCBs may encounter chemicals such as solvents, fuels, or cleaning agents. Conformal coating provides resistance against these chemicals, ensuring the PCB functions reliably even in chemically aggressive environments.
- Electrical Insulation: Some conformal coatings offer electrical insulation properties that prevent short circuits and leakage currents. By isolating conductive traces and components, the coating helps maintain the integrity of the electrical circuitry, especially in high-voltage or high-frequency applications.
- Mechanical Protection: In addition to environmental factors, PCBs can also suffer mechanical stress from vibration, shock, or physical impact. Conformal coating adds a layer of protection, reducing the risk of mechanical damage and increasing the PCB’s durability in demanding operational conditions.
- Thermal Management: Certain conformal coatings possess thermal conductivity properties, allowing them to more effectively dissipate heat generated by electronic components. This helps maintain optimal operating temperatures, which is crucial for preventing overheating and preserving the reliability of the PCB and its components.
Overall, PCB conformal coating is vital in ensuring the robustness, reliability, and longevity of electronic devices and systems, particularly those deployed in challenging environments or subjected to demanding operational conditions. It serves as a proactive measure to mitigate potential risks and safeguard the functionality of PCBs throughout their operational lifespan.
What are the common types of conformal coatings used in PCB assembly?
Conformal coatings protect printed circuit boards (PCBs) from environmental factors such as moisture, dust, chemicals, and temperature variations. They provide a thin protective layer that conforms to the contours of the PCB, safeguarding it from potential damage. Several types of conformal coatings are commonly used in PCB assembly:
- Acrylic Resin: Acrylic conformal coatings are popular due to their excellent moisture and chemical resistance. They offer good dielectric properties and are relatively easy to apply. Acrylic coatings provide a durable protective layer that withstands temperature variations and provides good electrical insulation.
- Silicone: Silicone conformal coatings offer outstanding thermal stability and flexibility. They can endure extreme temperatures, making them suitable for harsh operating environments. Due to their viscosity, silicone coatings provide excellent moisture resistance and protection against contaminants, but they may require careful handling during application.
- Urethane: Urethane conformal coatings offer a balance between flexibility and durability. They provide good chemical resistance and mechanical protection against abrasion and impact. Urethane coatings are often used in applications requiring enhanced solvents and humidity resistance.
- Epoxy: Epoxy conformal coatings are known for their high mechanical strength and chemical resistance. They form a hard, protective layer that protects against moisture, chemicals, and abrasion. Epoxy coatings are ideal for applications where superior adhesion and robust protection are necessary.
- Parylene: Parylene coatings are deposited as a vapor and conformally coat the PCB surface with a thin, uniform layer. They offer excellent dielectric properties, chemical resistance, and biocompatibility. Parylene coatings provide a barrier against moisture and contaminants without adding significant thickness to the PCB.
Selecting the appropriate conformal coating depends on factors such as the operating environment, desired level of protection, ease of application, and compatibility with other components. Proper application techniques, including surface preparation and thickness control, are essential to ensure the coating’s effectiveness in safeguarding the PCB from environmental hazards. Regular inspection and maintenance are also necessary to ensure conformally coated PCBs’ long-term reliability.
How does conformal coating protect PCBs from environmental hazards?
Conformal coating is a protective layer for printed circuit boards (PCBs), shielding them from environmental hazards that could compromise their performance or longevity. This coating is typically applied thinly and uniformly over the surface of the PCB, conforming to its contours and covering all exposed components. Here’s how conformal coating accomplishes this crucial task:
- Moisture Protection: Moisture can wreak havoc on PCBs, causing corrosion, short circuits, and overall deterioration. Conformal coating prevents moisture from reaching sensitive components such as conductive traces, solder joints, and integrated circuits. By sealing these vulnerable areas, the coating effectively safeguards the PCB against humidity, condensation, and water exposure.
- Chemical Resistance: PCBs may encounter a variety of chemical substances in their operating environments, ranging from cleaning solvents to industrial pollutants. Conformal coatings are designed to resist chemical penetration, shielding the underlying circuitry from corrosive agents that could corrode metal contacts or degrade insulating materials. This chemical resistance ensures the integrity and reliability of the PCB, even in harsh chemical environments.
- Mechanical Protection: Conformal coatings protect against mechanical damage, including abrasion, vibration, and impact. By encapsulating delicate components and securing them in place, the coating reduces the risk of physical harm during handling, transportation, or operation. This mechanical protection enhances the durability and robustness of the PCB, extending its service life in demanding conditions.
- Insulation: Besides safeguarding against external hazards, conformal coatings offer electrical insulation properties. By isolating conductive elements from each other and external conductive surfaces, the coating helps prevent short circuits and electrical leakage. This insulation is especially critical in high-voltage applications where proper electrical isolation is essential for safety and performance.
Overall, conformal coating plays a vital role in enhancing PCBs’ reliability, longevity, and performance by shielding them from environmental hazards such as moisture, chemicals, mechanical stress, and electrical interference. By applying this protective layer, electronics manufacturers can ensure their products maintain optimal functionality even in challenging operating conditions.
What are the fundamental properties to consider when selecting a conformal coating?
Several vital properties must be carefully considered when selecting a conformal coating for electronic components to ensure optimal performance and protection. These properties include:
- Chemical Resistance: The coating should resist various chemicals encountered during operation, such as solvents, fuels, oils, and cleaning agents. Chemical resistance prevents degradation and ensures long-term protection of the components.
- Moisture Resistance: A critical property, especially for electronics operating in humid environments or moisture exposure. The coating should effectively seal the components to prevent moisture ingress, which can cause corrosion, short circuits, and other electrical failures.
- Dielectric Strength: Conformal coatings must have adequate dielectric strength to avoid electrical leakage and short circuits. This property is particularly crucial in high-voltage applications where insulation integrity is paramount.
- Adhesion: Proper adhesion ensures the coating remains firmly bonded to the substrate over time, even under thermal cycling, mechanical stress, or vibration. Poor adhesion can lead to delamination and compromise the protective capabilities of the coating.
- Flexibilityis essential for conformal coatings applied to flexible or moving components. The coating should maintain its integrity and protective properties even when subjected to bending, flexing, or other mechanical stresses.
- Temperature Resistance: The coating should withstand the operating temperatures of the electronic device without degrading or becoming brittle. Some applications may require coatings capable of withstanding extreme temperatures encountered during operation or processing.
- UV Resistance: Exposure to ultraviolet (UV) radiation can degrade certain conformal coatings over time, leading to loss of protection and deterioration of underlying components. UV-resistant coatings are essential for outdoor or exposed applications.
- Thickness and Coverage: The coating thickness should provide adequate protection without interfering with component functionality or assembly processes. Additionally, it should uniformly cover all surfaces, including complex geometries, to ensure comprehensive protection.
- Ease of Application: Consideration should be given to the ease of application, curing time, and compatibility with existing manufacturing processes. Some coatings may require specialized equipment or conditions for application and curing.
By carefully evaluating these fundamental properties, manufacturers can select the most suitable conformal coating to ensure their electronic products’ long-term reliability and performance in diverse operating environments.
What are the application methods for PCB conformal coating?
Selective and complete coverage coating are two different approaches to applying conformal coating on printed circuit boards (PCBs), each serving specific purposes and offering distinct advantages.
- Selective Coating:
- Selective coating involves applying the conformal coating only to specific areas of the PCB while leaving other regions uncoated. This method typically protects sensitive components or areas prone to environmental stresses while avoiding coating on areas that may interfere with functionality or assembly processes.
- Selective coating is achieved using specialized equipment such as robotic dispensers or precision spray nozzles, which can precisely target desired areas for coating. Programming these systems requires detailed knowledge of the PCB layout and component locations.
- This method offers several benefits, including cost savings by minimizing the coating material used, reducing masking requirements for areas where the coating is not desired, and maintaining accessibility to critical components for testing, troubleshooting, or rework.
- Full Coverage Coating:
- Full coverage coating, as the name suggests, involves applying the conformal coating across the entire surface of the PCB, covering all components and areas uniformly. This method protects comprehensively against environmental factors such as moisture, dust, chemicals, and temperature fluctuations.
- Full coverage coating is commonly achieved through spraying, dipping, or vapor deposition techniques, depending on the desired coating thickness, production volume, and coating material properties.
- While full coverage coating offers robust protection for the entire PCB assembly, it may increase material and labor costs compared to selective coating. Additionally, it can make rework or repair tasks more challenging since the coating must be removed from the affected areas before access to components is possible.
- Despite these potential drawbacks, full coverage coating is often preferred for applications where comprehensive protection is paramount, such as in harsh operating environments or high-reliability electronic systems.
Selective coating targets specific areas of the PCB for protection, offering cost savings and flexibility. Full-coverage coating provides comprehensive protection across the entire assembly, ensuring maximum reliability but potentially increasing cost and complexity. The choice between these methods depends on factors such as the level of security required, production constraints, and the application’s specific requirements.
How does selective coating differ from full-coverage coating?
Selective and complete coverage coating are different approaches used in various industries, particularly surface treatment and protective coatings. These methods serve different purposes and have distinct applications based on the desired outcome and requirements of the coated material or product.
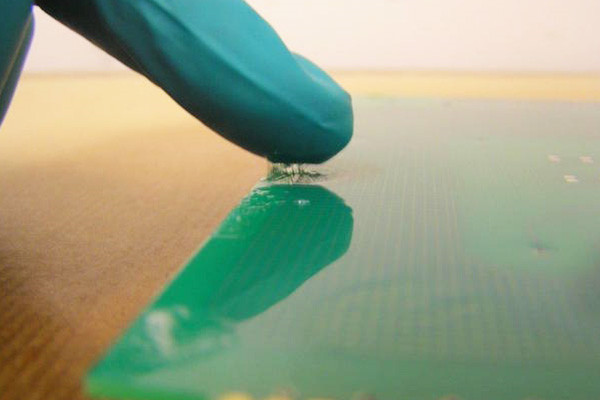
Selective coating:
Selective coating involves applying a coating material to specific areas or regions of an object or surface rather than covering the entire surface uniformly. This method is often employed when only certain surface parts need protection or enhancement, while other areas may not require coating or need a different treatment.
Advantages of selective coating:
- Precision: Selective coating allows for precise application, ensuring that only the intended areas receive the coating, conserving resources and minimizing waste.
- Cost-effectiveness: By coating only the necessary areas, selective coating can be more cost-effective than full coverage coating, as it reduces the amount of coating material required.
- Customization: Selective coating enables customization and tailored treatments, accommodating specific design requirements or functional needs of the object or surface.
- Flexibility: This method offers flexibility in coating applications, allowing for intricate designs, patterns, or multi-layer coatings to be applied selectively.
Applications of selective coating:
- Electronic components: Selective coating is commonly used in electronic manufacturing to protect circuit boards or specific components from environmental factors such as moisture, dust, or corrosion.
- Automotive industry: Certain automotive parts may require selective coating for targeted protection against wear, abrasion, or chemical exposure.
- Decorative coatings: Selective coating is utilized in decorative applications, such as adding patterns or designs to surfaces while leaving other areas untreated for aesthetic purposes.
Full coverage coating:
In contrast, full coverage coating involves uniformly applying a coating material across the entire surface of an object or substrate. This method ensures complete protection or enhancement of the surface and is often used when consistent coverage is required for durability, aesthetics, or functional purposes.
Advantages of full coverage coating:
- Comprehensive protection: Full coverage coating provides uniform protection to the entire surface, guarding against various environmental factors, corrosion, or wear.
- Durability: Since the entire surface is coated, full coverage coating enhances the overall durability and longevity of the material or product.
- Streamlined process: A uniform coating simplifies the coating process, making it efficient for large-scale production or standardized applications.
Applications of full coverage coating:
- Protective coatings:Full coverage coating is commonly used for protective purposes in aerospace, marine, and infrastructure industries to safeguard surfaces against harsh environmental conditions.
- Painting and finishing:Full coverage coating is employed in painting and finishing applications for surfaces such as metal, wood, or plastic to achieve a consistent appearance and protective layer.
- Corrosion prevention:Full coverage coating is essential for preventing corrosion on metal surfaces by creating a barrier between the substrate and corrosive elements.
While selective and complete coverage coating offers surface protection and enhancement, their approach and applications differ. Selective coating targets specific areas for treatment, offering precision and customization, while full coverage coating provides uniform protection across the entire surface, ensuring comprehensive coverage and durability. The choice between these methods depends on the specific requirements and objectives of the coating application.
What are the advantages of using a silicone-based conformal coating?
Silicone-based conformal coatings offer many advantages, making them popular for protecting electronic components in various industries. Here are some key benefits:
- High-Temperature Resistance: Silicone coatings can withstand extremely high and low temperatures without degrading or losing their protective properties. This resilience ensures that electronic components remain functional even in harsh environmental conditions, such as automotive engine compartments or aerospace applications.
- Chemical Resistance: Silicones exhibit excellent resistance to various chemicals, including solvents, acids, and bases. This property makes them suitable for environments where exposure to corrosive substances is a concern, such as industrial settings or marine applications.
- Flexibility and Elasticity: Silicone-based coatings maintain flexibility and elasticity over a wide temperature range. This flexibility allows them to expand and contract with the substrate during temperature fluctuations, preventing cracks or delamination and ensuring long-term protection of the components.
- Moisture Protection: Silicone conformal coatings provide effective moisture barrier properties, protecting sensitive electronic components from moisture ingress and preventing corrosion or electrical failures. This makes them ideal for outdoor applications or devices exposed to high-humidity environments.
- Electrical Insulation: Silicones have excellent dielectric properties, offering high electrical insulation resistance. This property prevents electrical leakage and shorts, enhancing the reliability and lifespan of electronic devices.
- UV Stability: Many silicone-based coatings are formulated to resist UV degradation, maintaining their performance and appearance over prolonged exposure to sunlight. This UV stability is advantageous for outdoor applications where prolonged exposure to sunlight is inevitable.
- Easy Application and Repair: Silicone coatings can be applied by various methods, including spraying, dipping, or brushing, and they cure rapidly at room temperature or with mild heat. Additionally, they can be easily reworked or repaired if necessary, simplifying maintenance and rework processes.
- Transparency: Some silicone formulations are optically transparent, allowing for inspection of components post-coating without hindering visibility. This transparency is beneficial for applications requiring visual inspection, such as in LED displays or optical sensors.
Overall, the combination of high-temperature resistance, chemical resistance, flexibility, moisture protection, electrical insulation, UV stability, ease of application, and transparency makes silicone-based conformal coatings an excellent choice for protecting electronic components in diverse and challenging environments.
What are the disadvantages of using acrylic conformal coatings?
While acrylic conformal coatings offer certain advantages, they also come with several disadvantages that should be considered when selecting a protective coating for electronic components:
- Limited Temperature Range: Acrylic coatings have a relatively narrow operating range compared to silicone or polyurethane coatings. They may need to perform better in extreme temperature environments, such as those found in automotive engine compartments or aerospace applications, where temperature fluctuations are typical.
- Poor Chemical Resistance: Acrylic coatings are generally less chemical-resistant than silicone or epoxy coatings. They may degrade or dissolve when exposed to certain solvents, acids, or bases, leading to diminished protection of the underlying electronic components.
- Brittleness: Acrylic coatings tend to be more brittle than other conformal coatings. This brittleness can lead to cracking or chipping of the coating over time, especially in applications where the coated components are subject to mechanical stress or vibration.
- Moisture Permeability: Acrylic coatings may have higher moisture permeability than other coatings, such as silicone or epoxy. This can increase susceptibility to moisture ingress, leading to potential corrosion and electrical failures of the protected electronic components, particularly in humid environments.
- UV Sensitivity: Many acrylic coatings are susceptible to UV degradation when exposed to sunlight over time. This can cause the coating to turn yellow, become brittle, or lose its protective properties, compromising the integrity of the coated components. UV stability is essential for outdoor applications where prolonged exposure to sunlight is inevitable.
- Limited Thickness Range: Acrylic coatings typically have limitations regarding the thickness that can be applied effectively. Applying thicker layers may result in uneven curing, leading to potential defects such as cracking or delamination.
- Difficulty in Rework: Acrylic coatings can be challenging to rework or remove once applied, especially if wholly cured. Specialized solvents or mechanical methods may be required for rework, which can be time-consuming and labor-intensive.
while acrylic conformal coatings offer certain advantages such as ease of application and cost-effectiveness, their limitations in temperature resistance, chemical resistance, brittleness, moisture permeability, UV sensitivity, thickness range, and rework difficulty make them less suitable for demanding applications where robust protection of electronic components is essential. It’s crucial to carefully assess the application’s specific requirements and environmental conditions before choosing the appropriate conformal coating.
How does UV cure conformal coating differ from traditional curing methods?
UV cure conformal coating and traditional curing methods differ significantly in process, speed, efficiency, and environmental impact.
UV cure conformal coating utilizes ultraviolet (UV) light to initiate a rapid chemical reaction that transforms liquid coating materials into a solid state. This process is known as photopolymerization. The coating material contains photoinitiators, which are sensitive to UV light and facilitate the curing process when exposed. UV cure conformal coating offers several advantages over traditional curing methods:
- Speed: UV cure conformal coating is faster than conventional curing methods. UV light typically takes seconds to minutes to cure the coating, whereas traditional methods such as thermal curing or air drying may take hours or even days.
- Precision: UV cure conformal coating allows precise control over the curing process. Since the curing reaction is initiated by UV light exposure, it can be accurately controlled in intensity, duration, and wavelength, resulting in consistent and uniform curing.
- Energy Efficiency: UV cure conformal coating requires less energy than traditional curing methods such as thermal curing, often involving heating large ovens or chambers. This energy efficiency can lead to cost savings and reduced environmental impact.
- Reduced Environmental Impact: UV cure conformal coating typically does not involve solvents or other volatile organic compounds (VOCs) commonly found in traditional coating materials. As a result, UV-cure conformal coating is considered more environmentally friendly and safer for operators and the surrounding environment.
- Increased Throughput: The rapid curing time of UV cure conformal coating allows for increased production throughput compared to traditional curing methods. Manufacturers can achieve higher volumes and faster turnaround times, improving productivity and profitability.
UV cure conformal coating offers advantages over traditional curing methods in speed, precision, energy efficiency, environmental impact, and throughput. These benefits make UV cure conformal coating an attractive choice for various industrial applications where fast, high-quality, and environmentally friendly coating processes are essential.
What are the challenges associated with masking during conformal coating application?
Masking during conformal coating application presents several challenges that require careful consideration and management to ensure successful outcomes:
- Precision Masking: Achieving precise masking is essential to protect sensitive components or areas that should not be coated. The challenge lies in ensuring that the masking material covers only the intended areas while leaving the rest exposed for coating. Any gaps or inaccuracies in the masking process can result in coating material seeping into protected areas, leading to potential damage or functionality issues.
- Adhesion of Masking Material: The masking material must adhere effectively to the substrate surface to prevent the coating material from penetrating underneath. Poor adhesion can result in the masking material lifting or shifting during the coating process, compromising the effectiveness of the masking and potentially leading to rework or defects.
- Compatibility with Coating Material: The masking material should be compatible with the applied conformal coating material. Compatibility issues can arise if the masking material reacts adversely with the coating material or if it cannot withstand the curing or drying process of the coating. Incompatibility can lead to adhesion problems, coating defects, or surface contamination.
- Removal Process: Removing masking materials after the conformal coating process can be challenging, especially if they adhere firmly to the substrate or leave behind residue. Care must be taken to ensure the removal process does not damage the coated surface or underlying components.
- Cost and Time: Masking adds additional cost and time to the conformal coating process, particularly for complex or intricate designs that require meticulous masking. Balancing the need for effective masking with cost and time considerations is crucial to maintaining efficiency and competitiveness in manufacturing operations.
- Operator Skill and Training: Proper masking requires skilled operators who understand the intricacies of the process and can execute it accurately. Providing comprehensive training and implementing standardized procedures can help mitigate the risk of masking-related errors.
Addressing these challenges requires careful planning, selecting appropriate masking materials, adherence to best practices, and continuous process improvement to ensure high-quality conformal coating application while minimizing the risks associated with masking.
What are the environmental regulations regarding conformal coating materials?
Environmental regulations regarding conformal coating materials vary by region but generally focus on limiting the use of hazardous substances and promoting adopting environmentally friendly practices. Some fundamental rules and directives that impact conformal coating materials include:
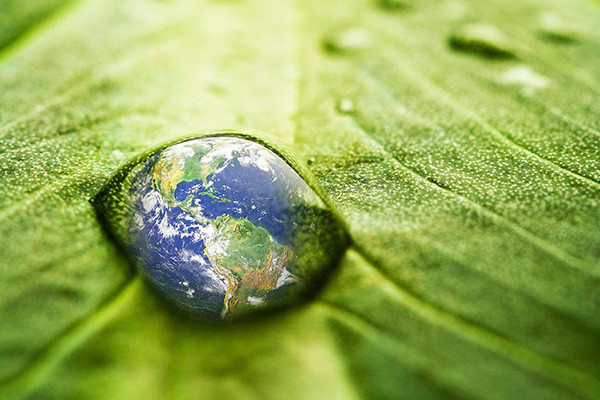
- Restriction of Hazardous Substances (RoHS): RoHS directives restrict the use of certain hazardous substances in electrical and electronic equipment, including conformal coating materials. Substances such as lead, mercury, cadmium, hexavalent chromium, and specific flame retardants are limited to reduce environmental and health risks associated with their use.
- Registration, Evaluation, Authorization, and Restriction of Chemicals (REACH): REACH is a European Union regulation that addresses the production and use of chemical substances. It aims to ensure the safe use of chemicals and to provide information on their properties and risks. Conformal coating manufacturers must comply with REACH requirements by registering substances, assessing risks, and implementing measures to minimize risks to human health and the environment.
- Waste Electrical and Electronic Equipment (WEEE) Directive: The WEEE Directive establishes requirements for the collection, recycling, and disposal of electrical and electronic equipment at the end of its life cycle. Conformal coating materials used in electronic products must comply with WEEE regulations to minimize the environmental impact of their disposal.
- Volatile Organic Compounds (VOC) Regulations: Many regions have rules restricting the use of VOCs in industrial coatings, including conformal coatings. VOCs contribute to air pollution and can have adverse health effects. Compliance with VOC regulations typically involves using low-VOC or VOC-free formulations and implementing practices to minimize VOC emissions during application and curing processes.
- Hazardous Waste Regulations: Conformal coating materials may generate dangerous waste during manufacturing processes or at the end of their life cycle. Regulations governing hazardous waste handling, storage, transportation, and disposal must be followed to prevent environmental contamination and ensure compliance with applicable laws.
Compliance with these environmental regulations requires manufacturers to carefully select conformal coating materials, assess their environmental impact, implement pollution prevention measures, and maintain proper documentation to demonstrate compliance with regulatory requirements. Additionally, ongoing monitoring and adaptation to evolving regulations are essential to ensure continued compliance and minimize environmental risks associated with conformal coating materials.
How can PCB conformal coating affect thermal management in electronic devices?
PCB (Printed Circuit Board) conformal coating significantly protects electronic devices from environmental factors such as moisture, dust, chemicals, and temperature fluctuations. However, its application can also influence thermal management within electronic devices, albeit indirectly.
- Insulation: Conformal coatings are often insulating materials, which can create a thermal barrier between the components on the PCB and the surrounding environment. While this insulation can protect against moisture and contaminants, it can also hinder heat dissipation from critical components like processors, power transistors, or voltage regulators.
- Thermal Conductivity: Some conformal coatings are designed to have specific thermal conductivity properties. While these coatings may provide protection, they can also facilitate heat transfer away from sensitive components, enhancing thermal management. However, the thermal conductivity of most conformal coatings is lower than that of traditional thermal interface materials like grease or pads, potentially leading to higher operating temperatures if not carefully considered.
- Thickness and Coverage: The thickness and coverage uniformity of the conformal coating layer can affect thermal management. A thicker coating layer may be a more significant thermal insulator, impeding heat dissipation. Conversely, a thin, uniform coating may protect without significantly impacting heat transfer.
- Application Method: The method used to apply conformal coating can influence its thermal effects. Techniques like selective coating, where only specific areas of the PCB are coated, can help manage thermal dissipation by exposing critical heat-generating components. Additionally, spray coating or dip coating methods may result in varying coating thicknesses, which can impact thermal conductivity.
- Ventilation and Heat Sinks: In devices with conformal coatings, designers often need to compensate by implementing additional thermal management measures such as enhanced ventilation or heat sinks. These supplementary measures help dissipate heat more effectively, counteracting any thermal insulation introduced by the conformal coating.
While PCB conformal coatings primarily protect electronic devices from environmental stresses, their thermal properties and application methods can indirectly affect thermal management. Careful consideration of coating material, thickness, coverage, and application technique is necessary to ensure optimal thermal performance alongside protection.
What are the typical thickness requirements for conformal coatings?
Conformal coatings are thin protective layers applied to electronic circuit boards and components to safeguard them against environmental stresses such as moisture, dust, chemicals, and temperature variations. The thickness requirements for conformal coatings depend on various factors, including the type of coating material, the intended level of protection, and the specific application requirements. Typically, conformal coatings are applied in thin layers to ensure adequate protection without impeding the functionality of the electronic device or interfering with its performance.
The most common types of conformal coatings include acrylics, silicones, urethanes, and epoxies. Each type has its optimal thickness range based on its properties and the level of protection it provides. Generally, conformal coatings are applied in thicknesses ranging from a few micrometers to tens of micrometers.
For example, acrylic coatings, known for their excellent moisture resistance and flexibility, are often applied at thicknesses between 25 and 75 micrometers. Silicones, valued for their wide temperature tolerance and good electrical insulation properties, may be used in thinner layers ranging from 12 to 50 micrometers.
Urethane coatings offer superior chemical resistance and mechanical strength and are typically applied at 25 to 75-micrometer thicknesses. Epoxies, known for their exceptional adhesion and hardness, may be used at slightly higher thicknesses, ranging from 50 to 125 micrometers.
The specific thickness requirement for a conformal coating is determined through careful consideration of the environmental conditions the electronic device will be subjected to, the level of protection required, and the compatibility of the coating material with the coated components. Too thin a coating may not provide adequate security, while too thick a coating may lead to increased weight, decreased thermal dissipation, and difficulties in rework or repair.
Ultimately, the goal of applying a conformal coating is to strike a balance between providing sufficient protection for the electronic components while maintaining the integrity and functionality of the device. This balance ensures the longevity and reliability of the electronics in various operating environments.
How does the choice of conformal coating impact PCB rework and repair processes?
Conformal coating protects printed circuit boards (PCBs) from environmental factors such as moisture, dust, chemicals, and mechanical stress. However, due to its properties and compatibility with rework techniques, conformal coating can significantly impact PCB rework and repair processes.
- Type of Coating: Different conformal coatings, such as acrylic, silicone, urethane, and epoxy, have varying properties. Acrylic coatings are relatively more straightforward to remove using solvents than silicone or epoxy coatings, which may require more aggressive methods like mechanical scraping or sanding. Thus, the type of coating chosen initially affects the ease of rework later.
- Compatibility with Rework Techniques: Some conformal coatings may not be compatible with specific rework techniques. For instance, epoxy coatings are highly resistant to solvents, making them challenging to remove without damaging the underlying components. Silicone coatings can withstand higher temperatures, making them more suitable for reflow soldering processes during repair work.
- Thickness and Application Method: The thickness of the conformal coating and the application method can also impact rework processes. Thick coatings may require more aggressive removal methods, while solvents may more easily penetrate thin coatings. Additionally, coatings applied by spraying may have a more uniform thickness than those applied by dipping, affecting the consistency of rework efforts.
- Masking and Protection of Critical Areas: Proper masking of critical areas such as connectors, test points, and fine-pitch components before conformal coating application is essential. Failure to mask these areas adequately can lead to coating buildup, making rework more difficult and increasing the risk of damage to sensitive components during removal.
- Reapplication Considerations: In cases where rework involves the removal of the conformal coating followed by reapplication, factors such as cure time and compatibility with subsequent coating layers must be taken into account to ensure proper adhesion and performance of the new coating.
The choice of conformal coating significantly influences PCB rework and repair processes due to its compatibility with rework techniques, ease of removal, thickness, application method, and considerations for reapplication. Careful selection based on the specific application requirements and potential rework scenarios is essential to facilitating efficient and successful PCB repair operations.
What are some common defects that may occur during conformal coating application?
During conformal coating application, several common defects can occur, impacting the integrity and effectiveness of the coating. Identifying and addressing these defects promptly is crucial to ensure the reliability and performance of the coated electronic assemblies. Here are some common defects:
- Incomplete Coverage: This defect occurs when certain areas of the PCB are not adequately coated, leaving them vulnerable to environmental stressors. Only complete coverage can result from proper application techniques, such as insufficient spraying pressure, incorrect nozzle positioning, or inadequate viscosity control of the coating material.
- Bridging: Bridging happens when the conformal coating forms a continuous film over adjacent conductive features, creating unintended electrical connections or short circuits. It can occur due to excessive coating thickness, improper masking, or inadequate control of coating viscosity, causing the material to flow where it shouldn’t.
- Orange Peel: Orange peel refers to a textured surface finish resembling the skin of an orange. It occurs when the coating material dries unevenly or quickly, resulting in a bumpy or rippled appearance. Factors contributing to orange peel include improper viscosity, incorrect drying conditions, or incompatible coating and solvent combinations.
- Fish Eyes: Fish eyes are small circular voids or defects in the coating film, resembling the eyes of a fish. They typically occur due to surface contamination, such as oils, residues, or moisture, which repel the coating material, preventing it from adhering correctly. Fish eyes can also result from poor substrate preparation or incompatible coating-material interactions.
- Pinholes: Pinholes are tiny perforations or voids in the coating film, compromising its barrier properties and exposing underlying components to environmental hazards. Pinholes can form due to inadequate coating thickness, improper curing conditions, or entrapped air or moisture during application.
- Cracking or Delamination: Cracking or delamination of the conformal coating can occur due to excessive mechanical stress, thermal cycling, or incompatible substrate-coating interactions. These defects compromise the protective barrier, allowing moisture and contaminants to penetrate the PCB assembly, leading to potential reliability issues.
Addressing these common defects requires careful process control, proper equipment calibration, adherence to manufacturer recommendations, and thorough inspection procedures during and after coating application. Implementing preventive measures and corrective actions can minimize the occurrence of defects and ensure the reliability and longevity of conformally coated electronic assemblies.
How can conformal coating inspection be carried out to ensure quality control?
Conformal coating inspection is crucial for ensuring the quality and reliability of electronic components, particularly in industries such as aerospace, automotive, and medical devices, where environmental factors can significantly affect performance. Here are critical methods for conducting practical conformal coating inspection:
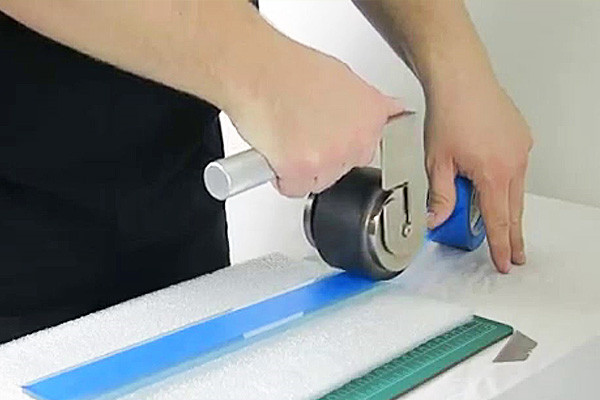
- Visual Inspection: The most straightforward method involves examining coated components under magnification. This inspection checks for coating uniformity and the presence of voids, bubbles, cracks, or other defects. Trained inspectors use specialized lighting and magnification tools to identify imperfections accurately.
- UV Inspection: Some conformal coatings fluoresce under ultraviolet (UV) light. UV inspection involves using UV lamps to illuminate coated surfaces, making defects like pinholes, thin spots, or inconsistencies more visible. This method enhances defect detection, especially for transparent coatings.
- Thickness Measurement: Conformal coating thickness is critical for performance and reliability. Various techniques, such as eddy current, magnetic induction, or optical methods, can measure coating thickness accurately. These methods ensure that coatings meet specified thickness requirements without being too thin or thick, which can lead to performance issues or damage.
- Electrical Testing: Electrical testing assesses conformal coatings’ insulation resistance and dielectric strength. Insulation resistance testing measures the coating’s ability to resist current flow between conductive traces, while dielectric strength testing evaluates the coating’s ability to withstand voltage without breakdown. These tests ensure coatings protect against moisture, dust, and other environmental factors.
- Cross-Sectional Analysis: Cross-sectional analysis involves cutting coated components to examine coating thickness, adhesion, and coverage at different layers. This method provides detailed insights into coating uniformity and integrity throughout the entire component.
- Thermal Cycling and Environmental Testing: Subjecting coated components to thermal cycling and environmental testing simulates real-world conditions, assessing coating performance under temperature variations, humidity, and other stressors. Monitoring changes in coating appearance, adhesion, and electrical properties helps identify potential weaknesses and failure points.
- Automated Inspection Systems: Automated vision systems equipped with cameras and image processing algorithms can efficiently inspect conformal coatings for defects. These systems offer rapid, consistent, and reliable inspection, reducing human error and increasing throughput in large-scale manufacturing.
By employing these inspection methods, manufacturers can ensure the quality, reliability, and longevity of conformal coatings, ultimately enhancing the performance and durability of electronic components in various applications.
What are the considerations for removing conformal coatings for rework or repair?
Removing conformal coatings for rework or repair requires careful consideration to avoid damaging the underlying components and ensuring the integrity of the coating itself. Here are some key considerations:
- Type of Conformal Coating: Different conformal coatings (e.g., acrylic, silicone, urethane) have varying chemical compositions and properties. Understanding the specific type of coating used is crucial for selecting appropriate removal methods that won’t compromise the underlying circuitry or components.
- Compatibility with Components: Some conformal coating removal methods involve harsh chemicals or mechanical abrasion, which can damage sensitive electronic components. It’s essential to assess the compatibility of the removal method with the components being worked on to prevent unintended damage.
- Environmental and Safety Concerns: Certain conformal coating removal techniques may involve chemicals that pose environmental or health risks. Proper safety precautions and environmental regulations must be followed to ensure personnel safety and compliance with regulations.
- Effectiveness of Removal Method: The chosen method should effectively remove the conformal coating without leaving residue or damaging the underlying substrate. Trial testing on sample boards or small areas can help determine the most suitable removal method for the specific application.
- Precision and Control: Conformal coatings are often applied in precise locations to protect critical regions of electronic assemblies. Removal methods should offer the necessary precision and control to target specific areas without affecting surrounding components or circuitry.
- Post-Removal Inspection and Testing: After removing the conformal coating, thorough inspection and testing are essential to ensure that no damage has occurred to the underlying components and that the rework or repair process can proceed without any issues.
- Reapplication Considerations: If reapplication of the conformal coating is necessary after rework or repair, factors such as compatibility with the removal method used, curing requirements, and application techniques should be taken into account to maintain the integrity and effectiveness of the coating.
By carefully considering these factors, technicians can effectively remove conformal coatings for rework or repair while minimizing the risk of damage to electronic components and ensuring the reliability of the finished assembly.
How does conformal coating contribute to the reliability of electronic assemblies in harsh environments?
Conformal coatings play a vital role in enhancing the reliability of electronic assemblies, particularly in harsh environments, by providing a protective barrier against various environmental stressors. Here’s how conformal coatings contribute to reliability:
- Protection Against Moisture and Contaminants: One of the primary functions of conformal coatings is to shield electronic components from moisture, dust, dirt, and other contaminants. By forming a barrier over the circuitry, conformal coatings prevent these elements from infiltrating the assembly, which can lead to corrosion, short circuits, and electrical malfunctions.
- Resistance to Chemicals: Many conformal coatings resist various chemicals, including solvents, fuels, oils, and cleaning agents. This chemical resistance helps prevent the degradation of the underlying components. It ensures the long-term stability and functionality of the electronic assembly, especially in environments where exposure to corrosive substances is prevalent.
- Thermal Management: Some conformal coatings offer thermal management properties, dissipating heat generated by electronic components and promoting more efficient operation. By reducing the risk of overheating, these coatings help maintain the reliability and performance of the assembly, particularly in applications where temperature fluctuations are expected or heat dissipation is critical.
- Electrical Insulation: Conformal coatings act as insulators, preventing electrical short circuits caused by moisture ingress or the accumulation of conductive contaminants. This insulation property is essential for maintaining signal integrity, preventing unintended current leakage, and minimizing the risk of electrical failures in harsh operating environments.
- Mechanical Protection: Besides environmental protection, conformal coatings offer mechanical protection against physical damage such as scratches, abrasion, and vibration. This safeguarding helps extend the lifespan of electronic assemblies, particularly those deployed in rugged environments or subjected to mechanical stresses.
- UV Resistance: Some conformal coatings are formulated to resist ultraviolet (UV) radiation, which can cause the degradation of unprotected electronic components over time. By shielding against UV exposure, these coatings ensure the long-term reliability and performance of the assembly, even in outdoor or high-UV environments.
Overall, conformal coatings significantly enhance the reliability of electronic assemblies in harsh environments by providing a robust protective barrier against moisture, contaminants, chemicals, thermal stress, electrical hazards, and mechanical damage. Their application helps prolong the lifespan, maintain performance, and reduce the likelihood of failures, ultimately contributing to electronic devices and systems’ overall reliability and durability.
What are the cost implications of implementing conformal coating in PCB assembly?
The implementation of conformal coating in PCB assembly involves several cost implications, both direct and indirect, which should be considered in the overall budgeting and decision-making process:
- Material Costs: The cost of the conformal coating material itself can vary depending on the type of coating chosen (e.g., acrylic, silicone, urethane), the volume needed for application, and the supplier. Specialty coatings designed for specific environmental conditions may incur higher material costs than standard coatings.
- Application Equipment and Labor: Investing in the necessary equipment for applying conformal coatings, such as spray guns, dip tanks, or robotic dispensers, adds to the initial cost. Additionally, labor costs associated with training personnel to apply the coatings accurately and efficiently should be considered.
- Process Integration: Integrating conformal coating into the PCB assembly process may require modifications or upgrades to existing production lines. These changes could involve retrofitting equipment, reconfiguring workflow, or implementing quality control measures, all contributing to additional costs.
- Quality Assurance and Testing: Ensuring the reliability and effectiveness of conformal coating applications may necessitate additional quality assurance measures and testing protocols. This can include inspections for uniformity, adhesion, and coverage and environmental testing to validate performance under harsh conditions.
- Rework and Repair: In cases where rework or repair is needed on coated PCBs, additional costs may arise from removing and reapplying the conformal coating. This includes the cost of materials, labor, and any associated downtime in the production process.
- Long-Term Reliability and Warranty: While conformal coatings enhance the reliability of electronic assemblies in harsh environments, their long-term effectiveness contributes to overall product reliability and customer satisfaction. Offering warranties or guarantees on coated assemblies may incur additional costs but can provide peace of mind to customers.
- Regulatory Compliance: Compliance with environmental regulations and industry standards regarding the use and disposal of conformal coating materials may entail administrative costs for documentation, reporting, and adherence to safety protocols.
By carefully evaluating these cost factors alongside the benefits of improved reliability and longevity in harsh environments, manufacturers can make informed decisions about implementing conformal coating in PCB assembly.
What are the future trends and advancements in PCB conformal coating technology?
The need for increased reliability, performance, and sustainability drives future trends and advancements in PCB conformal coating technology. Several key developments are expected to shape the future of conformal coatings:
- Nanotechnology: Integrating nanomaterials into conformal coatings offers enhanced properties such as improved barrier protection, moisture resistance, and thermal conductivity. Nanoparticle-based coatings can provide better coverage and adhesion while reducing coating thickness, leading to more compact and lightweight electronic assemblies.
- Self-healing Coatings: Research is underway to develop self-healing conformal coatings capable of autonomously repairing minor damage or scratches. These coatings contain microcapsules filled with healing agents that rupture upon damage, releasing compounds that mend the coating and restore its protective properties.
- Flexible and Stretchable Coatings: With the increasing demand for flexible and wearable electronics, there’s a growing need for conformal coatings that can withstand bending, stretching, and other mechanical stresses. Flexible coatings based on elastomers or polymers with tailored molecular structures are being developed to provide durable protection for flexible PCBs and circuits.
- Functional Coatings: Conformal coatings with additional functionalities beyond essential protection are gaining traction. These coatings may incorporate antimicrobial activity, anti-static properties, or enhanced adhesion to specific substrates, catering to diverse application requirements in various industries.
- Environmentally Friendly Formulations: As sustainability becomes a focal point across industries, there’s a push towards developing eco-friendly conformal coating formulations that comply with regulatory standards. Water-based coatings, bio-based materials, and reduced volatile organic compound (VOC) content are being explored to minimize environmental impact during manufacturing and disposal.
- Advanced Application Techniques: Innovations in application techniques, such as selective coating, jetting, or inkjet printing, enable more precise and efficient deposition of conformal coatings. These techniques offer greater control over coating thickness and coverage while reducing material waste and processing time.
- Integrated Quality Control: Future advancements may involve integrating real-time monitoring and quality control systems into the conformal coating application process. This could include sensors, machine vision systems, or artificial intelligence algorithms to detect defects, ensure uniformity, and optimize coating performance.
Overall, the future of PCB conformal coating technology is focused on delivering coatings that offer superior protection, functionality, sustainability, and application efficiency to meet the evolving needs of electronic assemblies in diverse industries.
Conclusion:
PCB conformal coating is an indispensable aspect of modern electronics manufacturing. It offers crucial protection against environmental hazards and enhances the reliability and longevity of electronic assemblies. By understanding the various types, application methods, considerations, and emerging trends in conformal coating technology, manufacturers can optimize their processes to meet the demanding requirements of today’s electronic devices.
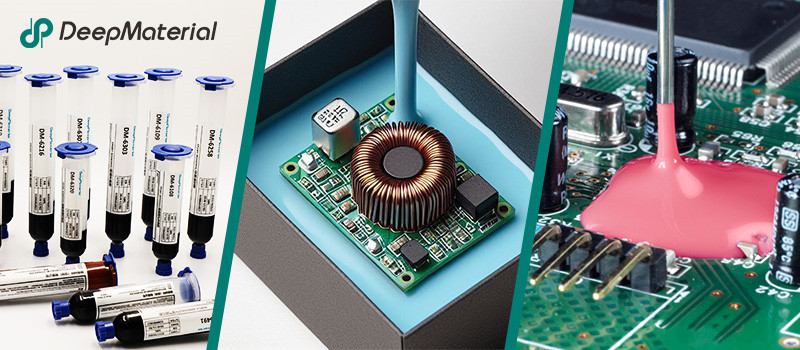
About DeepMaterial
DeepMaterial is a trusted supplier of encapsulant materials that are used in electronics manufacturing worldwide. From chip on board encapsulants such as glob top material to conformal coatings, underfills, low pressure molding, and potting solutions, DeepMaterial offers a full range of circuit board protection materials that effectively protect circuit boards while help reduce costs. More…Deepmaterial is a the manufacturer of epoxy adhesives including hardeners, metalbond, and metal filled resins. Structural, toughened medium viscosity, and non-sag adhesives are also offered. Some adhesives are resistant to thermal shock, chemical, vibration dampening, and impact. Suitable for metals, plastics, wood, and ceramics. Serves electronics, aerospace, automotive, tooling, marine, and construction industries. REACH and RoHS compliant. FDA approved. UL listed. Meets military specifications. We are the one of best adhesive manufacturers in China.
Blogs & News
Potting compounds are at the frontline of electronics assembly, delivering effective protection in challenging environmental conditions while improving mechanical strength and offering high electric insulation. Used within a variety of industries, electrical potting compounds are found within a broad range of consumer electronics, as well as used in applications across the automotive, aerospace, and other industries where electronic assemblies are prevalent.
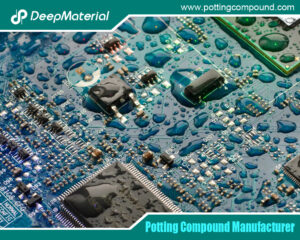
The Comprehensive Guide to Epoxy Potting Compound Manufacturers
The Comprehensive Guide to Epoxy Potting Compound Manufacturers Epoxy potting compounds are essential materials in the electronics industry, providing robust protection for sensitive components against
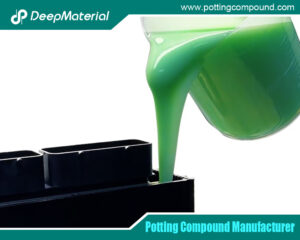
The Essential Guide to Potting Materials for Electronics
The Essential Guide to Potting Materials for Electronics In the rapidly evolving field of electronics, ensuring device reliability and longevity is critical. One of the
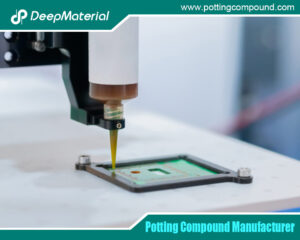
The Expanding Horizon of the Mini Silicone Optical Glue Market
The Expanding Horizon of the Mini Silicone Optical Glue Market The mini silicone optical glue market is witnessing unprecedented growth, fueled by technological advancements and
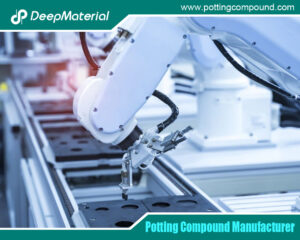
The Comprehensive Guide to PCB Potting Services: Ensuring Reliability in Electronics
The Comprehensive Guide to PCB Potting Services: Ensuring Reliability in Electronics Printed Circuit Boards (PCBs) are the backbone of modern electronics, enabling functionality in
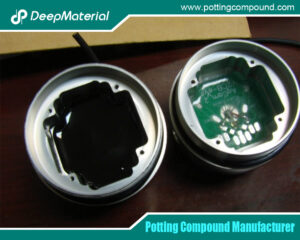
Comprehensive Insights on PCB Encapsulation in Potting Material
Comprehensive Insights on PCB Encapsulation in Potting Material In the fast-evolving landscape of electronics, ensuring the durability, reliability, and longevity of printed circuit boards
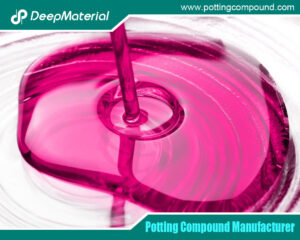
The Vital Role of Industrial Silicone Adhesive Manufacturers in Modern Industry
The Vital Role of Industrial Silicone Adhesive Manufacturers in Modern Industry In today’s fast-paced industrial landscape, the demand for reliable and durable adhesives is