Home > Potting Compound > Epoxy Potting Compound
Epoxy Potting Compound
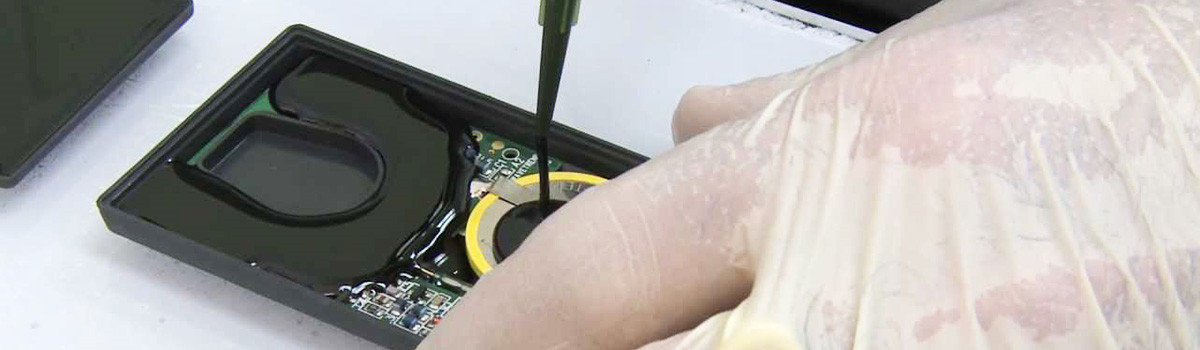
Epoxy potting compounds serve as the unsung heroes in the realm of electronic encapsulation and protection. Understanding their intricacies is crucial for engineers and manufacturers alike. In this comprehensive guide, we’ll delve into the world of epoxy potting compounds, exploring their composition, applications, and benefits, while addressing common queries along the way.
Table of Contents
ToggleWhat Are Epoxy Potting Compounds Exactly?
Epoxy potting compounds are specialized materials widely used in electronic engineering and manufacturing. They are crucial in encapsulating and protecting sensitive electronic components from various environmental factors, ensuring their longevity and reliability. Here’s a concise breakdown of what epoxy potting compounds are and how they work:
Definition: Epoxy potting compounds are a resin-based material formulated with epoxy resins, hardeners, and fillers. These compounds are designed to flow around electronic components and then cure to form a solid, protective encapsulation.
Functionality: Once applied, epoxy potting compounds encapsulate electronic components, forming a protective barrier that shields them from moisture, dust, vibrations, and other external hazards. This encapsulation enhances the durability and reliability of electronic devices, particularly in challenging environments.
Composition: Epoxy potting compounds typically have two main components: epoxy resin and a hardener. When mixed in the correct proportions, these components undergo a chemical reaction known as curing, transforming from a liquid to a solid state. Fillers may also be added to modify the compound’s properties, such as improving thermal conductivity or enhancing flame resistance.
Properties: Epoxy potting compounds exhibit desirable properties, including high electrical insulation, excellent adhesion to various substrates, resistance to chemicals and solvents, and thermal stability over a wide temperature range. These properties make them suitable for a diverse array of electronic applications.
Applications: Epoxy potting compounds are extensively used in industries such as electronics manufacturing, automotive, aerospace, telecommunications, and renewable energy. They are commonly employed to encapsulate and protect components such as integrated circuits, sensors, transformers, and power supplies.
Benefits: Using epoxy potting compounds offers numerous benefits, including improved reliability and lifespan of electronic devices, reduced risk of electrical failures, enhanced resistance to environmental stresses, and simplified manufacturing processes.
How Do Epoxy Potting Compounds Work?
Epoxy potting compounds might sound like jargon reserved for industrial experts, but their functionality is fascinatingly simple yet crucial. Let’s delve into the intricate world of epoxy potting compounds and uncover how they work their magic.
What are Epoxy Potting Compounds?
Epoxy potting compounds are versatile materials extensively used in electronics and manufacturing industries. These compounds are designed to encapsulate electronic components, providing insulation, protection, and structural support.
How Do They Work?
Epoxy potting compounds operate on a straightforward principle: encapsulation. Here’s a breakdown of their working mechanism:
- Encapsulation: Epoxy potting compounds are liquid resins that solidify when cured. The compound is poured or injected around electronic components during the potting process, encasing them entirely.
- Chemical Reaction: Once applied, the epoxy undergoes a curing process triggered by either heat or UV light, depending on the specific formulation. This curing process initiates a chemical reaction within the epoxy, transforming it from liquid to solid.
- Bond Formation: As epoxy cures, it forms strong chemical bonds, creating a robust and durable encapsulation around the electronic components. This encapsulation shields the components from environmental factors such as moisture, dust, chemicals, and mechanical stress.
- Insulation:Epoxy potting compounds offer excellent electrical insulation properties, preventing short circuits and electrical leakage. This insulation is crucial for ensuring the reliable performance of electronic devices, especially in harsh or demanding environments.
- Thermal Management: Some epoxy formulations are engineered to possess excellent thermal conductivity properties. These compounds efficiently dissipate heat generated by electronic components, enhancing their reliability and longevity.
Benefits of Epoxy Potting Compounds:
- Protection: Shield electronic components from moisture, dust, chemicals, and mechanical stress.
- Insulation: Prevent electrical leakage and short circuits, ensuring the integrity of electronic circuits.
- Enhanced Durability: Improve the reliability and lifespan of electronic devices by providing robust encapsulation.
- Thermal Management: Efficiently dissipates heat, preventing overheating and component failure.
- Versatility: Compatible with a wide range of electronic components and applications.
Why Choose Epoxy Potting Compounds Over Other Encapsulation Methods?
In encapsulation methods, epoxy potting compounds are a reliable and efficient solution for various industries. Their exceptional properties make them a preferred choice over other encapsulation methods. Let’s explore why epoxy potting compounds are the go-to option for many applications.
Why Choose Epoxy Potting Compounds?
Superior Protection:
- Epoxy potting compounds provide unparalleled protection to electronic components against environmental factors such as moisture, chemicals, and temperature extremes.
- They create a robust barrier that shields sensitive components from mechanical stress, vibration, and shock, ensuring longevity and reliability.
Excellent Electrical Insulation:
- Epoxy potting compounds offer high dielectric strength and insulation resistance, making them ideal for critical electrical insulation applications.
- They prevent electrical leakage and short circuits, maintaining the integrity and performance of electronic devices even in challenging conditions.
Versatility:
- Epoxy potting compounds exhibit versatility in encapsulating various components, including PCBs, sensors, connectors, and more.
- Their compatibility with diverse substrates and materials makes them suitable for various automotive, aerospace, telecommunications, and medical applications.
Chemical Resistance:
- Epoxy potting compounds are highly resistant to chemicals, solvents, and corrosive substances, safeguarding electronic components from degradation and damage.
- This chemical resistance ensures the stability and reliability of encapsulated devices, even in harsh operating environments where exposure to aggressive chemicals is every day.
Temperature Stability:
- Epoxy potting compounds demonstrate exceptional temperature stability, maintaining their properties and performance across various temperatures.
- Epoxy-encapsulated devices remain unaffected in extremely cold or high-temperature environments, ensuring consistent functionality and reliability.
Easy Application:
- Epoxy potting compounds are easy to apply and allow for efficient encapsulation of components through various methods such as casting, molding, or dispensing.
- Their low-viscosity formulations enable the complete filling of intricate cavities and voids, ensuring uniform encapsulation and reliable protection.
Long-Term Reliability:
- Epoxy potting compounds are renowned for their long-term reliability. They have proven track records of providing robust protection to encapsulated components for extended periods.
- Their resistance to aging, UV radiation, and thermal cycling ensures the longevity of electronic devices, minimizing maintenance and replacement costs.
Where Are Epoxy Potting Compounds Used?
Epoxy potting compounds are resinous materials widely used in various industries for encapsulating and protecting electronic components. Their versatility, durability, and excellent electrical insulation properties make them indispensable in numerous applications. Let’s delve into the diverse uses of epoxy potting compounds across different sectors:
Electronics Industry:
- Printed Circuit Boards (PCBs):Epoxy potting compounds are commonly utilized to encapsulate and protect PCBs from moisture, dust, and mechanical stresses. It enhances their reliability and longevity in demanding environments.
- LED Lighting:Epoxy potting compounds play a crucial role in sealing LED modules, ensuring their protection against environmental factors while maintaining optimal thermal management for enhanced performance and longevity.
- Power Supplies:Electronic components within power supplies often face harsh operating conditions. Epoxy potting compounds provide excellent thermal conductivity and electrical insulation, safeguarding these components from damage.
Automotive Sector:
- Electronic Control Units (ECUs):Epoxy potting compounds encapsulate ECUs, protecting them from vibrations, thermal cycling, and exposure to automotive fluids. It ensures the reliability and longevity of critical vehicle systems.
- Sensors and Actuators:Epoxy potting compounds offer robust protection to sensors and actuators used in automotive applications, shielding them from moisture, chemicals, and mechanical stresses encountered on the road.
Aerospace and Aviation:
- Avionics:Epoxy potting compounds are employed in avionics systems to encapsulate sensitive electronic components, ensuring their performance and reliability under extreme temperature variations and high-altitude conditions.
- Communication Systems:Satellites, aircraft communication systems, and radar equipment rely on epoxy potting compounds to protect critical electronics from the rigors of space and aviation environments, including radiation and thermal cycling.
Renewable Energy:
- Solar Power:Epoxy potting compounds are utilized in solar inverters and charge controllers to protect sensitive electronics from environmental factors and ensure efficient energy conversion over the lifespan of solar installations.
- Wind Turbines:Electronic components within wind turbine control systems are encapsulated with epoxy potting compounds to withstand the challenging conditions of wind farms, including moisture, temperature fluctuations, and mechanical stresses.
Industrial Applications:
- Automation and Robotics:Epoxy potting compounds find applications in industrial automation and robotics to protect electronic controllers, sensors, and actuators from harsh operating environments, including exposure to chemicals and contaminants.
- Underwater Equipment: Subsea electronics used in marine exploration, oil and gas production, and underwater communication systems are encapsulated with epoxy potting compounds to withstand high pressure, corrosion, and moisture.
What Makes Up the Composition of Epoxy Potting Compounds?
Epoxy Potting Compounds stand out as a reliable choice for encapsulating electronic components. These compounds offer robust protection against environmental factors, mechanical stress, and chemical agents, ensuring the longevity and performance of sensitive electronics. But what exactly constitutes these formidable compounds? Let’s delve into the composition of Epoxy Potting Compounds to understand their inner workings.
Epoxy Resin:
- The backbone of Epoxy Potting Compounds is epoxy resin, a versatile polymer known for its excellent adhesive properties and chemical resistance.
- Epoxy resin forms the matrix where other components are suspended, providing structural integrity and insulation.
Hardener:
- A hardener, a curing agent or catalyst, initiates the chemical reaction that transforms the epoxy resin from a liquid to a solid state.
- Different hardeners, such as amines or anhydrides, offer varying curing times and temperature requirements, allowing for customization based on application needs.
Fillers:
- Fillers are added to epoxy potting compounds to enhance thermal conductivity, electrical insulation, or flame retardancy.
- Common fillers include silica, alumina, and various mineral compounds, each contributing to the compound’s overall performance.
Plasticizers:
- Plasticizers are incorporated to modify the flexibility and elasticity of the cured epoxy.
- By adjusting the concentration of plasticizers, manufacturers can tailor the hardness and impact resistance of the potting compound to suit the intended application.
Modifiers:
- Modifiers are additives that impart additional characteristics to the epoxy potting compound, such as UV resistance, color stability, or resistance to thermal cycling.
- Examples of modifiers include UV stabilizers, pigments, and toughening agents like elastomers.
Solvents and Diluents:
- Solvents and diluents are used to adjust the viscosity of the epoxy resin, facilitating easy application and ensuring optimal flow around intricate components.
- These additives evaporate during curing, leaving behind a homogeneous and void-free encapsulation.
Adhesion Promoters:
- Adhesion promoters are surface-active agents that improve the bonding between the epoxy potting compound and the substrate.
- Proper adhesion is crucial for preventing delamination and ensuring long-term reliability in harsh operating environments.
Flame Retardants:
- In applications where fire safety is paramount, flame retardants are incorporated into epoxy potting compounds to inhibit the spread of flames and reduce smoke emissions.
- Phosphorus-based compounds and halogen-free additives are commonly used as flame retardants in epoxy formulations.
Are There Different Types of Epoxy Potting Compounds?
Epoxy potting compounds are versatile materials used for encapsulating and protecting electronic components. They provide electrical insulation, thermal conductivity, and mechanical support, ensuring the longevity and reliability of electronic devices.
Types of Epoxy Potting Compounds
Standard Epoxy Potting Compounds:
Formulated for general-purpose applications.
- Provide essential protection against moisture, vibration, and thermal cycling.
- Suitable for indoor use where exposure to harsh environments is minimal.
Thermally Conductive Epoxy Potting Compounds:
Designed to dissipate heat effectively from enclosed components.
- Enhance thermal management, preventing overheating and thermal stress.
- It is ideal for high-power electronic devices, LED lighting, and automotive applications.
Electrically Conductive Epoxy Potting Compounds:
It is formulated to maintain electrical conductivity while providing encapsulation.
- They are used in applications requiring grounding, EMI shielding, or electrical connections.
- They are commonly employed in electronics, telecommunications, and aerospace industries.
Flexible Epoxy Potting Compounds:
Offer flexibility and resilience, accommodating component expansion and contraction.
- Provide excellent shock absorption and vibration dampening.
- Suitable for applications subjected to mechanical stress or dynamic movements.
High-Temperature Epoxy Potting Compounds:
Withstand elevated temperatures without losing their structural integrity.
- Resist thermal degradation and maintain performance in extreme conditions.
- Essential for applications exposed to heat, such as automotive under-the-hood electronics and industrial machinery.
UL Listed Epoxy Potting Compounds:
Comply with specific safety standards set by Underwriters Laboratories (UL).
- Rigorous measures are implemented to ensure reliability and safety in electrical systems.
- They are widely used in consumer electronics, appliances, and medical devices.
Factors Influencing Selection
- Operating Environment:Consider temperature extremes, moisture levels, chemical exposure, and mechanical stress.
- Electrical Properties:Determine whether electrical insulation or conductivity is required.
- Thermal Management Needs:Assess the heat dissipation requirements of the components.
- Regulatory Compliance:Ensure adherence to industry standards and regulations.
- Application Specifics:Tailor the choice based on the specific demands of the application.
How Do You Select the Right Epoxy Potting Compound for Your Application?
Are you looking to safeguard electronic components from environmental factors such as moisture, dust, and vibration? Epoxy potting compounds could be your solution. However, selecting the suitable epoxy potting compound can take time and effort with many options available. Let’s delve into the key factors you must consider to make an informed decision.
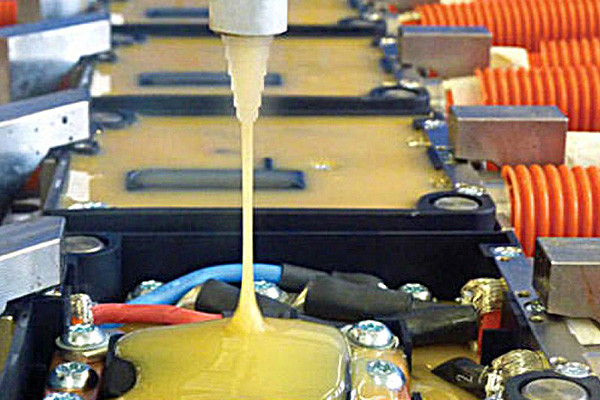
Factors to Consider When Selecting Epoxy Potting Compounds:
Environmental Conditions:
- Determine the specific environmental factors your application will face (moisture, temperature extremes, chemicals, etc.).
- Choose a potting compound with appropriate resistance properties to ensure longevity and reliability in your environment.
Operating Temperature Range:
- Consider the temperature range your electronic components will be exposed to during operation.
- Select an epoxy potting compound with a suitable temperature rating to prevent degradation or failure under extreme conditions.
Curing Time and Process:
- Evaluate the curing time required for the epoxy potting compound and match it with your production schedule.
- Determine whether your application requires a room temperature or heat-cured epoxy for optimal performance.
Mechanical Properties:
- Assess the mechanical requirements of your application, such as flexibility, hardness, and impact resistance.
- Choose a potting compound with mechanical properties that align with the demands of your specific application to prevent cracking or delamination.
Chemical Resistance:
- Identify any potential exposure to chemicals or solvents in your operating environment.
- Select an epoxy potting compound with excellent chemical resistance to ensure long-term stability and performance.
Electrical Insulation Properties:
- Evaluate the electrical insulation requirements of your electronic assembly.
- Choose a potting compound with high dielectric strength and low electrical conductivity to prevent short circuits and electrical failures.
Adhesion to Substrates:
- Consider the materials of your electronic components and substrates.
- Ensure compatibility by selecting an epoxy potting compound with solid adhesion properties to your substrates, minimizing the risk of delamination or separation.
Cost and Quantity:
- Determine your project’s budget constraints and the required quantity of epoxy potting compound.
- Strike a balance between performance requirements and cost-effectiveness to meet your application needs within budget constraints.
What Advantages Do Epoxy Potting Compounds Offer?
In the world of electronics, protection is paramount. Devices and components must withstand harsh environments, vibrations, moisture, and more without compromising performance. This is where epoxy potting compounds come into play, offering a robust solution to safeguard sensitive electronics. Let’s delve into the advantages these compounds offer.
Superior Protection:
- Epoxy potting compounds provide an encapsulating barrier around electronic components, shielding them from moisture, dust, chemicals, and physical damage.
- This protection extends the lifespan of the devices, ensuring reliable performance even in challenging conditions.
Excellent Insulation Properties:
- These compounds possess high dielectric strength, effectively insulating components against electrical currents.
- By preventing electrical leakage and short circuits, epoxy potting compounds enhance the safety and reliability of electronic systems.
Enhanced Thermal Management:
- Epoxy potting compounds exhibit excellent thermal conductivity, dissipating heat efficiently from electronic components.
- It prevents overheating, leading to performance degradation or failure, particularly in high-power applications.
Chemical Resistance:
- With their robust chemical composition, epoxy potting compounds resist various chemicals, including solvents, oils, and acids.
- This feature is crucial in industrial settings where corrosive substances are exposed daily.
Flexibility and Durability:
- Epoxy potting compounds offer flexibility, allowing them to conform to complex shapes and intricate designs, ensuring complete coverage and protection.
- Their durable nature ensures long-term performance, withstanding mechanical stresses and environmental factors without degradation.
Simplified Manufacturing Processes:
- Potting electronic components with epoxy compounds streamlines the manufacturing process by eliminating the need for additional protective measures.
- It reduces assembly time and labor costs while improving product consistency and quality.
Wide Range of Applications:
- Epoxy potting compounds find applications across various industries, including automotive, aerospace, telecommunications, and renewable energy.
- These compounds offer reliable protection in diverse environments, from automotive control modules to aerospace avionics.
Compliance with Industry Standards:
- Many epoxy potting compounds adhere to industry standards and certifications, ensuring compliance with safety and performance requirements.
- It gives manufacturers confidence in the reliability and quality of their products, meeting regulatory expectations.
What Are the Key Properties of Epoxy Potting Compounds?
When encapsulating electronic components or sealing sensitive devices, epoxy potting compounds are popular among engineers and manufacturers. These versatile materials offer a range of essential properties that ensure reliable protection and performance in various applications. Let’s delve into the fundamental properties that make epoxy potting compounds indispensable in the realm of electronics:
Chemical Resistance:
- Epoxy potting compounds exhibit exceptional resistance to various chemicals, including solvents, fuels, and acids. This property ensures longevity and reliability, even in harsh environments where exposure to corrosive substances is prevalent.
Electrical Insulation:
- One primary function of epoxy potting compounds is to provide electrical insulation. These compounds effectively shield electronic components from moisture and contaminants, thereby preventing short circuits and ensuring the integrity of electrical systems.
Thermal Stability:
- With their high thermal conductivity and heat dissipation capabilities, epoxy potting compounds offer superior thermal stability. They can withstand elevated temperatures without compromising their structural integrity, making them ideal for applications exposed to thermal stress.
Mechanical Strength:
- Epoxy potting compounds boast excellent mechanical properties, including high tensile and flexural strength. This inherent strength protects against mechanical shocks, vibrations, and impacts, safeguarding delicate electronic components from damage.
Adhesion:
- These compounds form strong bonds with various substrates, including metals, plastics, and ceramics. The exceptional adhesion of epoxy potting compounds ensures secure encapsulation and prevents moisture ingress, enhancing the durability and reliability of electronic assemblies.
Low Shrinkage:
- Epoxy potting compounds undergo minimal shrinkage during curing, maintaining dimensional stability and preventing stress buildup within the encapsulated components. This property eliminates the risk of cracking or delamination, ensuring long-term performance and reliability.
Environmental Compatibility:
- Epoxy potting compounds are formulated to meet stringent environmental standards, making them suitable for applications where regulatory compliance is essential. These compounds are free from hazardous substances such as volatile organic compounds (VOCs) and comply with RoHS directives.
Versatility:
- From automotive electronics to aerospace systems and industrial machinery, epoxy potting compounds find application in diverse industries. Their versatility allows engineers to tailor formulations to meet specific performance requirements, ensuring optimal performance in various environments and conditions.
Can Epoxy Potting Compounds Withstand Harsh Environmental Conditions?
Epoxy potting compounds have emerged as a go-to solution for encapsulating electronic assemblies, offering protection against moisture, chemicals, and mechanical stress. But the question remains: Can epoxy potting compounds withstand harsh environmental conditions? Let’s delve into this topic and uncover their resilience.
Understanding Epoxy Potting Compounds:
- Epoxy potting compounds are thermosetting polymers that, when cured, form a challenging and resilient encapsulant around electronic components.
- They are widely used in industries such as automotive, aerospace, marine, and telecommunications for their ability to provide excellent protection against environmental factors.
Factors Contributing to Resilience:
- Chemical Resistance:Epoxy potting compounds exhibit high resistance to various chemicals, including solvents, acids, and bases, making them suitable for applications in corrosive environments.
- Moisture Barrier:These compounds create a moisture-resistant barrier, preventing water ingress and safeguarding electronic components from moisture-induced damage.
- Thermal Stability:Epoxy potting compounds offer excellent thermal stability, maintaining their properties over a wide temperature range, from extreme cold to high heat.
- Mechanical Strength:Once cured, epoxy potting compounds form a robust and durable encapsulation capable of withstanding mechanical stress and vibration.
Performance in Harsh Environments:
- Extreme Temperatures:Epoxy potting compounds demonstrate resilience in both high and low-temperature environments, ensuring the integrity of electronic assemblies even under extreme thermal conditions.
- Chemical Exposure:Their resistance to chemicals makes epoxy potting compounds ideal for applications where exposure to harsh chemicals is a concern, such as industrial settings or automotive under-the-hood environments.
- Outdoor Applications:Epoxy potting compounds offer UV stability, preventing degradation from prolonged exposure to sunlight, making them suitable for outdoor applications like solar panels or outdoor lighting systems.
- Underwater Environments:Due to their moisture barrier properties, epoxy potting compounds are frequently utilized in underwater applications, including marine electronics and submersible devices.
Considerations for Application:
- Proper Selection:Choosing the suitable epoxy potting compound is crucial, considering factors such as the operating environment, temperature range, and specific performance requirements.
- Curing Conditions: Proper curing conditions, including temperature and humidity, are essential to achieving optimal performance and durability.
- Compatibility:It’s important to ensure compatibility between the potting compound and the materials it will contact, such as PCB substrates and component coatings.
How Important Is Proper Mixing and Curing of Epoxy Potting Compounds?
Before delving into the significance of mixing and curing, it’s crucial to grasp the fundamentals of epoxy potting compounds. These compounds are formulated to encapsulate electronic components, creating a protective barrier against environmental factors such as moisture, dust, vibration, and thermal stress.
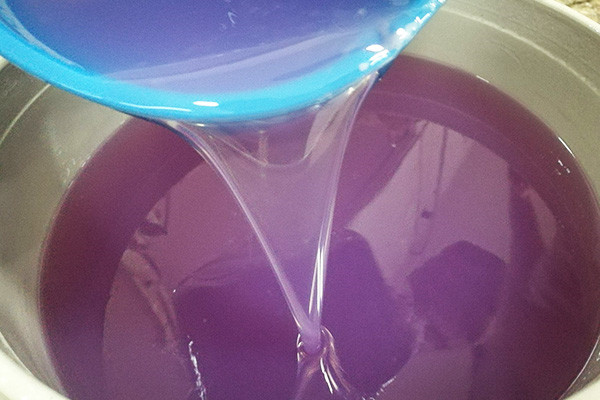
Importance of Proper Mixing:
Proper mixing of epoxy potting compounds ensures uniformity and consistency throughout encapsulation. Here’s why it matters:
- Homogeneous Dispersion:Thorough mixing facilitates the even distribution of resin and hardener components, preventing pockets of uneven curing that can compromise the integrity of the encapsulation.
- Chemical Reaction:Epoxy compounds undergo a chemical reaction when resin and hardener are mixed. Inadequate mixing can result in incomplete curing, leading to soft spots or brittleness within the encapsulation, which may reduce its protective capabilities.
- Optimized Properties:Well-mixed compounds exhibit optimized mechanical, thermal, and electrical properties, enhancing the performance and longevity of encapsulated devices.
The Role of Proper Curing:
Curing epoxy potting compounds transforming from liquid to solid is equally critical. Here’s why it cannot be overlooked:
- Cross-Linking:During curing, the resin and hardener molecules undergo cross-linking, forming a three-dimensional network that provides structural stability and chemical resistance to the encapsulation.
- Bond Strength:Adequate curing ensures strong adhesion between the encapsulant and the components, minimizing the risk of delamination or separation under stress conditions.
- Dimensional Stability:Proper curing prevents shrinkage or expansion of the encapsulant, maintaining dimensional stability and avoiding strain on sensitive components.
Consequences of Inadequate Mixing and Curing:
Failure to adhere to proper mixing and curing protocols can lead to several detrimental outcomes:
- Poor Adhesion:Incomplete curing or uneven mixing can result in poor adhesion between the encapsulant and the components, increasing the likelihood of moisture ingress or mechanical failure.
- Reduced Thermal Performance:Inadequate curing may compromise the thermal conductivity of the encapsulant, impeding heat dissipation and potentially leading to overheating of electronic components.
- Degradation Over Time:Compromised properties due to improper mixing or curing can lead to premature degradation of encapsulated devices, resulting in costly repairs or replacements.
What Techniques Are Used for Potting Electronic Components with Epoxy Compounds?
Epoxy potting compounds are an indispensable solution, offering robust protection against moisture, chemicals, shock, and vibration. But what techniques are used for effectively potting electronic components with epoxy compounds? Let’s delve into the intricacies:
- Encapsulation Process:The encapsulation process involves enclosing electronic components within a protective shell of epoxy resin. This process shields the components from external factors and enhances their durability and reliability.
- Selection of Epoxy Compounds:Choosing the suitable epoxy compound is crucial. Factors such as thermal conductivity, viscosity, curing time, and chemical resistance must be considered based on the specific application requirements.
- Surface Preparation:Surface preparation ensures strong adhesion between the epoxy compound and the electronic components. It involves thorough cleaning and, in some cases, roughening or priming of the surfaces to promote bonding.
- Dispensing Techniques:Various dispensing techniques are employed depending on the nature of the electronic components and the desired encapsulation. These techniques include manual dispensing using syringes or automated dispensing systems for precision and consistency.
- Vacuum Potting:Vacuum potting is a technique used to remove air bubbles trapped within the epoxy compound. This process helps minimize voids and ensures uniform encapsulation, thereby enhancing the overall performance and reliability of the potted components.
- Curing Process:Proper curing of the epoxy compound is essential for achieving optimal mechanical and chemical properties. Curing can be achieved through heat, UV radiation, or chemical reactions, depending on the specific formulation of the epoxy compound.
- Temperature Control:Maintaining proper temperature control during potting is critical to prevent premature curing or incomplete encapsulation. Temperature-controlled environments ensure consistent results and prevent potential issues such as cracking or delamination.
- Quality Control and Testing:Rigorous quality control measures and testing protocols are implemented to ensure the integrity and reliability of the potted electronic components. It includes visual inspection, mechanical testing, and environmental testing to assess performance under various conditions.
- Customization and Flexibility:Epoxy potting compounds offer a high degree of customization and flexibility to accommodate diverse applications and requirements. Formulations can be tailored to meet specific performance criteria, such as thermal conductivity or flame resistance.
- Environmental Considerations:Environmental considerations play a significant role in selecting and applying epoxy potting compounds. Eco-friendly formulations with low volatile organic compound (VOC) emissions are increasingly preferred to minimize environmental impact.
Are There Any Regulatory Considerations for Using Epoxy Potting Compounds?
Ensuring compliance with regulatory standards is paramount in the intricate landscape of electronics manufacturing. Manufacturers must navigate various regulatory considerations when utilizing epoxy potting compounds to guarantee product safety, environmental responsibility, and legal adherence. Let’s explore these considerations in detail:
- RoHS Compliance: The Restriction of Hazardous Substances (RoHS) directive restricts using certain hazardous materials, including lead, mercury, cadmium, and specific flame retardants, in electronic products. Epoxy potting compounds must comply with RoHS regulations to ensure they do not contain restricted substances above specified thresholds.
- REACH Regulations:The Registration, Evaluation, Authorization, and Restriction of Chemicals (REACH) regulation aims to protect human health and the environment from the risks posed by chemicals. Manufacturers using epoxy potting compounds must ensure compliance with REACH requirements by registering substances, assessing risks, and implementing appropriate risk management measures.
- UL Certification: Underwriters Laboratories (UL) certification signifies that a product has undergone rigorous testing and meets the safety standards set by UL. Epoxy potting compounds may require UL certification to comply with specific safety criteria, ensuring their suitability for electronic applications.
- Flammability Ratings:To mitigate fire risks, epoxy potting compounds used in electronics may need to meet specific flammability ratings, such as UL 94V-0. These ratings indicate the material’s ability to self-extinguish when exposed to flames, thus enhancing overall safety.
- Environmental Regulations: Environmental regulations, such as the Waste Electrical and Electronic Equipment (WEEE) directive, govern the disposal and recycling of electronic products. Manufacturers must consider the environmental impact of epoxy potting compounds throughout their lifecycle, from production to end-of-life disposal or recycling.
- VOC Emissions: Volatile organic compound (VOC) emissions from epoxy potting compounds can adversely affect air quality and human health. Compliance with regulations limiting VOC emissions is essential to mitigate environmental impact and ensure product safety.
- Food Contact Regulations: Epoxy potting compounds used in electronic devices intended for food processing or packaging applications must comply with regulations governing materials in contact with food. These regulations ensure that materials do not harm food safety or human health.
- International Standards: Besides regional regulations, international standards such as ISO 9001 (quality management) and ISO 14001 (environmental management) provide frameworks for ensuring consistency, quality, and environmental responsibility in manufacturing processes involving epoxy potting compounds.
- Documentation and Compliance Reporting: Maintaining comprehensive documentation and compliance records is essential for adhering to regulatory requirements. It includes material safety data sheets (MSDS), compliance certificates, test reports, and other relevant documentation.
What Innovations Are Driving the Evolution of Epoxy Potting Compounds?
Epoxy potting compounds have long been indispensable in various industries, offering superior protection and insulation to electronic components. As technology advances, so do the demands placed on these compounds. Let’s delve into the innovations propelling the evolution of epoxy potting compounds:
Nanotechnology Integration:
- Nanoparticles are incorporated into epoxy formulations to enhance mechanical, thermal, and electrical properties.
- It improved filler dispersion at the nanoscale level, resulting in strength and conductivity.
Sustainable Formulations:
- Manufacturers increasingly focus on eco-friendly alternatives, utilizing renewable raw materials and reducing VOC emissions.
- Bio-based epoxy resins derived from plant sources offer a greener option without compromising performance.
Enhanced Thermal Management:
- Advanced epoxy formulations now boast superior thermal conductivity, dissipating heat more efficiently.
- It ensures optimal operating temperatures for electronic devices, mitigating the risk of overheating.
Flexibility and Toughness:
- Innovations in epoxy chemistry have led to compounds with enhanced flexibility and toughness.
- These compounds can withstand mechanical stress, vibration, and thermal cycling without compromising protection.
Rapid Cure Systems:
- Developments in curing agents and additives have resulted in rapid-cure epoxy systems.
- Reduced curing times improve manufacturing efficiency while maintaining excellent performance properties.
Flame Retardant Solutions:
- With increasing safety regulations, epoxy potting compounds are now formulated with highly effective flame retardants.
- These compounds offer superior fire protection without sacrificing other desirable properties.
Adhesion to Diverse Substrates:
- Innovations in adhesion promoters enable epoxy compounds to bond effectively with various substrates.
- This ensures reliable encapsulation and protection for various electronic components.
Customizable Properties:
- Manufacturers are offering customizable epoxy formulations tailored to specific application requirements.
- Customers can choose properties such as hardness, flexibility, and thermal conductivity to suit their needs.
Can You Share Real-world Applications of Epoxy Potting Compounds?
Epoxy potting compounds are versatile materials widely used across various industries for encapsulating and protecting electronic components. Their exceptional properties make them indispensable in numerous applications, ensuring durability, insulation, and resistance to environmental factors. Let’s delve into some real-world scenarios where epoxy potting compounds play a crucial role:
Electronics Industry:
- Printed Circuit Boards (PCBs): Epoxy potting compounds provide insulation and protection to delicate electronic components on PCBs, safeguarding against moisture, dust, and vibrations.
- LED Lighting:LED modules are potted with epoxy to enhance thermal conductivity, prolonging LEDs’ lifespan by effectively dissipating heat.
- Automotive Electronics:Epoxy potting compounds in vehicles shield sensitive electronic components from harsh operating conditions, including temperature fluctuations, vibrations, and chemical exposure.
Aerospace and Defense:
- Avionics:Epoxy potting compounds protect critical avionics systems from extreme temperatures, shock, and vibration encountered during flight.
- Military Electronics:These compounds protect military-grade electronic equipment robustly, ensuring reliable performance in demanding environments such as combat zones and rugged terrains.
Renewable Energy:
- Solar Power Systems:Epoxy potting compounds encapsulate solar panels’ junction boxes, safeguarding them against moisture ingress and environmental degradation.
- Wind Turbines:Electronic components within wind turbine controllers are potted with epoxy to enhance reliability and longevity, even in offshore and high-altitude installations.
Industrial Automation:
- Sensor Systems:Epoxy potting compounds protect sensors used in industrial automation applications from corrosive chemicals, extreme temperatures, and mechanical stress.
- Control Systems:Potting electronics in control systems ensures reliable operation in harsh industrial environments, including manufacturing plants and chemical processing facilities.
Consumer Electronics:
- Wearable Devices:Epoxy potting compounds protect electronic components in wearable devices, enhancing durability and water resistance.
- Home Appliances:In appliances like washing machines and refrigerators, critical electronic modules are encapsulated with epoxy to ensure reliable performance and safety.
What Challenges Are Associated with Using Epoxy Potting Compounds?
Epoxy potting compounds are widely utilized in various industries for their excellent electrical insulation properties and ability to protect electronic components from environmental factors. However, despite their numerous advantages, several challenges are associated with their usage. Let’s delve into these challenges:
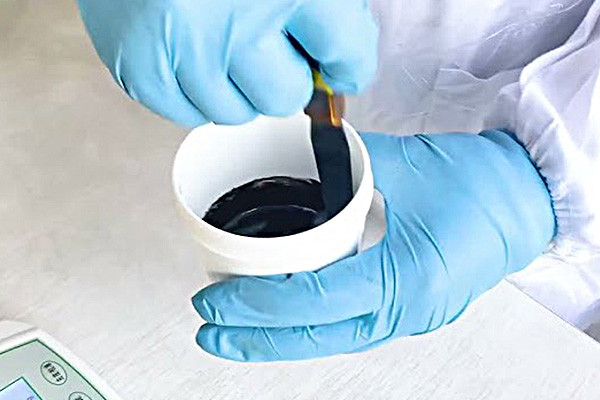
Thermal Management:
- Epoxy potting compounds have relatively poor thermal conductivity compared to other potting materials.
- It can cause heat to build up in the potted electronic assembly, leading to potential overheating issues.
Curing Time and Process:
- Epoxy compounds require a specific curing time and process for optimal performance.
- Inadequate or incorrect curing conditions can result in incomplete encapsulation or compromised mechanical properties.
Chemical Compatibility:
- Epoxy potting compounds may not be compatible with certain chemicals or solvents in the operating environment.
- Exposure to incompatible substances can lead to epoxy material degradation, compromising encapsulated components’ integrity.
Mechanical Strength and Flexibility:
- Achieving the right mechanical strength and flexibility balance in epoxy potting compounds can be challenging.
- Brittleness or lack of flexibility may result in stress concentration points, leading to mechanical failure under vibration or mechanical shock conditions.
Adhesion to Substrates:
- Ensuring proper adhesion of epoxy potting compounds to various substrates can be tricky.
- Poor adhesion may result in delamination or detachment of the epoxy from the substrate, jeopardizing the protection of the electronic components.
Moisture Ingress:
- Epoxy potting compounds may be susceptible to moisture ingress over time, especially if not properly formulated or cured.
- Moisture infiltration can lead to corrosion of sensitive electronic components, ultimately affecting the performance and reliability of the device.
How Can Manufacturers Ensure Cost-effectiveness When Using Epoxy Potting Compounds?
Due to their exceptional properties and versatility, epoxy potting compounds have become indispensable in various manufacturing processes. However, to ensure maximum cost-effectiveness, manufacturers need to implement strategic approaches in their utilization. Here are some key considerations:
Material Selection:
- Choose epoxy potting compounds that offer the best balance between cost and performance.
- Consider the specific requirements of your application to avoid over-specification of materials, which can unnecessarily inflate costs.
Quantity Optimization:
- Purchase epoxy potting compounds in bulk quantities to benefit from volume discounts.
- Forecast demand accurately to prevent overstocking or underutilization, which can lead to additional expenses.
Process Efficiency:
- Implement streamlined potting processes to minimize material waste and labor costs.
- Invest in automated dispensing equipment to ensure precise application and reduce manual errors.
Material Handling and Storage:
- Properly store epoxy potting compounds according to manufacturer guidelines to prevent degradation and spoilage.
- Use appropriate handling techniques to avoid spills and product loss, which can add to overall expenses.
Quality Assurance:
- Conduct thorough testing and validation procedures to ensure the selected epoxy potting compounds meet performance requirements.
- Prioritize reliability and longevity to avoid future rework or replacement costs.
Supplier Partnerships:
- Establish strong relationships with reputable suppliers to negotiate favorable pricing terms and access to technical support.
- Explore alternative suppliers periodically to benchmark costs and maintain competitiveness.
Environmental Considerations:
- Opt for eco-friendly epoxy potting compounds that comply with regulatory standards to avoid fines or penalties.
- Assess the long-term environmental impact of chosen materials to mitigate potential liabilities.
Are There Any Emerging Trends in the Field of Epoxy Potting Compounds?
Epoxy potting compounds protect electronic components from environmental factors like moisture, heat, and mechanical stress. As technology advances, so do the demands placed on these compounds. Let’s delve into some emerging trends in the field of epoxy potting compounds:
Eco-friendly Formulations:
- With increasing awareness of environmental issues, there’s a growing demand for epoxy potting compounds formulated with sustainable and biodegradable materials.
- Manufacturers are exploring renewable sources and recyclable components to reduce the environmental footprint of these compounds.
Enhanced Thermal Conductivity:
- As electronic devices become more compact and powerful, there’s a need for epoxy potting compounds with improved thermal conductivity to dissipate heat effectively.
- Innovations in filler materials and formulation techniques drive the development of compounds capable of efficiently managing heat dissipation.
Miniaturization and High Precision:
- The trend towards miniaturization in electronics requires epoxy potting compounds to fill increasingly smaller gaps and voids without sacrificing performance.
- Advanced dispensing technologies and ultra-low viscosity formulations enable precise application in densely packed electronic assemblies.
Increased Resistance to Harsh Environments:
- Industries such as automotive, aerospace, and oil & gas demand epoxy potting compounds that can withstand extreme temperatures, vibrations, and chemical exposure.
- Novel additives and cross-linking agents are incorporated into formulations to enhance resistance to harsh environmental conditions.
Adoption of Nanotechnology:
- Nanoparticle additives offer opportunities to improve the mechanical strength, electrical insulation, and thermal conductivity of epoxy potting compounds.
- Nanotechnology enables the development of lightweight yet robust compounds suitable for demanding applications in various industries.
Smart and Functionalized Compounds:
- With the rise of IoT and smart devices, there’s a growing need for epoxy potting compounds with built-in functionalities such as self-healing, self-adhesion, and even sensing capabilities.
- Integrating innovative materials and additives enables the creation of multifunctional compounds that can adapt to changing conditions and extend the lifespan of electronic components.
What Are Some Best Practices for Handling and Applying Epoxy Potting Compounds?
Epoxy potting compounds protect sensitive electronic components from environmental stresses like temperature variations, vibrations, and chemical exposure. However, proper handling and application techniques are essential to ensure optimal performance and longevity of these compounds. Let’s delve into some best practices for handling and applying epoxy potting compounds:
Preparation is Key:
- Thoroughly clean and dry the surfaces to be potted to remove any contaminants.
- Ensure all components are securely positioned within the enclosure to prevent movement during potting.
Select the Right Compound:
- When choosing an epoxy potting compound, consider operating temperature range, flexibility, and chemical resistance.
- Consult manufacturers or suppliers to select a compound tailored to your application requirements.
Follow Mixing Instructions:
- Adhere strictly to the manufacturer’s recommended mixing ratios and procedures to achieve the desired chemical and physical properties.
- Use calibrated measuring tools to ensure accuracy in mixing.
Mind the Pot Life:
- Work efficiently within the specified pot life of the epoxy compound to prevent premature curing.
- Avoid mixing large batches if the potting process is time-consuming to prevent waste.
Apply Uniformly:
- Use appropriate tools such as syringes, dispensing guns, or automated equipment to apply the epoxy compound evenly.
- Ensure that the compound fills all voids and encapsulates the components thoroughly.
Minimize Air Entrapment:
- Degassing the mixed epoxy before application can help reduce the presence of air bubbles, ensuring void-free potting.
- Employ vacuum degassing chambers or apply gentle agitation to release the trapped air.
Cure Properly:
- Allow sufficient time for the epoxy potting compound to cure at the recommended temperature and humidity conditions.
- Avoid disturbing the potting assembly during the curing process to prevent imperfections.
Inspect and Test:
- After curing, visually inspect the potted components for any defects or irregularities.
- Perform electrical and mechanical tests to ensure the encapsulated components meet performance specifications.
Conclusion
Epoxy potting compounds stand as a cornerstone in electronic manufacturing, offering unparalleled protection and insulation to sensitive components. By addressing common questions and delving into the nuances of these compounds, we’ve shed light on their importance and potential. Armed with this knowledge, engineers and manufacturers can confidently harness the power of epoxy potting compounds to elevate the reliability and durability of electronic systems across various industries.
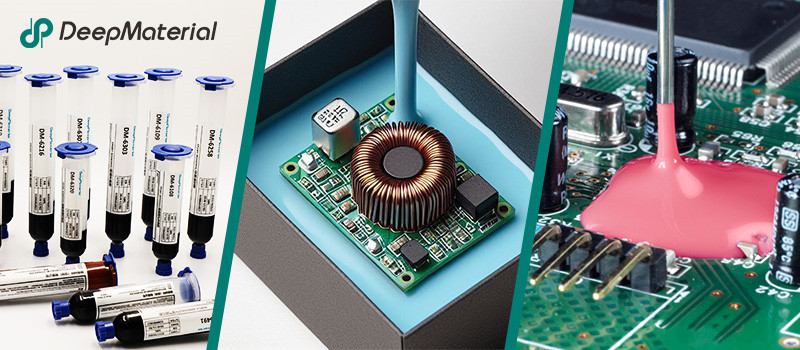
About DeepMaterial
DeepMaterial is a trusted supplier of encapsulant materials that are used in electronics manufacturing worldwide. From chip on board encapsulants such as glob top material to conformal coatings, underfills, low pressure molding, and potting solutions, DeepMaterial offers a full range of circuit board protection materials that effectively protect circuit boards while help reduce costs. More…Deepmaterial is a the manufacturer of epoxy adhesives including hardeners, metalbond, and metal filled resins. Structural, toughened medium viscosity, and non-sag adhesives are also offered. Some adhesives are resistant to thermal shock, chemical, vibration dampening, and impact. Suitable for metals, plastics, wood, and ceramics. Serves electronics, aerospace, automotive, tooling, marine, and construction industries. REACH and RoHS compliant. FDA approved. UL listed. Meets military specifications. We are the one of best adhesive manufacturers in China.
Blogs & News
Potting compounds are at the frontline of electronics assembly, delivering effective protection in challenging environmental conditions while improving mechanical strength and offering high electric insulation. Used within a variety of industries, electrical potting compounds are found within a broad range of consumer electronics, as well as used in applications across the automotive, aerospace, and other industries where electronic assemblies are prevalent.
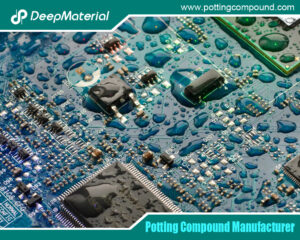
The Comprehensive Guide to Epoxy Potting Compound Manufacturers
The Comprehensive Guide to Epoxy Potting Compound Manufacturers Epoxy potting compounds are essential materials in the electronics industry, providing robust protection for sensitive components against
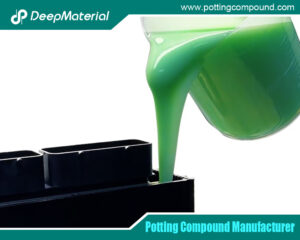
The Essential Guide to Potting Materials for Electronics
The Essential Guide to Potting Materials for Electronics In the rapidly evolving field of electronics, ensuring device reliability and longevity is critical. One of the
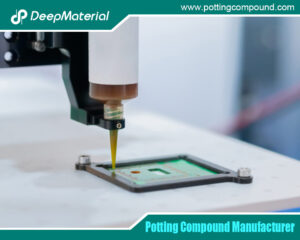
The Expanding Horizon of the Mini Silicone Optical Glue Market
The Expanding Horizon of the Mini Silicone Optical Glue Market The mini silicone optical glue market is witnessing unprecedented growth, fueled by technological advancements and
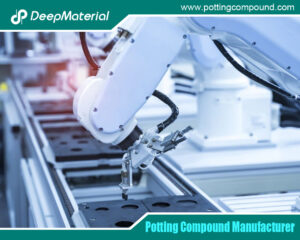
The Comprehensive Guide to PCB Potting Services: Ensuring Reliability in Electronics
The Comprehensive Guide to PCB Potting Services: Ensuring Reliability in Electronics Printed Circuit Boards (PCBs) are the backbone of modern electronics, enabling functionality in
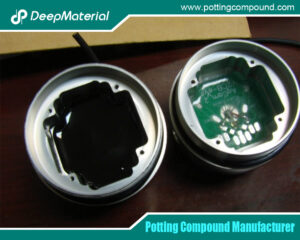
Comprehensive Insights on PCB Encapsulation in Potting Material
Comprehensive Insights on PCB Encapsulation in Potting Material In the fast-evolving landscape of electronics, ensuring the durability, reliability, and longevity of printed circuit boards
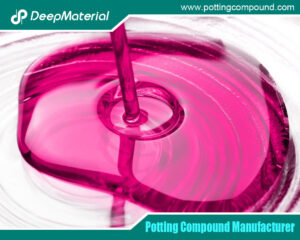
The Vital Role of Industrial Silicone Adhesive Manufacturers in Modern Industry
The Vital Role of Industrial Silicone Adhesive Manufacturers in Modern Industry In today’s fast-paced industrial landscape, the demand for reliable and durable adhesives is