UV Cure Conformal Coating
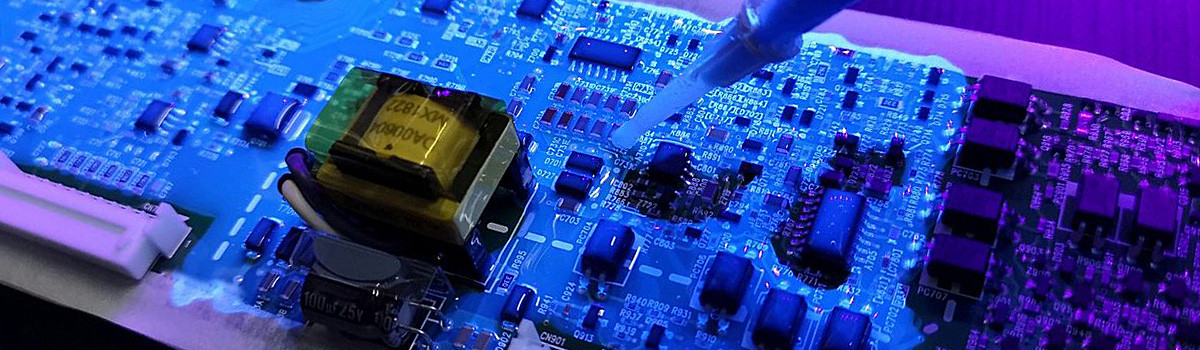
UV cure conformal coatings offer advanced protection for electronic components by providing a thin, durable, and protective layer that conforms to the contours of the substrate. These coatings are cured using ultraviolet (UV) light, providing rapid and efficient curing processes. They are widely used in various industries to safeguard electronic assemblies against environmental factors such as moisture, chemicals, dust, and temperature extremes.
Table of Contents
ToggleExplore the following questions to delve deeper into the world of UV cure conformal coatings:
What is UV cure conformal coating?
UV cure conformal coating is a specialized protective coating used in electronics manufacturing and other industries to safeguard sensitive electronic components from environmental factors such as moisture, dust, chemicals, and temperature fluctuations. This coating offers superior protection while maintaining the functionality and reliability of electronic devices. Here’s a breakdown of its key aspects:
- Composition: UV-cure conformal coatings are typically made from acrylic, epoxy, silicone, or polyurethane resins. These resins are formulated to provide excellent adhesion to various substrates, such as printed circuit boards (PCBs) and electronic components.
- Application Process: The application process involves dispensing the conformal coating onto the surface of the electronic assembly using techniques such as spraying, dipping, or brushing. Once applied, the coating is cured using ultraviolet (UV) light. The UV light triggers a photochemical reaction in the coating, causing it to cross-link and form a durable, protective layer.
- Fast Curing Time: One key advantage of UV-cured conformal coatings is their rapid curing time. Unlike traditional conformal coatings that require hours or even days to cure, UV-cured coatings can cure within seconds or minutes when exposed to UV light. This allows for increased efficiency in the manufacturing process, reducing production time and costs.
- Thin Film Thickness: UV cure conformal coatings can be applied in fragile layers, typically ranging from a few microns to tens of microns in thickness. This thin film thickness ensures that the coated electronic assembly maintains its dimensional integrity and does not interfere with the functionality of the components.
- High Performance: Despite their thinness, UV-cure conformal coatings offer high-performance protection against various environmental hazards. They provide excellent resistance to moisture, chemicals, abrasion, and thermal cycling, prolonging the lifespan and reliability of electronic devices.
- UV Inspection: UV cure conformal coatings can be formulated with fluorescent additives that fluoresce under UV light. This feature allows for easy inspection and quality control during manufacturing, ensuring uniform coverage and identifying any defects or inconsistencies in the coating application.
UV-cured conformal coating is a versatile and efficient solution for protecting electronic assemblies. It offers rapid curing, thin film thickness, and high-performance protection against environmental factors. Its application in electronics manufacturing helps enhance product reliability and longevity in various industries.
How does UV curing work in conformal coating?
UV curing in the conformal coating is widely utilized in electronics manufacturing to quickly and efficiently cure protective coatings applied to circuit boards. Conformal coatings are thin layers of material applied to electronic assemblies to protect them from environmental factors such as moisture, dust, chemicals, and temperature variations. UV curing involves using ultraviolet (UV) light to initiate a photochemical reaction in the coating material, leading to its rapid hardening or curing.
The process begins with applying a liquid conformal coating to the surface of the electronic assembly. This coating typically contains photoinitiators, chemical compounds that undergo a reaction when exposed to UV light. Photoinitiators are sensitive to specific wavelengths of UV light, commonly in the UVA and UVB ranges.
Once the coating is applied, the assembly is moved to a UV curing chamber or conveyor system with high-intensity UV lamps. These lamps emit UV light at the appropriate wavelength to activate the photoinitiators in the coating material. When exposed to UV light, the photoinitiators undergo a photopolymerization reaction, causing the coating to cross-link and form a hardened protective layer on the surface of the electronic components.
The UV curing is highly efficient and offers several advantages over traditional curing methods. It provides rapid curing times, allowing for increased production throughput and shorter cycle times. UV curing is also a “cold” process, meaning it does not generate excessive heat that could potentially damage sensitive electronic components. It also produces coatings with excellent adhesion and uniformity, ensuring reliable protection for the electronic assembly.
Furthermore, UV-cured coatings typically exhibit superior chemical and mechanical resistance compared to air-dried or heat-cured coatings. This makes them particularly well-suited for applications where durability and reliability are essential, such as automotive electronics, aerospace systems, and outdoor industrial equipment.
UV curing in conformal coating involves using UV light to initiate a photochemical reaction in the coating material, resulting in rapid curing and the formation of a protective layer on electronic assemblies. This process offers numerous benefits, including fast curing times, excellent adhesion, and enhanced durability, making it a preferred choice in electronics manufacturing.
What are the key benefits of UV-cure conformal coatings?
UV cure conformal coatings offer several key benefits, making them a popular choice for protecting electronic components and assemblies:
- Rapid Cure Time: UV cure conformal coatings cure almost instantly when exposed to ultraviolet light. This rapid cure time significantly reduces production time and allows for faster throughput in manufacturing processes. Compared to traditional coatings that may require long curing, UV cure coatings offer near-instantaneous hardening, enhancing efficiency and productivity.
- Energy Efficiency: UV cure coatings require minimal energy consumption during curing. The UV light source used for curing consumes less power than heat-curing methods, lowering energy costs and reducing environmental impact. This energy efficiency contributes to sustainable manufacturing practices and aligns with green initiatives.
- Superior Protection: UV-cure conformal coatings protect against various environmental factors, including moisture, dust, chemicals, and temperature fluctuations. They form a durable barrier that shields electronic components from corrosion, oxidation, and other damage forms, extending their lifespan and reliability in harsh operating conditions.
- Thin Film Application: UV cure coatings can be applied in fragile layers without sacrificing performance or coverage. Their low viscosity allows for precise application, ensuring uniform coating thickness and avoiding issues such as bridging or pooling. Maintaining tight tolerances on coating thickness is crucial for maintaining the functionality of delicate electronic components.
- Enhanced Quality Control: The instant curing nature of UV cure coatings facilitates real-time quality control during manufacturing. Manufacturers can inspect coated components immediately for defects or irregularities, allowing for timely adjustments or rework. This proactive approach helps minimize rejections, improve product quality, and reduce manufacturing costs.
- Minimal Volatile Organic Compounds (VOCs): UV cure conformal coatings typically contain fewer volatile organic compounds than solvent-based coatings. As a result, they contribute to a healthier work environment for operators and reduce emissions of harmful substances into the atmosphere, aligning with regulatory requirements and sustainability goals.
Overall, the key benefits of UV-cured conformal coatings include rapid cure time, energy efficiency, superior protection, thin film application, enhanced quality control, and minimal VOC emissions. These advantages make UV-cured coatings an attractive choice for electronics manufacturers seeking high-performance and environmentally friendly solutions for protecting their products.
Which industries commonly utilize UV-cure conformal coatings?
UV cure conformal coatings are versatile materials used across various industries to protect electronic components and assemblies. These coatings offer numerous advantages, such as rapid curing, excellent protection against moisture, chemicals, and mechanical stress, and enhanced electrical insulation properties. Some of the industries commonly utilizing UV cure conformal coatings include:
- Electronics Manufacturing: UV cure conformal coatings find extensive use in electronics manufacturing for protecting printed circuit boards (PCBs), semiconductor devices, LEDs, and other electronic components from environmental factors like moisture, dust, and corrosion. These coatings ensure the longevity and reliability of electronic devices, especially in harsh operating conditions.
- Automotive Industry: In the automotive sector, UV cure conformal coatings are applied to electronic control units (ECUs), sensors, connectors, and other critical electronic components to safeguard them against temperature fluctuations, vibration, and exposure to automotive fluids. These coatings help enhance the performance and durability of automotive electronics, ensuring consistent operation in challenging environments.
- Aerospace and Defense: Aerospace and defense applications demand high-performance coatings to protect sensitive electronic systems from extreme temperatures, humidity, and vibration during flight or military operations. UV cure conformal coatings provide lightweight and reliable protection for avionics, radar systems, communication equipment, and other electronics onboard aircraft, spacecraft, and military vehicles.
- Medical Devices: In the medical industry, UV cure conformal coatings protect electronic components in medical devices such as diagnostic equipment, patient monitoring systems, and surgical instruments. These coatings help prevent contamination, improve device reliability, and ensure compliance with stringent regulatory standards for medical device manufacturing.
- Industrial Automation: Industrial automation equipment often operates in demanding environments with dust, moisture, and chemical exposure. UV cure conformal coatings are applied to control panels, PLCs (programmable logic controllers), and other electronic components in industrial automation systems to enhance their reliability and lifespan, minimizing downtime and maintenance costs.
- Consumer Electronics: Consumer electronics manufacturers utilize UV cure conformal coatings to protect smartphones, tablets, wearables, and other electronic gadgets from everyday wear and tear, as well as environmental factors like moisture and dust. These coatings provide an invisible protective layer that preserves the functionality and appearance of electronic devices.
UV-cured conformal coatings play a crucial role in various industries, where protecting electronic components from environmental hazards is essential for ensuring reliability, longevity, and compliance with industry standards and regulations.
What are the main components of UV cure conformal coatings?
UV cure conformal coatings are specialized protective coatings used in electronics manufacturing to safeguard printed circuit boards (PCBs) and other sensitive electronic components from environmental factors such as moisture, dust, chemicals, and mechanical damage. These coatings are applied in liquid form and then cured rapidly using ultraviolet (UV) light. The main components of UV cure conformal coatings include:
- Oligomers: These are the primary building blocks of UV-cure conformal coatings. Oligomers are short-chain polymers with functional groups that facilitate cross-linking when exposed to UV light. They provide the coating’s backbone structure and contribute to its mechanical properties, such as flexibility, adhesion, and hardness.
- Monomers: Monomers are small molecules that undergo polymerization during the curing process. They help control the coating formulation’s viscosity and enable rapid curing under UV light. Monomers influence the coating’s final properties, such as hardness and chemical resistance.
- Photoinitiators: Photoinitiators are compounds that generate free radicals or reactive species upon exposure to UV light. These radicals initiate the polymerization reaction between oligomers and monomers, forming a solid coating. Photoinitiators are crucial in determining UV cure conformal coatings’ curing speed and efficiency.
- Additives: Various additives are incorporated into UV cure conformal coatings to enhance specific properties or address particular application requirements. These additives may include adhesion promoters, leveling agents, UV stabilizers, antioxidants, and flame retardants. They help improve coating performance, durability, and reliability in different operating environments.
- Solvents: Solvents are used to adjust the viscosity of the coating formulation for application purposes. However, in UV cure conformal coatings, the solvent content is typically minimal as these coatings are designed to cure rapidly without extensive solvent evaporation.
Overall, these components’ combination and careful formulation determine the performance, properties, and suitability of UV cure conformal coatings for protecting electronic assemblies and devices in diverse applications. Their ability to provide a thin, uniform, and durable protective layer makes them indispensable in modern electronics manufacturing processes.
How does UV cure conformal coating compare to traditional conformal coatings?
UV cure conformal coatings offer several advantages over traditional conformal coatings:
- Speed of Cure: UV cure conformal coatings cure rapidly when exposed to ultraviolet light, typically within seconds to minutes, depending on the formulation and thickness applied. In contrast, traditional coatings often require hours to cure completely. This rapid curing significantly reduces production time and increases throughput.
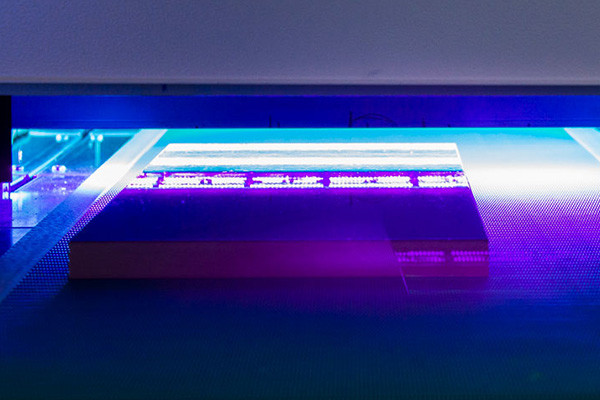
- Energy Efficiency: UV cure coatings require less energy for curing than traditional methods such as thermal or solvent evaporation. This energy efficiency leads to lower operating costs and reduced environmental impact.
- Lower Temperature Requirements: UV cure coatings cure at ambient or slightly elevated temperatures, eliminating the need for high-temperature curing ovens. This feature is particularly advantageous for heat-sensitive substrates or components, preventing thermal damage during the coating process.
- Consistency and Control: UV cure coatings offer precise control over the curing process, allowing manufacturers to achieve consistent coating thickness and coverage. Additionally, since curing occurs on-demand upon exposure to UV light, there is no risk of over-curing or under-curing, as seen with traditional methods.
- Reduced Volatile Organic Compounds (VOCs): UV cure coatings are typically solvent-free or contain less volatile organic compounds than solvent-based conventional coatings. Reducing VOC emissions contributes to a safer working environment and compliance with environmental regulations.
- Enhanced Performance: UV cure coatings often exhibit superior properties such as higher hardness, improved chemical resistance, and better adhesion than traditional coatings. These enhanced characteristics result in more durable and reliable protection for electronic assemblies in harsh environments.
Despite these advantages, UV cure conformal coatings may have limitations regarding substrate compatibility and upfront investment in UV curing equipment. Proper handling and safety precautions are also necessary when working with UV light sources. However, advancements in formulation technology and UV curing equipment continue to address these challenges, making UV-cure conformal coatings an increasingly popular choice for electronics manufacturers seeking efficient and high-performance coating solutions.
What types of substrates are suitable for UV-cure conformal coatings?
UV cure conformal coatings offer versatility in substrate compatibility, making them suitable for various materials commonly used in electronic assemblies. These substrates include:
- Printed Circuit Boards (PCBs): PCBs are the primary substrate for electronic assemblies. UV-cure conformal coatings can protect the components and traces on the board from environmental factors such as moisture, dust, and chemicals. Both rigid and flexible PCBs are compatible with UV cure coatings.
- Semiconductor Devices: Semiconductor devices, including microchips, integrated circuits, and sensors, often require protective coatings to insulate and shield them from external elements. UV cure coatings provide a thin, uniform layer of protection without compromising the performance of these devices.
- Glass: UV cure coatings adhere well to glass substrates, offering protection against scratches, abrasion, and chemical exposure. Glass substrates are commonly used in displays, touch panels, and optical components in electronic devices.
- Metal: Metal substrates, such as aluminum, steel, and copper, are prevalent in electronic assemblies for structural support, heat dissipation, and electrical conductivity. UV cure coatings can be applied to metal surfaces for corrosion resistance, insulation, and decorative finishes.
- Plastic: Various plastics, including polycarbonate, ABS, and polyamide, are used in electronic enclosures, connectors, and other components. UV cure coatings offer excellent adhesion to plastic substrates, enhancing their durability and resistance to environmental stressors.
- Ceramics: Ceramic substrates are valued for their thermal stability and electrical insulation properties. UV cure coatings can be applied to ceramic components to protect against moisture ingress, thermal cycling, and mechanical damage.
- Composite Materials: Composite materials, such as fiberglass-reinforced epoxy laminates, are used in applications requiring a high strength-to-weight ratio and dimensional stability. UV cure coatings can be applied to composite substrates to enhance their surface properties and prolong their service life.
UV-cured conformal coatings are compatible with a wide range of substrates commonly found in electronic assemblies, providing manufacturers with flexibility in design and protection options. However, proper surface preparation and compatibility testing are essential to ensure optimal adhesion and performance of the coating on specific substrates.
Can UV-cure conformal coatings be applied manually or through automated processes?
UV-cure conformal coatings can be applied through manual and automated processes, offering versatility and efficiency in various manufacturing environments.
Manual Application: In manual application, operators apply the UV-cure conformal coatings using various methods such as brushing, spraying, or dipping. This approach is suitable for smaller-scale production runs or products with complex geometries where automated systems might not be feasible. Operators have more control over the application process, allowing them to ensure thorough coverage and precise coating thickness. However, the manual application can be labor-intensive and time-consuming, potentially leading to inconsistencies in coating thickness and quality if not executed carefully.
Automated Processes: Automated processes involve using machinery and robotics to apply UV-cure conformal coatings. These systems offer higher throughput rates, consistency, and precision than manual methods. Automated spray or dip coating systems can be integrated into assembly lines, allowing for seamless integration with other manufacturing processes. Moreover, computerized processes reduce reliance on manual labor, increasing efficiency and reducing labor costs. Quality control measures can also be incorporated into automated systems to ensure uniform coating thickness and adherence to specifications.
Benefits of Automated Application:
- Consistency: Automated processes ensure consistent coating thickness and coverage, minimizing variations in product quality.
- Efficiency: Automated systems can operate continuously, leading to higher throughput rates and faster production cycles.
- Precision: Robotics and advanced machinery enable precise application of UV-cure coatings, reducing material waste and improving overall product quality.
- Cost-effectiveness: While initial setup costs may be higher for automated systems, they often result in long-term cost savings through increased productivity and reduced labor expenses.
UV-cure conformal coatings can be applied manually or through automated processes, each offering unique advantages depending on the scale and requirements of the manufacturing operation. Manual application provides flexibility and control, while computerized processes deliver efficiency, consistency, and precision, making them suitable for high-volume production environments.
What factors should be considered when selecting a UV cure conformal coating?
Selecting the right UV cure conformal coating involves considering several critical factors to ensure optimal performance and compatibility with the intended application:
- Substrate Compatibility: The coating should adhere well to the substrate material, whether PCBs, electronic components, or other surfaces. Compatibility testing ensures that the coating does not react negatively with the substrate, leading to delamination or other issues.
- Curing Properties: UV cure coatings cure rapidly when exposed to ultraviolet light, but the curing time can vary based on factors like coating thickness, UV intensity, and wavelength. Understanding the curing requirements is essential for efficient production processes.
- Chemical Resistance: The coating must resist degradation from various chemicals it might encounter in its operational environment. Consider the types of chemicals the coated surface will be exposed to and choose a coating with appropriate chemical resistance properties.
- Environmental Durability: Evaluate the coating’s resistance to environmental factors such as temperature extremes, humidity, moisture, and UV radiation. The coating should provide long-term protection against these elements to ensure the reliability and longevity of the coated components.
- Electrical Properties: For electronic applications, the coating should maintain desired electrical properties, such as insulation resistance and dielectric strength, to prevent electrical failures or short circuits.
- Mechanical Protection: The coating should offer mechanical protection against physical damage, vibration, abrasion, and impact. It should maintain its integrity even under harsh conditions to safeguard the underlying components.
- Application Method: Consider the practical aspects of applying the coating, such as spraying, dipping, or selective coating methods. Choose a coating compatible with the preferred application method and easily integrated into existing manufacturing processes.
- Regulatory Compliance: Ensure that the chosen coating complies with relevant industry standards and regulations, such as RoHS (Restriction of Hazardous Substances) and REACH (Registration, Evaluation, Authorization, and Restriction of Chemicals), mainly if the coated products will be used in sensitive applications or markets.
- Supplier Support and Reliability: Work with reputable suppliers who offer technical support, product consistency, and reliability. Establishing a good relationship with the supplier can facilitate troubleshooting and ensure consistent product quality over time.
By carefully considering these factors, you can select a UV-cure conformal coating that meets your application’s specific requirements while ensuring reliability, durability, and performance.
Are there any safety precautions when working with UV-cure conformal coatings?
When working with UV cure conformal coatings, there are several necessary safety precautions to consider to protect both yourself and the environment:
- Personal Protective Equipment (PPE):Always wear appropriate PPE, including safety glasses or goggles to protect your eyes from UV exposure, gloves to prevent skin contact with the coating, and a lab coat or protective clothing to shield your skin from spills or splashes.
- Ventilation:Ensure adequate ventilation in the work area to prevent the buildup of fumes and vapors from the coating. Use a fume hood or work in a well-ventilated room to minimize inhalation risks.
- UV Exposure:UV cure coatings rely on ultraviolet light to cure. Avoid direct exposure of your skin and eyes to UV light emitted during curing. Shield UV lamps or wear protective clothing that blocks UV rays.
- Handling and Storage:Handle UV cure coatings carefully to avoid spills or leaks. Store them in tightly sealed containers away from direct sunlight and heat sources to prevent premature curing. Follow manufacturer instructions for proper handling and storage.
- Curing Environment:Ensure the curing environment is clean and free from contaminants that could affect the quality of the coating. Keep the work area organized and clutter-free to minimize accidents.
- Emergency Preparedness:Have safety measures in place in case of accidents or spills, including access to a spill kit, eyewash station, and emergency shower. Know the proper procedures for handling spills and exposure incidents.
- Training:Provide adequate training to personnel handling UV cure coatings, including instruction on proper handling, PPE usage, emergency procedures, and the potential hazards associated with the materials.
- Material Compatibility:Be aware of the compatibility of UV cure coatings with substrates and other materials they may come into contact with during application. Test compatibility beforehand if unsure.
- Disposal:Dispose of waste materials, such as used containers or contaminated materials, according to local regulations and guidelines for hazardous waste disposal.
Adhering to these safety precautions can minimize the risks associated with working with UV-cure conformal coatings and ensure a safe working environment for yourself and others.
How does the curing time of UV cure conformal coatings compare to other methods?
UV-cured conformal coatings offer significant advantages in terms of curing time compared to other methods, such as thermal cure or moisture cure coatings. The curing time of UV-cured conformal coatings is typically much faster, often measured in seconds to minutes, depending on the thickness of the coating and the intensity of the UV light source.
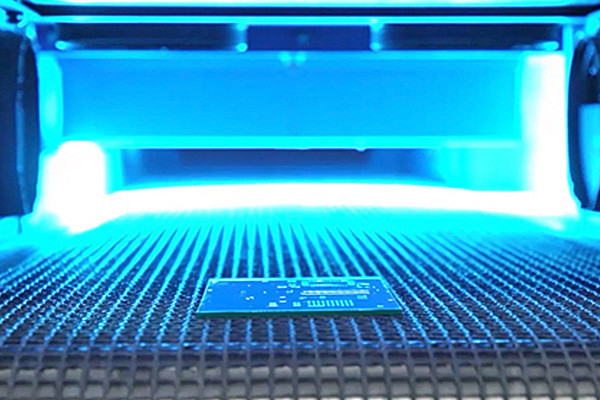
One primary reason for the rapid curing time of UV cure coatings is the use of ultraviolet light to initiate the curing process. When exposed to UV light of a specific wavelength, photoinitiators within the coating material undergo a chemical reaction, rapidly forming crosslinks between the polymer chains in the coating. This process, known as photopolymerization, results in the rapid solidification and curing of the layer.
In contrast, thermal cure coatings rely on elevated temperatures to facilitate curing. These coatings typically require longer curing times, ranging from several minutes to several hours, depending on the temperature and the specific formulation of the coating. The need for prolonged exposure to high temperatures can increase processing times and energy costs.
Moisture-cure coatings, on the other hand, rely on atmospheric moisture to initiate the curing process. While they offer the advantage of not requiring specialized equipment such as UV lamps or ovens, the curing time for moisture-cure coatings can vary significantly depending on environmental conditions such as temperature and humidity. Curing times may sometimes extend to several hours or even days, particularly in humid environments.
Overall, the rapid curing time of UV-cured conformal coatings makes them highly desirable for applications where fast throughput and efficiency are critical, such as electronics manufacturing. Additionally, UV-cured coatings offer the advantage of precise control over the curing process, allowing for rapid curing on-demand without the need for extended processing times or post-cure steps.
What role does viscosity play in UV-cure conformal coatings?
Viscosity plays a crucial role in UV cure conformal coatings, affecting their application, performance, and effectiveness in protecting electronic components. UV cure conformal coatings are commonly used to protect sensitive electronic assemblies from environmental factors such as moisture, dust, chemicals, and temperature variations. Viscosity, a measure of a fluid’s resistance to flow, influences several aspects of these coatings:
- Application Process: The viscosity of a UV cure conformal coating determines its flow characteristics during application. A coating with low viscosity flows more easily and can be applied evenly over intricate electronic components, ensuring uniform coverage and protection. Conversely, a coating with high viscosity may be challenging to apply, leading to uneven coating thickness, air entrapment, and potential defects.
- Coating Thickness: Viscosity influences the thickness of the applied coating layer. Higher viscosity coatings form thicker layers, which may be desirable for applications requiring more excellent protection or insulation. However, excessive thickness can lead to problems such as uneven curing, shrinkage, or cracking. Controlling viscosity allows manufacturers to achieve optimal coating thickness for specific application requirements.
- Cure Speed: The viscosity of UV cure conformal coatings affects the curing process. Lower viscosity coatings typically cure more rapidly under UV light exposure due to easier penetration into the substrate and better interaction with photoinitiators. Faster curing times can increase production efficiency and throughput. However, excessively low-viscosity coatings may cure too quickly, leading to incomplete curing or inadequate adhesion.
- Performance Properties: Viscosity impacts various performance properties of UV cure conformal coatings, including adhesion, flexibility, and resistance to environmental stressors. Proper viscosity control ensures that the coating adheres well to the substrate, forms a durable protective barrier, and maintains desired mechanical properties over time. Deviations in viscosity can compromise coating integrity and performance, resulting in reduced reliability or premature failure of electronic devices.
Viscosity is a critical parameter in UV-cured conformal coatings, influencing their application characteristics, curing behavior, and protective performance. Manufacturers must carefully tailor viscosity levels to meet specific application requirements and ensure the adequate protection of electronic assemblies against environmental hazards.
Can UV-cure conformal coatings be reworked or removed after application?
UV-cure conformal coatings offer numerous advantages in electronics manufacturing due to their fast curing times, high-performance properties, and environmental friendliness. However, reworking or removing these coatings after application can be challenging compared to traditional solvent-based coatings.
UV-cure conformal coatings are typically cross-linked upon exposure to ultraviolet (UV) light. This process initiates a chemical reaction within the coating, forming a hardened, protective layer on the substrate surface. Once cured, the coating forms strong bonds with the substrate, making removing it difficult without specialized equipment or techniques.
Reworking or removing UV-cure conformal coatings generally requires a combination of mechanical and chemical methods. One approach involves mechanically scraping or grinding the coating using precision tools to minimize damage to the underlying components. However, this method can be labor-intensive and risk damaging sensitive electronic components or substrates.
Chemical methods can also soften or dissolve the cured coating, facilitating its removal. Some solvents or chemical strippers designed specifically for UV-cure coatings may be effective in breaking down the cross-linked polymer structure, allowing the layer to be peeled or washed away. However, it’s essential to choose chemicals carefully to avoid damaging the substrate or compromising the integrity of nearby components.
Another technique for reworking UV-cure conformal coatings involves localized heating to soften the coating, making it easier to remove without damaging surrounding components. This method requires precise control of temperature to avoid overheating sensitive electronic parts.
Despite these methods, it’s important to note that reworking or removing UV-cure conformal coatings can be challenging and may not always result in satisfactory outcomes. Additionally, repeated rework attempts can compromise the performance or reliability of the electronic device.
While UV-cure conformal coatings offer numerous benefits in electronics manufacturing, reworking or removing these coatings after application requires careful consideration and specialized techniques. Manufacturers should weigh the advantages of UV-cure coatings against the challenges of rework ability to determine the most suitable solution for their specific application requirements.
What are the typical application methods for UV-cure conformal coatings?
UV cure conformal coatings are commonly used in electronics manufacturing to protect printed circuit boards (PCBs) and electronic components from environmental factors such as moisture, dust, and chemicals. These coatings provide a thin, protective layer that conforms to the contours of the components and PCB, ensuring complete coverage and protection. Several application methods are employed for applying UV cure conformal coatings:
- Spraying: This method involves using a spray gun or automated spraying equipment to apply the UV cure conformal coating evenly onto the surface of the PCB or electronic component. Spraying allows for fast and efficient coverage, making it suitable for high-volume production environments.
- Dipping: In the dipping method, the PCB or electronic component is immersed in a UV cure conformal coating bath. The coating adheres to the surface upon withdrawal, and excess coating is drained. Dipping ensures uniform coverage and is suitable for complex-shaped components.
- Brushing: Manual brushing involves applying the UV cure conformal coating using brushes or applicators. This method is ideal for small-scale production or touch-up applications requiring precision.
- Selective Coating: Selective coating involves applying the UV cure conformal coating to specific PCB or electronic component areas. This can be achieved using automated dispensing equipment or by masking off areas that do not require coating. Selective coating reduces waste and ensures that only critical areas are protected.
- Roller Coating: Roller coating utilizes a roller to apply the UV cure conformal coating onto the surface of the PCB or electronic component. This method is suitable for flat or slightly curved surfaces and provides uniform coverage.
- Film Lamination: In some cases, UV cure conformal coatings are available as pre-cut films or sheets. These films are applied to the surface of the PCB or electronic component using heat and pressure to activate the adhesive and bond the film to the substrate.
Each application method has advantages and is chosen based on factors such as production volume, complexity of components, and desired level of precision. Proper application ensures the effectiveness of UV-cured conformal coatings in protecting electronic devices from environmental hazards.
Are there specialized equipment requirements for applying UV cure conformal coatings?
UV-cure conformal coatings protect electronic components from environmental factors such as moisture, dust, chemicals, and temperature extremes. While applying UV cure conformal coatings shares similarities with traditional conformal coatings, there are specific equipment requirements due to the UV curing mechanism. Here are the specialized equipment requirements for applying UV cure conformal coatings:
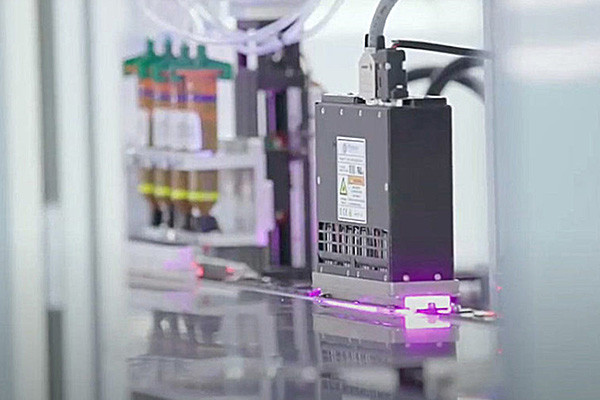
- UV Curing System: The primary requirement is a UV curing system, which emits ultraviolet light to initiate the curing process. This system typically consists of a UV lamp or array of lamps with specific wavelengths tailored to activate the photoinitiators present in the conformal coating material. The UV curing system must provide sufficient intensity and coverage to ensure uniform curing across the coated surface.
- Conveyor System or Station: A conveyor system or stationary platform may be used to streamline the coating process and ensure consistent exposure to UV light. Components coated with UV cure conformal coatings are passed through the UV curing system either manually or automatically. The conveyor speed or exposure time must be optimized to achieve the desired curing results without under or overexposure.
- Applicator Equipment: Similar to traditional conformal coatings, applicator equipment such as spray guns, needles, or robotic dispensers may apply UV-cure conformal coatings onto electronic assemblies. It’s essential to choose applicators compatible with the viscosity and flow properties of the coating material to achieve uniform coverage.
- UV-Absorbing Shielding: Since UV light can harm human skin and eyes, appropriate shielding measures such as UV-blocking curtains or enclosures are necessary to protect operators and bystanders during the coating and curing process. These shielding materials should effectively block UV radiation while allowing visibility and monitoring.
- Monitoring and Control Instruments: Monitoring and control instruments such as radiometers and photometers may be utilized to ensure quality control and optimize the curing process. These instruments measure UV intensity and exposure time, allowing operators to adjust parameters for consistent and thorough curing.
Specialized equipment for applying UV cure conformal coatings includes UV curing systems, conveyors or stationary platforms, applicator equipment, UV-absorbing shielding, and monitoring/control instruments. Adhering to these equipment requirements ensures efficient and practical application of UV cure conformal coatings, enhancing electronic components’ protection.
What are the environmental considerations associated with UV-cure conformal coatings?
UV cure conformal coatings offer various advantages in rapid curing, reduced energy consumption, and minimized environmental impact compared to traditional solvent-based coatings. However, several ecological considerations still need attention:
- Volatile Organic Compounds (VOCs):While UV cure coatings generally have lower VOC content than solvent-based coatings, some formulations may still contain VOCs. VOCs contribute to air pollution and can have adverse health effects. It’s essential to choose low-VOC or VOC-free formulations to minimize environmental impact.
- Energy Consumption:UV cure coatings require UV light for curing, which can consume significant energy. While UV curing is more energy-efficient than thermal curing processes, it still contributes to overall energy consumption. Implementing energy-efficient UV curing systems and optimizing curing processes can help reduce energy usage and environmental impact.
- Hazardous Materials:Some components of UV cure coatings may be dangerous to the environment if not handled properly. This includes chemicals used in the formulation and packaging materials. Proper handling, storage, and disposal procedures are necessary to prevent environmental contamination.
- Waste Generation:Unused or expired UV cure coating materials and packaging waste contribute to solid waste generation. It’s essential to minimize waste through efficient inventory management, proper storage, and recycling or disposal of waste materials according to regulations.
- Emissions:During UV curing, ozone, and other volatile compounds may be emitted depending on the specific formulation and curing conditions. These emissions can contribute to air pollution and may require mitigation measures such as exhaust ventilation or emission control systems.
- Lifecycle Considerations:Assessing the total lifecycle environmental impact of UV cure coatings is essential, including raw material extraction, manufacturing processes, transportation, use, and end-of-life disposal or recycling. Understanding and optimizing each stage can help minimize the overall environmental footprint.
While UV cure conformal coatings offer several environmental benefits compared to solvent-based alternatives, carefully considering factors such as VOCs, energy consumption, hazardous materials, waste generation, emissions, and lifecycle impacts is necessary to ensure their environmental sustainability. The ecological footprint of UV cure coatings can be minimized by choosing low-impact formulations, optimizing processes, and implementing proper handling and disposal practices.
How do UV-cure conformal coatings perform in harsh operating environments?
UV-cured conformal coatings offer excellent performance in harsh operating environments due to their unique properties and curing mechanisms. These coatings are designed to protect electronic components and assemblies in challenging conditions such as extreme temperatures, moisture, chemicals, and mechanical stress.
One key advantage of UV-cured conformal coatings is their rapid curing process. When exposed to ultraviolet (UV) light, these coatings undergo a chemical reaction that quickly transforms them from liquid to solid. This fast curing time allows for efficient production processes and ensures that the coating forms a durable barrier on the surface of the electronic components.
UV-cure conformal coatings in harsh operating environments demonstrate exceptional resistance to temperature extremes. They can withstand high and low temperatures without losing their protective properties or becoming brittle, which is crucial for electronics exposed to fluctuating environmental conditions.
Furthermore, UV-cure conformal coatings exhibit excellent resistance to moisture and chemicals. They create a barrier that prevents water and corrosive substances from reaching the sensitive electronic components, thus shielding them from damage and ensuring long-term reliability. This resistance to moisture and chemicals is significant in applications where electronics are exposed to outdoor environments, industrial processes, or corrosive substances.
UV cure conformal coatings also provide good adhesion to various substrates, including metals, plastics, and ceramics. This strong adhesion ensures that the coating remains securely bonded to the surface of the electronic assembly, even when subjected to mechanical stress or vibration.
Overall, UV-cure conformal coatings offer reliable protection for electronic components in harsh operating environments. Their fast curing time, resistance to temperature extremes, moisture, chemicals, and strong adhesion make them an ideal choice for applications where durability and performance are paramount.
Are there any limitations or drawbacks to using UV-cure conformal coatings?
UV cure conformal coatings offer numerous advantages, such as rapid curing times, precise application, and excellent protection against moisture, dust, and chemicals. However, they also come with several limitations and drawbacks that must be considered:
- Limited depth of cure: UV light can only penetrate a certain depth into the coating material. This limits the thickness of the coating that can be effectively cured. Thick coatings may need to be completed or completed, leading to potential performance issues.
- UV light accessibility: Components with complex geometries or shadowed areas may not receive sufficient UV exposure for complete curing. This can result in areas of incomplete coverage or inadequate protection, compromising the reliability of the coated assembly.
- Sensitivity to ambient conditions: UV cure coatings are sensitive to ambient conditions such as temperature and humidity. High humidity levels can interfere with the curing process or affect coating adhesion, leading to inconsistent results or coating failures.
- Potential for photoinitiator migration: UV cure coatings contain photoinitiators, which may migrate over time, particularly in applications exposed to high temperatures. Photoinitiator migration can lead to discoloration, reduced adhesion, or changes in coating properties, affecting long-term reliability.
- Limited chemical resistance: While UV cure coatings offer good resistance to many chemicals, they may not be suitable for extreme chemical environments. Harsh chemicals can degrade the coating over time, compromising the protection of the underlying components.
- Cost considerations: UV cure coatings may have higher initial material costs than other conformal coatings. Additionally, the equipment required for UV curing, such as UV lamps and curing chambers, can represent a significant investment.
- UV light safety concerns: UV light used for curing can pose health and safety risks to operators if proper precautions are not taken. Exposure to UV radiation can cause skin and eye damage, requiring the use of protective equipment and adherence to safety guidelines.
While UV-cured conformal coatings offer many benefits, including fast curing times and excellent protection, they also have limitations and drawbacks that need to be carefully considered in the selection and application process to ensure optimal performance and reliability in the intended application.
What advancements have been made in UV cure conformal coating technology recently?
In recent years, UV cure conformal coating technology has seen significant advancements, primarily driven by the demand for improved performance, efficiency, and environmental sustainability. These advancements have mainly focused on enhancing coating properties, application processes, and effectiveness.
- Improved Formulations: Manufacturers have developed new formulations with enhanced properties such as higher chemical resistance, increased flexibility, and better adhesion to various substrates. These advancements ensure that conformal coatings offer superior protection to electronic components against moisture, chemicals, and mechanical stress, thus improving the reliability and longevity of electronic devices.
- Faster Cure Times: One notable advancement is the reduction in cure times. New UV cure conformal coatings cure much faster than traditional coatings, enabling higher throughput in manufacturing processes and reducing energy consumption. Faster cure times also lead to shorter production cycles, ultimately increasing productivity.
- Thinner Coating Thickness: Advances in formulation technology have allowed the develop of thinner coatings without compromising protection. Thinner coatings help minimize the overall weight and size of electronic devices, particularly crucial in aerospace and automotive industries where space and weight considerations are significant.
- UV LED Technology: The adoption of UV LED technology for curing has gained momentum. UV LEDs offer several advantages over traditional UV lamps, including longer lifespan, energy efficiency, and precise control over the curing process. These benefits contribute to reduced operating costs and improved process control.
- Environmentally Friendly Solutions: There’s a growing emphasis on developing eco-friendly conformal coatings that comply with regulations such as REACH and RoHS. Manufacturers are actively seeking alternative raw materials and manufacturing processes to minimize the environmental impact of UV cure conformal coatings while maintaining high-performance standards.
- Enhanced Application Techniques: Advanced application techniques, such as selective coating and robotic dispensing systems, enable more precise and uniform application of conformal coatings. These techniques ensure complete coverage while minimizing material waste and optimizing the coating process.
Overall, recent advancements in UV cure conformal coating technology have resulted in coatings that offer improved performance, efficiency, and environmental sustainability. These developments continue to drive innovation in the electronics industry, providing manufacturers with solutions to meet the evolving demands of modern electronic devices.
What are some best practices for applying and maintaining UV-cure conformal coatings?
UV cure conformal coatings are widely used in electronics manufacturing to protect printed circuit boards (PCBs) from environmental factors such as moisture, dust, and chemicals. Here are some best practices for applying and maintaining UV cure conformal coatings:
- Surface Preparation: Ensure the PCB surface is thoroughly cleaned and free from contaminants like dust, oils, or residues. Proper surface preparation is crucial for achieving good adhesion and uniform coating coverage.
- Masking and Taping: Use masking materials to protect areas that should not be coated, such as connectors or sensitive components. Proper masking prevents the coating from interfering with these components’ functionality.
- Uniform Application: Apply the UV cure conformal coating evenly across the PCB surface using spray, dip, or brush techniques. Ensure consistent coating thickness to provide uniform protection to all board areas.
- UV Exposure: After applying the coating, expose the PCB to UV light according to the manufacturer’s specifications. Ensure adequate UV exposure time and intensity to fully cure the coating and achieve the desired properties such as hardness and adhesion.
- Post-Cure Inspection: After UV curing, inspect the coated PCB for defects such as bubbles, uneven coverage, or incomplete curing. Touch up any imperfections to ensure the coating provides adequate protection.
- Testing: Conduct electrical and functional testing on the coated PCB to ensure that the coating does not interfere with the performance of the electronic components. Testing may include insulation resistance, dielectric withstand voltage, and functionality checks.
- Maintenance: Regularly inspect coated PCBs for signs of damage or degradation, such as cracks, delamination, or discoloration. Promptly repair or recoat any damaged areas to maintain the integrity of the protective barrier.
- Environment Considerations: Consider the operating environment of the PCBs when selecting a UV cure conformal coating. Choose coatings with appropriate resistance to temperature, humidity, chemicals, and other environmental factors prevalent in the application area.
- Documentation: Maintain detailed records of the coating process, including coating type, application parameters, curing conditions, and inspection results. Documentation helps ensure consistency and traceability in the manufacturing process.
By following these best practices, manufacturers can effectively apply and maintain UV cure conformal coatings, ensuring electronic assemblies’ long-term reliability and performance in diverse applications.
Conclusion:
UV cure conformal coatings represent a cutting-edge solution for protecting electronic assemblies in diverse industries. Their rapid curing, excellent adhesion properties, and resistance to environmental factors make them a preferred choice for many applications. As technology continues to evolve, so will the capabilities and versatility of UV-cure conformal coatings, ensuring electronic components’ continued protection and reliability in demanding environments.
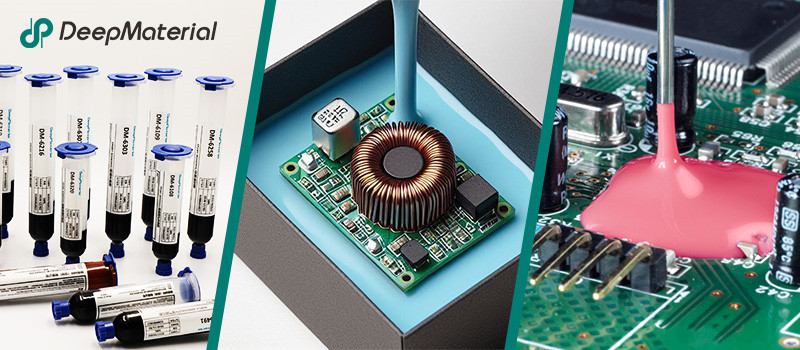
About DeepMaterial
DeepMaterial is a trusted supplier of encapsulant materials that are used in electronics manufacturing worldwide. From chip on board encapsulants such as glob top material to conformal coatings, underfills, low pressure molding, and potting solutions, DeepMaterial offers a full range of circuit board protection materials that effectively protect circuit boards while help reduce costs. More…Deepmaterial is a the manufacturer of epoxy adhesives including hardeners, metalbond, and metal filled resins. Structural, toughened medium viscosity, and non-sag adhesives are also offered. Some adhesives are resistant to thermal shock, chemical, vibration dampening, and impact. Suitable for metals, plastics, wood, and ceramics. Serves electronics, aerospace, automotive, tooling, marine, and construction industries. REACH and RoHS compliant. FDA approved. UL listed. Meets military specifications. We are the one of best adhesive manufacturers in China.
Blogs & News
Potting compounds are at the frontline of electronics assembly, delivering effective protection in challenging environmental conditions while improving mechanical strength and offering high electric insulation. Used within a variety of industries, electrical potting compounds are found within a broad range of consumer electronics, as well as used in applications across the automotive, aerospace, and other industries where electronic assemblies are prevalent.
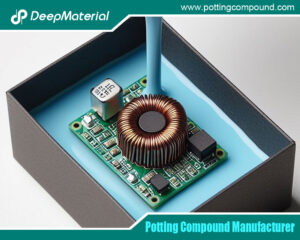
Potting Compound vs. Epoxy: A Comprehensive Comparison
Potting Compound vs. Epoxy: A Comprehensive Comparison In the world of electronics, manufacturing, and material encapsulation, two terms frequently come up: potting compounds and epoxy.
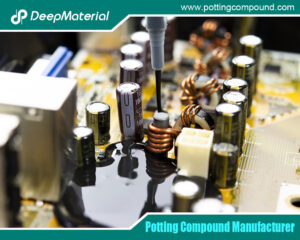
Potting Compound for PCB
Potting Compound for PCB A potting compound is a liquid or semi-liquid material that is poured or injected over a PCB or electronic assembly, then
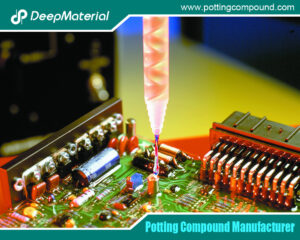
In – depth Analysis of the Curing Characteristics of Electronic Potting Compounds
In – depth Analysis of the Curing Characteristics of Electronic Potting Compounds Electronic potting compounds play a vital role in the electronics industry. They can
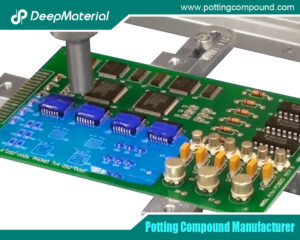
A Comprehensive Analysis of the Environmental Performance of Encapsulating Materials: From Regulations to Practices
A Comprehensive Analysis of the Environmental Performance of Encapsulating Materials: From Regulations to Practices In modern industrial manufacturing, encapsulating materials are widely used in numerous

A Comprehensive Analysis of PCB Encapsulation Quality Inspection: Innovative Application of Non-Destructive Testing Technologies
A Comprehensive Analysis of PCB Encapsulation Quality Inspection: Innovative Application of Non-Destructive Testing Technologies In the field of electronic manufacturing, the encapsulation process of printed
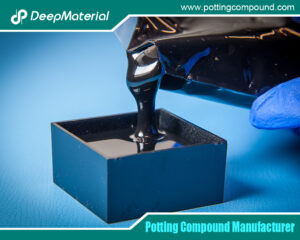
Analysis of the Improvement of the Seismic and Impact Resistance Performance of PCB by Encapsulation
Analysis of the Improvement of the Seismic and Impact Resistance Performance of PCB by Encapsulation During the operation of electronic devices, the PCB (Printed Circuit