Conformal Coating Thickness Standards: Ensuring Quality and Reliability
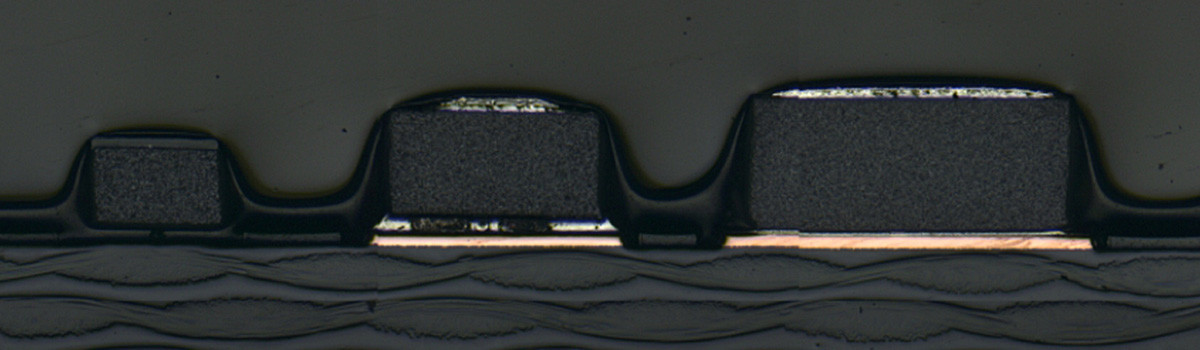
Conformal coating thickness standards are crucial for maintaining the reliability and performance of electronic components and assemblies. These standards provide guidelines for applying conformal coatings, ensuring adequate protection against environmental factors such as moisture, chemicals, and temperature extremes. By adhering to these standards, manufacturers can enhance the durability and longevity of their products, ultimately improving customer satisfaction and reducing the risk of costly failures. This category delves into various aspects of conformal coating thickness standards, providing insights, guidelines, and best practices for achieving optimal coating thickness.
Table of Contents
ToggleVital details you need to be acquainted with:
What are conformal coating thickness standards?
Conformal coating thickness standards are crucial in ensuring the effectiveness and reliability of conformal coatings used in various industries, particularly electronics manufacturing. Conformal coatings are thin protective films applied to electronic components to safeguard them against environmental factors such as moisture, dust, chemicals, and temperature extremes.
The thickness of conformal coatings is a critical parameter as it directly influences their protective capabilities and performance. Several standards and guidelines exist to define acceptable coating thickness levels, ensuring consistency and reliability across different applications.
One widely recognized standard is IPC-A-610, developed by the Association of Connecting Electronics Industries (IPC). IPC-A-610 outlines criteria for the acceptability of electronic assemblies, including guidelines for conformal coating thickness. It specifies acceptable thickness ranges for different types of conformal coatings based on their application methods, such as brushing, spraying, or dipping.
Another necessary standard is MIL-I-46058C, a military specification that defines the requirements for conformal coatings used in military electronic equipment. This specification includes detailed instructions for coating thickness measurement methods, and acceptable thickness ranges for various coating types.
The International Electrotechnical Commission (IEC) also publishes standards related to conformal coating thickness, such as IEC 60664, which provides guidelines for insulation coordination in electrical equipment. While not explicitly focused on coating thickness, these standards often include relevant requirements for conformal coatings used in electrical and electronic systems.
In practice, conformal coating thickness may vary depending on factors such as the type of coating material, the intended level of protection, and the application’s specific requirements. However, adherence to established standards helps ensure that coatings provide adequate protection without compromising the functionality or reliability of electronic assemblies.
Manufacturers typically employ measurement techniques, including manual or automated methods such as thickness gauges or optical inspection systems, to verify coating thickness and ensure compliance with applicable standards. Regular inspection and quality control processes are essential to maintaining consistency and reliability in conformal coating applications across industries.
Why are conformal coating thickness standards necessary in electronics manufacturing?
Conformal coating thickness standards are crucial in electronics manufacturing for several reasons.
- Protection from Environmental Factors: Conformal coatings are applied to electronic components to protect them from environmental factors such as moisture, dust, chemicals, and temperature variations. The thickness of the coating directly impacts its effectiveness in providing this protection. Standards ensure the coating is thick enough to provide adequate insulation and barrier properties against these environmental hazards.
- Prevention of Corrosion and Contamination: A uniform and appropriate conformal coating thickness helps prevent corrosion of sensitive electronic components. Corrosion can lead to malfunctions or failures in electronic devices. Additionally, conformal coatings avoid contamination from foreign particles, which can interfere with the proper functioning of the electronics.
- Maintaining Electrical Properties: While conformal coatings provide protection, they must not compromise the electrical properties of the components they cover. Excessive thickness can lead to issues such as capacitance changes or signal interference. Standards ensure that the coating is applied within the optimal range to maintain the electrical integrity of the components.
- Consistency and Reliability: Standardized thickness requirements promote consistency in manufacturing processes. Consistent coating thickness ensures uniform protection across all electronic components, reducing the likelihood of defects or failures. It also enhances the reliability of the final product, as deviations from standard thicknesses can lead to unpredictable performance or premature failure.
- Compliance and Quality Assurance: Adhering to established thickness standards is often required to comply with industry regulations and quality management systems such as ISO standards. Compliance with these standards assures customers and regulatory bodies that the electronic products meet specified quality criteria and are reliable in their intended applications.
Conformal coating thickness standards are essential in electronics manufacturing to ensure the effectiveness of protection against environmental factors, prevent corrosion and contamination, maintain electrical properties, promote consistency and reliability, and achieve compliance with industry regulations. Adhering to these standards contributes to electronic devices’ overall quality and longevity.
Who sets conformal coating thickness standards?
Industry organizations, governmental bodies, and international standards establish conformal coating thickness standards. These standards ensure consistency, reliability, and quality when applying conformal coatings, which protect electronic components from environmental factors such as moisture, dust, chemicals, and temperature extremes.
One prominent organization involved in setting standards for conformal coating thickness is the IPC (Association Connecting Electronics Industries). IPC develops and publishes standards widely adopted by the electronics manufacturing industry globally. IPC standards such as IPC-A-610 and IPC-CC-830 provide guidelines for applying and inspecting conformal coatings, including specifications for coating thickness.
Governmental bodies, such as the International Electrotechnical Commission (IEC) and the American National Standards Institute (ANSI), also set standards related to conformal coating thickness. These organizations often collaborate with industry stakeholders to develop standards that ensure safety, reliability, and compatibility with regulatory requirements.
Additionally, industry consortia and trade associations focused on electronics manufacturing may contribute to the establishment of conformal coating thickness standards. These groups bring together manufacturers, suppliers, and other stakeholders to develop best practices and guidelines for various aspects of electronic production, including conformal coating application.
Furthermore, material suppliers and equipment manufacturers in the conformal coating industry may have specifications and coating thickness recommendations based on their products and technologies. These specifications often align with industry standards but may also incorporate proprietary methodologies or considerations specific to their products.
Conformal coating thickness standards are established through a collaborative effort involving industry organizations, governmental bodies, standards-setting bodies, and industry stakeholders. These standards ensure uniformity, quality, and reliability when applying conformal coatings across the electronics manufacturing supply chain. Compliance with these standards helps manufacturers achieve consistent performance and reliability in their electronic products.
How do conformal coating thickness standards vary across industries?
Conformal coating thickness standards vary significantly across industries due to differences in application requirements, environmental conditions, and performance expectations. Conformal coatings are thin protective layers applied to electronic assemblies to protect them from environmental factors such as moisture, chemicals, dust, and temperature extremes. The thickness of these coatings is crucial as it directly impacts the effectiveness of protection and can influence factors like electrical insulation and thermal management. Here’s a brief overview of how conformal coating thickness standards vary across industries:
- Electronics Industry: In electronics, conformal coatings are commonly used to protect printed circuit boards (PCBs) and other electronic components. Thickness standards here are often dictated by international standards such as IPC-A-610 for PCB assembly, which provides guidelines for acceptable coating thickness ranges based on the coating material used.
- Automotive Industry: Automotive electronics require robust protection against harsh operating environments, including exposure to moisture, heat, and chemicals. Conformal coating thickness standards in the automotive industry are typically more stringent compared to other sectors due to safety and reliability concerns. Automotive manufacturers often have their specifications regarding coating thickness, which may exceed general industry standards.
- Aerospace and Defense: Aerospace and defense applications demand extremely high reliability and longevity, as electronic systems are subjected to extreme temperatures, vibration, and pressure variations. Conformal coating thickness standards in these sectors are often tailored to meet stringent military and aerospace standards such as MIL-I-46058C and IPC-CC-830. These standards specify precise thickness requirements to ensure optimal protection without compromising performance.
- Medical Device Industry: Medical devices require conformal coatings to protect sensitive electronic components from bodily fluids, sterilization processes, and other environmental factors. Conformal coating thickness standards in the medical device industry are governed by regulatory bodies such as the Food and Drug Administration (FDA) in the United States and international standards like ISO 13485. These standards emphasize biocompatibility, cleanliness, and durability while specifying acceptable coating thickness ranges.
Conformal coating thickness standards vary across industries based on the specific application requirements, environmental conditions, and regulatory considerations. While some sectors prioritize stringent thickness standards for enhanced protection and reliability, others may focus on compatibility with manufacturing processes and cost-effectiveness. Adherence to industry-specific standards is essential to ensure electronic assemblies’ optimal performance and reliability in diverse applications.
What are the standard methods for measuring conformal coating thickness?
Conformal coating thickness is crucial in ensuring optimal performance and protection of electronic components from environmental factors such as moisture, dust, and chemicals. Several methods are commonly used to measure conformal coating thickness:
- Cross-Sectional Analysis: This method involves cutting a sample of the coated substrate and examining it under a microscope. The thickness is determined by measuring the coating’s depth at various points across the cross-section. While accurate, this method is destructive and time-consuming.
- Non-contact Optical Measurement: Optical techniques like optical profilometry and laser scanning offer non-destructive measurement options. Optical profilometry employs lasers and cameras to scan the coated surface, generating a 3D profile from which thickness can be derived. Laser scanning operates similarly but with higher precision, using laser beams to measure surface contours.
- Eddy Current Testing: Eddy current probes induce electromagnetic fields in conductive materials, generating eddy currents. Variations in coating thickness alter the eddy currents’ behavior, allowing measurement of coating thickness. This method is non-destructive and suitable for metallic coatings.
- Ultrasonic Testing: Ultrasonic methods utilize high-frequency sound waves transmitted through the coating. The time taken for the waves to reflect provides information about the coating thickness. This versatile technique applies to various coating materials and offers high accuracy.
- Micrometer Measurement: Micrometers are precise instruments used to measure coating thickness directly at specific points on the substrate. While straightforward, this method may require surface preparation and is less suitable for irregular surfaces.
- X-ray Fluorescence (XRF): XRF analyzes the characteristic X-rays emitted by elements within the coating material. XRF provides a non-destructive method for thickness measurement by correlating X-ray intensity with coating thickness. However, it requires calibration and may not be suitable for all coating materials.
Each method has its advantages and limitations, and the choice depends on factors such as coating material, substrate type, required accuracy, and whether destructive testing is permissible. Combining multiple techniques can provide a more comprehensive evaluation of conformal coating thickness.
What are the consequences of inadequate conformal coating thickness?
Inadequate conformal coating thickness can lead to several consequences, affecting the performance, reliability, and lifespan of electronic components and assemblies. Conformal coatings protect against environmental factors such as moisture, dust, chemicals, and mechanical stress. Insufficient coating thickness compromises these protective properties, resulting in the following consequences:
- Reduced Environmental Protection:Conformal coatings with inadequate thickness provide less protection against environmental hazards such as moisture and contaminants. This increases the risk of corrosion, short circuits, and electrical leakage, especially in harsh operating conditions.
- Increased Vulnerability to Mechanical Damage:Thin coatings offer limited resistance to mechanical stress, including vibrations, impacts, and thermal cycling. Components with inadequate coating thickness are more susceptible to physical damage, leading to premature failure and decreased reliability.
- Insufficient Dielectric Strength:Conformal coatings act as insulating barriers, preventing electrical short circuits between adjacent components or conductive traces. Thin coatings may have lower dielectric strength, increasing the risk of electrical arcing or breakdown under high voltage conditions, potentially causing catastrophic failures.
- Poor Adhesion and Coverage:Inadequate coating thickness can result in poor adhesion to the substrate surface, leading to delamination or peeling over time. Gaps or uncovered areas leave components vulnerable to moisture ingress and contamination, exacerbating reliability issues.
- Inadequate Thermal Management:Conformal coatings can also aid in thermal management by dissipating heat away from electronic components. Thin coatings may not provide sufficient thermal conductivity, leading to localized hotspots, thermal stress, and degradation of sensitive components.
- Compromised Long-Term Performance:Components subjected to inadequate conformal coating thickness are more prone to degradation over time. Exposure to environmental factors and mechanical stress accelerates wear and deterioration, shortening the lifespan of electronic assemblies.
Inadequate conformal coating thickness compromises electronic components and assemblies’ protective, mechanical, electrical, and thermal properties. It increases the risk of premature failure, reliability issues, and reduced performance, highlighting the importance of precise coating application to ensure optimal protection and longevity in electronic devices and systems.
Can conformal coating thickness standards vary based on the type of coating material used?
Yes, conformal coating thickness standards vary based on the coating material used. Conformal coatings are applied to electronic circuitry to protect them from environmental stresses such as moisture, dust, chemicals, and temperature extremes. The thickness of the coating plays a critical role in ensuring adequate protection while avoiding negative impacts such as interference with electrical connections or excessive weight.
Different conformal coating materials have varying properties, including viscosity, curing mechanisms, and chemical compositions. These differences influence the optimal thickness required for adequate protection. Here’s how:
- Acrylic Coatings: Acrylic coatings are popular due to their versatility, cost-effectiveness, and ease of application. They typically require a thinner application than other coatings due to their relatively low viscosity. Generally, thickness standards for acrylic coatings range from 25 to 75 microns, depending on the specific application requirements.
- Urethane Coatings: Urethane coatings offer excellent chemical resistance and durability. They tend to have a higher viscosity than acrylics, necessitating slightly thicker application for adequate protection. Thickness standards for urethane coatings range from 50 to 150 microns.
- Silicone Coatings: Silicone coatings are known for their high-temperature resistance and flexibility. They often require thicker application due to their lower surface tension and ability to flow easily. Thickness standards for silicone coatings can range from 75 to 200 microns.
- Parylene Coatings: Parylene coatings are unique in that they are applied as a vapor and conform to the substrate’s shape, offering uniform coverage even on intricate components. Thickness standards for perylene coatings may vary but generally fall within the 10 to 50-micron range due to their excellent barrier properties, even at thin layers.
While general guidelines exist for conformal coating thickness, variations exist based on the material used. Viscosity, curing mechanisms, and desired protection properties influence the thickness standards. Manufacturers must consider these factors when selecting and applying conformal coatings to ensure optimal performance and reliability of electronic components in various operating environments.
Are there international standards for conformal coating thickness?
Yes, there are international standards for conformal coating thickness, which are crucial in ensuring the reliability and performance of electronic assemblies. Conformal coatings are applied to electronic circuits to protect them from environmental factors such as moisture, dust, chemicals, and temperature variations. Here are some of the essential international standards related to conformal coating thickness:
- IPC-CC-830: The Association of Connecting Electronics Industries ( developed this standard). It provides guidelines for the selection and application of conformal coatings. While it doesn’t specify exact thickness requirements, it does offer guidance on achieving uniform and adequate coverage.
- IEC 61086: This standard, developed by the International Electrotechnical Commission (IEC), specifies requirements for conformal coatings for electrical insulation of printed boards. It includes guidelines for thickness, adhesion, flexibility, and other properties.
- MIL-I-46058C: Although inactive, MIL-I-46058C was a United States military specification defining the requirements for conformal coatings. It included specifications for thickness, adhesion, flexibility, and other performance characteristics.
- ISO 14919: This standard, developed by the International Organization for Standardization (ISO), provides guidelines for applying conformal coatings and specifies requirements for coating materials and thickness.
- ASTM D7866: This standard, developed by ASTM International, provides a test method for measuring the thickness of conformal coatings using non-destructive eddy-current instruments. While not specifying acceptable thickness ranges, it offers a measurement method.
These standards may not prescribe specific thickness values universally applicable to all situations, as coating thickness requirements can vary depending on factors such as the intended application, environmental conditions, and the type of coating used. However, they provide guidelines and testing methods to ensure conformal coatings meet the necessary performance and reliability requirements. Compliance with these standards helps manufacturers produce electronic assemblies that meet quality and reliability expectations.
How do conformal coating thickness standards impact product reliability?
Conformal coating thickness standards play a crucial role in ensuring the reliability of electronic products by providing guidelines for applying protective coatings. Here’s how these standards impact product reliability:
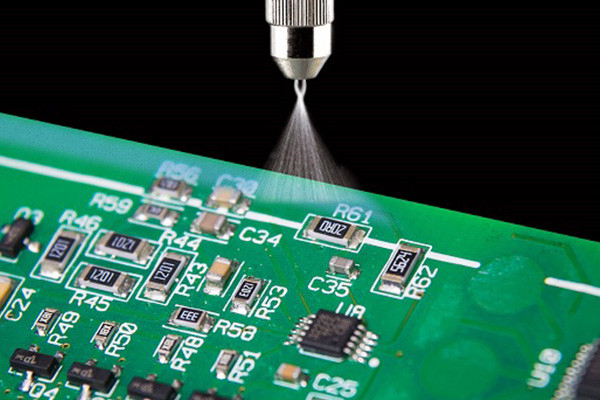
- Protection against Environmental Factors: Conformal coatings protect electronic components from environmental factors such as moisture, dust, chemicals, and temperature extremes. Proper thickness ensures sufficient coverage to shield components effectively. Inadequate coating thickness may expose vulnerable areas, leading to potential damage or failure under harsh environmental conditions.
- Prevention of Corrosion: Corrosion is a significant threat to the reliability of electronic assemblies, particularly in humid or corrosive environments. Conformal coatings act as barriers against moisture and corrosive agents. Standards specifying appropriate coating thickness help prevent corrosion by ensuring complete coverage of susceptible areas, extending electronic product lifespan.
- Insulation and Dielectric Strength: Conformal coatings also provide electrical insulation, protecting against short circuits and electrical failures. Standards define minimum thickness requirements to maintain adequate dielectric strength, ensuring that the coating effectively insulates conductive traces and components. Insufficient thickness can compromise insulation properties, leading to electrical issues and reduced reliability.
- Mechanical Protection: Besides environmental and electrical protection, conformal coatings offer mechanical protection against physical damage, such as scratches, abrasion, and impact. Standards ensure that coatings have sufficient thickness to provide a durable barrier, reducing the risk of mechanical failures during handling, assembly, or operation.
- Uniformity and Consistency: Standards specify minimum thickness requirements and address factors like coating uniformity and consistency. Proper application techniques and quality control measures are essential to achieving uniform coating thickness across the entire assembly. Consistency in thickness ensures consistent protection, contributing to overall product reliability.
Conformal coating thickness standards directly impact product reliability by ensuring effective protection against environmental factors, corrosion, electrical issues, and mechanical damage and by promoting uniformity and consistency in coating application. Compliance with these standards helps manufacturers produce electronic products that meet durability, performance, and longevity expectations, ultimately enhancing customer satisfaction and brand reputation.
What factors should be considered when determining the appropriate coating thickness?
Determining the appropriate coating thickness involves carefully considering various factors to ensure optimal performance and durability. Here are several key factors to consider:
- Substrate Material: The type of material being coated plays a crucial role. Different materials may require different coating thicknesses to achieve adequate adhesion and protection. Factors such as surface roughness and porosity also influence the required thickness.
- Environmental Conditions: The anticipated ecological conditions, including exposure to moisture, chemicals, abrasion, UV radiation, temperature fluctuations, and atmospheric pollutants, must be considered. Thicker coatings may be necessary for harsher environments to provide sufficient protection against corrosion, degradation, and wear.
- Intended Use and Function: The intended function of the coated surface influences the required thickness. For example, structural components may require thicker coatings for enhanced durability and load-bearing capacity, while decorative surfaces may require thinner coatings for aesthetic purposes.
- Coating Material Properties: The properties of the coating material, such as its adhesion strength, flexibility, hardness, and chemical resistance, impact the required thickness. Thicker coatings may be needed to achieve desired performance characteristics, such as improved barrier properties or increased wear resistance.
- Application Method: The method used to apply the coating, whether spray painting, dipping, brushing, or powder coating, affects the achievable thickness and uniformity. Application equipment, technique, and curing process influence the coating thickness.
- Cost Considerations: Thicker coatings generally require more material and longer application times, resulting in higher costs. Balancing performance requirements with budget constraints is essential to ensure cost-effective coating solutions.
- Regulatory Requirements: Regulatory standards and industry specifications may dictate minimum or maximum coating thicknesses for specific applications. Compliance with these requirements is essential to ensure safety, quality, and environmental sustainability.
- Quality Control Measures: Monitoring and testing procedures should be implemented to verify the uniformity and thickness of the applied coatings. Non-destructive testing methods, such as ultrasonic or eddy current testing, can be used to assess coating thickness and integrity.
By carefully considering these factors, engineers and coating professionals can determine the appropriate coating thickness to meet performance requirements, ensure longevity, and optimize cost-effectiveness for various applications.
How do environmental conditions affect conformal coating thickness requirements?
Environmental conditions play a significant role in determining the required thickness of the conformal coating, a protective layer applied to electronic components to shield them from environmental stressors like moisture, dust, chemicals, and temperature variations. Several factors influence the thickness requirements:
- Moisture and Humidity: High humidity and moisture levels can penetrate through thin coatings, potentially causing corrosion and electrical shorts in electronic components. In environments with elevated humidity, thicker coatings are necessary to provide a more robust barrier against moisture ingress.
- Temperature Extremes: Extreme temperatures, whether hot or cold, can impact the stability and effectiveness of conformal coatings. Thin coatings may not protect against thermal cycling, where components undergo frequent temperature fluctuations. Thicker coatings offer better insulation and thermal stability, safeguarding electronic components from temperature-induced stress.
- Chemical Exposure: Environments exposed to harsh chemicals or contaminants require thicker coatings to resist chemical penetration and degradation. Thin coatings may be susceptible to chemical attack, leading to premature failure of electronic devices. Thicker coatings act as a barrier, reducing the likelihood of chemical damage.
- Mechanical Stress: Conformal coatings also provide mechanical protection against physical damage such as abrasion, vibration, and shock. In environments where components are subjected to frequent mechanical stress, thicker coatings offer better resilience and durability, minimizing the risk of damage to sensitive electronic circuits.
- UV Exposure: Ultraviolet (UV) radiation from sunlight can degrade certain conformal coatings over time, compromising their protective properties. Thicker coatings provide better UV resistance and prolong the service life of electronic devices exposed to outdoor or high-UV environments.
Environmental conditions such as moisture, temperature, chemicals, mechanical stress, and UV exposure influence the required thickness of conformal coatings. Thicker coatings are generally preferred in harsher environments to ensure robust protection and extend the longevity of electronic components. However, selecting the appropriate coating thickness should consider the specific environmental challenges faced by the application, balancing protection with other factors such as cost and manufacturability.
What are the minimum, maximum, and optimal conformal coating thickness differences?
Conformal coating thickness is critical in protecting electronic components from environmental factors such as moisture, dust, chemicals, and mechanical stress. Understanding the differences between minimum, maximum, and optimal conformal coating thickness is essential for ensuring the reliability and performance of coated electronics.
- Minimum Conformal Coating Thickness: The minimum conformal coating thickness is the thinnest layer that adequately protects components. This thickness is determined based on the coating material’s properties and the specific environmental conditions the electronics will encounter. Insufficient coating thickness can leave components vulnerable to damage or failure due to moisture, contaminants, or mechanical stress exposure. The minimum thickness ensures that the coating forms a continuous barrier without pin holes or gaps that could compromise protection.
- Maximum Conformal Coating Thickness: Conversely, the maximum conformal coating thickness refers to the thickest layer of coating that can be applied without negatively impacting the performance or functionality of the electronic assembly. Excessive coating thickness can lead to increased thermal resistance, component operation interference, and rework or repair difficulty. It can also result in uneven coverage, trapping air bubbles, or contaminants within the coating, which may degrade electrical performance or cause reliability problems over time.
- Optimal Conformal Coating Thickness: The optimal conformal coating thickness represents the ideal balance between providing adequate protection and avoiding the drawbacks of excessive coating thickness. Achieving the optimal thickness requires considering various factors such as the specific application requirements, environmental conditions, coating material properties, and manufacturing processes. It involves selecting a thickness that ensures robust protection against environmental hazards while maintaining the integrity and functionality of the electronic assembly. Optimizing the coating thickness can also minimize material waste and production costs.
The differences between minimum, maximum, and optimal conformal coating thickness lie in their respective roles in providing protection, avoiding detrimental effects, and achieving the right balance between safety and performance. Understanding and controlling coating thickness is essential to ensuring the reliability and longevity of coated electronic assemblies in diverse operating environments.
Are there specific standards for conformal coating thickness in military applications?
In military applications, conformal coating thickness standards are crucial for ensuring the reliability and longevity of electronic components under harsh environmental conditions such as humidity, temperature variations, and exposure to contaminants. While specific standards may vary depending on the country, branch of the military, or the type of equipment being used, adherence to established guidelines is essential for consistent performance and interoperability.
One widely recognized standard in the United States military is MIL-STD-810, formally known as “Environmental Engineering Considerations and Laboratory Tests.” This standard provides guidelines for various environmental testing procedures, including those related to conformal coatings. While MIL-STD-810 does not prescribe specific conformal coating thickness requirements, it outlines test methods for assessing the effectiveness of coatings under different environmental conditions. For instance, Section 509 of MIL-STD-810 addresses using coatings to protect against fungus growth. Section 514 covers salt fog testing to evaluate corrosion resistance relevant to conformal coatings.
MIL-PRF-55365 is a performance specification that provides requirements for conformal coatings used in electronic assemblies for military applications. While it primarily focuses on performance characteristics such as adhesion, flexibility, and chemical resistance, it may indirectly influence coating thickness requirements by specifying the minimum and maximum thickness allowed for different coating types.
Moreover, specific military branches or defense contractors may have supplemental standards or specifications tailored to their unique requirements. These documents often provide detailed instructions regarding coating application methods, inspection criteria, and quality control measures, which may include recommendations or requirements for coating thickness.
Conformal coating thickness requirements in military applications aim to balance providing adequate protection for electronic components while avoiding potential issues such as interference with heat dissipation or mechanical fit within assemblies. Compliance with established standards ensures that military equipment meets rigorous performance and reliability expectations in demanding operational environments.
How do conformal coating thickness standards impact the cost of manufacturing?
Conformal coating thickness standards are crucial in determining the cost of electronic product manufacturing. Conformal coatings are applied to electronic assemblies to protect them from environmental factors such as moisture, dust, chemicals, and temperature fluctuations. The thickness of these coatings is a critical parameter that directly influences the effectiveness of protection. Here’s how conformal coating thickness standards impact manufacturing costs:
- Material Usage Efficiency: Compliance with specific thickness standards ensures optimal usage of coating materials. Applying too much coating material increases material costs unnecessarily while applying too little might compromise protection, leading to potential product failures and warranty claims. Adhering to established standards helps maintain material usage efficiency, minimize waste, and reduce overall material costs.
- Process Control and Quality Assurance: Conformal coating thickness standards guide process control and quality assurance during manufacturing. Implementing precise coating thickness ensures consistency in product quality and reliability. Consistent quality reduces the likelihood of defects and rework, ultimately lowering production costs associated with scrap, rework, and warranty claims.
- Equipment and Training Costs: To achieve the desired coating thickness consistently, manufacturers may need to invest in specialized equipment such as spray guns, dip coaters, or automated dispensing systems. Additionally, training personnel to operate these systems effectively adds to the overall manufacturing costs. However, adherence to established thickness standards maximizes the efficiency of these investments by minimizing errors and rework.
- Regulatory Compliance: In industries subject to regulatory standards, such as aerospace, automotive, or medical devices, conformal coating thickness may be specified to meet regulatory requirements for product reliability and safety. Non-compliance could result in costly penalties, product recalls, or legal liabilities. Therefore, investing in adhering to thickness standards from the outset can mitigate the risk of non-compliance-related expenses.
- Performance and Reliability: Optimal conformal coating thickness enhances the performance and reliability of electronic assemblies, extending their lifespan and reducing the likelihood of premature failures. This leads to increased customer satisfaction, fewer returns, and a positive brand reputation, which translates into higher sales and market share, offsetting initial manufacturing costs.
Conformal coating thickness standards impact manufacturing costs by influencing material usage efficiency, process control, equipment and training expenses, regulatory compliance, and product performance. While adhering to these standards may entail upfront investments, the long-term benefits of quality, reliability, and customer satisfaction often outweigh the initial costs.
What role does process control play in maintaining conformal coating thickness within standards?
Process control is essential in maintaining conformal coating thickness within standards to ensure the reliability and performance of electronic components. Conformal coatings serve as protective layers for printed circuit boards (PCBs), shielding them from environmental factors such as moisture, dust, chemicals, and temperature extremes. However, the effectiveness of these coatings heavily relies on their uniformity and adherence to specified thickness standards.
Process control in conformal coating involves a series of measures to achieve consistency and accuracy throughout the coating application process. Several vital aspects contribute to maintaining thickness within standards:
- Material Selection and Preparation: Choosing the appropriate conformal coating material is crucial, considering factors such as viscosity, curing method, and compatibility with the PCB and its components. Proper preparation of the coating material, including mixing and filtering, ensures its uniformity and consistency during application.
- Equipment Calibration and Maintenance: Calibration and regular maintenance of coating equipment, such as spray guns or dip tanks, are imperative to achieve consistent coating thickness. Adequately calibrated equipment ensures accurate deposition of the coating material onto the PCB surface, minimizing variations in thickness.
- Process Parameters Monitoring: Monitoring and controlling process parameters such as temperature, humidity, airflow, and coating application speed are vital for achieving the desired coating thickness. Deviations in these parameters can impact the viscosity and flow characteristics of the coating material, leading to inconsistencies in thickness.
- Quality Control and Inspection: Implementing robust quality control measures, including in-process inspections and post-coating thickness measurements, helps identify deviations from standards promptly. Automated inspection systems or manual measurement techniques, such as optical profilometry or eddy current measurement, can verify coating thickness across the PCB surface.
- Feedback and Adjustment: Continuous process performance monitoring allows timely adjustments to optimize coating thickness. Feedback mechanisms, such as statistical process control or real-time monitoring systems, enable operators to identify trends or deviations and take corrective actions as necessary.
By implementing effective process control measures, manufacturers can ensure that conformal coating thickness remains within standards, thereby enhancing electronic assemblies’ reliability, longevity, and performance in various operating environments. Consistent thickness also meets regulatory requirements and customer expectations for quality and reliability.
Can conformal coating thickness standards be adjusted for specific applications?
Yes, conformal coating thickness standards can be adjusted for specific applications, and this customization is often essential to ensure optimal performance and protection of electronic components in various environments.
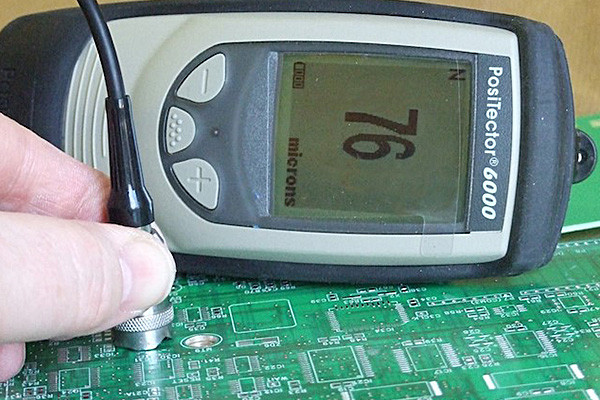
Conformal coatings are applied to electronic circuitry to protect it from moisture, chemicals, dust, and other environmental contaminants. The thickness of the coating plays a critical role in determining the level of protection provided. However, due to the diverse range of applications and environmental conditions electronics may encounter, there is no one-size-fits-all approach to coating thickness standards.
The adjustment of conformal coating thickness standards typically involves a comprehensive evaluation of several factors:
- Environmental Conditions: The specific environmental conditions the electronic device will be exposed to are crucial in determining the appropriate coating thickness. For instance, if the device operates in a highly corrosive environment, a thicker coating may be required for enhanced protection.
- Functionality Requirements: The functional requirements of the electronic device also influence coating thickness. Devices operating in high-vibration environments or undergoing frequent thermal cycling may require thicker coatings to prevent delamination or cracking.
- Regulatory Compliance: Certain industries or applications may have regulatory standards dictating minimum coating thickness requirements for compliance. These standards must be considered when adjusting coating thickness.
- Cost and Manufacturing Constraints: Thicker coatings generally provide better protection but may also increase manufacturing costs and complexity. Balancing the desired level of protection with cost considerations is essential.
- Testing and Validation: Once a coating thickness is determined, it’s necessary to validate its effectiveness through rigorous testing methods tailored to the specific application. This may involve accelerated aging tests, environmental exposure tests, and performance evaluations.
Customizing conformal coating thickness standards for specific applications requires collaboration between electronics manufacturers, coating suppliers, and sometimes regulatory bodies. By considering environmental conditions, functionality requirements, regulatory compliance, cost constraints, and thorough testing, tailored coating thickness standards can be established to ensure the reliability and longevity of electronic devices in diverse operating environments.
What are the challenges in achieving uniform conformal coating thickness?
Achieving uniform conformal coating thickness poses several challenges across various industries, particularly in electronics, automotive, aerospace, and medical device manufacturing. Here are some key challenges:
- Substrate Variability: Substrate materials may vary in composition, surface roughness, and geometry, affecting coating adhesion and thickness distribution. Non-uniform substrates can lead to variations in coating thickness.
- Coating Material Properties: The rheological properties of coating materials, such as viscosity and surface tension, influence their flow and wetting behavior. Controlling these properties is crucial for achieving uniform coverage, especially on complex or irregular surfaces.
- Application Method: Different application methods, such as spray, dip, or spin coating, need help ensuring uniformity. Factors like spray pattern, nozzle distance, and immersion speed can affect coating thickness distribution.
- Process Control: Maintaining consistent process parameters, such as temperature, humidity, and curing time, is essential for uniform coating thickness. Variations in these parameters can result in uneven drying or curing, leading to non-uniform coatings.
- Edge Coverage: Achieving uniform thickness around edges and corners is difficult due to the capillary action and fluid dynamics involved. Uneven edge coverage can leave areas vulnerable to corrosion, delamination, or other defects.
- Masking and Selective Coating: In applications where only specific areas require coating, precise masking techniques are necessary to avoid overcoating or undercoating. Improper masking can lead to consistency in thickness.
- Quality Control and Inspection: Monitoring and inspecting coating thickness across the entire surface is challenging, especially for large or complex components. Techniques such as optical inspection, profilometry, or X-ray fluorescence may be used but can be time-consuming or limited in accuracy.
- Environmental Factors: Environmental conditions, such as airflow, dust particles, and static electricity, can interfere with the coating process and affect thickness uniformity. Controlling these factors within the manufacturing environment is crucial for consistent results.
Addressing these challenges requires precise process design, advanced equipment, material selection, and quality control measures. By understanding and mitigating these factors, manufacturers can improve the consistency and reliability of conformal coating applications.
Are there industry-specific guidelines for conformal coating thickness?
Yes, conformal coating thickness guidelines vary depending on the industry and the application’s specific requirements. Conformal coatings are thin protective films applied to electronic circuitry to protect against environmental factors such as moisture, dust, chemicals, and temperature extremes. While there are no universal standards for coating thickness, several industries have established guidelines based on their unique needs.
In the automotive industry, for instance, conformal coatings are commonly used to protect electronic vehicle components from moisture, vibrations, and temperature variations. Thickness guidelines typically align with the protection required for specific components and their exposure to harsh conditions. For example, coatings for engine control units may require thicker layers than those used for interior electronics.
In the aerospace and defense sector, where reliability and performance are critical, conformal coatings safeguard electronics from extreme temperatures, radiation, and other environmental stressors encountered during flight or military operations. Thickness guidelines here are often stringent, with precise control over coating application to ensure consistent coverage and protection.
In the medical device industry, conformal coatings protect electronics from bodily fluids, sterilization processes, and other contaminants. Guidelines focus on maintaining a uniform and adequate coating thickness to prevent moisture ingress and ensure device reliability over its intended lifespan.
Electronic manufacturing standards such as IPC (Association Connecting Electronics Industries) provide general recommendations for conformal coating thickness based on the type of coating material used and the intended application. However, specific industries may develop standards or adhere to customer specifications to meet their unique performance and reliability requirements.
Ultimately, determining the appropriate conformal coating thickness involves considering factors such as the operating environment, the level of protection needed, and the characteristics of the coating material. Adhering to industry-specific guidelines ensures that electronic components remain reliably protected while meeting the stringent demands of their respective applications.
How do conformal coating thickness standards contribute to regulatory compliance?
Conformal coating thickness standards play a vital role in ensuring electronic device regulatory compliance, particularly in aerospace, automotive, medical, and telecommunications industries where reliability and safety are paramount. These standards establish guidelines for the thickness of conformal coatings applied to printed circuit boards (PCBs) and electronic components to protect them from environmental factors like moisture, dust, chemicals, and temperature variations.
First and foremost, conformal coating thickness standards help ensure consistency and reliability in the performance of electronic devices. By specifying acceptable thickness ranges, these standards ensure that conformal coatings provide adequate protection without compromising the functionality of the electronic components. This consistency in coating thickness helps prevent issues such as uneven coverage, inadequate security, or excessive buildup that could lead to electrical failures or malfunctions.
Moreover, conformal coating thickness standards contribute to regulatory compliance by aligning with industry-specific regulations and standards. For example, in the aerospace and defense sector, adherence to standards like MIL-I-46058C or IPC-CC-830B ensures that electronic components meet the stringent requirements for reliability and durability in harsh operating environments. Similarly, industries such as automotive and medical devices adhere to standards like IPC-CC-830D or IEC 61086 to comply with regulatory mandates related to safety, performance, and environmental sustainability.
Compliance with conformal coating thickness standards also facilitates quality control and traceability throughout manufacturing. Manufacturers can establish and maintain documented processes for applying conformal coatings within the specified thickness ranges, ensuring consistency and repeatability in production. Adherence to these standards also enables thorough inspection and testing protocols to verify coating thickness and performance, enhancing product quality and reliability.
Furthermore, conformal coating thickness standards contribute to risk mitigation by minimizing the likelihood of failures or defects that could lead to product recalls, safety hazards, or regulatory non-compliance issues. By following established standards, manufacturers demonstrate their commitment to producing high-quality, reliable electronic devices that meet regulatory requirements and customer expectations.
Conformal coating thickness standards are essential for ensuring regulatory compliance by promoting consistency, reliability, quality control, and risk mitigation in the manufacturing of electronic devices. Adherence to these standards enhances product performance and durability and fosters trust and confidence among regulatory agencies, customers, and stakeholders.
What are the emerging trends in conformal coating thickness standards?
Conformal coating thickness standards are essential in ensuring the reliability and performance of electronic devices, particularly in harsh environments where they may be exposed to moisture, chemicals, and physical stresses. Several emerging trends are shaping these standards to address evolving industry needs:
- Miniaturization and Component Density: With the ongoing trend towards smaller and denser electronic components, conformal coating thickness standards are adapting to accommodate the need for thinner coatings. This requires precision application techniques and accurate measurement methods to ensure adequate coverage without compromising component functionality.
- Nanotechnology: The emergence of nanotechnology offers opportunities to develop ultra-thin conformal coatings with enhanced protective properties. Standards are being developed to define acceptable thickness ranges at the nanoscale, leveraging advancements in materials science and deposition techniques.
- Flexible Substrates and Wearable Devices: As wearable electronics and flexible substrates become more prevalent, conformal coating thickness standards are evolving to address the unique challenges posed by these applications. Flexible coatings with controlled thicknesses are crucial to maintain device flexibility while providing adequate protection against environmental factors.
- Environmental Regulations and Sustainability: There is a growing emphasis on environmentally friendly coatings and processes in response to regulatory requirements and sustainability concerns. Conformal coating thickness standards incorporate criteria related to material composition, application methods, and waste reduction to promote eco-friendly practices across the industry.
- Advanced Measurement Techniques: Developing non-destructive and high-resolution measurement techniques, such as optical coherence tomography and laser scanning confocal microscopy, influences conformal coating thickness standards. These techniques enable a more accurate and efficient assessment of coating thickness, contributing to improved quality control and reliability.
- Industry Collaboration and Standardization: Collaborative efforts among industry stakeholders, including manufacturers, suppliers, and standards organizations, drive the development of comprehensive and globally recognized conformal coating thickness standards. Standardization promotes consistency in coating applications and facilitates interoperability across supply chains.
Emerging trends in conformal coating thickness standards revolve around the need for thinner coatings to accommodate miniaturization, advancements in nanotechnology, adaptation to flexible substrates, sustainability considerations, utilization of advanced measurement techniques, and collaborative standardization efforts. These trends are essential for ensuring electronic devices’ reliability, performance, and environmental sustainability in diverse applications.
Conclusion:
Conformal coating thickness standards are essential for ensuring the reliability and longevity of electronic components and assemblies. By adhering to these standards, manufacturers can mitigate risks associated with environmental factors and enhance the overall quality of their products. From measurement techniques to regulatory compliance, understanding and implementing conformal coating thickness standards are integral to achieving optimal performance and customer satisfaction in the electronics industry.
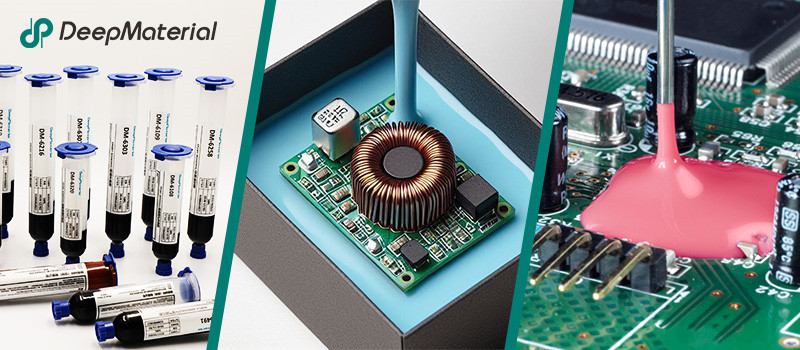
About DeepMaterial
DeepMaterial is a trusted supplier of encapsulant materials that are used in electronics manufacturing worldwide. From chip on board encapsulants such as glob top material to conformal coatings, underfills, low pressure molding, and potting solutions, DeepMaterial offers a full range of circuit board protection materials that effectively protect circuit boards while help reduce costs. More…Deepmaterial is a the manufacturer of epoxy adhesives including hardeners, metalbond, and metal filled resins. Structural, toughened medium viscosity, and non-sag adhesives are also offered. Some adhesives are resistant to thermal shock, chemical, vibration dampening, and impact. Suitable for metals, plastics, wood, and ceramics. Serves electronics, aerospace, automotive, tooling, marine, and construction industries. REACH and RoHS compliant. FDA approved. UL listed. Meets military specifications. We are the one of best adhesive manufacturers in China.
Blogs & News
Potting compounds are at the frontline of electronics assembly, delivering effective protection in challenging environmental conditions while improving mechanical strength and offering high electric insulation. Used within a variety of industries, electrical potting compounds are found within a broad range of consumer electronics, as well as used in applications across the automotive, aerospace, and other industries where electronic assemblies are prevalent.
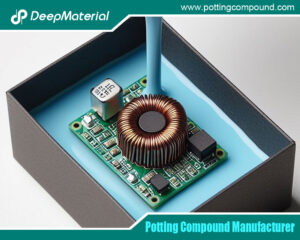
Potting Compound vs. Epoxy: A Comprehensive Comparison
Potting Compound vs. Epoxy: A Comprehensive Comparison In the world of electronics, manufacturing, and material encapsulation, two terms frequently come up: potting compounds and epoxy.
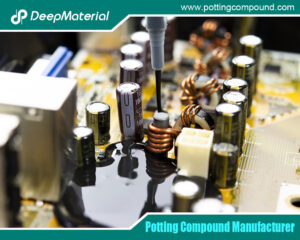
Potting Compound for PCB
Potting Compound for PCB A potting compound is a liquid or semi-liquid material that is poured or injected over a PCB or electronic assembly, then
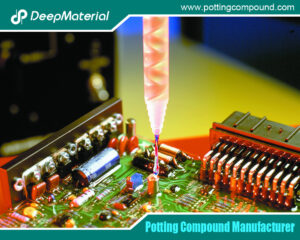
In – depth Analysis of the Curing Characteristics of Electronic Potting Compounds
In – depth Analysis of the Curing Characteristics of Electronic Potting Compounds Electronic potting compounds play a vital role in the electronics industry. They can
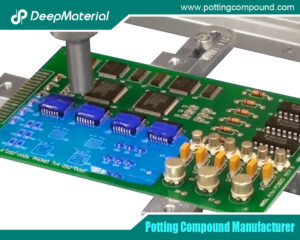
A Comprehensive Analysis of the Environmental Performance of Encapsulating Materials: From Regulations to Practices
A Comprehensive Analysis of the Environmental Performance of Encapsulating Materials: From Regulations to Practices In modern industrial manufacturing, encapsulating materials are widely used in numerous

A Comprehensive Analysis of PCB Encapsulation Quality Inspection: Innovative Application of Non-Destructive Testing Technologies
A Comprehensive Analysis of PCB Encapsulation Quality Inspection: Innovative Application of Non-Destructive Testing Technologies In the field of electronic manufacturing, the encapsulation process of printed
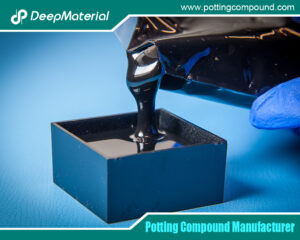
Analysis of the Improvement of the Seismic and Impact Resistance Performance of PCB by Encapsulation
Analysis of the Improvement of the Seismic and Impact Resistance Performance of PCB by Encapsulation During the operation of electronic devices, the PCB (Printed Circuit