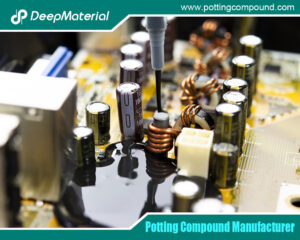
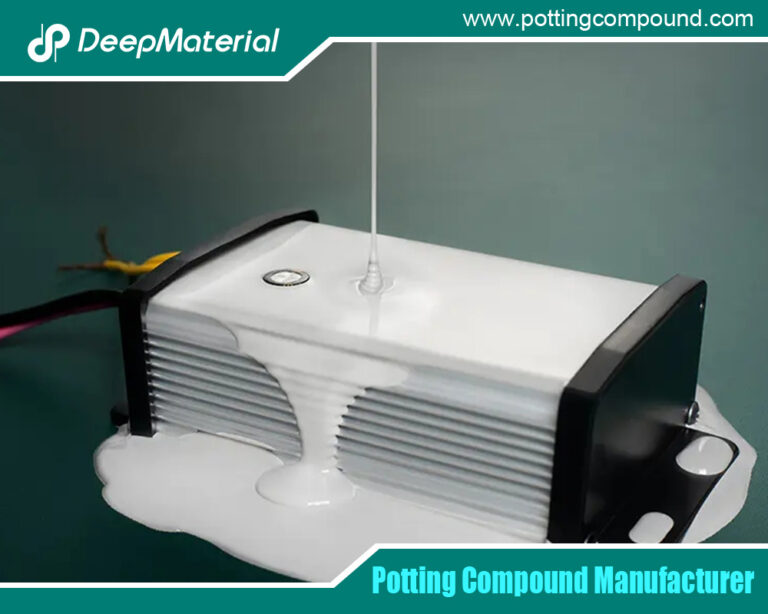
Potting Material for Electronics: A Comprehensive Guide
- Electronic Potting Material Manufacturer
- September 2, 2024
- acrylic vs silicone conformal coating, Automotive potting material manufacturers, china electronic potting silicone manufacturer, Connector Potting Compound, customize china electronic potting silicone factories, electronic potting material, electronic potting material manufacturer, electronic potting silicone china fabrication, Epoxy potting material manufacturers, Flexible Potting Compound, LED Potting Compound, PCB Potting Compound, polyurethane potting compound, potting compound material, potting material, potting material for electronic, potting material for electronic components, potting material for electronics, potting material manufacturer, potting material manufacturers, Potting Materials for Electronics, Silicone Potting Compound, uv conformal coating, UV Cure Conformal Coating, UV Cure Potting Compound, uv epoxy electronic adhesive glue, uv potting compound, uv silicone adhesive glue, waterproof potting compound
Potting Material for Electronics: A Comprehensive Guide
Potting materials are critical in the electronics industry. They play an essential role in protecting electronic components from environmental factors such as moisture, dust, chemicals, and mechanical shock. Potting involves encapsulating an electronic assembly in a solid or gelatinous compound, which enhances the device’s durability and longevity. This article delves into the various aspects of potting materials for electronics, including their types, applications, benefits, and factors to consider when selecting suitable potting materials for specific electronic applications.
Types of Potting Materials
Potting materials can be categorized based on their chemical composition, each offering unique properties suitable for different applications. The primary types of potting materials include:
- Epoxy Resins:
- Properties: Epoxy resins are widely used in the electronics industry due to their excellent adhesive properties, high thermal stability, and resistance to chemicals and moisture. They provide a rigid and robust encapsulation that can withstand mechanical stress.
- Applications: Epoxy resins are ideal for applications requiring high mechanical strength and thermal conductivity, such as power electronics, transformers, and automotive electronics.
- Advantages: Strong adhesion, high mechanical strength, excellent chemical resistance.
- Disadvantages: Brittleness at low temperatures, the potential for high exotherm during curing.
- Polyurethane (PU) Resins:
- Properties: Polyurethane resins offer flexibility and resilience, making them suitable for applications where the electronic components might experience vibrations or movement. They are also resistant to moisture and provide good electrical insulation.
- Applications: Commonly used in consumer electronics, automotive sensors, and LED drivers, where flexibility and vibration resistance are crucial.
- Advantages: Flexible, good moisture resistance, excellent electrical insulation.
- Disadvantages: Limited thermal stability compared to epoxy can be sensitive to moisture during curing.
- Silicone Resins:
- Properties: Silicone resins are known for their exceptional thermal stability, flexibility, and resistance to extreme temperatures. They also offer excellent electrical insulation and are less likely to shrink during curing.
- Applications: Ideal for high-temperature applications, such as aerospace electronics, LED lighting, and automotive electronics exposed to harsh environments.
- Advantages: High thermal stability, flexibility, excellent electrical insulation.
- Disadvantages: Lower mechanical strength compared to epoxy, higher cost.
- Acrylic Resins:
- Properties: Acrylic resins are known for their fast curing times and ease of rework. They offer moderate protection and are typically used in applications where cost and speed are essential.
- Applications: Often used in general electronics, consumer devices, and applications requiring quick turnaround times.
- Advantages: Fast curing, easy to apply, reworkable.
- Disadvantages: Lower chemical and moisture resistance compared to epoxy and polyurethane.
Applications of Potting Materials
Potting materials are used across various industries to protect electronic components from environmental hazards. Some of the most common applications include:
- Automotive Electronics:
- Use Case: Potting materials are extensively used in automotive electronics to protect sensors, control units, and other critical components from harsh environmental conditions such as temperature fluctuations, moisture, and vibrations.
- Materials: Epoxy and polyurethane resins are commonly used due to their mechanical strength and vibration resistance.
- Consumer Electronics:
- Use Case: In consumer electronics, potting materials protect circuit boards, connectors, and other sensitive components from moisture, dust, and physical damage.
- Materials: Polyurethane and acrylic resins are frequently used due to their flexibility and ease of application.
- Aerospace and Defense:
- Use Case: Potting is critical in aerospace and defense electronics, where components are exposed to extreme temperatures, mechanical stress, and corrosive environments.
- Materials: Silicone resins are preferred for their high-temperature resistance and flexibility.
- LED Lighting:
- Use Case: Potting materials are used in LED drivers and fixtures to protect them from moisture, thermal cycling, and mechanical shock.
- Materials: Silicone and epoxy resins are commonly used due to their thermal stability and electrical insulation properties.
- Industrial Electronics:
- Use Case: In industrial settings, potting materials protect electronic components in machinery, sensors, and control systems from harsh environmental conditions such as chemicals, dust, and vibrations.
- Materials: Epoxy and polyurethane resins are often used due to their robustness and chemical resistance.
Benefits of Using Potting Materials
Using potting materials in electronics offers several benefits, enhancing electronic devices’ performance, reliability, and longevity. Some of the key benefits include:
- Environmental Protection:
- Potting materials shield electronic components from environmental factors such as moisture, dust, chemicals, and UV radiation. This protection is crucial for devices operating in harsh or outdoor environments, ensuring they function reliably over time.
- Mechanical Strength and Shock Resistance:
- Potting materials provide mechanical strength to electronic assemblies, protecting them from vibrations, shocks, and physical impacts. This is particularly important in applications where electronic devices are subject to movement or mechanical stress.
- Thermal Management:
- Potting materials with high thermal conductivity help dissipate heat generated by electronic components, preventing overheating and ensuring optimal performance. This is especially important in high-power applications where heat dissipation is critical.
- Electrical Insulation:
- Potting materials offer excellent electrical insulation, preventing short circuits and electrical interference. This is essential for maintaining the integrity of the electronic circuit and ensuring safe operation.
- Chemical and Corrosion Resistance:
- Many potting materials resist chemicals, solvents, and corrosive agents, protecting electronic components from damage in industrial and automotive environments.
- Enhanced Durability and Longevity:
- By providing robust protection against environmental and mechanical stresses, potting materials significantly enhance the durability and longevity of electronic devices, reducing the likelihood of failures and the need for repairs.
Factors to Consider When Selecting Potting Materials
Choosing the suitable potting material for a specific electronic application requires careful consideration of various factors. Some of the critical factors to consider include:
- Thermal Properties:
- Thermal Conductivity: Selecting a potting material with high thermal conductivity is essential for applications where heat dissipation is critical.
- Thermal Stability: Consider the operating temperature range of the electronic device and select a potting material that can withstand those temperatures without degradation.
- Mechanical Properties:
- Flexibility vs. Rigidity: Depending on the application, you may need a flexible potting material (e.g., polyurethane) for components subject to vibrations or a rigid material (e.g., epoxy) for applications requiring high mechanical strength.
- Hardness: The hardness of the cured potting material affects its ability to absorb impacts and resist physical damage.
- Electrical Properties:
- Dielectric Strength: Ensure the potting material provides adequate electrical insulation to prevent short circuits and electrical interference.
- Volume Resistivity: Consider the material’s volume resistivity to ensure it meets the electrical insulation requirements of the application.
- Chemical Resistance:
- Exposure to Chemicals: If the electronic device is exposed to chemicals, solvents, or corrosive agents, select a potting material that offers strong chemical resistance to prevent degradation and failure.
- Curing Process:
- Curing Time: The curing time of the potting material can impact the production process. Fast-curing materials like acrylics may be preferred in high-volume manufacturing environments.
- Curing Temperature: Consider the curing temperature of the potting material, especially if the electronic components are sensitive to heat.
- Reworkability:
- Ease of Rework: In some applications, reworking or repairing the potted electronic assembly may be necessary. Materials like acrylics are more accessible to remove and rework than more rigid materials like epoxy.
- Cost:
- Material Cost: The cost of the potting material is an important consideration, especially in high-volume production. While silicone resins offer superior properties, they are generally more expensive than other materials.
- Environmental Impact:
- Eco-Friendliness: Consider the environmental impact of the potting material, including its disposal and any potential hazards during manufacturing. Some materials may be more environmentally friendly than others.
Innovations and Future Trends in Potting Materials
The electronics industry is continuously evolving, with new technologies and applications driving the development of advanced potting materials. Some of the emerging trends and innovations in potting materials include:
- Nanotechnology-Enhanced Potting Materials:
- Nanotechnology is being used to develop potting materials with enhanced properties, such as increased thermal conductivity, improved mechanical strength, and better electrical insulation. These materials are particularly useful in high-performance and miniaturized electronic devices.
- Environmentally Friendly Potting Materials:
- With growing concerns about environmental sustainability, there is an increasing demand for eco-friendly potting materials. Manufacturers are developing materials that are biodegradable, recyclable, or made from renewable resources, reducing the environmental impact of electronic devices.
- Smart Potting Materials:
- Innovative potting materials are being developed with the ability to self-heal or change properties in response to environmental stimuli. These materials can enhance the reliability and longevity of electronic devices, particularly in critical applications such as aerospace and medical devices.
- Advanced Thermal Management Solutions:
- As electronic devices become more powerful and compact, efficient thermal management is becoming increasingly important. New potting materials with superior thermal conductivity and heat dissipation properties are being developed to meet the demands of high-performance electronics.
- Customizable Potting Solutions:
- Manufacturers are offering more customizable potting solutions tailored to specific applications. This includes adjusting the viscosity, curing time, and mechanical properties of the potting material to meet the unique requirements of different electronic devices.
Conclusion
Potting materials protect electronic components from environmental factors, mechanical stress, and electrical interference. Selecting suitable potting material depends on various factors, including thermal properties, mechanical strength, electrical insulation, chemical resistance, and cost. With advancements in technology, the development of innovative potting materials continues to evolve, offering enhanced protection and performance for a wide range of electronic applications. As the electronics industry moves towards more compact, powerful, and sustainable devices, the role of potting materials will remain crucial in ensuring the reliability and longevity of electronic components.
For more about choosing the top potting material for electronics: a comprehensive guide, you can pay a visit to DeepMaterial at https://www.pottingcompound.com/ for more info.
Recent Posts
- Potting Compound for PCB
- In – depth Analysis of the Curing Characteristics of Electronic Potting Compounds
- A Comprehensive Analysis of the Environmental Performance of Encapsulating Materials: From Regulations to Practices
- A Comprehensive Analysis of PCB Encapsulation Quality Inspection: Innovative Application of Non-Destructive Testing Technologies
- Analysis of the Improvement of the Seismic and Impact Resistance Performance of PCB by Encapsulation
- A Comprehensive Guide to Evaluating the Reliability of Encapsulation Materials for Encapsulated PCBs
- In-depth Analysis of the Reparability of Encapsulation Materials
- A Comprehensive Analysis of Post-Potting PCB Issues and the Repair and Rework of Potting Materials
- A Comprehensive Analysis of the Compatibility between Encapsulation Materials and PCBs: Exploration of Chemical Reactions and Their Impact on Performance
- How to Ensure the Compatibility between Encapsulation Materials and Various Components on PCBs