What are Potting and Encapsulation Services
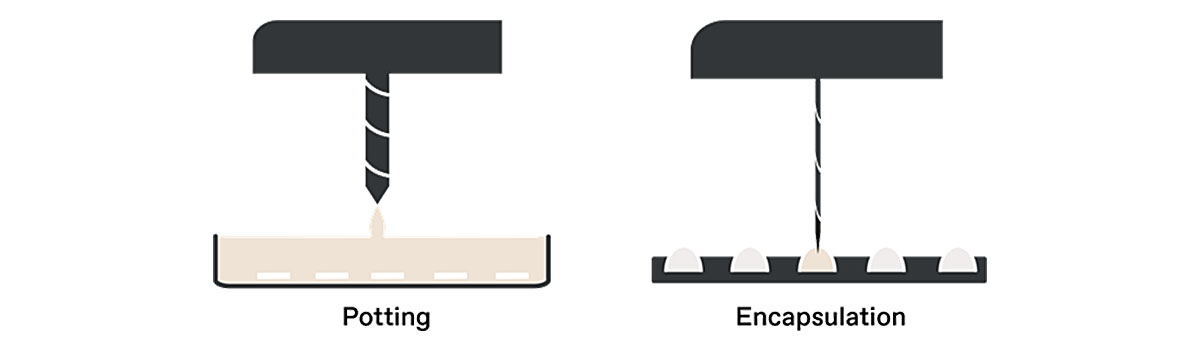
Potting and encapsulation services are essential in various industries, particularly electronics and manufacturing. These processes involve enclosing electronic components, devices, or assemblies in a protective material to safeguard them from environmental factors such as moisture, dust, vibration, and other contaminants. Potting and encapsulation not only enhance the durability and reliability of the components but also provide electrical insulation and thermal management, thus ensuring optimal performance and longevity. In this category, we delve into the intricacies of potting and encapsulation services, exploring their significance, techniques, applications, and advantages.
Table of Contents
ToggleWhat is potting and encapsulation?
Potting and encapsulation are essential in various industries, particularly electronics and manufacturing, to protect sensitive components from environmental factors such as moisture, dust, vibration, and mechanical shock.
Potting:
Potting involves covering electronic components or assemblies with a protective material, typically a liquid resin or compound. This resin is poured or injected around the components and then allowed to cure, forming a solid protective layer. The primary purpose of potting is to provide mechanical support, electrical insulation, and environmental protection to the enclosed components.
Common potting materials include epoxy resins, polyurethanes, silicones, and acrylics. These materials offer different properties, such as flexibility, thermal conductivity, chemical resistance, and adhesion strength, allowing manufacturers to choose the most suitable material for their specific application.
Potting offers several advantages:
- Environmental Protection: Potting seals components from moisture, dust, chemicals, and other contaminants, preventing corrosion and electrical shorts.
- Mechanical Stability: The solid resin encapsulation provides structural support, reducing the risk of damage from vibration, shock, or mechanical stress.
- Improved Thermal Management: Some potting compounds offer excellent thermal conductivity, helping to dissipate heat generated by enclosed components, thus improving reliability and lifespan.
- Electrical Insulation: Potting materials insulate components from each other and external electrical contacts, reducing the risk of short circuits and electrical interference.
Encapsulation:
Encapsulation is similar to potting but typically covers individual components rather than entire assemblies. It is often used for integrated circuits (ICs), sensors, and other delicate components. Encapsulation involves surrounding the element with a protective material, such as molded plastic or resin, to shield it from external elements.
Encapsulation offers similar benefits to potting, including environmental protection, mechanical stability, and electrical insulation. However, it allows for more precise coverage of individual components, making it suitable for applications where space is limited or components must be easily accessible for maintenance or replacement.
Potting and encapsulation are crucial for protecting electronic components from environmental hazards and ensuring their reliability and longevity in various industrial applications.
What are the primary objectives of potting and encapsulation services?
Potting and encapsulation services are crucial in various industries, particularly electronics, to protect sensitive components or devices from environmental factors, mechanical stress, and other potential hazards. The primary objectives of these services can be summarized as follows:
- Environmental Protection: Potting and encapsulation protect against moisture, dust, chemicals, and other contaminants. Manufacturers ensure their durability and reliability by encapsulating electronic components or assemblies in harsh operating conditions, such as outdoor environments or industrial settings.
- Mechanical Stability: One of the critical objectives of potting and encapsulation is to enhance the mechanical stability of electronic devices. This includes supporting delicate components, preventing vibration-induced damage, and improving resistance to physical shocks or impacts. Encapsulation materials such as epoxy resins or silicone elastomers reinforce the assembly’s structural integrity, reducing the risk of mechanical failure.
- Electrical Insulation: Potting and encapsulation materials possess excellent dielectric properties, which insulate electronic components from electrical interference and prevent short circuits. By encapsulating sensitive circuits or conductive traces, manufacturers can minimize the risk of electrical malfunction caused by exposure to moisture or foreign particles, thus improving the device’s overall reliability.
- Thermal Management: Effective potting and encapsulation can aid thermal management by dissipating heat generated by electronic components. Certain encapsulation materials possess high thermal conductivity, allowing them to transfer heat away from sensitive areas and maintain optimal operating temperatures. Proper thermal management helps prolong the lifespan of electronic devices and ensures consistent performance under varying thermal conditions.
- Chemical Resistance: Encapsulation materials often resist various chemicals, including solvents, fuels, and cleaning agents. This chemical resistance prevents degradation of the encapsulated components and ensures long-term reliability in environments where exposure to corrosive substances is a concern.
The primary objectives of potting and encapsulation services revolve around safeguarding electronic components from environmental hazards, enhancing mechanical stability, providing electrical insulation, managing thermal issues, and ensuring chemical resistance. By fulfilling these objectives, manufacturers can produce robust and reliable electronic devices suitable for various applications.
How do potting and encapsulation protect electronic components?
Potting and encapsulation are techniques used in electronics manufacturing to protect electronic components from environmental hazards such as moisture, dust, vibration, and mechanical stress. These methods involve surrounding the sensitive components with a protective material, typically a polymer resin or epoxy, to form a barrier against external factors. Here’s how potting and encapsulation work to safeguard electronic components:
- Physical Protection: Potting and encapsulation create a physical barrier around the electronic components, shielding them from physical damage caused by impact, vibration, or rough handling during transportation, installation, or operation. The encapsulating material acts as a shock absorber, dampening vibrations and preventing mechanical stress from reaching the delicate components.
- Moisture Resistance: Electronics are highly susceptible to damage from moisture, which can cause corrosion, short circuits, and electrical malfunctions. Potting and encapsulation seal the components within a waterproof barrier, preventing moisture ingress and maintaining the integrity of the circuitry even in humid or wet environments. This is particularly crucial for outdoor applications or electronic devices exposed to harsh weather conditions.
- Chemical Protection: Some electronic components are sensitive to chemicals in the environment or during operation. Potting and encapsulation materials can offer chemical resistance, shielding the components from exposure to corrosive substances, solvents, oils, and other potentially harmful chemicals that could compromise their functionality or lifespan.
- Electrical Insulation: The encapsulating material used in potting and encapsulation processes often provides electrical insulation properties. This insulation helps prevent short circuits and electrical interference by effectively isolating the components from each other and external conductive materials.
- Enhanced Durability: By encapsulating electronic components, manufacturers can improve their durability and longevity. The protective barrier provided by potting and encapsulation helps extend the lifespan of the components by reducing wear and tear caused by environmental factors and mechanical stressors.
Potting and encapsulation play vital roles in safeguarding electronic components by providing physical, moisture, chemical, and electrical protection. These techniques enhance electronic devices’ reliability, durability, and performance, ensuring they can withstand various operating conditions and environments without compromising functionality.
What materials are commonly used for potting and encapsulation?
Potting and encapsulation are common techniques used in various industries, such as electronics, automotive, aerospace, and even consumer goods manufacturing, to protect components from environmental factors like moisture, chemicals, vibration, and physical damage. These techniques involve surrounding electronic components, circuits, or assemblies with a protective material to enhance their durability and reliability. Several materials are commonly used for potting and encapsulation, each offering unique properties suited to specific applications.
- Epoxy Resins: Epoxy resins are widely used for potting and encapsulation due to their excellent adhesion, chemical resistance, and thermal stability. They can be formulated to have different viscosities and curing times to suit various applications.
- Silicone: Silicone-based compounds offer flexibility, good electrical insulation properties, and resistance to moisture, heat, and chemicals. They are often used in applications with expected thermal cycling or extreme temperatures.
- Polyurethanes: Polyurethane resins provide good mechanical properties, including impact resistance and flexibility. They are commonly used when vibration damping and shock absorption are essential.
- Acrylics: Acrylic resins offer fast curing times and good adhesion to various substrates. They provide excellent UV resistance and clarity, making them suitable for outdoor applications and applications requiring optical clarity.
- Potting Gels: Potting gels are semi-solid materials that protect against moisture and physical shock. They are often used in applications where components may need to be replaced or repaired.
- Thermal Interface Materials (TIMs): TIMs improve heat transfer between electronic components and heat sinks. They come in various forms, such as greases, pads, and phase change materials, offering different levels of thermal conductivity and ease of application.
- Encapsulation Compounds: Encapsulation compounds are formulated to protect against harsh environmental conditions while maintaining optical clarity. They are commonly used in LED lighting, display, and sensor applications.
Selecting the appropriate potting or encapsulation material depends on the application requirements, environmental conditions, desired mechanical properties, and ease of processing. Compatibility with other materials in the system and regulatory considerations may also influence the choice of material.
What are the differences between potting and encapsulation?
Potting and encapsulation are two standard techniques used in various industries, particularly electronics and manufacturing, to protect sensitive components from environmental factors such as moisture, dust, vibration, and shock. While both processes serve the same overarching purpose of safeguarding electronic components, their methods and applications differ.
Potting involves immersing an electronic component or assembly in a liquid resin or compound. This resin then cures to form a solid protective barrier around the element. The resin used in potting is typically chosen for its insulating properties and ability to resist temperature fluctuations and chemical exposure. Potting compounds come in various formulations, including epoxy, silicone, polyurethane, and acrylic, each offering different levels of protection and flexibility. Potting is often preferred for components that require robust protection against harsh environments or physical damage, such as outdoor electronics, automotive electronics, and industrial control systems.
Encapsulation, on the other hand, involves applying a protective coating or shell directly onto the surface of the electronic component. Unlike potting, which fully immerses the component, encapsulation only covers the exposed surfaces, leaving other areas open. Encapsulation materials can include resins, epoxies, silicones, or other coatings applied through spraying, dipping, or brush coating. Encapsulation is commonly used for applications where selective protection is needed, such as integrated circuits (ICs), sensors, and small electronic devices. It offers advantages in weight reduction, cost-effectiveness, and accessibility for repairs or modifications.
The primary difference between potting and encapsulation lies in the level of coverage and application method. Potting fully immerses the component in a protective resin, offering comprehensive protection but potentially limiting accessibility and flexibility. Encapsulation selectively coats the component’s surfaces, providing targeted protection while allowing for easier maintenance and customization. Both techniques play critical roles in ensuring the reliability and longevity of electronic systems in demanding environments. The choice between potting and encapsulation depends on the specific application requirements, environmental conditions, and desired level of protection.
What industries utilize potting and encapsulation services?
Potting and encapsulation services find applications across various industries where electronic components or devices’ protection, insulation, and stabilization are crucial. Here’s an overview of some sectors that extensively utilize these services:
- Electronics and Semiconductor: Potting and encapsulation are commonly used in electronics manufacturing to protect sensitive components from environmental factors like moisture, dust, chemicals, and mechanical shocks. This includes consumer electronics, telecommunications, industrial control systems, automotive electronics, and aerospace electronics applications.
- Automotive: In the automotive industry, potting and encapsulation services protect electronic control units (ECUs), sensors, and connectors from harsh operating conditions such as temperature variations, vibrations, and exposure to chemicals and fluids. These services help enhance the reliability and longevity of electronic components in vehicles.
- Medical Devices: Medical device manufacturers utilize potting and encapsulation to protect electronic components within medical equipment, such as patient monitoring systems, diagnostic devices, implantable devices, and surgical instruments. These services ensure medical devices’ safety, reliability, and longevity, particularly in demanding clinical environments.
- Renewable Energy: In renewable energy applications like solar power and wind turbines, potting and encapsulation services protect electronics associated with power generation, monitoring, and control systems. These services help safeguard sensitive components from extreme weather conditions, UV radiation, and moisture ingress, thereby ensuring the reliable operation of renewable energy systems.
- Industrial Automation: Industries relying on automation systems, such as manufacturing, process control, and robotics, use potting and encapsulation to protect electronic components housed in controllers, sensors, actuators, and motor drives. These services enhance the resilience of automation equipment against harsh industrial environments and operational stresses.
- Military and Defense: Potting and encapsulation play a crucial role in military and defense applications, where electronic systems must withstand rugged conditions, including temperature extremes, high humidity, shock, and vibration. These services are utilized in various defense technologies, such as radar systems, communication equipment, surveillance devices, and guided munitions.
Overall, potting and encapsulation services cater to diverse industries seeking to enhance the reliability, durability, and performance of electronic components and systems in demanding operating environments.
What are the expected environmental challenges addressed by potting and encapsulation?
Potting and encapsulation are two standard techniques used in various industries to protect electronic components, devices, and assemblies from environmental challenges. These techniques involve encasing sensitive electronics in epoxy resins, silicone gels, or other polymers to provide mechanical support, electrical insulation, and environmental protection. Some of the everyday ecological challenges addressed by potting and encapsulation include:
- Moisture and Humidity: Electronics are susceptible to damage from moisture and humidity, leading to corrosion, short circuits, and performance degradation. Potting and encapsulation create a barrier that seals moisture, preventing it from reaching sensitive components and ensuring long-term reliability in humid environments.
- Chemical Exposure: Exposure to chemicals in industrial environments or harsh operating conditions can corrode electronic components and degrade their performance. Potting and encapsulation materials resist various chemicals, safeguarding electronics from damage and extending their lifespan in chemically aggressive environments.
- Vibration and Mechanical Shock: Electronic components may experience mechanical stresses due to vibration and shock during transportation, handling, or operation. Potting and encapsulation provide structural support and damping properties, reducing the risk of damage from mechanical shocks and ensuring the integrity of the electronic assembly.
- Thermal Cycling: Temperature variations can cause expansion and contraction of materials, leading to mechanical stress and potential failure of electronic components. Potting and encapsulation materials with high thermal conductivity can dissipate heat efficiently, minimizing thermal stress and maintaining stable operating temperatures for electronics in diverse thermal environments.
- Dust and Contaminants: Dust, dirt, and other contaminants can accumulate on electronic assemblies, compromising performance and reliability. Potting and encapsulation create a protective barrier that shields electronics from airborne particles and contaminants, maintaining clean and functional surfaces for optimal operation.
- Electrical Insulation: Potting and encapsulation materials provide electrical insulation, preventing electrical short circuits and leakage currents that can occur due to exposure to moisture, dust, or other environmental factors. This insulation ensures reliable electrical performance and compliance with safety standards.
Overall, potting and encapsulation play a crucial role in mitigating various environmental challenges electronic components and assemblies face, enhancing their reliability, longevity, and performance in diverse operating conditions.
How do potting and encapsulation contribute to product reliability?
Potting and encapsulation are essential processes in electronics manufacturing that significantly contribute to product reliability by protecting environmental factors, mechanical stress, and chemical exposure. These techniques involve covering electronic components with a protective material, typically a resin or polymer, to create a barrier that shields them from external hazards. Here’s how potting and encapsulation enhance product reliability:
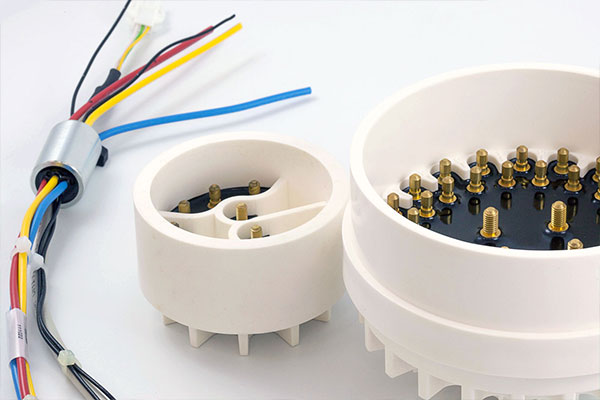
- Environmental Protection: Potting and encapsulation create a sealed barrier around electronic components, preventing moisture, dust, dirt, and other contaminants from infiltrating the device. This protection is crucial for electronics used in harsh environments, such as outdoor applications or industrial settings, where exposure to moisture and debris can lead to corrosion, short circuits, and component failure.
- Mechanical Stability: The encapsulating material adds structural reinforcement to the electronic assembly, enhancing its mechanical strength and durability. It helps to absorb shocks and vibrations, reducing the risk of damage from impact or movement during handling, transportation, or operation. This mechanical stability is particularly beneficial for devices deployed in rugged environments or subjected to frequent handling.
- Electrical Insulation: Potting and encapsulation materials often have excellent electrical insulation properties, safeguarding sensitive electronic components from electrical interference, short circuits, and electrostatic discharge (ESD). By isolating the components from external electrical sources and each other, these techniques minimize the risk of malfunctions or damage caused by electrical faults.
- Thermal Management: Some potting compounds and encapsulants possess thermal conductivity properties that aid in heat dissipation from electronic components. By facilitating efficient thermal management, these materials help prevent overheating and thermal stress, which can degrade performance and reliability over time. Effective heat dissipation prolongs the lifespan of electronic devices and maintains consistent operation under varying temperature conditions.
- Chemical Resistance: Encapsulation materials often resist chemicals, solvents, and other corrosive substances, providing additional protection against environmental hazards. This resistance helps prevent the degradation of the electronic components. It ensures long-term reliability, especially in applications where exposure to chemicals is daily, such as automotive, aerospace, and industrial systems.
Potting and encapsulation play crucial roles in enhancing product reliability by safeguarding electronic components against environmental, mechanical, electrical, thermal, and chemical threats. By providing robust protection and insulation, these techniques contribute to electronic devices’ longevity, performance, and integrity in diverse applications and operating conditions.
What factors should be considered when selecting potting and encapsulation materials?
Selecting the appropriate potting and encapsulation materials is crucial for ensuring electronic components and devices’ durability, reliability, and functionality. Several factors should be carefully considered during the material selection process:
- Environmental Conditions: The operating environment, including temperature fluctuations, humidity levels, chemical exposure, and potential mechanical stresses, plays a significant role. The material chosen should have suitable properties to withstand these conditions without degrading or compromising performance.
- Electrical Properties: Depending on the application, electrical insulation, dielectric strength, and thermal conductivity are essential factors to consider. Potting materials should provide adequate insulation to prevent electrical leakage or short circuits while efficiently dissipating heat generated by the electronic components.
- Chemical Compatibility: Compatibility with other materials used in the system, such as circuit boards, connectors, and substrates, is critical to prevent adverse reactions that could lead to corrosion or degradation over time. Additionally, resistance to chemicals present in the operating environment ensures long-term reliability.
- Mechanical Strength and Flexibility: Potting materials should possess sufficient mechanical strength to provide structural support and protect delicate electronic components from mechanical shocks, vibrations, and external impacts. However, flexibility is essential to accommodate thermal expansion and contraction without cracking or delaminating.
- Adhesion: Strong adhesion to the substrate and encapsulated components is vital to creating a reliable bond that prevents moisture ingress and enhances long-term durability. Proper adhesion also ensures the potting material maintains its integrity under varying conditions.
- Curing Process: Consideration should be given to the curing process of the potting material, including curing time, temperature requirements, and compatibility with the manufacturing process. Optimal curing conditions ensure uniformity and consistency in the final product.
- Cost and Availability: Balancing performance requirements with cost considerations is necessary to achieve a cost-effective solution. Additionally, the availability of the chosen materials in the required quantities should be ensured to prevent supply chain disruptions.
By carefully evaluating these factors, engineers can select potting and encapsulation materials that meet the specific requirements of their application, ensuring the long-term reliability and performance of electronic devices and systems.
What are the various techniques employed in potting and encapsulation?
Potting and encapsulation are essential in electronics manufacturing to protect sensitive components from environmental factors such as moisture, dust, vibration, and thermal shock. These techniques involve the use of materials to encase or cover electronic assemblies. Several methods are employed in potting and encapsulation, each suited to different applications and requirements.
- Resin Encapsulationinvolves using liquid resin materials such as epoxy, silicone, or urethane to encapsulate electronic components. These resins are poured or dispensed onto the assembly and then cured to form a solid protective layer.
- Molding: Molding involves placing electronic components into a mold cavity and injecting molten material such as plastic or rubber. Once the material cools and solidifies, it forms a protective housing around the components.
- Conformal Coating: Conformal coating is a thin protective film applied directly onto the surface of electronic assemblies. These coatings can be sprayed, brushed, or dipped onto the components and provide protection against moisture, chemicals, and mechanical stress.
- Potting Compounds: Potting compounds are dense materials poured or injected into enclosures to surround and protect electronic components completely. These compounds often consist of epoxy or polyurethane and protect against environmental factors.
- Gel Encapsulation: Gel encapsulation involves using soft, flexible gels to encapsulate electronic assemblies. These gels conform to the shape of the components and provide excellent shock absorption and vibration resistance.
- Underfilling: Underfilling is a technique commonly used in semiconductor packaging, where a liquid epoxy is dispensed under the edges of a chip to reinforce the solder joints and improve mechanical strength.
- Vacuum Encapsulation: Vacuum encapsulation involves placing electronic components in a vacuum chamber and introducing a liquid or gel encapsulant. The vacuum helps to remove air bubbles and ensures that the encapsulant surrounds the components.
Each technique offers advantages and disadvantages depending on factors such as the type of protected components, the desired level of protection, and the manufacturing process. By carefully selecting the appropriate potting or encapsulation technique, manufacturers can ensure the reliability and durability of electronic assemblies in various operating environments.
What are the advantages of using potting and encapsulation services?
Potting and encapsulation services offer several advantages across various industries, primarily electronics, aerospace, automotive, and manufacturing. These processes involve enclosing electronic components or assemblies in a protective material such as epoxy resin or silicone. Here are some of the key advantages:
- Protection from Environmental Factors: Potting and encapsulation provide excellent protection against environmental factors such as moisture, dust, chemicals, and vibrations. This shielding helps enhance electronic components’ durability and reliability, particularly in harsh operating conditions like outdoor environments or industrial settings.
- Enhanced Mechanical Strength: The encapsulating materials used in these processes add mechanical strength to delicate electronic components. This reinforcement can prevent damage from physical shocks, vibration, or mishandling during transportation, installation, or operation, thereby extending the lifespan of the components.
- Improved Thermal Management: Potting and encapsulation can improve thermal conductivity, helping to dissipate heat generated by electronic components more effectively. This feature is crucial for maintaining optimal operating temperatures and preventing overheating, which can degrade performance and reliability.
- Electrical Insulation: Encapsulating materials provide insulation, avoiding short circuits and electrical interference. This insulation is essential for ensuring the proper functioning of electronic devices and systems, particularly in high-voltage or sensitive applications where even minor disruptions can cause malfunctions or failures.
- Customized Solutions: Potting and encapsulation services offer flexibility in material selection and application techniques, allowing personalized solutions tailored to specific requirements such as size, shape, performance, and environmental conditions. This versatility enables manufacturers to address diverse needs and optimize the performance of their products.
- Compliance and Standards: Utilizing potting and encapsulation services can help ensure compliance with industry standards and regulatory requirements for product safety, reliability, and environmental protection. Meeting these standards is essential for gaining market acceptance and maintaining customer trust.
- Cost-Effectiveness: While potting and encapsulation services may involve upfront costs, they often result in long-term savings by reducing the need for repairs, replacements, and maintenance associated with unprotected electronic components. Additionally, these services’ enhanced durability and reliability can minimize downtime and improve overall operational efficiency.
Potting and encapsulation services offer a range of benefits, including environmental protection, mechanical reinforcement, thermal management, electrical insulation, customization, compliance, and cost-effectiveness. These advantages make them invaluable for ensuring the performance, reliability, and longevity of electronic components and assemblies across various industries.
How do potting and encapsulation enhance thermal management?
Potting and encapsulation are techniques used in electronics manufacturing to enhance thermal management by providing protection and efficient heat dissipation. These methods involve surrounding electronic components or assemblies with a protective material, typically a resin or polymer compound. While primarily used for protection against environmental factors such as moisture, dust, and mechanical stress, potting and encapsulation also offer significant benefits for thermal management.
Firstly, potting and encapsulation materials often have high thermal conductivity. This means they can efficiently transfer heat from sensitive electronic components to the surrounding environment or heat sinks. By filling the voids and gaps around components, these materials create a more uniform thermal pathway, reducing hot spots and improving overall heat dissipation.
Secondly, encapsulation can provide a barrier against contaminants that could interfere with thermal performance. Dust, moisture, and other environmental factors can degrade the performance of electronic components and hinder heat transfer. By sealing components within a protective enclosure, potting and encapsulation prevent the ingress of contaminants, maintaining optimal thermal conductivity over the long term.
Moreover, potting and encapsulation can enhance the structural integrity of electronic assemblies, allowing for more efficient heat sink integration. Components can be securely embedded within the encapsulation material, facilitating direct contact with heat sinks or thermal interfaces. This close contact improves heat transfer efficiency and ensures effective thermal management throughout the system.
Potting and encapsulation can also enable the design of more compact and lightweight electronic systems. By eliminating the need for bulky heat sinks or external thermal management solutions, manufacturers can reduce their products’ overall size and weight without sacrificing thermal performance. This is particularly advantageous in applications with critical space and weight constraints, such as aerospace or automotive electronics.
Potting and encapsulation are crucial in enhancing thermal management in electronic systems. By providing thermal conductivity and environmental protection, these techniques enable efficient heat dissipation, prevent thermal degradation, and facilitate the design of compact, lightweight, and reliable electronic device design.
What role do potting and encapsulation play in waterproofing electronic devices?
Potting and encapsulation are crucial processes in waterproofing electronic devices. They provide a protective barrier against environmental factors such as moisture, dust, and chemicals. These techniques involve surrounding sensitive electronic components with a material that forms a secure seal, safeguarding them from potential damage.
Potting involves filling the enclosure of an electronic device with a liquid or gel-like compound, typically a polymer resin, which solidifies to form a protective layer around the components. This material effectively shields the electronics from moisture and other contaminants, preventing corrosion and short circuits. Additionally, potting helps to stabilize components, dampen vibrations, and enhance thermal conductivity, improving overall device reliability and performance.
Encapsulation, conversely, entails coating individual components or the entire circuit board with a protective material, usually a resin or silicone compound. This process creates a physical barrier that shields the electronics from external elements, ensuring long-term durability and reliability. Encapsulation can be applied using techniques such as conformal coating, where a thin layer of protective material is sprayed or brushed onto the circuit board, or glob-top encapsulation, where a resin is dispensed directly onto specific components.
Both potting and encapsulation play critical roles in waterproofing electronic devices by creating an airtight seal that prevents water ingress. Water damage is a significant threat to electronic devices, as it can cause corrosion, electrical shorts, and component failure. By effectively sealing the sensitive electronics, potting and encapsulation ensure that devices remain operational even in harsh environments such as outdoor settings or industrial applications where exposure to moisture is every day.
Moreover, these techniques are not only limited to waterproofing but also enhance electronic devices’ mechanical strength and resistance to shock vibration and thermal cycling. This is particularly important in automotive electronics, aerospace systems, and marine equipment applications, where reliability and longevity are paramount.
Potting and encapsulation are essential processes in waterproofing electronic devices. They provide robust protection against moisture and other environmental hazards while improving overall reliability and performance. These techniques are indispensable for ensuring the longevity and functionality of electronic devices in diverse applications and challenging operating conditions.
Can potting and encapsulation services be customized for specific applications?
Potting and encapsulation services play a crucial role in protecting electronic components and assemblies from environmental factors such as moisture, dust, chemicals, and mechanical stress. While these services often involve standard processes, they can indeed be customized to suit specific applications. Customization allows for tailoring the encapsulation material, process parameters, and design considerations to meet the unique requirements of the application in question.
One aspect of customization lies in the selection of the encapsulation material. Different materials offer varying levels of protection and properties such as thermal conductivity, flexibility, and chemical resistance. For example, silicone-based compounds might be preferred for their flexibility and resistance to moisture, while epoxy resins might be chosen for their excellent adhesion and mechanical strength. The choice of material depends on factors such as the operating environment, temperature range, and desired properties of the encapsulated components.
Furthermore, customization extends to the encapsulation process itself. Parameters such as curing time, temperature, viscosity, and dispensing method can be adjusted based on the specific needs of the application. For instance, components destined for high-volume production might require faster curing formulations to minimize production time, while sensitive components might necessitate low-temperature curing to prevent damage.
Moreover, the design of the encapsulation can be customized to accommodate the form factor and layout of the components. This may involve designing molds or fixtures tailored to the shape and size of the assembly, ensuring complete coverage and proper protection without impeding functionality or access to critical areas.
In addition to these technical considerations, customization can also involve compliance with industry standards and regulations relevant to the application, such as RoHS (Restriction of Hazardous Substances) directives for electronics or specific safety standards for automotive or aerospace applications.
Overall, potting and encapsulation services can indeed be customized extensively to meet the precise needs of various applications, offering tailored solutions for enhanced protection, reliability, and performance of electronic components and assemblies in diverse operating environments.
What role do potting and encapsulation play in waterproofing electronic devices?
Potting and encapsulation are crucial processes in waterproofing electronic devices. They provide a protective barrier against environmental factors such as moisture, dust, and chemicals. These techniques involve surrounding sensitive electronic components with a material that forms a secure seal, safeguarding them from potential damage.
Potting involves filling the enclosure of an electronic device with a liquid or gel-like compound, typically a polymer resin, which solidifies to form a protective layer around the components. This material effectively shields the electronics from moisture and other contaminants, preventing corrosion and short circuits. Additionally, potting helps to stabilize components, dampen vibrations, and enhance thermal conductivity, improving overall device reliability and performance.
Encapsulation, conversely, entails coating individual components or the entire circuit board with a protective material, usually a resin or silicone compound. This process creates a physical barrier that shields the electronics from external elements, ensuring long-term durability and reliability. Encapsulation can be applied using techniques such as conformal coating, where a thin layer of protective material is sprayed or brushed onto the circuit board, or glob-top encapsulation, where a resin is dispensed directly onto specific components.
Both potting and encapsulation play critical roles in waterproofing electronic devices by creating an airtight seal that prevents water ingress. Water damage is a significant threat to electronic devices, as it can cause corrosion, electrical shorts, and component failure. By effectively sealing the sensitive electronics, potting and encapsulation ensure that devices remain operational even in harsh environments such as outdoor settings or industrial applications where exposure to moisture is every day.
Moreover, these techniques are not only limited to waterproofing but also enhance electronic devices’ mechanical strength and resistance to shock vibration and thermal cycling. This is particularly important in automotive electronics, aerospace systems, and marine equipment applications, where reliability and longevity are paramount.
Potting and encapsulation are essential processes in waterproofing electronic devices. They provide robust protection against moisture and other environmental hazards while improving overall reliability and performance. These techniques are indispensable for ensuring the longevity and functionality of electronic devices in diverse applications and challenging operating conditions.
What are the steps involved in the potting and encapsulation process?
Potting and encapsulation are crucial processes in electronics manufacturing that protect sensitive components from environmental factors such as moisture, dust, vibration, and shock. These processes involve encapsulating components within a protective material, typically a resin or polymer. Here’s an overview of the steps involved in potting and encapsulation:
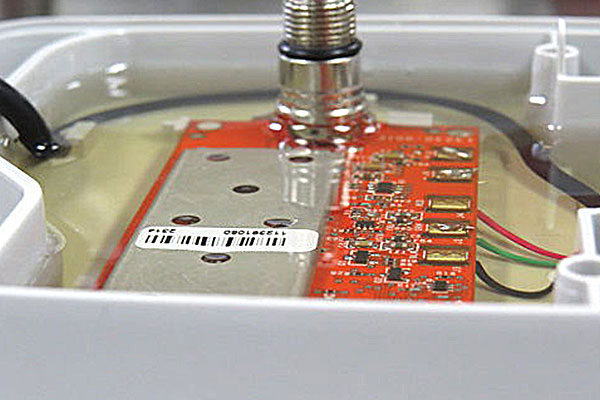
- Selection of Materials: The first step is to choose appropriate potting compounds or encapsulants based on the specific requirements of the application, including temperature range, flexibility, chemical resistance, and mechanical properties.
- Preparation of Components: Components to be potted or encapsulated are inspected for any defects or contaminants. They may also be cleaned and dried to ensure proper encapsulant adhesion.
- Fixture and Molding: Components are placed into fixtures or molds that hold them in the desired position during encapsulation. These fixtures are designed to allow proper encapsulant flow around the components.
- Mixing and Degassing: The potting compound or encapsulant is prepared by mixing the resin and hardener in the correct proportions. This mixture is often degassed to remove any air bubbles that could compromise the integrity of the encapsulation.
- Pouring or Injection: The mixed encapsulant is poured or injected into the mold or fixture containing the components. Care must ensure the encapsulant fills all voids and covers the components uniformly.
- Curing: Once the encapsulant is in place, it can cure or harden. This process may occur at room temperature or require elevated temperatures depending on the type of encapsulant used.
- Post-Cure Inspection: After curing, the encapsulated components are inspected to ensure that the encapsulation is uniform and defects-free. Any excess material may be trimmed or removed as necessary.
- Testing: Encapsulated components undergo various tests to evaluate their performance and durability under simulated operating conditions. This may include tests for electrical conductivity, thermal resistance, moisture resistance, and mechanical strength.
- Final Packaging: Once encapsulation is complete and the components have passed testing, they are packaged for shipment or further assembly into larger electronic systems.
Overall, potting and encapsulation are essential processes in electronics manufacturing that help ensure electronic devices’ reliability and longevity in various operating environments. Proper execution of these steps is critical to the performance and durability of encapsulated components.
How does potting and encapsulation affect the mechanical properties of electronic components?
Potting and encapsulation are standard techniques in electronics manufacturing to protect electronic components from environmental factors such as moisture, dust, vibrations, and thermal fluctuations. While these techniques offer excellent protection against external influences, they can also significantly affect the components’ mechanical properties.
One primary way potting and encapsulation affect mechanical properties is through changes in stiffness and flexibility. When electronic components are potted or encapsulated in epoxy resins or silicones, they become surrounded by a solid matrix. This matrix can increase the component’s stiffness, making it less flexible than in its original state. While increased stiffness can provide additional structural support, it may also make the component more susceptible to mechanical stress and strain, particularly in applications where flexibility is essential.
Additionally, potting and encapsulation can impact electronic components’ thermal expansion and contraction characteristics. Different materials have varying coefficients of thermal expansion, meaning they expand and contract at different rates when subjected to changes in temperature. If the potting or encapsulation material has a significantly different coefficient of thermal expansion than the electronic component, it can lead to mechanical stresses during temperature cycling. These stresses may cause cracking or delamination within or between the encapsulant and the component, compromising mechanical integrity.
Furthermore, potting and encapsulation can affect electronic assemblies’ overall weight and size. While encapsulation adds a layer of protection, it also increases the mass and volume of the component. This increase in weight and size can impact the system’s mechanical requirements, particularly in applications where weight or space constraints are critical factors.
While potting and encapsulation are essential for protecting electronic components from environmental hazards, they can also alter their mechanical properties. These changes include increased stiffness, altered thermal expansion characteristics, and changes in weight and size. Understanding these effects is crucial for designing robust electronic systems that meet the necessary mechanical requirements for their intended application.
Are there any limitations or drawbacks associated with potting and encapsulation?
Potting and encapsulation are widely used in various industries, especially electronics, to protect components and devices from environmental factors such as moisture, dust, and mechanical stresses. However, despite their effectiveness, there are several limitations and drawbacks associated with these processes.
- Limited Repairability: Once a component or device is potted or encapsulated, repairing or replacing individual parts becomes challenging. This lack of repairability can be a significant drawback, especially in applications requiring maintenance or upgrades.
- Thermal Management: Potting compounds and encapsulation materials often have different thermal properties than the components they protect. This can lead to heat buildup and inadequate thermal dissipation, potentially affecting the performance and reliability of the device, particularly in high-temperature environments.
- Material Compatibility: Selecting the appropriate potting compound or encapsulation material is crucial to ensure compatibility with the components being protected. Incompatibility can lead to chemical reactions, degradation of materials, or even failure of the device over time.
- Cost: Potting and encapsulation processes can add significant costs to manufacturing, especially if specialized materials or equipment are required. Additionally, the need for precision and expertise in application adds to the overall cost of production.
- Weight and Size: Potting and encapsulation can increase the weight and size of the final product, which may be undesirable in applications where space and weight are critical factors.
- Curing Time: Many potting compounds and encapsulation materials require significant curing times, extending manufacturing lead times and delaying product delivery.
- Impact on Testing: Potting and encapsulation can make it challenging to perform testing and diagnostics on components or devices, as access to internal components may be restricted.
Despite these limitations, potting and encapsulation remain essential for protecting sensitive electronics and components in harsh environments. Mitigating these drawbacks often involves careful selection of materials, thorough testing, and consideration of specific application requirements. Advances in material science and manufacturing processes continue to address some of these limitations, offering improved solutions for potting and encapsulation.
How do advancements in materials science impact potting and encapsulation services?
Advancements in materials science have significantly impacted potting and encapsulation services, revolutionizing how electronic components are protected and insulated. Potting and encapsulation are crucial in electronics manufacturing, safeguarding delicate components from environmental factors such as moisture, dust, vibration, and temperature extremes. Here’s how advancements in materials science have influenced these services:
- Improved Performance: New materials with enhanced thermal conductivity, dielectric strength, and chemical resistance have emerged, allowing for better performance and durability of encapsulated components. For instance, advanced polymers and resins provide superior protection against moisture ingress and mechanical stress, ensuring the longevity of electronic devices.
- Miniaturization: As electronic devices shrink, materials scientists have developed nano-engineered encapsulants that penetrate tiny gaps and crevices, providing adequate protection even in the most compact electronic assemblies. This enables the miniaturization of devices without compromising their reliability or functionality.
- Customization and Flexibility: The ability to tailor material properties according to specific application requirements has expanded with advancements in materials science. Potting and encapsulation services can now offer customized solutions, such as materials with varying degrees of flexibility, adhesion, and curing time, catering to diverse industry needs.
- Environmental Sustainability: With growing concerns about environmental impact, materials scientists are focusing on developing eco-friendly encapsulation materials derived from renewable sources or recyclable polymers. These sustainable alternatives reduce the carbon footprint associated with electronics manufacturing while maintaining high-performance standards.
- Integration with Advanced Technologies: Materials science advancements have facilitated the integration of additional functionalities into encapsulation materials, such as self-healing properties to repair minor damages or additives for electromagnetic interference (EMI) shielding. These innovations enhance the overall reliability and functionality of encapsulated electronic systems.
- Cost Efficiency: Continuous research in materials science has led to the developing of cost-effective encapsulation materials without compromising quality. Manufacturers can now access high-performance materials at competitive prices, making potting and encapsulation services more accessible across various industries.
Advancements in materials science have propelled potting and encapsulation services to new heights, offering improved performance, customization, sustainability, and cost efficiency. These innovations play a pivotal role in ensuring the reliability and longevity of electronic devices in an ever-evolving technological landscape.
What considerations are essential for ensuring successful potting and encapsulation?
Potting and encapsulation are crucial in various industries, particularly electronics, where they protect sensitive components from environmental factors such as moisture, shock, and vibration. Ensuring successful potting and encapsulation involves several considerations to maintain the integrity and functionality of the encapsulated components.
- Material Selection: Choosing the right potting or encapsulation material is paramount. Factors such as thermal conductivity, flexibility, chemical resistance, and compatibility with encapsulated components should be considered. Common materials include epoxies, silicones, urethanes, and acrylics.
- Compatibility Testing: Before full-scale encapsulation, compatibility testing should be conducted to ensure that the potting material does not adversely affect the components it will encapsulate. This involves assessing potential chemical reactions or physical changes that may occur over time.
- Environmental Conditions: Understanding the operating environment is crucial for selecting an appropriate potting material. Considerations such as temperature extremes, exposure to moisture, chemicals, and mechanical stresses should be considered to ensure the encapsulated components’ longevity and reliability.
- Proper Encapsulation Technique: The potting or encapsulation process should be carried out meticulously to avoid air entrapment, voids, or incomplete coverage of components. Proper dispensing equipment, curing processes, and mold designs should be employed to achieve uniform encapsulation and maximum protection.
- Thermal Management: In applications where heat dissipation is critical, considerations for thermal management should be incorporated into the potting or encapsulation design. This may involve selecting high-const conductivity materials or incorporating heat sinks within the encapsulated assembly.
- Mechanical Protection: Potting and encapsulation should provide adequate mechanical support and shock resistance to the encapsulated components, particularly in applications subject to vibration or impact.
- Regulatory Compliance: Depending on the industry and application, regulatory standards and requirements may exist governing the potting and encapsulation process. Ensuring compliance with relevant standards is essential for product reliability and safety.
By carefully considering these factors and implementing appropriate measures, successful potting and encapsulation can be achieved, enhancing the reliability, durability, and performance of electronic and mechanical assemblies in various applications.
What are some real-world examples showcasing the effectiveness of potting and encapsulation services?
Potting and encapsulation services are crucial in various industries where electronic components or devices need protection from environmental factors such as moisture, dust, vibration, and temperature extremes. Here are some real-world examples showcasing the effectiveness of these services:
- Electronics in Harsh Environments: In the automotive industry, potting and encapsulation protect vehicles’ electronic control units (ECUs). These ECUs control critical functions like engine management and safety systems. By encapsulating them, manufacturers ensure reliable operation despite exposure to extreme temperatures, moisture, and mechanical stress encountered on the road.
- Marine Electronics: Marine navigation equipment, such as GPS units and depth sounders, must withstand exposure to saltwater, humidity, and constant vibration. Potting and encapsulation provide a protective barrier, preventing corrosion and water ingress, thus extending the lifespan of these electronic devices.
- Aerospace Applications: In aerospace, where weight is critical and components are exposed to extreme conditions during flight, potting, and encapsulation play a vital role. Avionics systems, sensors, and communication equipment are often potted to ensure they remain functional in high-altitude environments with significant temperature and pressure fluctuations.
- Renewable Energy Systems: In solar power installations, electronic components such as inverters and charge controllers are subjected to outdoor conditions, including UV radiation, moisture, and temperature variations. Encapsulation protects these components from environmental damage, ensuring reliable performance and longevity of the solar power system.
- Medical Devices: Many medical devices, such as pacemakers and insulin pumps, rely on sensitive electronic components that need protection from bodily fluids and external contaminants. Potting and encapsulation ensure the integrity of these devices, preventing malfunctions that could jeopardize patient health.
- Consumer Electronics: Potting and encapsulation enhance durability and water resistance in consumer electronics, such as smartphones and wearables. This protects internal components from accidental spills, moisture ingress, and mechanical shocks, increasing the lifespan of the devices.
In each of these examples, potting and encapsulation services contribute to electronic systems’ reliability, durability, and performance, ultimately reducing maintenance costs and improving user satisfaction.
Conclusion:
Potting and encapsulation services are indispensable in modern manufacturing, offering a protective shield to electronic components against various environmental stresses. Through the use of specialized materials and techniques, these processes ensure the reliability, durability, and performance of electronic devices across diverse industries. Understanding the nuances of potting and encapsulation is crucial for optimizing product design, enhancing functionality, and meeting stringent reliability standards in today’s competitive market landscape.
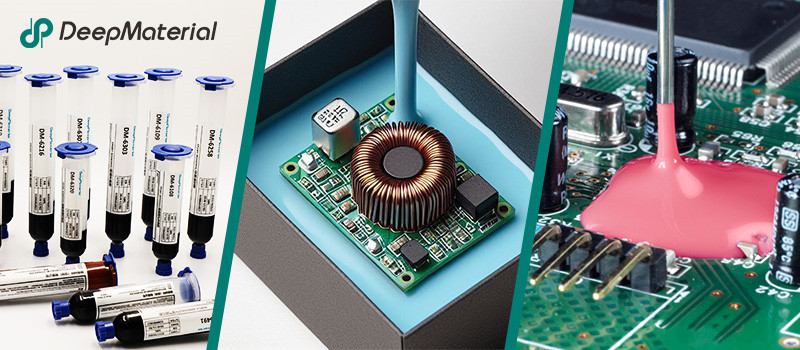
About DeepMaterial
DeepMaterial is a trusted supplier of encapsulant materials that are used in electronics manufacturing worldwide. From chip on board encapsulants such as glob top material to conformal coatings, underfills, low pressure molding, and potting solutions, DeepMaterial offers a full range of circuit board protection materials that effectively protect circuit boards while help reduce costs. More…Deepmaterial is a the manufacturer of epoxy adhesives including hardeners, metalbond, and metal filled resins. Structural, toughened medium viscosity, and non-sag adhesives are also offered. Some adhesives are resistant to thermal shock, chemical, vibration dampening, and impact. Suitable for metals, plastics, wood, and ceramics. Serves electronics, aerospace, automotive, tooling, marine, and construction industries. REACH and RoHS compliant. FDA approved. UL listed. Meets military specifications. We are the one of best adhesive manufacturers in China.
Blogs & News
Potting compounds are at the frontline of electronics assembly, delivering effective protection in challenging environmental conditions while improving mechanical strength and offering high electric insulation. Used within a variety of industries, electrical potting compounds are found within a broad range of consumer electronics, as well as used in applications across the automotive, aerospace, and other industries where electronic assemblies are prevalent.
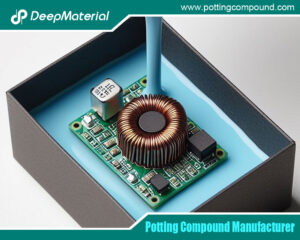
Potting Compound vs. Epoxy: A Comprehensive Comparison
Potting Compound vs. Epoxy: A Comprehensive Comparison In the world of electronics, manufacturing, and material encapsulation, two terms frequently come up: potting compounds and epoxy.
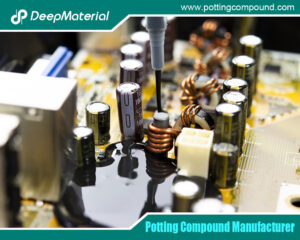
Potting Compound for PCB
Potting Compound for PCB A potting compound is a liquid or semi-liquid material that is poured or injected over a PCB or electronic assembly, then
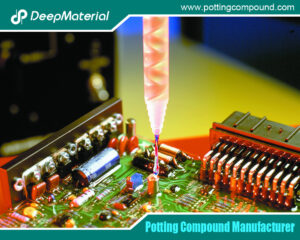
In – depth Analysis of the Curing Characteristics of Electronic Potting Compounds
In – depth Analysis of the Curing Characteristics of Electronic Potting Compounds Electronic potting compounds play a vital role in the electronics industry. They can
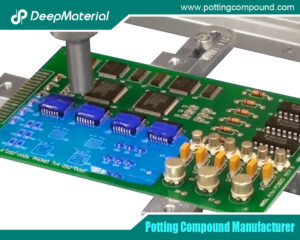
A Comprehensive Analysis of the Environmental Performance of Encapsulating Materials: From Regulations to Practices
A Comprehensive Analysis of the Environmental Performance of Encapsulating Materials: From Regulations to Practices In modern industrial manufacturing, encapsulating materials are widely used in numerous

A Comprehensive Analysis of PCB Encapsulation Quality Inspection: Innovative Application of Non-Destructive Testing Technologies
A Comprehensive Analysis of PCB Encapsulation Quality Inspection: Innovative Application of Non-Destructive Testing Technologies In the field of electronic manufacturing, the encapsulation process of printed
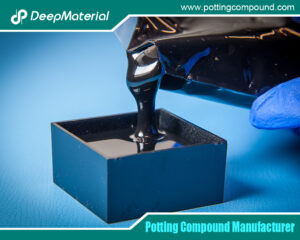
Analysis of the Improvement of the Seismic and Impact Resistance Performance of PCB by Encapsulation
Analysis of the Improvement of the Seismic and Impact Resistance Performance of PCB by Encapsulation During the operation of electronic devices, the PCB (Printed Circuit