Potting Compound
Welcome to our comprehensive guide on potting compounds. Whether you’re a seasoned professional or a novice enthusiast, this page aims to answer common questions about potting compounds. Potting compounds are crucial in various industries, offering protection, insulation, and structural support for electronic components. Let’s delve into the world of potting compounds and explore some frequently asked questions. Whether you’re seeking to enhance your understanding of these materials or seeking guidance on selecting the suitable compound for your application, this guide is here to assist you with every step.
Table of Contents
ToggleWhat is a potting compound?
A potting compound, encapsulant, or potting material is a specialized substance used to encapsulate electronic components for protection and insulation. It serves as a protective housing, encasing delicate electronic parts to shield them from environmental factors such as moisture, dust, vibrations, and mechanical stress. Potting compounds are typically formulated with materials like epoxy, silicone, or urethane, chosen for their ability to provide excellent insulation and structural support.
The primary function of a potting compound is to thoroughly encapsulate electronic components, creating a barrier that prevents the ingress of moisture and contaminants. This encapsulation helps extend the lifespan and reliability of electronic devices by reducing the risk of electrical shorts or malfunctions caused by exposure to external elements. Potting compounds also offer exceptional electrical insulation properties, preventing short circuits and electrical interference by insulating the components from each other and external conductive materials.
Furthermore, potting compounds provide structural support to fragile electronic components, distributing mechanical stresses evenly across the device to reduce the risk of damage from impacts or vibrations. Their versatility and reliability make them indispensable in various industries, including automotive, aerospace, telecommunications, and consumer electronics, where the durability and performance of electronic devices are critical concerns.
What are the primary uses of potting compounds?
Potting compounds find extensive applications across diverse industries due to their versatile properties and protective capabilities. Here are the primary uses of potting compounds:
- Encapsulation:Potting compounds are widely employed to encapsulate electronic components, providing a protective barrier against moisture, dust, vibrations, and mechanical stress.
- Electrical Insulation:They offer excellent electrical insulation properties, safeguarding sensitive electronic parts from short circuits and electrical interference by insulating the components from each other and external conductive materials.
- Environmental Protection:Potting compounds shield electronic devices from harsh environmental conditions, such as extreme temperatures, humidity, and chemical exposure, ensuring their longevity and reliability.
- Structural Support:These compounds reinforce delicate electronic components, distributing mechanical stresses evenly across the device to reduce the risk of damage from impacts or vibrations.
- Thermal Management:Many formulations of potting compounds excel in dissipating heat, preventing overheating of enclosed components, and ensuring optimal performance, particularly in applications where thermal management is crucial.
- Vibration Damping:Potting compounds help absorb and dampen vibrations, reducing the risk of mechanical failures and ensuring the stability and reliability of electronic systems in dynamic environments.
- Customization:Potting compounds come in various formulations, offering flexibility to tailor the encapsulation process to specific application requirements, such as rigidity, flexibility, flame retardancy, or UV resistance.
Potting compounds are indispensable for protecting electronic devices, enhancing their reliability, and extending their lifespan across automotive, aerospace, telecommunications, consumer electronics, and more industries. Their ability to provide robust encapsulation, electrical insulation, environmental protection, and structural support makes them essential components in electronic manufacturing.
How does potting compound differ from other encapsulation materials?
Potting compounds distinguish themselves from alternative encapsulation materials through several critical factors, making them a preferred choice in various industries. Here’s a concise breakdown:
- Chemical Composition:Potting compounds typically consist of epoxy, silicone, or urethane resins, offering a diverse range of chemical compositions suitable for different applications. Unlike other materials, these compounds provide exceptional chemical resistance, ensuring longevity and durability in harsh environments.
- Mechanical Properties:One significant difference lies in their mechanical properties. Potting compounds offer superior adhesion and cohesive strength, effectively encapsulating and securing delicate components against vibration, shock, and mechanical stress. This robustness surpasses many conventional encapsulants, such as adhesives or conformal coatings.
- Thermal Conductivity:Another distinguishing factor is thermal conductivity. Potting compounds often have superior thermal conductivity compared to other plastics or rubbers. This feature facilitates efficient heat dissipation, which is crucial for electronic devices prone to overheating, and enhances overall reliability and performance.
- Environmental Protection:Potting compounds provide exceptional protection against environmental factors such as moisture, humidity, dust, and chemicals. Their ability to form a seamless barrier around components shields them from external elements, ensuring reliable operation even in demanding conditions, a trait not always achievable with alternative encapsulation materials.
- Customization and Application Flexibility:Potting compounds offer versatility in application and customization. They can be tailored to meet specific requirements regarding viscosity, cure time, flexibility, and color, allowing for precise encapsulation of various component geometries and configurations. This adaptability suits them for multiple industries and applications, from automotive electronics to aerospace systems.
Potting compounds stand out from other encapsulation materials due to their unique combination of chemical, mechanical, thermal, and environmental properties, as well as their flexibility and customization options. These characteristics make them an ideal choice for ensuring the reliability and longevity of electronic assemblies in diverse operating conditions.
What are the main components of a potting compound?
Potting compounds are complex formulations designed to provide robust protection and insulation for electronic components. Understanding the composition of these materials is essential for selecting the suitable potting compound for specific applications.
Resins:
- Resins serve as the primary binding agent in potting compounds.
- They provide structural integrity and adhesion to the encapsulated components.
- Epoxy, polyurethane, and silicone resins are commonly used in potting compound formulations.
Hardeners:
- Hardeners are chemical agents that initiate the curing process of potting compounds.
- They react with the resin to form a solid, durable matrix around the electronic components.
- Different hardeners are chosen based on desired curing time, temperature resistance, and mechanical properties.
Fillers:
- Fillers are added to potting compounds to modify their physical properties and reduce cost.
- They enhance thermal conductivity, mechanical strength, and viscosity control.
- Joint fillers include silica, glass fibers, and various mineral powders.
Additives:
- Additives are included in potting compound formulations to impart specific properties or enhance performance.
- Antioxidants and UV stabilizers protect against environmental degradation.
- Flame retardants improve fire resistance, which is crucial in applications with stringent safety requirements.
Solvents and Diluents:
- Solvents and diluents adjust the viscosity of potting compounds for ease of application.
- They facilitate the proper mixing of resin, hardener, and other components.
- Some solvents evaporate during curing, while others may remain in the cured compound or require removal.
Modifiers:
- Modifiers are incorporated into potting compounds to tailor their properties for specific applications.
- Flexibilizers enhance the flexibility of cured compounds, which is beneficial in applications subject to mechanical stress.
- Thickeners control the flow characteristics of potting compounds, ensuring uniform coverage and minimizing waste.
Potting compounds consist of a carefully balanced combination of resins, hardeners, fillers, additives, solvents, and modifiers. Each component plays a vital role in determining the overall performance and suitability of the potting compound for its intended application. By understanding the main components of potting compounds, engineers and manufacturers can make informed decisions when selecting and formulating these materials to meet the unique requirements of their electronic assemblies.
Are there different types of potting compounds available?
Potting compounds come in various formulations, each tailored to specific performance requirements and environmental conditions. Understanding the different types of potting compounds is crucial for selecting the most suitable option for a particular application.
Epoxy Potting Compounds:
- Epoxy potting compounds are renowned for their excellent adhesion, mechanical strength, and chemical resistance.
- They offer superior protection against moisture, chemicals, and temperature extremes.
- Epoxy potting compounds are ideal for highly reliable and durable applications, such as automotive electronics and aerospace systems.
Polyurethane Potting Compounds:
- Polyurethane potting compounds are known for their flexibility, impact resistance, and thermal stability.
- They exhibit good electrical insulation properties and can withstand vibration and thermal cycling.
- Polyurethane potting compounds are commonly used in applications requiring component movement or flexibility, such as in consumer electronics and outdoor equipment.
Silicone Potting Compounds:
- Silicone potting compounds offer exceptional thermal stability, weather resistance, and electrical insulation.
- They maintain flexibility over a wide temperature range and provide excellent protection against moisture and UV radiation.
- Silicone potting compounds are preferred for outdoor applications, LED lighting, and electronic devices exposed to harsh environmental conditions.
Acrylic Potting Compounds:
- Acrylic potting compounds feature fast curing times, low shrinkage, and good adhesion to various substrates.
- They offer a balance of properties suitable for general-purpose potting applications where rapid production turnaround is essential.
- Acrylic potting compounds are used in electronics manufacturing, prototyping, and small-scale applications.
Thermally Conductive Potting Compounds:
- Thermally conductive potting compounds are formulated to dissipate heat efficiently from encapsulated components.
- They feature high thermal conductivity while providing reliable electrical insulation.
- These compounds are essential for thermal management in power electronics, LED lighting, and high-performance computing applications.
The availability of different types of potting compounds allows engineers and manufacturers to select the most appropriate formulation based on specific performance requirements, environmental conditions, and application constraints. Whether prioritizing mechanical strength, flexibility, thermal conductivity, or chemical resistance, a potting compound is available to meet the needs of diverse electronic assemblies.
What factors should be considered when selecting a potting compound?
When selecting a potting compound, several crucial factors should be considered to ensure optimal performance and suitability for the intended application:
- Chemical Compatibility:Evaluate the compatibility of the potting compound with the materials it will contact, such as substrates, components, and environmental factors like solvents or corrosive agents.
- Mechanical Properties:Assess the mechanical strength, flexibility, and durability of the potting compound to withstand stresses such as vibration, thermal expansion, and mechanical shock without cracking or degrading.
- Electrical Insulation:Ensure the potting compound provides adequate electrical insulation to protect sensitive electronic components from short circuits, moisture, and other environmental hazards.
- Thermal Conductivity:Consider the thermal conductivity of the potting compound to dissipate heat effectively, especially in applications where temperature management is critical to prevent overheating.
- Curing Time and Process:Evaluate the curing time and process of the potting compound, considering factors such as temperature requirements, pot life, and curing method (e.g., heat cure, room temperature cure, UV cure) to meet production schedules and efficiency.
- Environmental Resistance:Check the potting compound’s resistance to environmental factors such as moisture, humidity, UV exposure, chemicals, and extreme temperatures to ensure long-term reliability and performance in diverse operating conditions.
- Application Method:Choose a potting compound compatible with the preferred application method, whether manual dispensing, automated dispensing, casting, or molding, to streamline the manufacturing process and achieve consistent results.
- Regulatory Compliance:Verify that the potting compound complies with relevant industry standards, regulations, and certifications (e.g., UL, RoHS, REACH) for safety, environmental sustainability, and end-user requirements.
- Cost and Availability:Consider the overall cost-effectiveness of the potting compound, including the material cost, application costs, and availability of the product in required quantities and lead times.
By carefully evaluating these factors, manufacturers can select the most suitable potting compound to ensure their electronic assemblies and devices’ reliability, performance, and longevity in various applications.
Can potting compounds withstand extreme temperatures?
Potting compounds are widely used in various industries to protect electronic components from environmental factors such as moisture, vibration, and temperature fluctuations. One critical consideration in their selection is their ability to withstand extreme temperatures. Here, we delve into the factors influencing the temperature resilience of potting compounds and their implications in different applications.
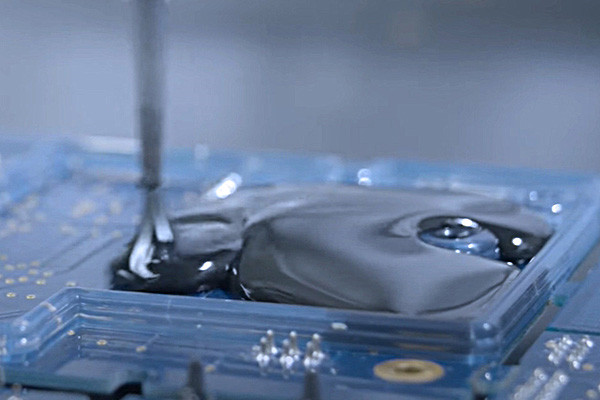
Factors Affecting Temperature Resilience:
Several factors contribute to the ability of potting compounds to withstand extreme temperatures. The chemical composition, curing process, and filler materials significantly determine their thermal stability. Silicones, epoxies, and polyurethanes are common base materials, each offering distinct advantages and limitations in temperature resistance.
Chemical Composition
The chemical structure of potting compounds dictates their thermal properties. Silicones, known for their wide temperature range tolerance, exhibit remarkable resilience at high and low temperatures. Epoxies offer excellent thermal conductivity but may degrade under prolonged exposure to high temperatures. Polyurethanes balance flexibility and temperature resistance, making them suitable for various applications.
Curing Process
The curing process influences the final properties of potting compounds, including their thermal stability. Proper curing ensures the formation of strong bonds within the compound, enhancing its ability to withstand temperature extremes. Controlled curing parameters such as temperature, humidity, and time are critical for optimal thermal performance.
Filler Materials
Incorporating fillers, such as ceramics, silica, or metals, can enhance potting compounds’ thermal conductivity and mechanical strength. However, the choice of filler material and its concentration must be carefully balanced to prevent adverse effects on temperature resilience. Some fillers may exacerbate thermal expansion issues or introduce vulnerabilities to thermal cycling.
Applications and Considerations
The temperature resilience of potting compounds is vital in numerous applications, ranging from automotive electronics to aerospace systems. In automotive environments, where temperature variations can be extreme, potting compounds must maintain their integrity to ensure the longevity and reliability of electronic components. Similarly, in aerospace applications, where temperature differentials between atmospheric re-entry and space vacuum are substantial, potting compounds must withstand extreme conditions without compromising performance.
How do potting compounds provide protection against moisture and contaminants?
Potting compounds are a robust barrier against moisture and contaminants, safeguarding electronic components from potential damage. Several mechanisms contribute to their protective properties:
- Chemical Resistance:Many potting compounds are formulated with materials that exhibit high chemical resistance, making them impervious to moisture, solvents, oils, and other corrosive substances. This resistance ensures long-term stability and reliability, even in harsh operating environments where exposure to chemicals is prevalent.
- Water Repellency:Some potting compounds feature hydrophobic properties, actively repelling water and moisture to prevent ingress and migration within the encapsulated assembly. This water repellency helps maintain the integrity of the electrical insulation and prevents the formation of conductive paths that could compromise performance.
- Adhesion and Bonding:Potting compounds adhere firmly to the surfaces of electronic components and substrates, creating a durable bond that seals gaps and prevents moisture intrusion. This adhesion minimizes the risk of delamination or separation over time, ensuring continuous protection against environmental contaminants.
- Thermal Stability:Potting compounds with high thermal stability maintain their protective properties across various temperatures, resisting degradation or breakdown in extreme thermal conditions. This stability further enhances their ability to shield electronic assemblies from moisture and contaminants, even in challenging operating environments.
- Testing and Certification:Manufacturers subject potting compounds to rigorous testing to evaluate their performance against moisture and contaminant ingress. Certifications such as IP (Ingress Protection) ratings provide standardized metrics for assessing a compound’s effectiveness in resisting environmental hazards and guiding selection decisions for specific application requirements.
Potting compounds provide multifaceted protection against moisture and contaminants through encapsulation, chemical resistance, water repellency, adhesion, thermal stability, and rigorous testing. These compounds ensure critical devices and systems’ long-term reliability and performance, even in demanding operating conditions, by effectively sealing and safeguarding electronic assemblies.
Are potting compounds electrically insulating?
Potting compounds serve as effective electrical insulators, protecting electronic components from electrical hazards and ensuring the integrity of electrical systems. Here are some key points to consider regarding the electrical insulating properties of potting compounds:
- Dielectric Strength:Potting compounds exhibit high dielectric strength, meaning they can withstand high electric field strengths without breaking down. This property is essential for preventing electrical arcing or short circuits that could damage components or compromise system functionality.
- Insulation Resistance:Potting compounds possess excellent insulation resistance, effectively blocking the flow of electrical current between conductive elements. This insulation barrier prevents leakage currents and ensures reliable electrical isolation within the encapsulated assembly.
- Surface Resistance:The surface of potting compounds typically exhibits high resistance to electrical conductivity, minimizing the risk of surface leakage or tracking that could lead to electrical malfunctions or failures. This property is fundamental in applications where environmental contaminants may be present.
- Dielectric Constant and Loss Tangent:Potting compounds often have low dielectric constants and loss tangents, meaning they have minimal influence on the electrical characteristics of the encapsulated components. To prevent the potting material from introducing significant capacitance or energy loss to the circuit, careful selection and application of appropriate compounds are necessary.
- Breakdown Voltage:Potting compounds are engineered to have high breakdown voltages, the voltage at which the material experiences electrical breakdown and allows current to flow. High breakdown voltages ensure the potting material can withstand voltage spikes or transient electrical events without compromising insulation integrity.
- Compliance with Standards:Potting compounds are typically designed and tested to meet industry standards and regulatory requirements for electrical insulation, such as UL (Underwriters Laboratories) standards or specific international standards like IEC (International Electrotechnical Commission) standards. Compliance with these standards ensures that the potting compounds provide reliable electrical insulation in various applications.
Potting compounds are electrically insulating materials, offering essential protection against electrical hazards in electronic assemblies. Their high dielectric strength, insulation resistance, surface resistance, low dielectric constant and loss tangent, high breakdown voltage, and compliance with industry standards make them indispensable for ensuring electrical systems’ safety, reliability, and performance.
What are the key properties to look for in a high-quality potting compound?
Selecting a suitable potting compound protects electronic components from environmental stresses and ensures their long-term reliability. High-quality potting compounds possess specific vital properties that make them ideal for various applications. Here, we discuss the essential properties to consider when choosing a high-quality potting compound to meet the demanding requirements of different industries.
Chemical Stability:
One primary consideration in assessing a potting compound’s quality is its chemical stability. High-quality compounds exhibit excellent chemical resistance, including solvents, acids, and bases, ensuring the integrity of encapsulated electronics in harsh operating environments. This property is particularly crucial in automotive, aerospace, and industrial manufacturing industries, where exposure to corrosive substances occurs daily.
Temperature Resistance:
Another critical property of a high-quality potting compound is its ability to withstand extreme temperatures. Whether subjected to high heat in automotive engine compartments or sub-zero temperatures in outdoor applications, the potting compound must maintain its structural integrity and electrical insulation properties. Compounds with a wide operating temperature range offer versatility and reliability in diverse thermal environments.
Mechanical Strength:
The mechanical strength of a potting compound is essential for protecting encapsulated electronic components against physical shocks, vibrations, and mechanical stress. High-quality compounds exhibit superior adhesion to substrates and exceptional resistance to cracking, delamination, and impact, ensuring the longevity and reliability of the electronics in demanding industrial settings.
Electrical Insulation:
A fundamental property of high-quality potting compounds is their ability to provide effective electrical insulation. The compound should have a high dielectric strength to prevent electrical leakage and breakdown, especially in high-voltage applications. Additionally, low dissipation factor and high volume resistivity are desirable characteristics to maintain the electrical integrity of encapsulated electronics over time.
Environmental Compatibility:
High-quality potting compounds are designed to be environmentally friendly, with minimal impact on human health and the ecosystem. Compounds free from harmful substances such as volatile organic compounds (VOCs), heavy metals, and ozone-depleting chemicals contribute to sustainable manufacturing practices while ensuring compliance with environmental regulations.
How is potting compound applied to electronic components?
Potting compound application is critical in protecting electronic components from environmental factors and ensuring their reliability in various applications. Understanding the process of applying potting compounds to electronic components is essential for achieving effective encapsulation and optimal performance. Here, we explore the critical steps involved in the potting process and the methods commonly used for applying potting compound.
Preparation of Components:
Before applying the potting compound, proper preparation of the electronic components is essential to ensure adhesion and effectiveness of encapsulation. These steps involve thoroughly cleaning the components to remove any contaminants that may hinder bonding and inspecting them for defects or damage.
Encapsulation Process:
The encapsulation process involves applying the potting compound to the electronic components to protect them from environmental stresses. Several methods are commonly used for encapsulating electronic components:
- Dipping:Components are immersed in a container of liquid potting compound, allowing the compound to flow and cover the surfaces uniformly.
- Pouring:The potting compound is poured over the electronic components placed in a mold or enclosure, ensuring complete coverage.
- Injection Molding:The potting compound is injected into a mold containing the electronic components, filling the space around them and forming a protective layer.
Curing and Solidification:
After application, the potting compound undergoes curing or solidification to form a durable protective layer around the electronic components. The curing process may involve:
- Heat Curing:Applying heat accelerates the curing reaction and promotes cross-linking of the compound’s molecules.
- Room Temperature Curing:Allowing the compound to cure naturally at ambient temperature may take longer but can be suitable for heat-sensitive components.
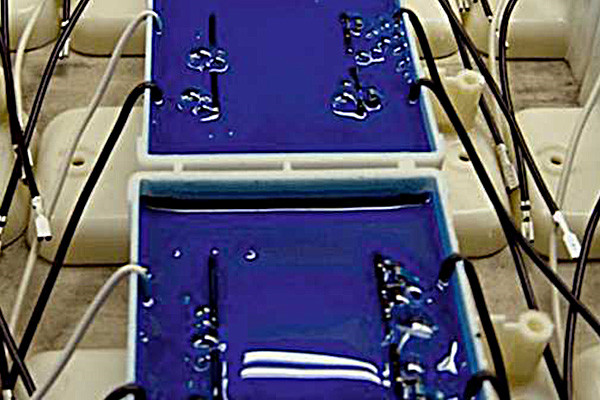
Quality Control and Testing:
Once the potting compound has cured, quality control measures are implemented to ensure the encapsulated electronic components meet performance standards. The process may involve:
- Visual Inspection:Examining the encapsulated components for defects, such as air bubbles, voids, or incomplete coverage.
- Mechanical Testing: Subjecting the encapsulated components to mechanical stress tests to evaluate the strength and integrity of the encapsulation.
- Electrical Testing:Testing the electrical properties of the encapsulated components to ensure proper insulation and functionality.
Applying potting compounds to electronic components involves several key steps, including preparation of components, encapsulation using various methods, curing or solidification, and quality control testing. By following these steps meticulously, manufacturers can ensure electronic components’ adequate protection and reliability in multiple applications.
What precautions should be taken when working with potting compounds?
Working with potting compounds requires careful attention to safety protocols to protect personnel and the integrity of electronic components. Understanding and implementing appropriate precautions is essential for minimizing risks and achieving successful encapsulation outcomes. Here, we outline vital precautions to safeguard individuals and equipment when working with potting compounds.
Personal Protective Equipment (PPE):
Proper personal protective equipment is crucial to prevent exposure to potentially hazardous chemicals and ensure personal safety. The following PPE should be worn:
- Safety goggles or face shield:Protect eyes from splashes or fumes.
- Chemical-resistant gloves:Prevent skin contact with potting compounds.
- Long-sleeved clothing:Minimize skin exposure to chemicals.
- Respirator or mask:Provide respiratory protection against fumes or vapors.
Ventilation and Workspace Setup:
Adequate ventilation and proper workspace setup are essential for minimizing exposure to airborne contaminants and maintaining a safe working environment. Consider the following precautions:
- Work in a well-ventilated area: Ensure good airflow to disperse fumes and vapors.
- Use a fume hood or exhaust fan:Direct harmful fumes away from the work area.
- Avoid confined spaces:Work in areas with sufficient space and ventilation to prevent the accumulation of vapors.
Handling and Mixing Precautions:
Proper handling and mixing of potting compounds are critical to prevent accidents and ensure the effectiveness of encapsulation. Take the following precautions:
- Follow manufacturer instructions:Adhere to recommended mixing ratios and curing procedures.
- Use appropriate tools:Clean, dry utensils and containers are used for measuring and mixing compounds.
- Avoid skin contact:Wear gloves and avoid touching potting compounds with bare hands.
- Work in small batches:Mix only the compound needed to minimize waste and exposure.
Curing and Post-Application Safety Measures:
After applying the potting compound, certain precautions should be taken during the curing process and afterward to ensure safety and quality:
- Allow adequate curing time:Follow recommended curing times to ensure proper solidification of the compound.
- Monitor temperature:Prevent exposure to excessive heat sources during curing to avoid thermal hazards.
- Dispose of waste properly:Dispose of unused or expired potting compounds according to local regulations.
- Clean tools and equipment:Thoroughly clean mixing tools and equipment after use to prevent cross-contamination.
Emergency Preparedness:
Be prepared to respond to emergencies or accidents that may occur during potting operations:
- Emergency eyewash and shower facilities:Provide quick access to facilities for rinsing eyes or skin in case of chemical contact.
- Know emergency procedures: Train personnel on properly handling spills, exposure incidents, or other emergencies.
- Keep emergency contact information:Maintain a list of emergency contacts for medical assistance or spill cleanup services.
Can potting compounds be removed or reworked?
Potting compounds protect electronic components from environmental factors, ensuring their longevity and reliability. However, there are instances where the need arises to remove or rework potting compounds for various reasons, such as component replacement, repair, or design changes. Understanding the feasibility and methods for eliminating or reworking potting compounds is essential for maintaining flexibility and efficiency in electronic assembly processes.
Feasibility of Removal:
Before attempting to remove or rework potting compounds, it is essential to assess the feasibility of the process based on factors such as the type of compound used, the application, and the desired outcome. While some potting compounds are designed to be removable or reworkable, others may pose challenges due to their adhesive strength or chemical properties.
Methods for Removal:
Depending on their composition and adhesion to the substrate, several methods can be employed to remove potting compounds. Some standard techniques include:
- Mechanical removal: Using tools such as chisels, scrapers, or abrasive materials to break down and remove the potting compound physically.
- Heat-based methods:Applying heat through hot air guns, infrared heaters, or soldering irons to soften the potting compound and facilitate removal.
- Chemical solvents:Chemical solvents or strippers specifically formulated to dissolve or weaken the potting compound for easier removal are utilized.
Considerations for Rework:
In cases where reworking the potting compound is necessary, specific considerations must be taken into account to ensure the integrity of the electronic components and the effectiveness of the encapsulation. These considerations may include:
- Compatibility with new components:Ensuring the latest components or modifications are compatible with the remaining potting compound or any rework materials used.
- Adhesion and compatibility:Selecting rework materials or potting compounds that adhere well to the substrate and provide adequate protection against environmental stresses.
- Avoiding damage:Taking precautions to prevent damage to surrounding components, circuitry, or substrates during rework.
Challenges and Limitations:
Despite the availability of removal and rework methods, there are challenges and limitations associated with these processes. These may include:
- Time and labor-intensive:Reworking or removing potting compounds can be time-consuming and labor-intensive, especially for compounds with solid adhesion or complex encapsulation designs.
- Risk of damage:There is a risk of damaging electronic components or substrates during the removal or rework, particularly if proper precautions and techniques are not followed.
- Effectiveness of rework:The effectiveness of reworking potting compounds may vary depending on factors such as the type of compound, substrate material, and application requirements.
Are there environmentally friendly options for potting compounds?
Potting compounds encapsulate electronic components, protecting them from environmental factors such as moisture, dust, and vibration. They are widely employed in various industries, including electronics, automotive, and aerospace, to ensure the longevity and reliability of electronic devices.
Environmental Impact of Conventional Potting Compounds:
However, the widespread use of conventional potting compounds raises concerns about their environmental impact. Many traditional formulations contain hazardous substances like volatile organic compounds (VOCs), heavy metals, and other toxic chemicals. These substances can leach into the environment during production, use, and disposal, posing risks to ecosystems and human health.
Exploring Eco-Friendly Alternatives:
Researchers and manufacturers are actively exploring alternative, more environmentally friendly formulations in response to these environmental challenges. These eco-friendly potting compounds aim to reduce or eliminate the use of hazardous substances while maintaining the performance and reliability required for various applications.
Biodegradable Potting Compounds:
One promising avenue is the development of biodegradable potting compounds derived from renewable resources such as plant-based polymers. These compounds offer the advantage of breaking down naturally over time, reducing the long-term environmental impact associated with traditional formulations.
Low-VOC Formulations:
Another approach focuses on formulating potting compounds with low or no VOCs, minimizing emissions during production and use. These formulations often utilize water-based or solvent-free systems, reducing the release of harmful chemicals into the environment.
Recyclable Materials:
Furthermore, efforts are being made to incorporate recyclable materials into potting compound formulations, facilitating the recycling process at the end of the product’s life cycle. By designing compounds with recyclability in mind, manufacturers can help reduce the amount of waste generated and promote a more circular economy.
How does the curing process of potting compounds work?
Understanding how potting compounds cure is crucial for ensuring their effectiveness and reliability in protecting electronic components. The curing process involves several key steps and factors that influence the final properties of the encapsulant. Here’s an overview:
- Chemical Reaction:Many potting compounds undergo a chemical reaction during curing, typically initiated by heat or a catalyst. This reaction causes the compound to change from a liquid or gel-like state to a solid, forming a durable protective barrier around the components.
- Crosslinking:In thermosetting compounds, curing involves the formation of crosslinks between polymer chains. These crosslinks create a three-dimensional network that enhances the compound’s mechanical strength, thermal stability, and resistance to environmental factors.
- Time and Temperature:The curing time and temperature play crucial roles in determining the final properties of the potting compound. Higher temperatures generally accelerate the curing process, but excessive heat can lead to issues such as thermal stress or incomplete curing. Manufacturers carefully optimize curing parameters to achieve the desired performance and production efficiency balance.
- Exothermic Reaction:Some curing reactions are exothermic, which releases heat as they proceed. Proper thermal management is essential to prevent overheating, which can affect the integrity of the encapsulated components or lead to thermal runaway.
- Post-Cure Aging:After initial curing, potting compounds may undergo additional aging or post-cure processes to enhance their properties further. This process may involve exposing the cured material to elevated temperatures or humidity. This exposure helps improve adhesion, reduce internal stresses, or enhance long-term stability.
Understanding the intricacies of the curing process allows manufacturers to select the appropriate potting compound formulation and optimize curing conditions for specific applications. By ensuring thorough and reliable curing, engineers can maximize the performance and longevity of electronic devices in demanding environments.
Can potting compounds be colored for aesthetic purposes?
Potting compounds can be colored to enhance the aesthetic appeal of electronic devices while maintaining their protective functionality. Here are some key considerations and methods for coloring potting compounds:
- Pigment Addition:One standard method for coloring potting compounds involves adding pigments or dyes during the formulation stage. These colorants are carefully selected to ensure compatibility with the base resin and curing system while achieving the desired hue and opacity.
- Customization Options:Manufacturers offer a range of color options to suit different design preferences and branding requirements. From vibrant primary colors to subtle earth tones, engineers can choose from a diverse palette to complement the overall aesthetics of their products.
- UV Stability:When selecting colorants for potting compounds, UV stability is critical, especially for outdoor or high-exposure applications. UV-resistant pigments help maintain color integrity over time, preventing fading or discoloration caused by prolonged sunlight exposure.
- Transparency and Opacity:Depending on the desired effect, engineers can opt for transparent, translucent, or opaque coloring formulations. Transparent compounds allow visibility of underlying components or indicators, while opaque options provide complete coverage and hide internal circuitry.
- Consistency and Uniformity:A professional finish must achieve consistent color distribution throughout the potting compound. Proper mixing techniques and quality control measures ensure uniform dispersion of colorants, minimizing variations and streaks in the final product.
- Impact on Performance:While coloring potting compounds offers aesthetic benefits, it’s crucial to consider any potential effects on material properties or performance. Adding colorants may alter curing kinetics, thermal conductivity, or electrical insulation properties, requiring careful evaluation and testing.
By leveraging colored potting compounds, designers can enhance the visual appeal of electronic devices, convey brand identity, differentiate products in the market, and create cohesive design schemes across product lines. With a diverse range of color options and careful attention to performance requirements, colored potting compounds offer versatility and creativity in electronic design.
What considerations are important for potting compound compatibility with different substrates?
When selecting a potting compound for electronic encapsulation, ensuring compatibility with various substrates is paramount to the performance and reliability of the final product. Several key considerations must be taken into account:
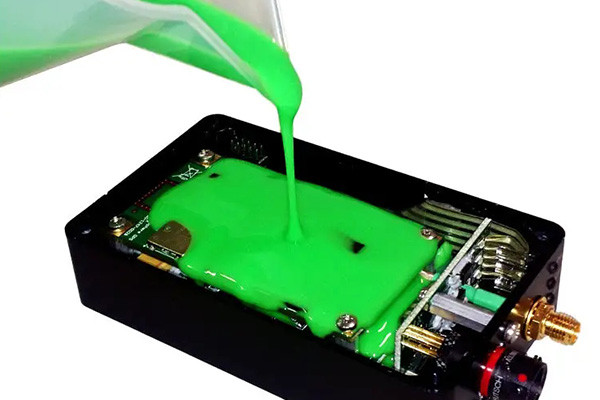
Substrate Material Compatibility:
Different substrates, such as metals, plastics, and ceramics, may interact differently with potting compounds due to variations in surface energy, porosity, and thermal expansion coefficients. Understanding the specific properties of the substrate material is essential for selecting a compatible potting compound that adheres well and minimizes the risk of delamination or mechanical stress.
Chemical Compatibility:
Potting compounds must also be compatible with coating, adhesives, or surface treatments applied to the substrate. Chemical interactions between the potting compound and substrate coatings could lead to adhesion failure or degradation of protective layers, compromising the device’s performance and longevity.
Thermal Expansion Matching:
Matching the thermal expansion coefficients of the potting compound and substrate is critical to minimize the risk of thermal stress-induced cracks or delamination. Significant disparities in thermal expansion can lead to mechanical failure, especially in environments with wide temperature fluctuations.
Electrical Insulation Properties:
The potting compound must maintain sufficient electrical insulation properties for electronic applications to protect against short circuits or leakage currents. Compatibility with the substrate material ensures uniform insulation coverage and prevents electrical breakdowns, safeguarding the device’s functionality and safety.
Adhesion Strength and Surface Preparation:
Proper surface preparation of the substrate is essential to promote adhesion between the potting compound and substrate material. Techniques such as cleaning, degreasing, and roughening the surface enhance bonding strength and ensure long-term adhesion stability in challenging operating conditions.
Environmental Compatibility:
Consideration must also be given to the environmental conditions the encapsulated device will encounter, such as temperature extremes, humidity, and exposure to chemicals or solvents. Compatibility with the operating environment helps prevent the potting compound and substrate from degrading, swelling, or corroding over time.
By carefully evaluating these compatibility factors and selecting a potting compound tailored to the specific requirements of the application and substrate materials, engineers can ensure optimal performance, reliability, and longevity of electronic devices in diverse operating environments.
Are there specific potting compounds designed for specialized applications?
Potting compounds are engineered to meet the diverse needs of various industries and applications, with specialized formulations tailored to specific requirements. Here are some examples of specialized potting compounds and their applications:
High-Temperature Applications:
- Potting compounds are designed to withstand extreme temperatures, such as those encountered in automotive engine compartments or aerospace components.
- Formulations with enhanced thermal stability and resistance to thermal cycling prevent degradation or loss of mechanical properties under heat stress.
Chemical Resistance:
- Potting compounds are formulated to resist exposure to harsh chemicals, solvents, or corrosive substances commonly found in industrial environments.
- Chemically inert formulations that maintain integrity and performance when subjected to aggressive chemical agents ensure long-term reliability in chemical processing plants or laboratory equipment.
Underwater and Marine Applications:
- Waterproof potting compounds are engineered to provide effective encapsulation and protection for electronic devices operating in underwater environments or marine applications.
- Formulations with high water resistance and saltwater corrosion resistance, preventing ingress of moisture and safeguarding sensitive electronics on marine vessels or underwater sensors.
Flexible and Vibration Damping:
- Flexible potting compounds that absorb mechanical shocks and vibrations are ideal for applications subjected to frequent movement or impact.
- Elastomeric formulations that maintain flexibility over a wide temperature range, ensuring resilience and durability in automotive suspension systems or industrial machinery.
Optical Transparency:
- Transparent potting compounds optimized for optical clarity and light transmission are suitable for encapsulating LEDs, sensors, or display panels.
- Low-refractive-index formulations minimize light scattering and distortion, thereby maximizing the efficiency and performance of optical devices.
Biocompatible and Medical Grade:
- Potting compounds are formulated to meet stringent biocompatibility standards for medical devices and implants.
- Non-toxic, hypoallergenic materials with minimal risk of adverse reactions or tissue irritation, ensuring compatibility with the human body in medical applications such as pacemakers, implants, or wearable health monitors.
These specialized potting compounds demonstrate the versatility and customization options available to engineers, enabling them to address unique challenges and requirements in diverse industries ranging from automotive and aerospace to electronics and healthcare. By selecting the appropriate potting compound for each application, manufacturers can optimize their products’ performance, reliability, and safety.
What are some common challenges encountered when using potting compounds?
Potting compounds offer adequate protection for electronic components, but their application can present various challenges that engineers must address to ensure optimal performance and reliability. Here are some common challenges encountered when using potting compounds:
Adhesion and Compatibility:
Achieving proper adhesion between the potting compound and substrate material is crucial for long-term reliability. Ensuring compatibility with diverse substrates and surface treatments requires careful consideration of material properties and surface preparation techniques to prevent delamination or adhesion failure.
Thermal Management:
Managing heat dissipation within encapsulated electronic assemblies is essential to prevent thermal stress and degradation of component performance. Selecting potting compounds with suitable thermal conductivity properties and optimizing encapsulation designs help dissipate heat effectively while maintaining component integrity.
Curing and Processing:
The curing process of potting compounds can pose challenges related to curing time, temperature, and uniformity. Proper curing parameters must be established to ensure thorough crosslinking and achieve desired mechanical and electrical properties without inducing thermal damage or incomplete curing.
Mechanical Stress and Shock Absorption:
Electronic devices subjected to mechanical shock or vibration require potting compounds with adequate shock-absorbing properties to protect sensitive components from damage. Balancing stiffness and flexibility in the potting material helps mitigate mechanical stress and enhance device durability in rugged environments.
Chemical Exposure and Environmental Factors:
Potting compounds may be exposed to various chemicals, solvents, and environmental conditions that can degrade their performance over time. Selecting chemically resistant formulations and conducting thorough compatibility testing help mitigate the effects of exposure and ensure long-term reliability in challenging operating environments.
Optical Clarity and Light Transmission:
Applications requiring optical transparency, such as LED encapsulation or optical sensors, demand potting compounds with high optical clarity and minimal light scattering. Maintaining optical performance while providing effective encapsulation and protection presents a unique challenge that requires specialized formulations and processing techniques.
Conclusion:
Potting compounds are essential materials in various industries, offering protection and stability for electronic components. By addressing these frequently asked questions, we hope to provide you with a better understanding of potting compounds and their applications. Whether you’re seeking durability, insulation, or environmental resilience, choosing the right potting compound is crucial for the success of your projects. If you have further inquiries or require assistance in selecting the ideal potting compound for your needs, don’t hesitate to reach out to our experts.
Welcome to our comprehensive guide on potting compounds. Whether you’re a seasoned professional or a novice enthusiast, this page aims to answer common questions about potting compounds. Potting compounds are crucial in various industries, offering protection, insulation, and structural support for electronic components. Let’s delve into the world of potting compounds and explore some frequently asked questions. Whether you’re seeking to enhance your understanding of these materials or seeking guidance on selecting the suitable compound for your application, this guide is here to assist you with every step.
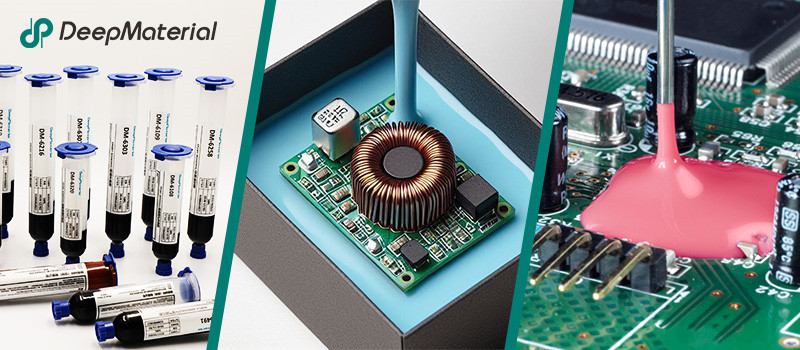
About DeepMaterial
DeepMaterial is a trusted supplier of encapsulant materials that are used in electronics manufacturing worldwide. From chip on board encapsulants such as glob top material to conformal coatings, underfills, low pressure molding, and potting solutions, DeepMaterial offers a full range of circuit board protection materials that effectively protect circuit boards while help reduce costs. More…Deepmaterial is a the manufacturer of epoxy adhesives including hardeners, metalbond, and metal filled resins. Structural, toughened medium viscosity, and non-sag adhesives are also offered. Some adhesives are resistant to thermal shock, chemical, vibration dampening, and impact. Suitable for metals, plastics, wood, and ceramics. Serves electronics, aerospace, automotive, tooling, marine, and construction industries. REACH and RoHS compliant. FDA approved. UL listed. Meets military specifications. We are the one of best adhesive manufacturers in China.
Blogs & News
Potting compounds are at the frontline of electronics assembly, delivering effective protection in challenging environmental conditions while improving mechanical strength and offering high electric insulation. Used within a variety of industries, electrical potting compounds are found within a broad range of consumer electronics, as well as used in applications across the automotive, aerospace, and other industries where electronic assemblies are prevalent.
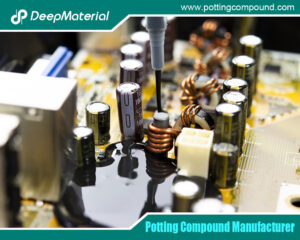
Potting Compound for PCB
Potting Compound for PCB A potting compound is a liquid or semi-liquid material that is poured or injected over a PCB or electronic assembly, then
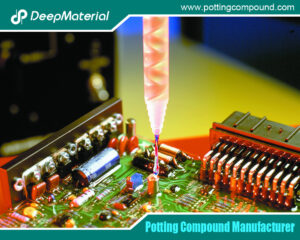
In – depth Analysis of the Curing Characteristics of Electronic Potting Compounds
In – depth Analysis of the Curing Characteristics of Electronic Potting Compounds Electronic potting compounds play a vital role in the electronics industry. They can
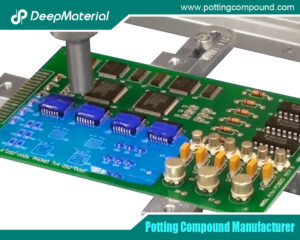
A Comprehensive Analysis of the Environmental Performance of Encapsulating Materials: From Regulations to Practices
A Comprehensive Analysis of the Environmental Performance of Encapsulating Materials: From Regulations to Practices In modern industrial manufacturing, encapsulating materials are widely used in numerous

A Comprehensive Analysis of PCB Encapsulation Quality Inspection: Innovative Application of Non-Destructive Testing Technologies
A Comprehensive Analysis of PCB Encapsulation Quality Inspection: Innovative Application of Non-Destructive Testing Technologies In the field of electronic manufacturing, the encapsulation process of printed
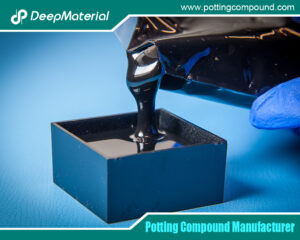
Analysis of the Improvement of the Seismic and Impact Resistance Performance of PCB by Encapsulation
Analysis of the Improvement of the Seismic and Impact Resistance Performance of PCB by Encapsulation During the operation of electronic devices, the PCB (Printed Circuit
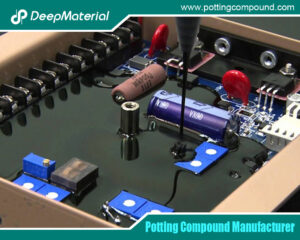
A Comprehensive Guide to Evaluating the Reliability of Encapsulation Materials for Encapsulated PCBs
A Comprehensive Guide to Evaluating the Reliability of Encapsulation Materials for Encapsulated PCBs In modern electronic devices, the printed circuit board (PCB) plays a central