What is the difference between conformal coating and non conformal coating
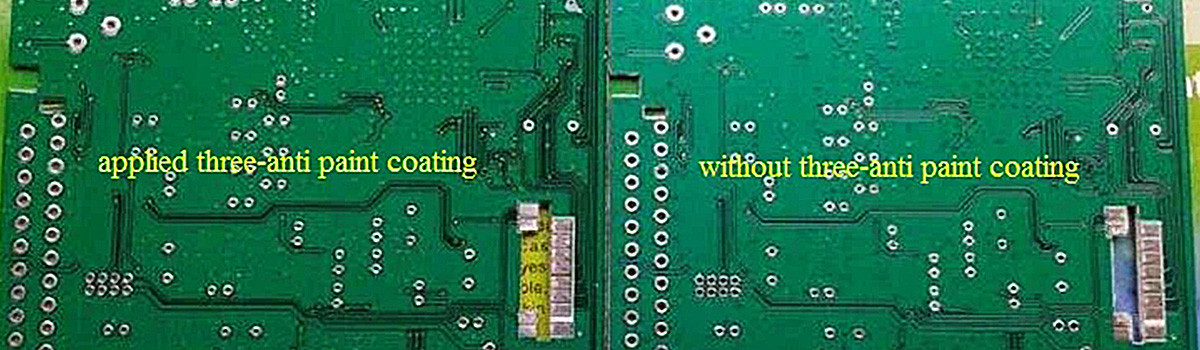
Conformal and non-conformal coatings are both essential processes in electronic manufacturing. They protect electronic components from environmental factors such as moisture, dust, chemicals, and mechanical stress. While they serve the same overarching purpose, they differ significantly in their application methods, material properties, and areas of use. Understanding the differences between conformal and non-conformal coatings is crucial for choosing the right protective solution for various electronic assemblies.
Table of Contents
ToggleWhat is Conformal Coating?
Conformal coating is a protective material applied to electronic circuitry to protect it from environmental factors such as moisture, dust, chemicals, and temperature extremes. It conforms to the contours of the electronic components, providing a thin, protective film that adheres to the surface of the PCB (Printed Circuit Board) and its components. This coating is typically transparent, allowing visual inspection of the circuitry after application.
The primary purpose of conformal coating is to enhance the reliability and longevity of electronic devices by preventing corrosion, short circuits, and other forms of damage caused by environmental stressors. By forming a barrier between the sensitive electronic components and the external environment, conformal coatings safeguard the integrity and functionality of the circuitry.
Various conformal coatings are available, each offering unique properties suited to specific application requirements. Common types include acrylic, silicone, polyurethane, and epoxy coatings. Each type has advantages and limitations regarding properties, such as chemical resistance, flexibility, dielectric strength, and ease of application.
Acrylic coatings are widely used due to their affordability, ease of application, and good moisture resistance. Silicone coatings offer excellent flexibility and thermal stability but may have reduced chemical resistance compared to other types. Polyurethane coatings provide robust protection against chemicals and abrasion but may require specialized application techniques. Epoxy coatings offer superior protection against moisture and chemicals, making them suitable for harsh environments.
The application process of conformal coating involves spraying, dipping, brushing, or dispensing the coating onto the PCB. After application, the coating is cured through air drying, UV, or thermal curing to form a durable protective layer.
What is Non-Conformal Coating?
Non-conformal coating is a type of protective coating applied to electronic circuitry to protect it from environmental factors such as moisture, dust, chemicals, and other contaminants. Unlike conformal coatings, which uniformly cover the entire surface of a circuit board, non-conformal coatings are selectively applied to specific areas or components of the board, leaving other areas exposed.
Non-conformal coatings are typically used when certain circuitry parts need to remain accessible for troubleshooting, repairs, or adjustments after assembly. By selectively applying the coating, manufacturers can protect sensitive components while allowing access to critical areas when necessary.
Common types of non-conformal coatings include silicone-based coatings, acrylics, and urethanes. These coatings provide a barrier against environmental factors while offering electrical insulation and protection against mechanical stress.
Non-conformal coatings are widely used in aerospace, automotive, consumer electronics, and medical devices, where electronic components may be exposed to harsh operating conditions. Proper application of non-conformal coatings is crucial to ensure the reliability and longevity of electronic devices in challenging environments.
What are the Key Differences Between Conformal and Non-Conformal Coatings?
Conformal and non-conformal coatings are utilized in various industries, particularly electronics, to protect components from environmental factors such as moisture, dust, chemicals, and temperature variations. However, they differ significantly in their application methods, properties, and suitability for different situations.
Conformal coatings are applied thinly and uniformly to conform to the contours of the substrate, covering all surfaces evenly. They typically include acrylics, silicones, urethanes, and epoxies. The primary advantage of conformal coatings is their comprehensive protection while maintaining the integrity of delicate components and intricate circuitry. They offer excellent moisture and chemical resistance, electrical insulation, and thermal stability. Moreover, conformal coatings can be easily removed and re-applied if necessary, making them ideal for applications where maintenance or rework may be required.
On the other hand, non-conformal coatings are applied more thickly and do not necessarily conform to the substrate’s contours. These coatings are often used in applications requiring a higher degree of protection, such as in harsh environmental conditions or where mechanical stresses are prevalent. Non-conformal coatings may include materials like potting compounds, encapsulants, or thick layers of certain conformal coatings. Unlike conformal coatings, non-conformal coatings are more challenging to remove and rework, often requiring specialized tools or processes.
The choice between conformal and non-conformal coatings depends on several factors, including the application’s specific requirements, environmental conditions, mechanical stresses, and the level of protection needed. Conformal coatings are typically preferred for applications where precision, flexibility, and ease of rework are essential, such as in consumer electronics or aerospace electronics. In contrast, non-conformal coatings are favored for applications where ruggedness, durability, and enhanced protection are paramount, such as in automotive electronics or industrial machinery subjected to harsh operating conditions.
While both conformal and non-conformal coatings serve the common purpose of protecting electronic components, their differences lie in application methods, properties, and suitability for various environmental and mechanical challenges. Understanding these distinctions is crucial for selecting the most appropriate coating solution for a given application.
What are the Main Application Methods for Conformal Coating?
Conformal coating is a protective film applied to electronic circuitry to protect against environmental factors such as moisture, dust, chemicals, and temperature extremes. The main application methods for conformal coating include:
- Spraying: Spraying is one of the most common application methods for conformal coating. It involves using specialized equipment such as air spray guns or automated spraying systems to apply a uniform coating of liquid conformal material onto the surface of the electronic assembly. This method is efficient for covering large areas quickly and can be automated for high-volume production.
- Dipping: Dipping involves immersing the electronic assembly into a bath of liquid conformal coating material. The assembly is typically held in the bath for a predetermined amount to ensure complete coverage, and then it is withdrawn and allowed to drain and cure. Dipping is suitable for coating complex shapes and components with intricate geometries but may require more extended processing than spraying.
- Brushing: Brushing is a manual method where the conformal coating material is applied to the surface of the electronic assembly using a brush or applicator. This method offers precise control over the coating thickness and is suitable for touch-up or repair work on small areas where automated methods may be impractical.
- Selective Coating: Selective coating involves applying conformal coating material only to specific electronic assembly areas while masking off other areas to prevent coating. This method is often used to protect sensitive components or areas that require additional protection without covering the entire assembly.
- Vapor Deposition: Vapor deposition is a more advanced application method that involves depositing a thin film of conformal coating material onto the surface of the electronic assembly using a vacuum chamber and a deposition process such as chemical vapor deposition (CVD) or physical vapor deposition (PVD). This method is suitable for producing highly uniform and precise coatings but may require specialized equipment and processes.
Each application method for conformal coating offers advantages and is chosen based on factors such as the complexity of the electronic assembly, production volume, desired coating thickness, and the properties of the conformal coating material.
How is Non-Conformal Coating Applied?
Non-conformal coating is a protective layer applied to electronic circuit boards and components to safeguard them against environmental factors such as moisture, dust, chemicals, and temperature fluctuations. Applying non-conformal coatings involves several steps to ensure adequate coverage and protection.
Firstly, the circuit board undergoes a thorough cleaning process to remove any contaminants, such as dust, oils, or residues, that might interfere with the coating’s adhesion. This cleaning step is crucial as it ensures proper adhesion and coating uniformity.
Next, the circuit board is masked to protect areas that should not be coated, such as connectors, switches, and sensitive components. Masking typically uses specialized tapes, plugs, or liquid masking materials applied precisely to the desired areas.
The non-conformal coating material is then prepared according to manufacturer specifications. Standard non-conformal coatings include acrylics, epoxies, silicones, urethanes, and perylene. The coating material is often applied using spraying, dipping, brushing, or selective coating methods.
Spraying is a commonly used method where the coating material is atomized into fine droplets and applied evenly onto the surface of the circuit board using a spray gun. Dipping involves immersing the circuit board into a coating material reservoir, allowing the material to flow over and encapsulate the components. Brushing is a manual method of applying the coating material using brushes or applicators to ensure precise coverage in specific areas.
On the other hand, selective coating involves masking off areas of the circuit board to be protected and then applying the coating only to the exposed areas using specialized equipment that can accurately dispense the coating material.
After application, the coated circuit board is typically cured using heat or UV light to facilitate the curing process and ensure proper adhesion and durability of the coating. Once cured, the masking materials are removed, and the circuit board undergoes inspection to ensure uniform coverage and quality of the non-conformal coating.
The application of non-conformal coatings involves cleaning, masking, applying the coating material using various methods, curing, and final inspection to ensure adequate protection of electronic components and circuit boards.
What are Some Examples of Conformal Coating Materials?
Conformal coating materials protect electronic components from environmental factors such as moisture, dust, chemicals, and temperature variations. They form a protective layer over circuit boards, ensuring their reliability and longevity. Here are some examples of conformal coating materials commonly used in electronics manufacturing:
- Acrylic Resins: Acrylic conformal coatings offer excellent moisture resistance and insulation properties. They are relatively easy to apply and remove if necessary. Acrylic coatings are also known for their flexibility, making them suitable for applications where the board may experience slight bending or flexing.
- Silicone: Silicone conformal coatings provide superior protection against extreme temperatures, making them ideal for harsh environments. They offer excellent moisture resistance and can withstand thermal cycling without cracking or losing adhesion. Silicone coatings also provide good electrical insulation properties.
- Urethane Resins: Urethane conformal coatings offer a balance of properties, including chemical resistance, moisture resistance, and mechanical durability. They provide a rigid, protective barrier against abrasion and solvent exposure. Urethane coatings are often preferred for applications requiring high-performance protection.
- Parylene: Parylene coatings are deposited through a vapor deposition process, resulting in a thin, uniform layer that conforms to the shape of the substrate. Parylene coatings offer outstanding moisture and chemical resistance without adding significant weight or thickness to the assembly. They are commonly used in medical devices and aerospace applications.
- Epoxy Resins: Epoxy conformal coatings provide excellent adhesion to various substrates, including metals, plastics, and ceramics. They offer good chemical and moisture resistance and mechanical protection against impact and vibration. Epoxy coatings can be formulated to meet specific requirements for flexibility and hardness.
- Fluoropolymer: Fluoropolymer conformal coatings, such as PTFE (polytetrafluoroethylene) or FEP (fluorinated ethylene propylene), offer exceptional chemical resistance and non-stick properties. They are often used in applications where protection against corrosive chemicals or contaminants is critical.
Each type of conformal coating material has its advantages and is selected based on factors such as environmental conditions, desired performance characteristics, and ease of application. Proper selection and application of conformal coatings are crucial to ensuring the reliability and longevity of electronic assemblies in various industries.
What Types of Materials are Used for Non-Conformal Coating?
Non-conformal coatings are applied to electronic components and assemblies to protect them from environmental factors such as moisture, dust, chemicals, and mechanical stress. These coatings can be of various types, offering unique application properties. Some typical materials used for non-conformal coating include:
Acrylics: Acrylic coatings are popular due to their ease of application, low cost, and good moisture resistance. They provide excellent protection against environmental factors and have good dielectric properties, making them suitable for various electronic applications.
Silicones: Silicone coatings offer high flexibility and thermal stability, making them ideal for applications with extreme temperatures. They provide excellent protection against moisture, chemicals, and mechanical stress, making them suitable for harsh environments.
Urethanes: Urethane coatings offer superior chemical and abrasion resistance compared to other coatings. They provide excellent protection against solvents, oils, and fuels, making them suitable for applications in industries such as automotive and aerospace.
Epoxy Resins: Epoxy coatings provide excellent adhesion and chemical resistance. They offer high dielectric strength and thermal stability, making them suitable for critical electrical insulation applications.
Parylene: Parylene coatings are applied via vapor deposition, resulting in a conformal and pinhole-free coating. Parylene offers excellent barrier properties against moisture and chemicals while maintaining good electrical insulation properties. It is commonly used in medical devices and aerospace applications.
Fluoropolymers: Fluoropolymer coatings such as Teflon offer exceptional non-stick properties and resistance to chemicals and high temperatures. They are commonly used in applications requiring low friction and high chemical resistance.
Polyurethanes: Polyurethane coatings provide excellent flexibility and abrasion resistance. They offer good moisture and chemical resistance, making them suitable for outdoor applications exposed to harsh weather conditions.
Hybrid Coatings: Some non-conformal coatings are formulated by combining two or more materials to achieve specific properties. For example, a hybrid coating may combine silicone’s flexibility with urethane’s chemical resistance.
Non-conformal coatings are essential for protecting electronic components and assemblies from environmental factors. The choice of coating material depends on the application’s specific requirements, including environmental conditions, desired properties, and budget constraints.
Which Environmental Factors Do Conformal Coatings Protect Against?
Conformal coatings are crucial in safeguarding electronic components from many environmental factors, ensuring their reliability and longevity in various operating conditions. These coatings, typically applied in thin layers, adhere to the contours of electronic assemblies, providing a protective barrier against a range of environmental stressors. Some prominent environmental factors that conformal coatings protect against include moisture, dust, chemicals, temperature fluctuations, and mechanical shock.
Moisture ingress is one of the most prevalent causes of electronic failure, leading to corrosion, short circuits, and electrical leakage. Conformal coatings, often formulated with moisture-resistant materials such as silicone, acrylic, or polyurethane, act as a barrier to prevent moisture penetration into sensitive electronic components, thus preserving their functionality.
Dust and airborne contaminants threaten electronic assemblies, potentially causing interference, overheating, or electrical arcing. Conformal coatings effectively shield against these particles, minimizing the risk of contamination and ensuring optimal performance in dusty environments.
Chemical exposure can severely compromise electronic components, leading to corrosion, degradation of solder joints, or insulation breakdown. Conformal coatings formulated with chemical-resistant materials create a protective layer that shields against exposure to corrosive substances, acids, solvents, and other hazardous chemicals, enhancing electronic assemblies’ durability.
Temperature fluctuations, including extreme heat or cold, can induce thermal stress on electronic components, leading to material expansion, contraction, and subsequent mechanical failure. Conformal coatings offer thermal insulation, dissipating heat and providing a buffer against rapid temperature changes, thus maintaining the integrity of electronic circuits in diverse thermal environments.
Mechanical shock and vibration represent additional challenges for electronic devices, especially in rugged applications or during transportation. Conformal coatings with shock-absorbent properties help cushion the impact of mechanical stress, reducing the risk of physical damage and ensuring the reliability of electronic assemblies in demanding operating conditions.
Conformal coatings are versatile protective measures that guard electronic components against moisture, dust, chemicals, temperature variations, and mechanical shocks. By mitigating these environmental factors, conformal coatings contribute to electronic devices’ reliability, longevity, and performance across a wide range of applications.
What Environmental Hazards Are Non-Conformal Coatings Effective Against?
Non-conformal coatings safeguard electronic components and devices against many environmental hazards. Typically, polymer-based coatings provide a protective barrier that shields sensitive electronics from various detrimental factors. While their effectiveness can vary depending on the specific composition and application method, non-conformal coatings generally mitigate several environmental hazards.
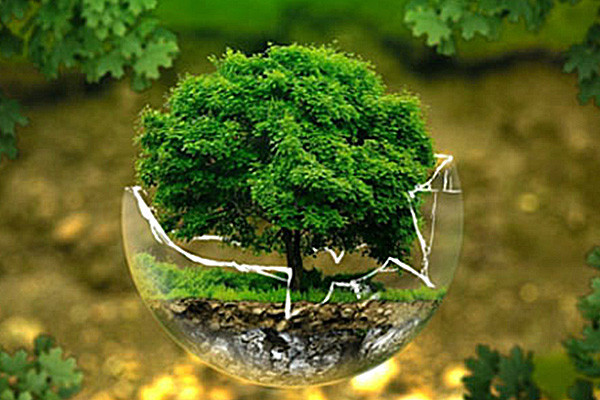
One of the primary threats that non-conformal coatings address is moisture ingress. Moisture can cause corrosion, short circuits, and electrical leakage in electronic circuits, leading to malfunctions or complete failure. Non-conformal coatings create a barrier that prevents moisture from reaching the delicate electronic components, thereby enhancing the device’s reliability and longevity, particularly in humid or wet environments.
Moreover, these coatings offer resistance against chemical contaminants such as solvents, fuels, acids, and alkalis. Electronic devices deployed in industrial settings, automotive applications, or outdoor environments are often exposed to chemicals that can degrade their performance and reliability. Non-conformal coatings provide a protective shield, preventing these chemicals from interacting with the electronic circuitry and compromising functionality.
Additionally, non-conformal coatings offer thermal insulation properties, helping to dissipate heat generated by electronic components. Excessive heat can degrade the performance of electronic devices and reduce their operational lifespan. By providing thermal insulation, non-conformal coatings help maintain optimal operating temperatures, ensuring reliable performance even in demanding conditions.
Furthermore, these coatings can provide mechanical protection against physical damage such as abrasion, vibration, and shock. Electronic devices may encounter mechanical stress during handling, transportation, or operation, leading to component failure if unprotected. Non-conformal coatings form a durable barrier that absorbs mechanical shocks and vibrations, reducing the risk of damage to the electronic components.
Non-conformal coatings are effective in combating a wide range of environmental hazards, including moisture ingress, chemical contamination, thermal stress, and mechanical damage. By providing a protective barrier, they enhance the reliability, durability, and performance of electronic devices, making them indispensable in various industries and applications.
How Does Conformal Coating Enhance Electrical Insulation?
Conformal coating is a protective layer applied to electronic circuitry to enhance electrical insulation properties. This coating, typically made from silicone, acrylic, or polyurethane, serves several vital functions that contribute to improved insulation.
First, conformal coating creates a physical barrier over the circuitry, effectively sealing it from external environmental factors such as moisture, dust, chemicals, and temperature variations. By preventing these elements from coming into direct contact with the electronic components, the risk of electrical short circuits or corrosion is significantly reduced. Moisture, in particular, can cause conductivity between adjacent conductive traces or components, leading to malfunctions or failures. Conformal coating acts as a barrier against moisture ingress, thereby enhancing insulation.
Moreover, conformal coatings often exhibit high dielectric strength, meaning they can withstand high voltages without conducting electricity. This property is crucial for maintaining insulation integrity, mainly when circuits operate at elevated voltages. By providing an additional insulation layer, conformal coatings help prevent electrical leakage and breakdown, ensuring the reliability and safety of the electronic device.
Furthermore, conformal coatings offer excellent adhesion to various substrate materials commonly used in electronic assemblies, such as printed circuit boards (PCBs). This strong bond ensures uniform coverage and prevents the formation of voids or gaps where electrical discharge could occur. Additionally, the flexibility of many conformal coating materials allows them to conform to the contours of complex circuitry, covering delicate components and ensuring comprehensive insulation.
Conformal coating enhances electrical insulation by:
- Creating a protective barrier against environmental contaminants.
- Providing high dielectric strength to withstand voltage stresses.
- Ensuring strong adhesion and uniform coverage for adequate insulation.
- Conforming to the shape of circuitry, including delicate components.
Overall, applying conformal coating is a critical step in the manufacturing process of electronic devices, contributing significantly to their reliability, longevity, and performance in various operating environments.
Can Non-Conformal Coatings Provide Electrical Insulation?
Non-conformal coatings can provide electrical insulation, although their effectiveness may vary depending on the specific application and requirements. Non-conformal coatings refer to coatings that do not conform precisely to the shape of the substrate or the components to which they are applied. These coatings are typically used for various purposes, including moisture protection, corrosion resistance, and electrical insulation.
Non-conformal coatings can be applied in various forms, such as spray, dip, or brush coatings. They are often used in situations where conformal coatings, which conform closely to the contours of the substrate, may not be suitable or necessary.
Regarding electrical insulation, non-conformal coatings can effectively provide insulation between electrical components or traces on a circuit board. However, their effectiveness may depend on factors such as the thickness of the layer, the material composition, and the application’s specific requirements.
It’s essential to ensure that the non-conformal coating is applied uniformly and thoroughly to provide adequate insulation and protect against electrical shorts or breakdowns. Additionally, proper selection of the coating material and thorough testing are crucial to verify its electrical insulation properties in the intended application environment.
What Industries Commonly Use Conformal Coatings?
Conformal coatings are thin protective films applied to electronic components and circuit boards to safeguard them from environmental factors such as moisture, dust, chemicals, and temperature fluctuations. Industries that rely heavily on electronic devices and circuits often utilize conformal coatings to enhance the reliability and longevity of their products.
- Electronics Manufacturing: Conformal coatings are extensively used in manufacturing, protecting printed circuit boards (PCBs), integrated circuits, and other sensitive electronic components. This includes consumer electronics such as smartphones, tablets, laptops, and televisions, as well as industrial electronics like control systems, sensors, and instrumentation.
- Automotive: The automotive industry employs conformal coatings to shield electronic components within vehicles from harsh conditions encountered on the road. These coatings protect electronic control units (ECUs), sensors, ignition systems, and other critical components from moisture, vibration, and temperature extremes, ensuring reliable performance and longevity.
- Aerospace and Defense: In aerospace and defense applications, conformal coatings safeguard electronic systems onboard aircraft, satellites, missiles, and military vehicles. These coatings protect sensitive electronics from the rigors of aerospace environments, including high-altitude exposure, extreme temperatures, and vibration, ensuring optimal performance and mission success.
- Medical Devices: Medical device manufacturers utilize conformal coatings to protect electronic components embedded in medical equipment, such as patient monitoring devices, diagnostic instruments, and implantable devices. These coatings help maintain the integrity and reliability of electronic systems used in critical healthcare applications.
- Telecommunications: Conformal coatings are essential in telecommunications equipment to protect networking devices, antennas, and communication systems from environmental hazards such as moisture, dust, and corrosion. This ensures uninterrupted connectivity and reliable operation of telecommunications infrastructure.
- Industrial Automation: Industries relying on automation technologies, such as manufacturing, oil and gas, and utilities, utilize conformal coatings to protect electronic control systems, PLCs (programmable logic controllers), and sensors from harsh industrial environments. These coatings enhance the durability and reliability of automation equipment, minimizing downtime and maintenance costs.
- Renewable Energy: Conformal coatings are crucial in renewable energy systems, including solar panels, wind turbines, and energy storage systems. By protecting electronic components within these systems from outdoor elements such as UV radiation, moisture, and temperature fluctuations, conformal coatings contribute to the efficiency and longevity of renewable energy infrastructure.
Industries spanning electronics manufacturing, automotive, aerospace, defense, medical devices, telecommunications, industrial automation, and renewable energy rely on conformal coatings to protect electronic components and ensure the reliability and longevity of their products and systems.
In Which Applications are Non Conformal Coatings Preferred?
Non Conformal coatings, which do not adhere uniformly to the surface they are applied to, find utility in various applications where selective protection or specific performance characteristics are required. Here’s an overview of some critical applications where non conformal coatings are preferred:
- Electronics: Non Conformal coatings are extensively used in electronics, particularly in areas where selective protection is needed. For instance, in printed circuit boards (PCBs), components like connectors, switches, and exposed metal contacts may require protection from environmental factors such as moisture, dust, or chemical exposure. Non Conformal coatings like silicone-based are applied precisely to these vulnerable areas to provide targeted protection while allowing other parts of the PCB to remain uncoated for accessibility or heat dissipation.
- Medical Devices: Non Conformal coatings are employed for implantable devices and sensors in the medical field. These coatings may need to cover specific areas of the device while exposing others to interaction with bodily tissues or fluids. Additionally, non-conformal coatings can be tailored to provide properties like biocompatibility or antimicrobial protection, further enhancing their suitability for medical applications.
- Aerospace and Automotive: Components in aerospace and automotive industries often require protection against harsh environmental conditions such as extreme temperatures, humidity, and chemical exposure. Non Conformal coatings offer targeted protection to critical areas like electrical connections, sensors, and exposed metal surfaces without adding unnecessary bulk or interfering with mechanical tolerances.
- Optoelectronics: In optoelectronic devices like LEDs and photovoltaic cells, nonconformal coatings enhance performance by providing tailored optical properties such as anti-reflection, light diffusion, or wavelength selectivity. These coatings are applied selectively to specific regions of the device to achieve desired optical effects while maintaining functionality.
- Military and Defense: Non Conformal coatings play a vital role in military and defense applications where equipment needs to withstand extreme conditions, including moisture, salt spray, and rugged terrain. Coatings with specific properties such as camouflage, infrared reflectance, or radar absorption can be applied selectively to military equipment for tactical advantages while preserving functionality.
Non Conformal coatings offer versatility and customization in various applications where selective protection, tailored properties, or precise performance characteristics are essential. Their ability to provide targeted solutions while minimizing unnecessary coverage makes them valuable in electronics and healthcare.
What Challenges are Associated with Applying Conformal Coatings?
Conformal coatings are widely used in various industries to protect electronic components from environmental factors such as moisture, dust, chemicals, and temperature extremes. While they offer significant benefits, applying conformal coatings comes with its own set of challenges.
- Surface Preparation: One of the critical challenges is ensuring proper surface preparation before applying the conformal coating. Any contaminants, such as oil, dust, or residues, can interfere with the coating’s adhesion and performance. Cleaning and degreasing the surface thoroughly are essential but can be time-consuming and labor-intensive.
- Uniform Application: Achieving uniformity in coating thickness is vital for consistent protection across all assembly parts. Irregularities in coating thickness can lead to areas of vulnerability where the component may be exposed to environmental hazards. Achieving this uniformity manually can be challenging, especially on complex geometries or densely populated circuit boards.
- Masking and Selective Coating: Many assemblies require selective coating, where certain areas must be masked to prevent coating application. Proper masking is crucial to avoid unintended coverage, leading to functionality issues or interfering with subsequent assembly processes. Achieving precise masking without affecting neighboring components or areas can be technically demanding.
- Curing Process: Conformal coatings typically require curing to achieve their intended properties, such as adhesion, hardness, and chemical resistance. Ensuring the proper curing conditions, such as temperature, humidity, and duration, is crucial. Inadequate curing can result in incomplete polymerization, reduced protection, or even coating failure.
- Compatibility and Material Selection: Selecting the appropriate conformal coating material is critical to ensure compatibility with the coated components and the environmental conditions to which they will be exposed. Factors such as thermal expansion coefficients, flexibility, and chemical resistance must be considered. Choosing the wrong material can lead to issues such as cracking, delamination, or inadequate protection.
- Quality Control and Inspection: Maintaining consistent quality throughout the coating process requires robust quality control measures. Inspection for defects such as bubbles, voids, or uneven coverage is essential to identify potential issues early and prevent costly rework or failures in the field.
Addressing these challenges requires careful planning, proper equipment, trained personnel, and adherence to best practices in conformal coating application. Despite the complexities involved, overcoming these challenges is essential to ensuring the reliability and longevity of electronic assemblies in harsh environments.
Are There Any Limitations to Using Non-Conformal Coatings?
Non-conformal coatings typically applied to electronic components, circuits, and assemblies, offer protection against environmental factors such as moisture, dust, chemicals, and mechanical stress. However, despite their advantages, they also come with certain limitations that need to be considered:
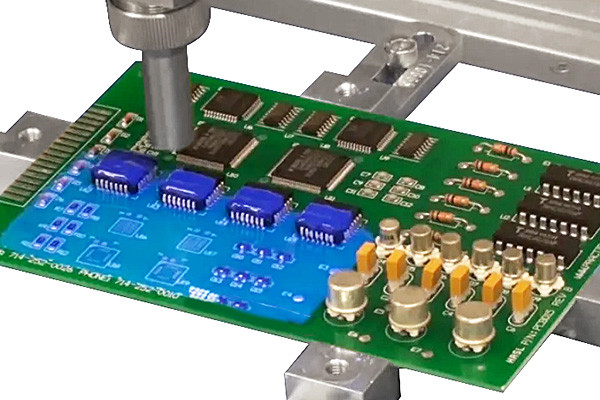
- Limited Coverage: Non-conformal coatings may only partially cover intricate or densely populated circuit board areas. Components with complex geometries, tight spaces, or areas with high component density might not receive adequate coating, leaving them vulnerable to environmental damage.
- Uniformity Issues: Achieving uniform coating thickness can be challenging, especially on assemblies with varying surface geometries. Inconsistencies in coating thickness may lead to uneven protection, potentially leaving some areas more susceptible to damage than others.
- Accessibility Concerns: Coatings can hinder accessibility to components for troubleshooting, repair, or rework. In scenarios where frequent maintenance or modifications are necessary, non-conformal coatings may pose significant obstacles, increasing the time and effort required for servicing.
- Thermal Management: Some non-conformal coatings may have poor thermal conductivity, leading to heat buildup and potentially affecting the performance and reliability of sensitive electronic components, particularly in high-temperature environments.
- Compatibility Issues: Certain coatings may not be compatible with all materials or components. Compatibility issues could arise with specific substrates, solder masks, or conformal coatings already applied, leading to adhesion problems or chemical reactions that compromise the assembly’s integrity.
- Repairability: Repairing assemblies coated with non-conformal coatings can be challenging. Removing and reapplying the coating often requires specialized equipment and expertise. Additionally, the process can increase the risk of damaging sensitive components or disrupting nearby circuitry.
- Cost Considerations: Non-conformal coatings may be more expensive than other protective measures. The cost of materials, equipment, and application processes, coupled with the potential need for rework or repair, should be factored into the overall cost of the manufacturing or maintenance process.
While non-conformal coatings offer valuable protection for electronic assemblies, they have limitations. Designers and engineers must carefully evaluate these limitations and consider alternative protective measures based on their applications’ specific requirements and constraints.
How Do Conformal Coatings Impact Assembly and Repair Processes?
Conformal coatings protect electronic components from environmental factors such as moisture, dust, chemicals, and temperature fluctuations. However, they also have significant implications for assembly and repair processes.
Conformal coatings can both aid and complicate assembly. Initially, they provide a protective barrier, safeguarding delicate components from damage caused by handling, soldering, or mechanical stress. This protection ensures that components remain functional and reliable throughout the assembly process. Additionally, conformal coatings can enhance solder joint reliability by reducing the risk of solder bridging or short circuits.
However, conformal coatings can also pose challenges during assembly. Their presence requires careful consideration of application methods to ensure uniform coverage without excess material buildup, which could interfere with component functionality or lead to quality issues. Selecting the appropriate coating material and application technique is crucial to prevent problems such as incomplete coverage, uneven thickness, or contamination of sensitive areas.
Furthermore, conformal coatings complicate repair processes. While they protect components during operation, they can hinder accessibility during troubleshooting or repair tasks. Technicians may need to remove or reapply the coating, which adds time and complexity to the repair process. Additionally, improper removal techniques or damage to the coating can compromise its protective properties, leaving components vulnerable to environmental hazards.
Choosing a suitable conformal coating material is essential to mitigate these challenges. Chemical compatibility, temperature resistance, and ease of rework must be carefully evaluated to ensure optimal performance in assembly and repair scenarios. Additionally, advancements in coating technologies, such as UV-curable coatings or peelable masks, offer alternative solutions to address specific assembly and repair requirements.
Conformal coatings significantly impact assembly and repair processes in electronics manufacturing. While they provide essential protection for components, they also introduce complexities that require careful consideration and strategic planning to optimize efficiency and reliability throughout the product lifecycle.
What Factors Should Be Considered When Selecting a Conformal Coating?
Selecting the suitable conformal coating for electronic components involves considering several critical factors to ensure optimal protection and performance. These factors include:
- Environmental Conditions:Assess the operating environment where the coated components will be deployed. Factors such as temperature extremes, humidity, exposure to chemicals, salt spray, and UV radiation can significantly impact the choice of conformal coating.
- Substrate Compatibility:Ensure compatibility between the conformal coating material and the substrate material. Substrates such as printed circuit boards (PCBs), metals, plastics, and ceramics may require specific coating formulations to ensure adhesion and long-term reliability.
- Application Method:Consider the application method, whether dip coating, spray coating, brush coating, or selective coating. Each technique may require a different type of coating formulation for optimal coverage and performance.
- Thickness Requirements:Determine the desired thickness of the conformal coating layer based on the level of protection needed and the space constraints within the electronic assembly. Some applications may require a thin, lightweight coating, while others require a thicker layer for enhanced protection.
- Electrical Properties:Evaluate the electrical properties of the conformal coating, such as dielectric strength, surface resistance, and impedance, to ensure compatibility with the electronic components and circuitry. The coating should not interfere with electrical signals or introduce unwanted capacitance or leakage.
- Chemical Resistance:Consider the resistance of the coating to various chemicals, including solvents, fuels, oils, and cleaning agents, especially if the electronic assembly will be exposed to harsh industrial or automotive environments.
- Thermal Stability:Assess the conformal coating’s thermal stability and heat dissipation properties, mainly if the components will operate in high-temperature environments or undergo thermal cycling.
- Curing Method:Determine whether the coating requires heat curing, UV curing, or room-temperature curing, and consider the feasibility and compatibility of the curing process with the manufacturing environment and production schedule.
- Regulatory Compliance:Ensure that the chosen conformal coating complies with relevant industry standards and regulations, such as RoHS (Restriction of Hazardous Substances) and REACH (Registration, Evaluation, Authorization, and Restriction of Chemicals), mainly if the electronic assembly will be used in consumer products or other regulated markets.
By carefully considering these factors, manufacturers can select the most suitable conformal coating to protect their electronic components effectively and ensure reliable performance in diverse operating conditions.
What Considerations are Important When Choosing a Non-Conformal Coating?
Choosing a suitable non-conformal coating for electronic components is crucial to ensure the reliability and longevity of the devices, particularly in harsh environments. Several key considerations must be taken into account:
- Environmental Conditions: Understand the conditions the coated electronics will be exposed to, such as temperature extremes, humidity, chemicals, and mechanical stress. The coating must provide adequate protection against these factors to prevent corrosion, moisture ingress, and other forms of damage.
- Substrate Compatibility: Ensure compatibility between the coating material and the substrate material. The coating should adhere well to the substrate without causing any adverse reactions or compromising the performance of the electronics.
- Application Method: Consider the application method, whether spraying, dipping, brushing, or selective coating. The chosen coating should suit the selected application method to ensure uniform coverage and proper protection of all components.
- Thickness and Coverage: Determine the desired thickness and coverage of the coating based on the level of protection required and the size of the components. Thicker coatings may offer better protection but can also affect thermal management and electrical properties.
- Dielectric Properties: Evaluate the dielectric properties of the coating, mainly if it will be applied to sensitive electronic components. The coating should have high dielectric strength to prevent electrical leakage and short circuits.
- Chemical Resistance: Assess the resistance of the coating to chemicals, including solvents, oils, and cleaning agents. A coating with good chemical resistance will provide long-term protection against exposure to various substances.
- Thermal Properties: Consider the coating’s thermal conductivity and heat dissipation characteristics, mainly if it will be applied to components generating significant heat. The coating should not impede thermal transfer or contribute to overheating.
- UV Stability: If the coated electronics are exposed to sunlight or other ultraviolet (UV) radiation sources, choose a coating with UV stability to prevent degradation and yellowing over time.
- Repairability and Rework: Evaluate the coating’s ease of repair and rework in case modifications or repairs are needed after application. Some coatings may require specialized processes for rework, while others can be easily removed and reapplied.
By carefully considering these factors, you can select a non-conformal coating that provides optimal protection for your electronic components in their intended operating environment.
How does the Cost Factor affect the decision between conformal and non conformal coatings?
Cost is critical in determining whether to use conformal or non conformal coatings in various applications. Conformal coatings, typically thin layers applied directly onto electronic circuitry, offer protection against environmental factors such as moisture, dust, and chemicals. Conversely, non conformal coatings are thicker and provide a more robust barrier against these elements.
When considering cost, several factors come into play:
- Material Cost: Conformal coatings are generally more expensive per unit volume than non conformal coatings due to their specialized formulations tailored for thin, uniform applications. Non Conformal coatings, often applied in thicker layers, may use less expensive materials in larger quantities.
- Application Process: Conformal coatings often require precise application techniques such as spraying, dipping, or brushing to achieve uniform coverage. This can involve specialized equipment and skilled labor, adding to the overall cost. Non Conformal coatings, while also requiring proper application, may be less demanding in terms of precision and equipment.
- Labor Cost: The labor required for applying conformal coatings tends to be higher due to the meticulous nature of the process. Skilled technicians are needed to ensure uniform coverage without causing damage to delicate electronic components. Non Conformal coatings may be applied more quickly and with less precision, potentially reducing labor costs.
- Maintenance and Repair: Conformal coatings, mainly when applied thinly, may require more frequent inspection and maintenance to ensure continued effectiveness. Repairs or re-application may be necessary if the coating becomes damaged or wears off over time. Non Conformal coatings, with their thicker layers, offer excellent durability and longevity, reducing the need for frequent maintenance.
- Performance Requirements: The specific performance requirements of the application will also influence the cost considerations. Conformal coatings may be necessary for applications where precise coverage and protection of individual components are paramount, even if they come at a higher cost. Non Conformal coatings may be suitable for less demanding environments where cost-effectiveness is prioritized over precision.
While conformal coatings may offer superior protection in specific applications, they have higher material, labor, and maintenance costs than non conformal coatings. The decision between the two depends on the application’s particular needs, balancing performance requirements and budget constraints.
What Future Trends Are Emerging in the Field of Conformal and Non-Conformal Coatings?
In conformal and non-conformal coatings, several emerging trends are reshaping the landscape, driven by technological advancements, environmental concerns, and evolving industry needs.
- Eco-Friendly Formulations: With increasing environmental regulations and consumer demand for sustainable products, there’s a growing emphasis on developing conformal and non-conformal coatings with eco-friendly formulations. This includes reducing or eliminating volatile organic compounds (VOCs) and hazardous materials, opting for water-based or UV-curable coatings, and exploring bio-based alternatives.
- Nano-coatings and Thin Film Technologies: Nanotechnology enables the development of ultra-thin conformal coatings with superior protective properties. These coatings offer enhanced barrier functions, corrosion resistance, and insulation capabilities while maintaining a minimal footprint. Thin film deposition techniques such as atomic layer deposition (ALD) and chemical vapor deposition (CVD) are increasingly used to control coating thickness and uniformity precisely.
- Functional Coatings for Emerging Applications: As electronic devices become more compact and complex, there’s a growing demand for conformal coatings with tailored functionalities. These include coatings with enhanced thermal management properties, self-healing capabilities, anti-fogging properties, and even conductive coatings for flexible electronics and wearable devices.
- Advanced Application Techniques: Innovations in application techniques are improving the efficiency and effectiveness of coating processes. This includes the development of robotics and automated systems for precise and uniform coating deposition, as well as advancements in spray coating, dip coating, and selective coating methods to accommodate various substrate geometries and materials.
- Innovative Coatings and IoT Integration: With the rise of the Internet of Things (IoT), there’s a trend towards integrating innovative functionalities into conformal and non-conformal coatings. These coatings can offer sensing capabilities for monitoring environmental conditions, corrosion levels, and structural integrity in real time, enabling proactive maintenance and extending the lifespan of coated components.
- Adaptive and Self-Healing Coatings: Future coatings may incorporate adaptive and self-healing properties, where the coating can autonomously repair minor damages or adapt to changing environmental conditions. This could significantly reduce maintenance requirements and enhance the durability of coated surfaces, particularly in harsh or dynamic operating environments.
the future of conformal and non-conformal coatings is characterized by a convergence of advanced materials, intelligent technologies, and sustainable practices, catering to the evolving needs of industries ranging from electronics manufacturing to automotive and aerospace.
Conclusion:
In summary, while conformal coatings conform precisely to the contours of electronic assemblies, providing uniform protection against environmental hazards, non-conformal coatings offer versatility in protecting components with irregular shapes or sizes. The choice between conformal and non-conformal coatings depends on factors such as application requirements, environmental conditions, and cost considerations, highlighting the importance of understanding their differences and selecting the most suitable solution for each electronic assembly.
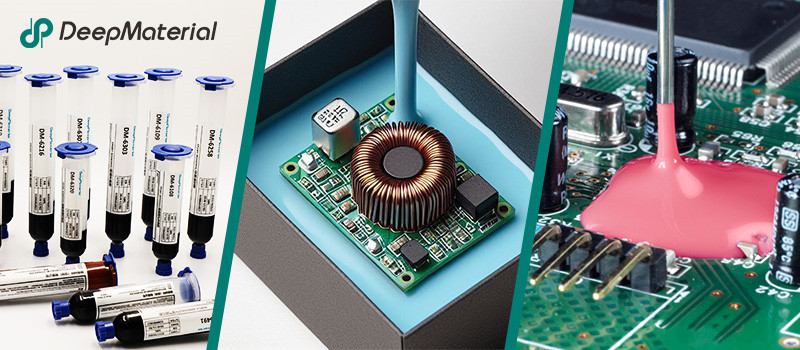
About DeepMaterial
DeepMaterial is a trusted supplier of encapsulant materials that are used in electronics manufacturing worldwide. From chip on board encapsulants such as glob top material to conformal coatings, underfills, low pressure molding, and potting solutions, DeepMaterial offers a full range of circuit board protection materials that effectively protect circuit boards while help reduce costs. More…Deepmaterial is a the manufacturer of epoxy adhesives including hardeners, metalbond, and metal filled resins. Structural, toughened medium viscosity, and non-sag adhesives are also offered. Some adhesives are resistant to thermal shock, chemical, vibration dampening, and impact. Suitable for metals, plastics, wood, and ceramics. Serves electronics, aerospace, automotive, tooling, marine, and construction industries. REACH and RoHS compliant. FDA approved. UL listed. Meets military specifications. We are the one of best adhesive manufacturers in China.
Blogs & News
Potting compounds are at the frontline of electronics assembly, delivering effective protection in challenging environmental conditions while improving mechanical strength and offering high electric insulation. Used within a variety of industries, electrical potting compounds are found within a broad range of consumer electronics, as well as used in applications across the automotive, aerospace, and other industries where electronic assemblies are prevalent.
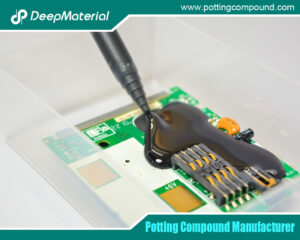
The Potting and Encapsulating Compounds Market: An In-Depth Exploration of Trends, Innovations, and Future Prospects
The Potting and Encapsulating Compounds Market: An In-Depth Exploration of Trends, Innovations, and Future Prospects In the rapidly evolving technology landscape, the potting and
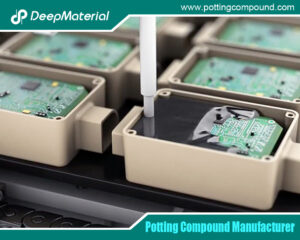
The Comprehensive Guide to Polyurethane Potting Compound Manufacturers
The Comprehensive Guide to Polyurethane Potting Compound Manufacturers In today’s rapidly advancing technological landscape, the protection and reliability of electronic components have become paramount.
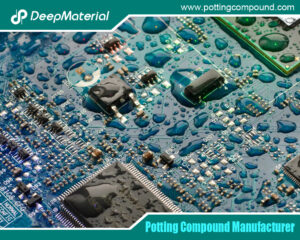
The Comprehensive Guide to Epoxy Potting Compound Manufacturers
The Comprehensive Guide to Epoxy Potting Compound Manufacturers Epoxy potting compounds are essential materials in the electronics industry, providing robust protection for sensitive components against
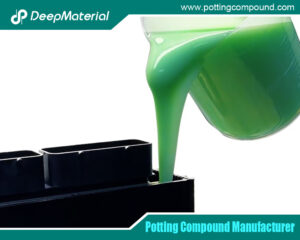
The Essential Guide to Potting Materials for Electronics
The Essential Guide to Potting Materials for Electronics In the rapidly evolving field of electronics, ensuring device reliability and longevity is critical. One of the
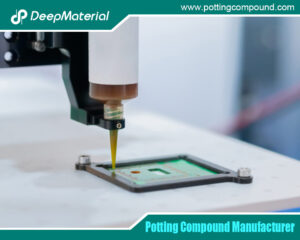
The Expanding Horizon of the Mini Silicone Optical Glue Market
The Expanding Horizon of the Mini Silicone Optical Glue Market The mini silicone optical glue market is witnessing unprecedented growth, fueled by technological advancements and
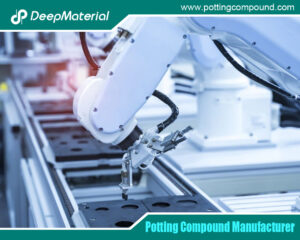
The Comprehensive Guide to PCB Potting Services: Ensuring Reliability in Electronics
The Comprehensive Guide to PCB Potting Services: Ensuring Reliability in Electronics Printed Circuit Boards (PCBs) are the backbone of modern electronics, enabling functionality in