Exploring the Best Potting Compounds for Your Needs
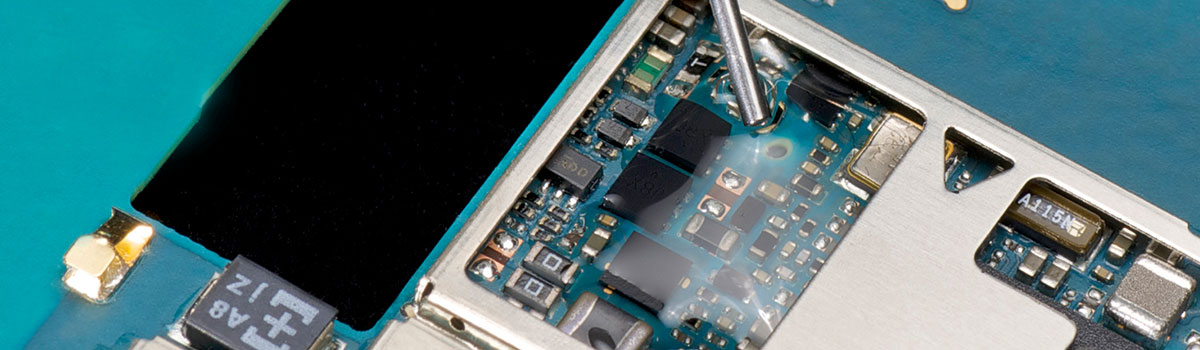
Potting compounds are essential in various industries, offering protection and insulation for electronic components, circuits, and devices. With many options available, selecting a suitable potting compound can be daunting. This category aims to demystify the world of potting compounds by addressing common questions and providing insights into the best application options.
Table of Contents
ToggleNecessary information for your knowledge:
What are potting compounds, and how do they work?
Potting compounds are materials used in electronics and electrical applications to encapsulate or protect components, such as circuit boards, wires, and electronic assemblies. They are typically liquid or semi-liquid polymers that cure or harden into a solid form after application. Potting compounds serve several essential functions:
- Protection from Environmental Factors: Potting compounds shield electronic components from environmental factors such as moisture, dust, chemicals, and vibration. This protection is crucial for ensuring the longevity and reliability of electronic devices, particularly in harsh operating conditions.
- Electrical Insulation: Many potting compounds possess excellent electrical insulation properties, preventing electrical shorts and maintaining the integrity of the circuitry. This insulation is vital for safeguarding sensitive electronic components from damage or malfunction.
- Mechanical Support: Potting compounds provide structural support to delicate components, reducing the risk of mechanical stress or damage due to handling, temperature fluctuations, or mechanical shocks. They help maintain components’ alignment and positioning within the electronic assembly.
- Thermal Management: Some potting compounds offer thermal conductivity properties, aiding in heat dissipation generated by electronic components during operation. Effective thermal management helps prevent overheating and ensures optimal performance and reliability.
Potting compounds work through a process called encapsulation or potting. The liquid or semi-liquid potting compound is poured or dispensed over the electronic components or assemblies during encapsulation. Once applied, the compound undergoes a curing process, transforming from liquid to solid. This curing can be achieved through various methods, such as heat, UV light, or chemical reactions initiated by catalysts or hardeners present in the compound.
As the potting compound cures, it forms a protective and insulating layer around the components, effectively encapsulating them within a durable enclosure. The cured compound adheres to the surfaces, creating a tight seal that prevents moisture and other contaminants from infiltrating the electronic assembly.
Overall, potting compounds play a crucial role in enhancing electronic devices’ reliability, longevity, and performance by providing robust protection, insulation, mechanical support, and thermal management for sensitive components.
Why is choosing the suitable potting compound important for electronic applications?
Choosing the suitable potting compound for electronic applications is crucial for several key reasons:
- Environmental Protection: Electronic devices often operate in diverse and challenging environments exposed to moisture, chemicals, dust, and other contaminants. The proper potting compound is a barrier, shielding sensitive components from these elements. Failure to select an appropriate compound can lead to corrosion, short circuits, and other forms of damage, compromising the reliability and lifespan of the electronics.
- Electrical Insulation: Insulation is essential for preventing electrical shorts and ensuring the proper functioning of electronic circuits. The suitable potting compound should have high dielectric strength and resistivity to effectively insulate the components. Using an unsuitable compound with poor insulation properties can result in electrical leakage, voltage breakdown, and potential safety hazards.
- Mechanical Stability: Electronic assemblies may experience mechanical stress from vibration, shock, and thermal expansion. A suitable potting compound should provide robust mechanical support, maintaining the integrity and alignment of the components within the enclosure. Failure to choose a compound with adequate mechanical properties can lead to physical damage, component displacement, or solder joint failures, impacting the device’s performance and longevity.
- Thermal Management: Efficient thermal management is critical for dissipating heat generated by electronic components during operation. Potting compounds with good thermal conductivity help to transfer heat away from the components, preventing overheating and thermal damage. Selecting an inappropriate compound with low thermal conductivity can result in heat buildup, reduced performance, and premature electronics failure.
- Compatibility: It’s essential to consider the compatibility of the potting compound with the materials used in the electronic assembly, including substrates, coatings, adhesives, and connectors. Incompatible materials can lead to adhesion issues, chemical reactions, or dimensional changes, compromising the effectiveness of the potting and potentially causing damage to the components.
Choosing a suitable potting compound is paramount for ensuring electronic devices’ reliability, performance, and longevity. Failure to select an appropriate compound tailored to the application’s specific requirements can lead to a myriad of issues, ranging from environmental damage and electrical failures to mechanical instability and thermal problems. Therefore, thoroughly considering ecological conditions, electrical properties, mechanical stability, thermal management, and material compatibility is essential in the selection process.
What are the fundamental properties to consider when selecting a potting compound?
Selecting a suitable potting compound is crucial for ensuring the longevity and performance of electronic components, particularly in harsh environments. Several vital properties should be considered:
- Chemical Resistance: Potting compounds should resist the chemicals in their operating environment to prevent corrosion or degradation. This includes resistance to oils, solvents, acids, and bases.
- Temperature Resistance: The compound should maintain its properties across a wide temperature range, ensuring stability even in extreme conditions. High-temperature resistance prevents melting or degradation, while low-temperature resistance prevents brittleness or cracking.
- Electrical Insulation: Potting compounds should effectively insulate electronic components, protecting them from electrical short circuits and ensuring reliable performance. They should have high dielectric strength and resistivity.
- Mechanical Strength: The compound should provide robust mechanical support to the components, protecting them from physical damage due to shock, vibration, or mechanical stress. This involves flexural strength, impact resistance, and adhesion to substrates.
- Water and Moisture Resistance: Potting compounds should effectively seal out moisture to prevent corrosion and short circuits. They should have low water absorption and good hydrolytic stability.
- UV Resistance: If the application involves exposure to sunlight or ultraviolet (UV) radiation, UV resistance is crucial to prevent degradation and maintain the integrity of the potting material over time.
- Thermal Conductivity: In some applications, efficient heat dissipation is essential for maintaining the performance and reliability of electronic components. Potting compounds with high thermal conductivity facilitate heat transfer away from the components.
- Curing Time and Process: Consideration should be given to the curing time and process of the potting compound, ensuring compatibility with production timelines and methods.
- Cost and Availability: Balancing performance requirements with cost considerations is essential. Additionally, ensuring the availability of the chosen potting compound for future production needs is critical for long-term reliability.
By carefully evaluating these fundamental properties, engineers can select a potting compound that meets the specific requirements of their application, ensuring optimal performance and longevity of electronic components.
How does temperature resistance factor into choosing a potting compound?
Temperature resistance is critical when selecting a potting compound for electronic components or devices. Potting compounds encapsulate and protect sensitive electronics from environmental factors such as moisture, vibration, and temperature fluctuations. Temperature resistance refers to the ability of the compound to maintain its physical and electrical properties under varying temperature conditions. Here’s how it factors into the selection process:
- Operating Temperature Range: One of the primary considerations is the range of temperatures the electronic device will be exposed to during operation. The potting compound must withstand these temperatures without degrading or losing effectiveness. For example, in automotive or industrial applications, where components may experience extreme temperatures, a potting compound with a wide operating temperature range, such as -40°C to 150°C or higher, would be necessary.
- Thermal Conductivity: Temperature resistance also relates to the compound’s ability to dissipate heat generated by the electronic components. High operating temperatures can lead to overheating, which may degrade performance or cause failure. Potting compounds with good thermal conductivity help transfer heat from sensitive components, thereby maintaining optimal operating temperatures and extending the device’s lifespan.
- Thermal Cycling Stability: Electronic devices often experience temperature cycling through repeated heating and cooling cycles during operation or environmental exposure. The potting compound should withstand these thermal cycles without cracking, delaminating, or undergoing significant dimensional changes, which could compromise the integrity of the encapsulation and expose the components to potential damage.
- Chemical Stability: High temperatures can accelerate chemical reactions within the potting compound or between the compound and surrounding materials. A temperature-resistant potting compound should exhibit good chemical stability, resisting degradation or reactions that could compromise its effectiveness or damage the encapsulated electronics.
- Application-specific Requirements: Different applications may have specific temperature requirements based on industry standards or regulatory compliance. For example, aerospace or military applications may demand potting compounds capable of withstanding extremely low temperatures encountered at high altitudes or in space.
Temperature resistance is a critical factor in choosing a potting compound as it ensures electronic devices’ reliability, longevity, and performance, particularly in environments with extreme temperature conditions. By selecting a potting compound with the appropriate temperature resistance characteristics, manufacturers can ensure the durability and functionality of their products in diverse operating environments.
Are there specific potting compounds designed for outdoor applications?
Yes, specific potting compounds are designed for outdoor applications and engineered to withstand the various challenges posed by outdoor environments. These compounds are formulated to protect against factors such as moisture, temperature fluctuations, UV radiation, and mechanical stresses daily in outdoor settings.
One key consideration for outdoor potting compounds is their ability to resist moisture ingress. If not adequately protected, outdoor environments often expose electronic components to rain, snow, and humidity, possibly leading to corrosion and electrical malfunctions. Therefore, outdoor potting compounds typically have excellent water resistance properties, forming a durable barrier preventing moisture from reaching sensitive components.
Additionally, exposure to sunlight can degrade unprotected materials through UV radiation. Outdoor potting compounds often incorporate UV stabilizers to mitigate the damaging effects of sunlight, prolonging the lifespan of the encapsulated components and maintaining their performance over time.
Temperature fluctuations are another significant challenge in outdoor environments, particularly in regions with extreme climates. Potting compounds for outdoor applications are designed to maintain their mechanical and electrical properties over a wide temperature range, ensuring reliable performance in both hot summers and cold winters.
Mechanical robustness is also essential for outdoor potting compounds, as electronic devices may be subjected to vibration, shock, or impact during transportation, installation, or operation. These compounds are formulated to provide excellent adhesion to various substrates, effectively immobilizing components and preventing displacement or damage.
Furthermore, outdoor potting compounds may need to comply with specific environmental protection and safety regulatory standards. Manufacturers often ensure that their products meet relevant industry certifications and guidelines, such as RoHS (Restriction of Hazardous Substances) and REACH (Registration, Evaluation, Authorization, and Restriction of Chemicals), to guarantee compliance and suitability for outdoor applications.
Outdoor potting compounds are specially formulated to provide robust protection against moisture, UV radiation, temperature fluctuations, and mechanical stresses, ensuring electronic components’ long-term reliability and performance in outdoor environments.
Can potting compounds withstand exposure to chemicals or solvents?
Potting compounds are specially formulated materials that encapsulate electronic components, protecting them from environmental factors such as moisture, dust, vibration, and temperature extremes. Their ability to withstand exposure to chemicals or solvents depends on various factors, including the type of potting compound, the specific chemicals or solvents involved, and the application conditions.
Several types of potting compounds are available, each with its own set of properties and intended applications. The most commonly used types are epoxy resins, polyurethanes, silicones, and acrylics. Each of these materials has different chemical resistance properties.
Epoxy resins, for example, are generally resistant to a wide range of chemicals and solvents, including fuels, oils, and many acids and bases. Polyurethane potting compounds also resist many chemicals but may degrade when exposed to certain solvents like ketones or strong acids. Silicones are known for their excellent resistance to moisture and extreme temperatures, but their chemical resistance can vary depending on the specific formulation.
When selecting a potting compound for an application where exposure to chemicals or solvents is a concern, compatibility testing is essential. This involves exposing samples of the potting compound to the specific chemicals or solvents it will encounter in its intended environment and assessing any changes in properties such as hardness, flexibility, or appearance.
Additionally, proper application techniques, such as thorough mixing and adequate curing time, can enhance the chemical resistance of potting compounds. In some cases, additional protective measures, such as barrier coatings or secondary encapsulation, may be necessary to further shield electronic components from harmful chemicals.
Overall, while many potting compounds offer some level of resistance to chemicals and solvents, carefully considering the application requirements and compatibility testing is essential to ensure optimal performance and protection of electronic devices in challenging environments.
What role does flexibility play in potting compound selection?
Flexibility is a critical factor in potting compound selection, as it directly impacts the performance and durability of encapsulated electronic components in various applications. The level of flexibility required depends on factors such as the mechanical stresses the component will encounter, thermal cycling, and the potential for vibration or impact.
One of the primary functions of potting compounds is to provide structural support and protection to delicate electronic components. In applications where components are subject to mechanical stresses or vibrations, a flexible potting compound can help absorb and distribute these forces, reducing the risk of damage or failure. For example, in automotive electronics or aerospace applications, where components may experience significant vibrations or thermal cycling, flexible potting compounds are often preferred to minimize the risk of fatigue or cracking.
Flexibility also plays a crucial role in accommodating thermal expansion and contraction of encapsulated components due to temperature variations. In environments with wide temperature ranges, such as outdoor electronics or industrial settings, rigid potting compounds may become brittle and prone to cracking, compromising the integrity of the encapsulation. Flexible potting compounds can better withstand thermal cycling, maintaining a secure seal around the components and preventing moisture ingress or other environmental contaminants from compromising performance.
Moreover, flexibility can influence the ease of installing and maintaining encapsulated electronics. Flexible potting compounds are typically easier to work with during potting, allowing for better flow and penetration around complex shapes or irregularities in the components. This can result in more uniform encapsulation and improved protection against environmental factors.
However, it’s essential to balance flexibility and other properties such as hardness and chemical resistance. While flexible potting compounds offer excellent impact resistance and thermal cycling capabilities, they may have limitations in chemical resistance or dimensional stability compared to more rigid formulations. Therefore, the application’s specific requirements must be carefully considered when selecting a potting compound to ensure optimal performance and reliability over the product’s lifespan.
Are there environmentally friendly options available in potting compounds?
Yes, potting compounds have environmentally friendly options, reflecting a growing trend toward sustainability and eco-conscious manufacturing practices. These options aim to minimize the environmental impact of electronics production and disposal by using less harmful materials throughout their lifecycle.
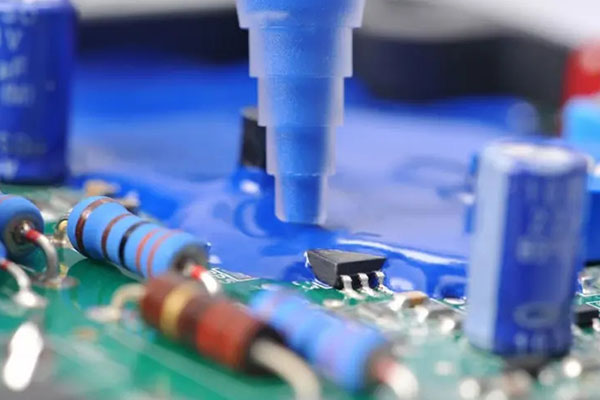
One approach to achieving environmentally friendly potting compounds is to utilize bio-based or renewable materials in their formulation. These materials are derived from natural sources such as plants, vegetable oils, or starches, offering a more sustainable alternative to traditional petroleum-based compounds. Bio-based potting compounds can help reduce reliance on finite fossil fuel resources and decrease greenhouse gas emissions associated with their production.
Additionally, some environmentally friendly potting compounds prioritize biodegradability or compostability at the end of their lifecycle. These compounds are designed to break down into non-toxic byproducts under specific environmental conditions, reducing the accumulation of electronic waste in landfills and promoting circular economy principles. Biodegradable potting compounds can be particularly beneficial in applications where end-of-life disposal is a concern, such as disposable electronics or products with short lifespans.
Furthermore, manufacturers are increasingly focusing on reducing the environmental footprint of potting compound production processes. This includes optimizing manufacturing methods to minimize energy consumption, waste generation, and emissions of harmful substances. Companies may also implement recycling initiatives to reclaim and reuse materials from production waste or end-of-life products, reducing resource consumption and environmental impact.
It’s worth noting that while environmentally friendly potting compounds offer several benefits in terms of sustainability, they must still meet performance requirements and compatibility with application-specific needs. Therefore, carefully considering mechanical properties, chemical resistance, and thermal stability is necessary when selecting environmentally friendly potting compounds to ensure they meet the desired performance standards while minimizing environmental impact. Overall, the availability of environmentally friendly options in potting compounds reflects a broader commitment within the electronics industry to embrace sustainable practices and reduce its ecological footprint.
How do I determine the appropriate cure time for a potting compound?
Determining the appropriate cure time for a potting compound involves considering various factors, including the type of compound, application requirements, environmental conditions, and desired properties of the cured material. Here’s a step-by-step guide to help you determine the optimal cure time:
- Refer to Manufacturer Guidelines: Start by consulting the manufacturer’s technical data sheet or guidelines for the potting compound. Manufacturers typically provide recommended cure times based on the specific formulation of the compound. This serves as a good starting point for your evaluation.
- Evaluate Application Requirements: Consider the specific requirements of your application. Factors such as the size and complexity of the potted components desired mechanical properties (e.g., hardness, flexibility) and environmental conditions (e.g., temperature, humidity) can influence the required cure time.
- Perform Test Samples: Conduct small-scale test samples to evaluate different cure times. Prepare samples using the potting compound and cure them for varying durations, ranging from shorter to more extended than the manufacturer recommends.
- Monitor Cure Progress: Throughout the curing process, monitor the samples for changes in properties such as viscosity, tackiness, and hardness. Visual inspection and tactile assessment can provide valuable insights into curing progress.
- Perform Mechanical Testing: Mechanical testing on the samples will be performed to assess their performance once cured. This may include hardness, adhesion, flexibility, and thermal stability tests. Compare the results with cure times to determine which timeframe yields the desired properties.
- Consider Environmental Factors: Consider the environmental conditions in which the potting compound will be used. For example, if the application involves exposure to high temperatures, longer cure times may be necessary to ensure adequate thermal stability.
- Optimize Cure Time: Based on the results of your evaluation, optimize the cure time to achieve the desired balance of properties for your specific application. This may involve selecting a sufficient-strength and durable cure while minimizing production time and costs.
- Document and Validate: Document the chosen cure time and validate it through further testing and validation procedures to ensure consistency and reliability in production.
By following these steps and conducting thorough testing and evaluation, you can determine the appropriate cure time for a potting compound that meets your application’s requirements.
What are the differences between epoxy, silicone, and urethane potting compounds?
Epoxy, silicone, and urethane potting compounds are materials used to encapsulate and protect electronic components, typically in harsh environments or to provide mechanical support. Each type has distinct properties, advantages, and disadvantages.
Epoxy Potting Compounds:
- Epoxy resins are versatile and widely used for potting applications due to their excellent adhesion, chemical resistance, and mechanical properties.
- They offer high strength and stiffness, making them suitable for applications where structural integrity is crucial.
- Epoxy potting compounds protect against moisture, chemicals, and thermal cycling.
- However, epoxies can be brittle and may experience thermal expansion mismatches with some components, leading to potential cracking under extreme temperature variations.
- They typically cure through an exothermic reaction, requiring careful control of curing conditions.
Silicone Potting Compounds:
- Silicone potting compounds offer exceptional flexibility, thermal stability, and electrical insulation properties.
- They have a wide operating temperature range and maintain their properties over various temperatures.
- Silicone materials are highly resistant to moisture, UV radiation, and chemicals, making them suitable for outdoor and marine applications.
- Their flexibility relieves stress, making them ideal for encapsulating delicate components or those subject to mechanical shock.
- However, silicones generally have lower mechanical strength than epoxies and urethanes, which may limit their use in high-stress applications.
Urethane Potting Compounds:
- Urethane potting compounds offer a balance between flexibility and mechanical strength.
- They have good adhesion to various substrates and provide excellent protection against moisture and chemicals.
- Urethanes can absorb mechanical shocks and vibrations, making them suitable for rugged applications.
- They exhibit lower shrinkage during curing compared to epoxies, reducing the risk of internal stresses in encapsulated components.
- However, urethanes may be susceptible to hydrolysis in humid environments and degrade when exposed to UV radiation.
The choice between epoxy, silicone, and urethane potting compounds depends on the application’s specific requirements, including factors such as mechanical strength, flexibility, chemical resistance, temperature range, and environmental conditions. Each type offers distinct advantages and limitations, and selecting the appropriate material is crucial to ensuring encapsulated electronic devices’ optimal performance and reliability.
Are there potting compounds suitable for high-voltage applications?
Yes, potting compounds specifically designed for high-voltage applications require excellent electrical insulation properties to prevent electrical breakdown and ensure safety and reliability. These compounds are engineered to withstand high electric field strengths without compromising their dielectric strength or integrity. Here are some key characteristics and considerations for potting compounds suitable for high-voltage applications:
- Dielectric Strength: Potting compounds for high-voltage applications must exhibit high dielectric strength to withstand the electric field without breaking down. Dielectric strength is typically measured in volts per mil (V/mil) or kilovolts per millimeter (kV/mm), indicating the maximum electric field a material can withstand without electrical breakdown.
- Insulation Resistance: High-voltage potting compounds should have excellent insulation resistance to minimize leakage currents and prevent electrical leakage paths between conductive elements. Insulation resistance is crucial for maintaining electrical isolation and avoiding short circuits.
- Thermal Stability: Thermal stability is essential in high-voltage environments to ensure that the potting compound maintains its electrical and mechanical properties over a wide temperature range. Stable thermal performance prevents degradation or breakdown of the material under elevated temperatures, which may occur during operation or due to external factors.
- Chemical Resistance: Potting compounds in high-voltage applications should also resist chemicals, moisture, and environmental factors that could degrade the material and compromise its electrical insulation properties over time.
- Compatibility: Compatibility with the encapsulated components and substrates is essential to ensure proper adhesion, minimal stress concentrations, and long-term reliability. Potting compounds should be formulated to adhere well to various materials commonly used in high-voltage applications, such as metals, ceramics, and plastics.
- Regulatory Compliance: Potting compounds intended for high-voltage applications may need to meet specific regulatory standards and certifications, such as UL (Underwriters Laboratories) or IEC (International Electrotechnical Commission), to ensure safety and performance requirements compliance.
High-voltage potting compounds are critical in protecting electronic components and assemblies from electrical hazards in applications such as power supplies, transformers, high-voltage cables, and electrical insulation systems. Proper selection and testing of potting materials are essential to ensure high-voltage equipment’s safety, reliability, and long-term performance.
What considerations should be made for potting compounds in high-moisture environments?
Potting compounds protect electronic components and devices from environmental factors such as moisture, temperature fluctuations, vibration, and mechanical shock. In high-moisture environments, the selection and application of potting compounds become even more critical to ensure the longevity and reliability of the encapsulated electronics. Here are several considerations that should be made for potting compounds in such environments:
- Water Resistance: The primary concern in high-moisture environments is water ingress. Potting compounds should have excellent water resistance properties to prevent moisture from penetrating and damaging sensitive electronics. Silicone-based compounds are often preferred for their hydrophobic nature and superior water resistance.
- Adhesion: Proper adhesion to the substrate and components is essential to create a reliable seal against moisture ingress. To effectively encapsulate the electronics, the potting compound should adhere well to various surfaces, including metals, plastics, and circuit boards.
- Chemical Compatibility: The potting compound should be compatible with the materials it comes into contact with, including the electronic components and the enclosure. It should resist degradation when exposed to chemicals commonly found in high-moisture environments, such as saltwater or industrial solvents.
- Thermal Stability: High-moisture environments often accompany temperature variations. The potting compound should maintain its properties and integrity over a wide temperature range to ensure long-term protection of the encapsulated electronics.
- Flexibility: Flexibility is crucial to accommodate thermal expansion and contraction of the encapsulated components. A flexible potting compound can help reduce stress on the electronic assembly, minimizing the risk of cracking or delamination in high-moisture environments.
- Curing Method: The curing method of the potting compound should be compatible with the manufacturing process and environmental conditions. Some compounds cure at room temperature, while others require elevated temperatures or UV light.
- Testing and Certification: Potting compounds in high-moisture environments should undergo rigorous testing to verify their performance and reliability under simulated conditions. Certification from relevant regulatory bodies may also be necessary to ensure industry standards and regulations compliance.
By carefully considering these factors and selecting the appropriate potting compound, manufacturers can protect electronic components and devices in high-moisture environments, ensuring their durability and reliability in challenging conditions.
How do I ensure proper adhesion of the potting compound to substrates?
Proper adhesion of potting compounds to substrates is crucial for creating durable and practical encapsulations, particularly in electronic and electrical applications. Here are several vital steps to achieve this:
- Surface Preparation:Proper surface preparation is essential for good adhesion. Ensure the substrate surface is clean, dry, and free from previous processes’ contaminants, such as dust, oils, greases, and residues. Use appropriate cleaning methods such as solvent wiping, degreasing, or abrasive cleaning to achieve a clean surface.
- Surface Activation:Some substrates may require surface activation to enhance adhesion. Techniques such as plasma treatment, corona treatment, or chemical priming can modify the surface chemistry and increase surface energy, promoting better wetting and adhesion of the potting compound.
- Adhesion Promoters:Utilize adhesion promoters or primers to enhance the bonding between the substrate and the potting compound. These materials are applied to the substrate surface before potting compound application and facilitate adhesion by creating a solid interfacial bond.
- Proper Mixing and Application:Ensure adequate mixing of the potting compound according to the manufacturer’s instructions. Only complete or proper mixing can lead to insufficient curing and good adhesion. Apply the potting compound evenly and consistently onto the substrate surface, avoiding air entrapment and ensuring complete coverage.
- Curing Conditions:Follow the recommended conditions specified by the potting compound manufacturer. Proper curing is essential for achieving optimal adhesion strength. Maintain appropriate temperature, humidity, and curing time to fully allow the potting compound to cross-link and bond to the substrate.
- Compatibility Testing:Conduct compatibility testing to ensure that the potting compound is suitable for the specific substrate material and environmental conditions it will be exposed to. Compatibility issues can arise due to differences in thermal expansion coefficients, chemical resistance, or surface properties.
- Quality Control:Implement robust quality control measures to assess adhesion strength through adhesion testing methods such as pull-off, peel, or shear tests. Regularly monitor and evaluate adhesion performance to identify any potential issues and make necessary adjustments in the process.
By following these steps diligently, you can ensure proper adhesion of the potting compound to substrates, resulting in reliable and long-lasting encapsulations for your electronic and electrical components.
Are there flame-retardant potting compounds available?
Yes, flame-retardant potting compounds are readily available and widely used in various industries where fire safety is a concern, such as electronics, aerospace, automotive, and construction. These compounds are specifically formulated to minimize the risk of fire propagation and provide protection to enclosed components.
One common type of flame-retardant potting compound is epoxy resin. Epoxy resins are versatile materials known for their excellent adhesion, chemical resistance, and thermal stability. To make them flame-retardant, manufacturers incorporate additives such as phosphorus-based compounds, halogen-containing compounds, or mineral fillers like alumina trihydrate. These additives work by interrupting the combustion process or forming a protective char layer when exposed to heat and flames, thereby slowing down or preventing the spread of fire.
Polyurethane potting compounds are another option for flame-retardant encapsulation. Similar to epoxy resins, polyurethane formulations can be modified with flame-retardant additives to enhance their fire resistance. These additives may include phosphorus-based flame retardants, reactive flame retardants, or intumescent agents that swell when exposed to heat, forming a barrier against flames and heat transfer.
Silicone-based potting compounds also offer flame-retardant properties. Silicones are inherently resistant to high temperatures and do not readily support combustion. However, manufacturers may enhance their flame resistance by incorporating additives such as aluminum hydroxide, magnesium hydroxide, or silicone resins with flame-retardant properties.
When selecting a flame-retardant potting compound, it’s essential to consider the specific requirements of the application, including environmental conditions, thermal management needs, and regulatory compliance. Additionally, compatibility with the components being encapsulated and ease of processing are important factors to evaluate.
Overall, flame-retardant potting compounds play a crucial role in enhancing the safety and reliability of electronic and electrical systems by minimizing the risk of fire hazards and protecting sensitive components from heat and environmental factors.
What are the best practices for mixing and applying potting compounds?
Mixing and applying potting compounds effectively is crucial for ensuring the reliability and durability of electronic components. Here are some best practices:
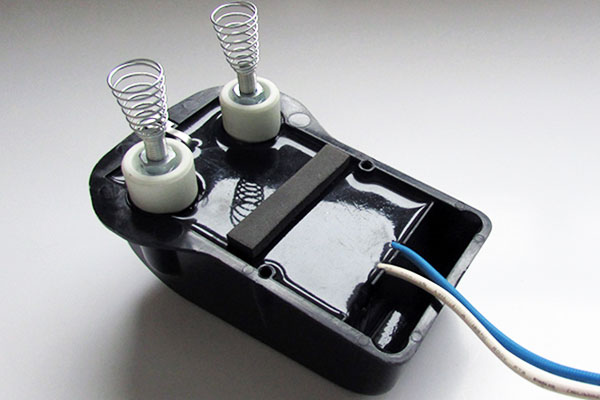
- Selecting the Right Compound: Choose a potting compound suitable for the intended application, considering factors like temperature resistance, chemical resistance, flexibility, and electrical properties.
- Preparation: Clean the surfaces to be potted thoroughly to remove any contaminants affecting adhesion. Ensure that the components are dry before potting.
- Mixing Ratio: Follow the manufacturer’s instructions precisely regarding the mixing ratio of the potting compound components. Use calibrated measuring tools to ensure accuracy.
- Mixing Procedure: Mix the potting compound components thoroughly but gently to avoid introducing air bubbles. Use a low-speed mixer or hand stirring, depending on the manufacturer’s recommendations.
- Degassing: After mixing, degas the potting compound mixture to remove trapped air bubbles. Vacuum degassing is a standard method used to ensure the integrity of the potting.
- Application Method: Choose the appropriate method for applying the potting compound, such as dipping, pouring, or dispensing. Consider factors like the size and shape of the component and the desired coverage.
- Curing Conditions: Follow the manufacturer’s recommended curing conditions, including temperature and humidity requirements. Ensure proper ventilation to aid in curing and prevent the buildup of potentially harmful fumes.
- Potting Enclosure: Use suitable potting enclosures or molds to contain the compound during curing. Ensure that the enclosure material is compatible with the potting compound and can withstand the curing conditions.
- Quality Control: Implement quality control measures throughout the potting process to detect issues early on. Inspect the potted components for uniform coverage, adhesion, and absence of defects.
- Documentation: Keep detailed records of the potting process, including the batch number of the potting compound, mixing and curing parameters, and any observations or deviations encountered during the process. This documentation is valuable for traceability and troubleshooting.
By following these best practices, you can ensure the adequate mixing and application of potting compounds, resulting in reliable and durable electronic components.
Can potting compounds be reworked or removed if needed?
Potting compounds are commonly used in electronics and electrical applications to protect components from environmental factors such as moisture, vibration, and thermal stress. While these compounds offer excellent protection, their permanence can be a concern when rework or removal is necessary.
The reworkability of potting compounds largely depends on the type of compound used and the specific application. Some potting compounds are designed to be reworkable, allowing for easier removal or modification of the encapsulated components. These compounds typically have lower adhesion properties or are formulated to be softened or dissolved by specific solvents or heat.
Thermoplastic potting compounds, for instance, can be softened by applying heat, allowing for the extraction of components without damaging them. This method is often used in applications where components may need to be replaced or upgraded periodically.
On the other hand, thermoset potting compounds, once cured, become rigid and chemically inert, making them difficult to rework. In such cases, removal typically involves mechanical methods such as scraping, cutting, or milling, which can be time-consuming and may risk damaging the encapsulated components.
In situations where reworkability is critical, engineers may opt for encapsulation methods that offer easier removal, such as using encapsulation materials with lower curing temperatures or incorporating features like access points or removable covers to facilitate future maintenance.
However, it’s important to note that reworkability often comes with trade-offs in terms of the overall protection provided by the potting compound. Compounds designed for easy removal may offer less robust protection against environmental factors than those formulated for maximum durability.
Ultimately, the choice of potting compound and encapsulation method depends on the application’s specific requirements, balancing factors such as protection, reworkability, and ease of maintenance. Collaboration between engineers, material scientists, and manufacturers is crucial in selecting the most appropriate solution for each use case.
Are there specialized potting compounds for sensitive electronic components?
Yes, there are specialized potting compounds designed specifically for sensitive electronic components. These compounds are formulated to protect against environmental factors such as moisture, dust, chemicals, and mechanical stress while offering electrical insulation and thermal conductivity when necessary. Here are some key points about these specialized potting compounds:
- Low Electrical Conductivity: Potting compounds for sensitive electronic components typically have low electrical conductivity to prevent short circuits and interference. They form a barrier between components and external elements, reducing the risk of electrical damage.
- Thermal Conductivity: In some applications, such as high-power electronics or components prone to overheating, thermal conductivity is essential for dissipating heat efficiently. Specialized potting compounds may incorporate materials like ceramics or fillers to enhance thermal conductivity while providing protection.
- Chemical Resistance: Sensitive electronic components may be exposed to various chemicals in their operating environments. Potting compounds with chemical resistance protect the components from corrosion and degradation caused by exposure to acids, bases, solvents, and other chemicals.
- Flexibility vs. Rigidity: Depending on the application, potting compounds can range from flexible to rigid. Flexible compounds are suitable for applications where mechanical stress or vibrations are a concern, as they can absorb shock and prevent damage to delicate components. Rigid compounds offer enhanced structural support and protection against physical impact.
- Optical Clarity: Potting compounds with optical clarity are preferred in specific applications where visual inspection or transmission of light is necessary, such as optical sensors or LED modules. These compounds maintain transparency over time, ensuring the performance of optical components is not compromised.
- UL Certification: Many potting compounds undergo testing and certification by organizations like Underwriters Laboratories (UL) to ensure they meet industry standards for safety and performance. UL-certified potting compounds provide reassurance of quality and reliability in sensitive electronic applications.
- Application Method: Specialized potting compounds are available in various forms, including liquid, gel, and paste. The choice of application method depends on factors such as the component’s complexity, the desired encapsulation level, and the manufacturing process.
Specialized potting compounds play a crucial role in safeguarding sensitive electronic components, ensuring their reliability and longevity in demanding environments.
How do cost and performance trade-offs influence potting compound selection?
Selecting the suitable potting compound involves a delicate balance between cost and performance, with several factors influencing the decision-making process. Potting compounds are:
- Materials that encapsulate electronic components or assemblies.
- Protecting against environmental factors such as moisture.
- Thermal stress.
Here’s how cost and performance trade-offs impact potting compound selection:
- Material Cost: The initial cost of the potting compound is a significant consideration. Some compounds may be more expensive upfront due to their superior performance characteristics or specialized properties. However, higher material costs can impact the overall project budget, especially for large-scale manufacturing.
- Performance Requirements: The intended application dictates the performance criteria for the potting compound. Factors such as thermal conductivity, electrical insulation, chemical resistance, and mechanical strength are crucial. Higher-performing compounds often come with a higher price tag, but they may be necessary for demanding environments or critical applications where reliability is paramount.
- Processing Costs: The ease of application and curing process also affect the overall cost. Compounds that require specialized equipment or longer curing times may increase labor costs and production time. Conversely, compounds with more straightforward application methods and faster curing times can reduce processing costs and improve efficiency.
- Long-Term Reliability: While cheaper compounds may offer short-term cost savings, they might not provide the required durability and longevity. Investing in a higher-quality, more expensive potting compound can pay off in the long run by reducing the risk of premature failure, warranty claims, and costly repairs or replacements.
- Environmental Considerations: Some applications require potting compounds with specific environmental certifications or compliance with regulations such as RoHS (Restriction of Hazardous Substances). Meeting these requirements may add to the cost, but they are necessary for ensuring compatibility and avoiding legal or regulatory issues.
Selecting a potting compound involves evaluating various cost and performance trade-offs to balance meeting application requirements and budget constraints. It’s essential to consider the upfront material cost and factors such as long-term reliability, processing costs, and environmental considerations to make an informed decision.
What common challenges are encountered when using potting compounds, and how can they be mitigated?
Potting compounds, commonly used in electronics and electrical applications, protect against environmental factors such as moisture, dust, and vibration. However, they also come with their own set of challenges:
- Air Entrapment: During the potting process, air bubbles can get trapped within the compound, leading to voids and reduced effectiveness of the potting material. Proper mixing techniques and vacuum degassing can be employed to remove air bubbles before potting to mitigate this.
- Curing Issues: Inadequate curing can result in incomplete polymerization or uneven curing throughout the material, reducing mechanical strength and durability. Ensuring proper conditions, such as temperature and humidity control, and using compatible curing agents can help mitigate this issue.
- Adhesion Problems: Poor adhesion between the potting compound and substrate can lead to delamination and compromised protection. Surface preparation techniques such as cleaning, roughening, and using adhesion promoters can enhance bonding between the compound and substrate.
- Thermal Expansion Mismatch: Differences in thermal expansion coefficients between the potting compound and the encapsulated components can induce mechanical stress and potentially lead to cracking or failure over time, especially in applications subject to temperature cycling. Selecting potting materials with thermal properties closely matched to those of the components can minimize this issue.
- Chemical Compatibility: Exposure to certain chemicals or solvents in the operating environment can degrade the potting compound, compromising its protective properties. Conducting compatibility tests with potential contaminants and selecting chemically resistant potting materials can help address this concern.
- Cost and Process Complexity: Some high-performance potting compounds can be costly, and the potting process itself may require specialized equipment and expertise, increasing production costs and complexity. Balancing performance requirements with cost considerations and optimizing the potting process for efficiency can help manage these challenges.
Overall, addressing these challenges requires careful selection of potting materials, thorough process optimization, and adherence to best practices to ensure the reliability and effectiveness of the encapsulation.
Are there industry standards or certifications for choosing a potting compound?
When selecting a potting compound, several industry standards and certifications can guide your decision-making process, ensuring that the compound meets certain quality, safety, and performance benchmarks. Here are some key considerations:
- UL Recognition: Underwriters Laboratories (UL) is a globally recognized safety certification organization. UL certification ensures that the potting compound has undergone rigorous testing for safety and performance. Look for UL recognition marks on the product, indicating compliance with specific standards relevant to potting compounds.
- IPC Standards: The Institute for Printed Circuits (IPC) sets electronics manufacturing and assembly processes standards. IPC standards for potting compounds address thermal conductivity, dielectric properties, and adhesion strength. Ensuring compliance with relevant IPC standards can help guarantee the potting compound’s suitability for electronic applications.
- RoHS Compliance: The Restriction of Hazardous Substances (RoHS) directive restricts using certain hazardous materials in electrical and electronic equipment. Choosing a potting compound that is RoHS compliant ensures that it does not contain restricted substances such as lead, mercury, cadmium, and certain flame retardants, thus promoting environmental sustainability and safety.
- ISO Certifications: ISO standards provide quality management systems and product specifications guidelines. ISO 9001 certification indicates that the manufacturer has implemented a robust quality management system, while certifications such as ISO 14001 demonstrate commitment to environmental management. These certifications can enhance confidence in the quality and reliability of the potting compound.
- Military Specifications (MIL-STD): For applications requiring high reliability and durability, compliance with military specifications such as MIL-STD-810 for environmental testing or MIL-STD-883 for microelectronic devices may be essential. These standards define rigorous testing procedures and performance requirements for materials used in military and aerospace applications.
Considering these industry standards and certifications, you can ensure that the potting compound meets the necessary criteria for your specific application, whether it’s electronics manufacturing, aerospace, automotive, or other industries requiring reliable encapsulation and protection of components. Consulting with industry experts and suppliers can provide valuable insights into selecting the most appropriate potting compound for your needs.
Conclusion:
Selecting the best potting compound involves considering various factors such as application requirements, environmental conditions, and material properties. By exploring these questions and understanding the diverse options available, you can make informed decisions to ensure the optimal protection and performance of your electronic assemblies and devices. Whether it’s for industrial, automotive, aerospace, or consumer electronics, the suitable potting compound can significantly enhance the reliability and longevity of your products.
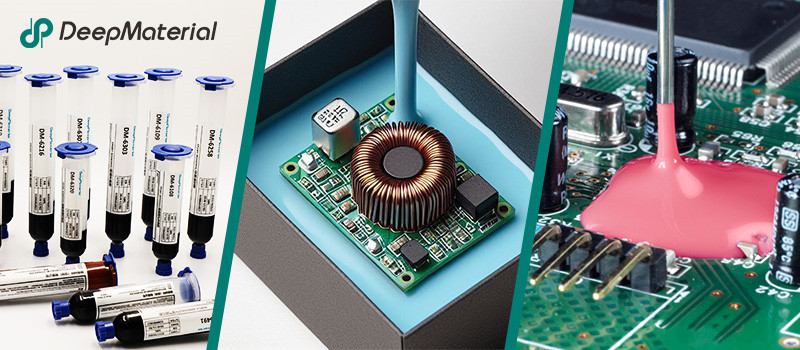
About DeepMaterial
DeepMaterial is a trusted supplier of encapsulant materials that are used in electronics manufacturing worldwide. From chip on board encapsulants such as glob top material to conformal coatings, underfills, low pressure molding, and potting solutions, DeepMaterial offers a full range of circuit board protection materials that effectively protect circuit boards while help reduce costs. More…Deepmaterial is a the manufacturer of epoxy adhesives including hardeners, metalbond, and metal filled resins. Structural, toughened medium viscosity, and non-sag adhesives are also offered. Some adhesives are resistant to thermal shock, chemical, vibration dampening, and impact. Suitable for metals, plastics, wood, and ceramics. Serves electronics, aerospace, automotive, tooling, marine, and construction industries. REACH and RoHS compliant. FDA approved. UL listed. Meets military specifications. We are the one of best adhesive manufacturers in China.
Blogs & News
Potting compounds are at the frontline of electronics assembly, delivering effective protection in challenging environmental conditions while improving mechanical strength and offering high electric insulation. Used within a variety of industries, electrical potting compounds are found within a broad range of consumer electronics, as well as used in applications across the automotive, aerospace, and other industries where electronic assemblies are prevalent.
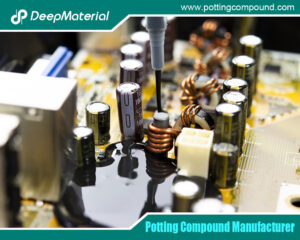
Potting Compound for PCB
Potting Compound for PCB A potting compound is a liquid or semi-liquid material that is poured or injected over a PCB or electronic assembly, then
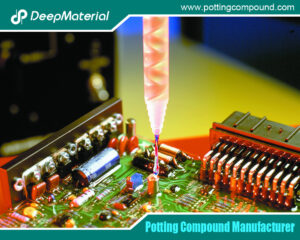
In – depth Analysis of the Curing Characteristics of Electronic Potting Compounds
In – depth Analysis of the Curing Characteristics of Electronic Potting Compounds Electronic potting compounds play a vital role in the electronics industry. They can
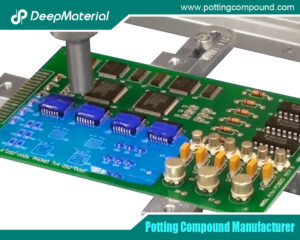
A Comprehensive Analysis of the Environmental Performance of Encapsulating Materials: From Regulations to Practices
A Comprehensive Analysis of the Environmental Performance of Encapsulating Materials: From Regulations to Practices In modern industrial manufacturing, encapsulating materials are widely used in numerous

A Comprehensive Analysis of PCB Encapsulation Quality Inspection: Innovative Application of Non-Destructive Testing Technologies
A Comprehensive Analysis of PCB Encapsulation Quality Inspection: Innovative Application of Non-Destructive Testing Technologies In the field of electronic manufacturing, the encapsulation process of printed
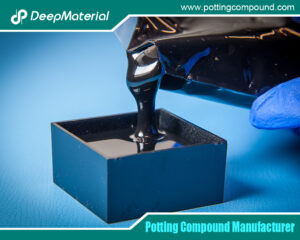
Analysis of the Improvement of the Seismic and Impact Resistance Performance of PCB by Encapsulation
Analysis of the Improvement of the Seismic and Impact Resistance Performance of PCB by Encapsulation During the operation of electronic devices, the PCB (Printed Circuit
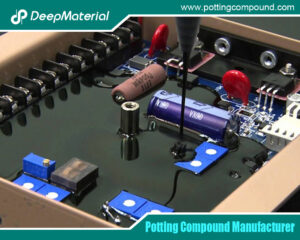
A Comprehensive Guide to Evaluating the Reliability of Encapsulation Materials for Encapsulated PCBs
A Comprehensive Guide to Evaluating the Reliability of Encapsulation Materials for Encapsulated PCBs In modern electronic devices, the printed circuit board (PCB) plays a central
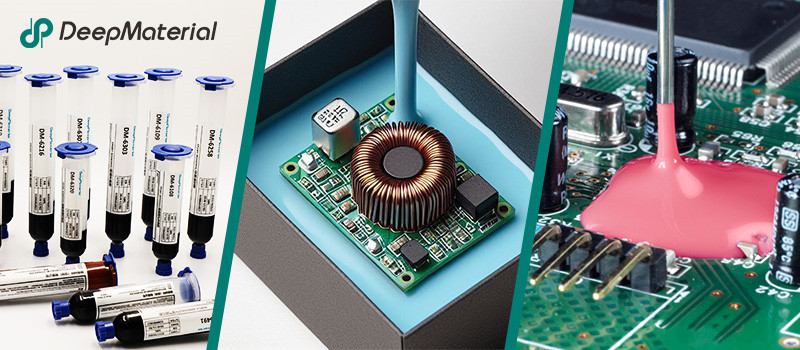
About DeepMaterial
DeepMaterial is a trusted supplier of encapsulant materials that are used in electronics manufacturing worldwide. From chip on board encapsulants such as glob top material to conformal coatings, underfills, low pressure molding, and potting solutions, DeepMaterial offers a full range of circuit board protection materials that effectively protect circuit boards while help reduce costs. More…Deepmaterial is a the manufacturer of epoxy adhesives including hardeners, metalbond, and metal filled resins. Structural, toughened medium viscosity, and non-sag adhesives are also offered. Some adhesives are resistant to thermal shock, chemical, vibration dampening, and impact. Suitable for metals, plastics, wood, and ceramics. Serves electronics, aerospace, automotive, tooling, marine, and construction industries. REACH and RoHS compliant. FDA approved. UL listed. Meets military specifications. We are the one of best adhesive manufacturers in China.
Blogs & News
Potting compounds are at the frontline of electronics assembly, delivering effective protection in challenging environmental conditions while improving mechanical strength and offering high electric insulation. Used within a variety of industries, electrical potting compounds are found within a broad range of consumer electronics, as well as used in applications across the automotive, aerospace, and other industries where electronic assemblies are prevalent.
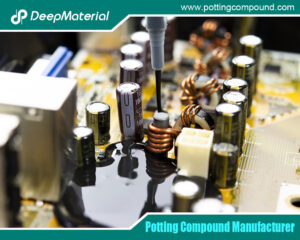
Potting Compound for PCB
Potting Compound for PCB A potting compound is a liquid or semi-liquid material that is poured or injected over a PCB or electronic assembly, then
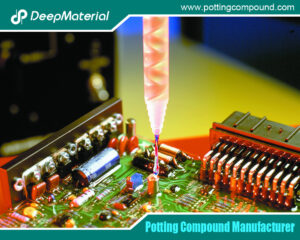
In – depth Analysis of the Curing Characteristics of Electronic Potting Compounds
In – depth Analysis of the Curing Characteristics of Electronic Potting Compounds Electronic potting compounds play a vital role in the electronics industry. They can
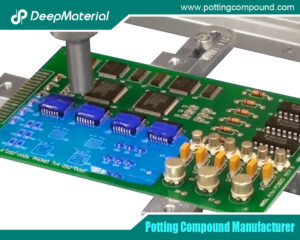
A Comprehensive Analysis of the Environmental Performance of Encapsulating Materials: From Regulations to Practices
A Comprehensive Analysis of the Environmental Performance of Encapsulating Materials: From Regulations to Practices In modern industrial manufacturing, encapsulating materials are widely used in numerous

A Comprehensive Analysis of PCB Encapsulation Quality Inspection: Innovative Application of Non-Destructive Testing Technologies
A Comprehensive Analysis of PCB Encapsulation Quality Inspection: Innovative Application of Non-Destructive Testing Technologies In the field of electronic manufacturing, the encapsulation process of printed
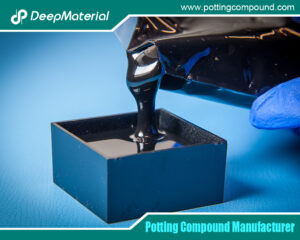
Analysis of the Improvement of the Seismic and Impact Resistance Performance of PCB by Encapsulation
Analysis of the Improvement of the Seismic and Impact Resistance Performance of PCB by Encapsulation During the operation of electronic devices, the PCB (Printed Circuit
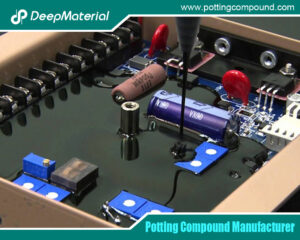
A Comprehensive Guide to Evaluating the Reliability of Encapsulation Materials for Encapsulated PCBs
A Comprehensive Guide to Evaluating the Reliability of Encapsulation Materials for Encapsulated PCBs In modern electronic devices, the printed circuit board (PCB) plays a central