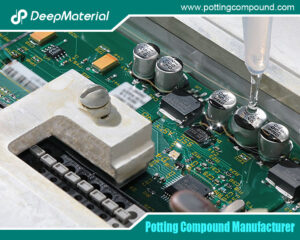
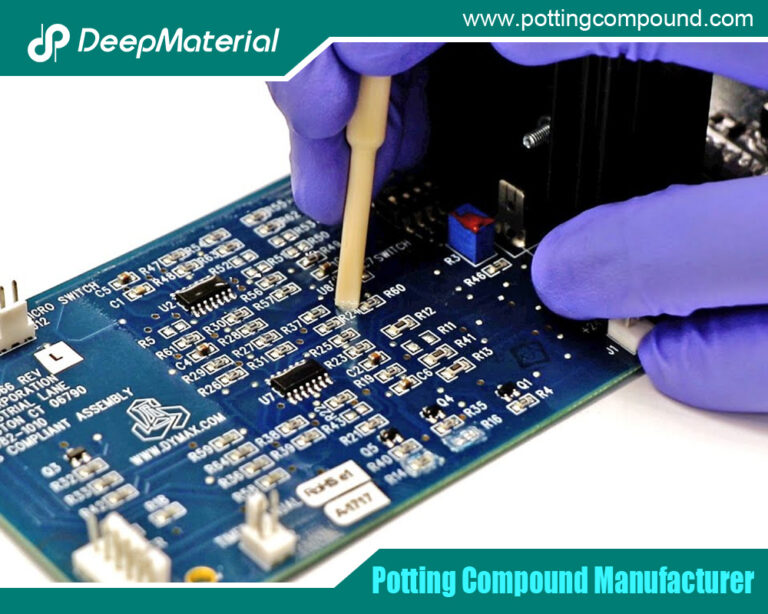
Exploring Potting Materials for Electronics: Enhancing Durability and Performance
- Electronic Potting Material Manufacturer
- June 24, 2024
- Automotive potting material manufacturers, Benefits of Potting Electronics, china electronic potting silicone manufacturer, china electronic potting silicone supplier, custom automated electronics potting, customize china electronic potting silicone manufacturer, customize china electronic potting silicone supplier, electrical potting compound, electronic epoxy encapsulant potting compounds, Electronic Potting and Encapsulation, Electronic Potting and Encapsulation Resins, electronic potting compound, Electronic Potting Compounds Manufacturer, electronic potting material, electronic potting silicone manufacturers china, epoxy potting compound, Epoxy potting material manufacturers, polyurethane potting compound, potting compound for electronics, potting compound for pcb, potting compound vs epoxy, potting material for electronic compounds, potting material for electronics, Potting Materials for Electronics, potting pcb, silicone potting compound for electronics, thermal potting compound, UV curing potting compound, waterproof potting compound
Exploring Potting Materials for Electronics: Enhancing Durability and Performance
Protection against environmental factors like moisture, dust, vibration, and temperature variations is paramount in electronics, where delicate components and circuitry thrive. Potting materials, also known as encapsulants or potting compounds, play a crucial role in safeguarding electronic assemblies from these external influences. This article delves into the world of potting materials, exploring their types, properties, and applications in ensuring the longevity and reliability of electronic devices.
Understanding Potting Materials:
Potting materials are substances used to encapsulate electronic components, forming a protective barrier that shields them from mechanical stresses and environmental hazards. These materials typically come in liquid form, allowing them to conform to the intricate shapes and contours of electronic assemblies before curing into a solid, protective layer. The choice of potting material depends on various factors, including the application requirements, operating conditions, and desired performance attributes.
Types of Potting Materials:
- Epoxy Resins: Epoxy-based potting compounds are among the most commonly used materials due to their excellent adhesion, chemical resistance, and thermal stability. They offer robust protection against moisture and mechanical impact, making them ideal for harsh environments. Epoxy resins come in various formulations, including rigid, flexible, and flame-retardant options, catering to different application needs.
- Silicone Elastomers: Silicone-based potting materials exhibit exceptional flexibility, thermal stability, and resistance to moisture and extreme temperatures. They maintain their properties over various operating conditions, making them suitable for outdoor and automotive applications where exposure to harsh weather conditions is prevalent. Silicone elastomers effectively cushion against mechanical shocks and vibrations, safeguarding sensitive electronic components.
- Polyurethane Resins: Polyurethane potting compounds balance flexibility and toughness, providing reliable protection against moisture, chemicals, and thermal cycling. They are commonly used in applications requiring a combination of ruggedness and environmental resistance, such as industrial control systems, automotive electronics, and outdoor LED lighting.
- Polyolefin Resins: Polyolefin-based potting materials offer good electrical insulation properties and chemical resistance, making them suitable for encapsulating high-voltage electronic components and power distribution systems. They provide a cost-effective solution for applications with critical dielectric strength and long-term reliability.
Properties and Considerations: When selecting a potting material for a specific application, several vital properties should be considered:
- Electrical Insulation: Potting materials should possess high dielectric strength to insulate sensitive electronic components from electrical hazards.
- Thermal Conductivity: Efficient heat dissipation is essential to prevent overheating and ensure the optimal performance of electronic devices.
- Adhesion: The potting material should adhere well to the substrate surface, forming a solid bond to prevent delamination or moisture ingress.
- Chemical Compatibility: Compatibility with other materials in the assembly and resistance to chemicals and solvents is crucial for long-term reliability.
- Mechanical Properties: Flexibility, toughness, and resistance to impact and vibration help protect electronic components from mechanical stresses.
Applications: Potting materials find applications across various industries and sectors, including:
- Automotive Electronics: Protecting control modules, sensors, and wiring harnesses from moisture, vibration, and thermal cycling.
- Consumer Electronics: Encapsulating circuit boards, connectors, and displays in smartphones, tablets, and wearable devices to enhance durability and reliability.
- Aerospace and Defense: Ensuring the robustness and longevity of avionics systems, radar equipment, and military-grade electronics in harsh operating environments.
- Industrial Automation: Safeguarding PLCs, motor drives, and sensors in manufacturing equipment from dust, humidity, and mechanical shocks.
- LED Lighting: Enhancing the weather resistance and thermal management of outdoor and architectural lighting fixtures through effective potting solutions.
Advancements in Potting Materials:
The field of potting materials continues to evolve with ongoing research and development efforts to enhance performance, sustainability, and process efficiency. Some notable trends and advancements include:
- Eco-Friendly Formulations: With increasing emphasis on environmental sustainability, there is a growing demand for potting materials formulated with renewable or recycled ingredients. Manufacturers are exploring bio-based resins and biodegradable additives to reduce the ecological footprint of electronic products while maintaining high performance and reliability.
- Nanocomposite Materials: Incorporating nanoparticles into potting formulations can impart superior mechanical strength, thermal conductivity, and barrier properties. Nanocomposite potting materials exhibit enhanced moisture, corrosion, and thermal cycling resistance, making them well-suited for demanding automotive, aerospace, and renewable energy applications.
- Self-Healing Materials: Researchers are exploring developing self-healing potting materials capable of autonomously repairing minor cracks and damage induced by mechanical stress or environmental factors. By leveraging microencapsulated healing agents or reversible chemical reactions, self-healing potting compounds could extend the service life of electronic assemblies and reduce maintenance requirements.
- Additive Manufacturing: Additive manufacturing, or 3D printing, offers new possibilities for customizing potting solutions to meet specific application requirements. By leveraging digital design tools and rapid prototyping techniques, manufacturers can optimize encapsulated components’ geometry and material properties, leading to improved performance and cost-effectiveness.
- Innovative Potting Materials: Integrating sensing and diagnostic capabilities into potting materials enables real-time environmental conditions, mechanical stresses, and component health monitoring. Innovative potting materials with embedded sensors or RFID tags facilitate condition-based maintenance, predictive analytics, and remote troubleshooting, enhancing overall system reliability and uptime.
- Thermal Management Solutions: Effective thermal management is essential for maintaining optimal operating temperatures within electronic assemblies, particularly in high-power applications such as power electronics and LED lighting. Potting materials with enhanced thermal conductivity help dissipate heat more efficiently, reducing the risk of thermal runaway and prolonging the lifespan of sensitive components. Advanced thermal interface materials (TIMs) integrated into potting compounds facilitate efficient heat transfer between the encapsulated components and heat sinks or enclosures, improving overall system reliability and performance.
- Customized Formulations: The diverse nature of electronic applications often requires tailored potting solutions to meet specific performance requirements and regulatory standards. Manufacturers increasingly offer customized formulations and consulting services to address unique challenges in different industries and applications. By collaborating closely with customers and leveraging material science and engineering expertise, suppliers can develop bespoke potting materials optimized for temperature range, chemical resistance, flame retardancy, and compliance with industry standards.
- Miniaturization and Lightweighting: As electronic devices become smaller, lighter, and more compact, the demand for potting materials with low density and minimal thickness increases. Advanced lightweight potting compounds based on aerogels, microspheres, or syntactic foams offer high strength-to-weight ratios and excellent dielectric properties, making them suitable for aerospace, automotive, and portable electronics applications. These materials enable the encapsulation of miniaturized components without compromising performance or adding unnecessary bulk to the final product.
- Global Regulatory Compliance: Adherence to international regulatory requirements and industry standards is crucial for market acceptance and product certification in an increasingly interconnected world. Potting material manufacturers must ensure that their formulations comply with relevant directives such as RoHS (Restriction of Hazardous Substances), REACH (Registration, Evaluation, Authorization, and Restriction of Chemicals), UL (Underwriters Laboratories), and IPC (Association Connecting Electronics Industries). Suppliers can demonstrate their potting materials’ safety, reliability, and environmental sustainability by conducting rigorous testing and documentation, fostering trust and confidence among customers and stakeholders worldwide.
- Continuous Improvement and Quality Assurance: Leading potting material manufacturers are known for their pursuit of excellence in product quality, consistency, and reliability. Continuous improvement initiatives, supported by robust quality management systems and process optimization techniques, enable suppliers to identify and address performance gaps, enhance manufacturing efficiency, and meet evolving customer expectations. Rigorous quality assurance measures, including incoming raw material inspection, in-process monitoring, and final product testing, ensure that potting materials conform to stringent specifications and deliver consistent performance under real-world conditions.
Conclusion:
Potting materials enhance electronic devices’ durability, reliability, and performance in diverse applications. By providing a protective barrier against environmental hazards, these materials help extend the lifespan of electronic assemblies and reduce the risk of premature failure. With a wide range of formulations and properties available, selecting suitable potting material is crucial for ensuring the optimal functioning of electronic systems in challenging operating conditions. As technology advances, the evolution of potting materials will likely lead to further innovations in electronics design and manufacturing, enabling the development of more robust and resilient devices for the future.
For more about exploring potting materials for electronics: enhancing durability and performance, you can pay a visit to DeepMaterial at https://www.pottingcompound.com/ for more info.
Recent Posts
- Silicone Potting Compound for Electronics
- Potting Compound vs. Epoxy: A Comprehensive Comparison
- Potting Compound for PCB
- In – depth Analysis of the Curing Characteristics of Electronic Potting Compounds
- A Comprehensive Analysis of the Environmental Performance of Encapsulating Materials: From Regulations to Practices
- A Comprehensive Analysis of PCB Encapsulation Quality Inspection: Innovative Application of Non-Destructive Testing Technologies
- Analysis of the Improvement of the Seismic and Impact Resistance Performance of PCB by Encapsulation
- A Comprehensive Guide to Evaluating the Reliability of Encapsulation Materials for Encapsulated PCBs
- In-depth Analysis of the Reparability of Encapsulation Materials
- A Comprehensive Analysis of Post-Potting PCB Issues and the Repair and Rework of Potting Materials