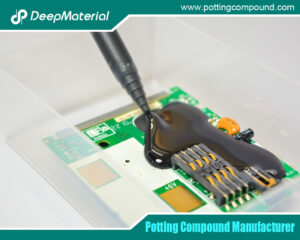
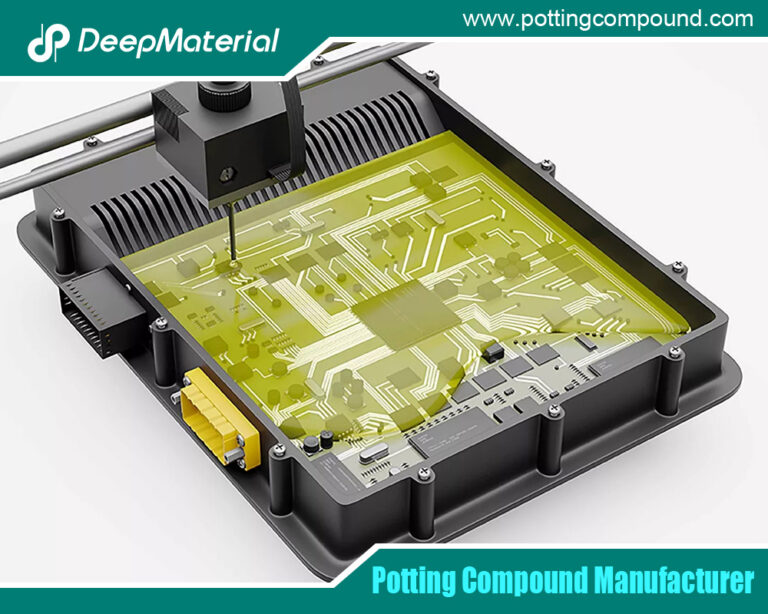
Electronics Encapsulation Epoxy Adhesive: Ensuring Durability and Reliability in Modern Devices
- Electronic Potting Material Manufacturer
- July 5, 2024
- adhesive glue manufacturer, conformal coating for electronics, conformal coating for pcb, conformal coating for pcb standards, conformal coating material, conformal coating pcb, conformal coating silicone, conformal coating waterproof, deepmaterial adhesive glue, electrical potting compound, electronics adhesive glue, electronics encapsulation adhesive, electronics encapsulation epoxy adhesive, electronics encapsulation epoxy adhesive glue, electronics epoxy adhesive, encapsulation epoxy adhesive, epoxy encapsulation, epoxy encapsulation electronic components, epoxy encapsulation led, epoxy encapsulation meaning, epoxy encapsulation molding compound, epoxy potting compound, epoxy resin encapsulation, industrial adhesive suppliers, One Part Epoxy Adhesive, polyurethane potting compound, potting compound for electronics, potting compound for pcb, silicone epoxy adhesive glue, UV curing potting compound, waterproof potting compound
Electronics Encapsulation Epoxy Adhesive: Ensuring Durability and Reliability in Modern Devices
In the rapidly advancing world of electronics, the demand for reliable and durable devices has never been higher. One key technology contributing to the longevity and performance of electronic components is encapsulation epoxy adhesive. This adhesive protects sensitive electronic parts from environmental factors, mechanical stress, and electrical interference. This comprehensive article will explore the various aspects of electronics encapsulation epoxy adhesive, including its composition, types, applications, benefits, and advancements in the field.
Understanding Electronics Encapsulation Epoxy Adhesive
Electronics encapsulation epoxy adhesive is a resin used to encapsulate and protect electronic components. This adhesive forms a hard, protective layer that shields delicate parts from external damage. The primary purpose of encapsulation is to enhance the durability and reliability of electronic devices by providing robust protection against moisture, dust, chemicals, and mechanical shock.
Composition of Epoxy Adhesives
Epoxy adhesives are thermosetting polymers that consist of two main components: the resin and the hardener. A chemical reaction occurs when these two components are mixed, resulting in a rigid, durable material. The composition of epoxy adhesives can be tailored to achieve specific properties, making them highly versatile for various applications. Key ingredients in epoxy formulations include:
- Epoxy Resins: These are the primary building blocks of the adhesive, providing the structural framework.
- Hardeners: Also known as curing agents, these chemicals react with the epoxy resin to initiate the curing process.
- Fillers and Additives: These materials enhance thermal conductivity, electrical insulation, and mechanical strength.
Types of Epoxy Adhesives for Electronics Encapsulation
Several types of epoxy adhesives are used for electronics encapsulation, each offering unique properties tailored to specific applications. Some of the common types include:
- Room Temperature Cure Epoxies: These adhesives cure at ambient temperatures and are ideal for applications where heat-sensitive components are involved.
- Heat Cure Epoxies: These require elevated temperatures to cure, resulting in higher mechanical strength and thermal stability.
- UV Cure Epoxies: These cure upon exposure to ultraviolet light, providing quick curing times and suitability for precision applications.
- Thermally Conductive Epoxies: These contain fillers that enhance thermal conductivity, making them suitable for applications requiring efficient heat dissipation.
- Electrically Conductive Epoxies: These are formulated with conductive fillers to provide electrical conductivity and are often used in applications requiring electrical interconnections.
Applications of Electronics Encapsulation Epoxy Adhesive
Epoxy adhesives are used in various electronic applications, from consumer electronics to industrial and automotive electronics. Some of the critical applications include:
- Printed Circuit Boards (PCBs): Encapsulation of PCBs protects the delicate circuits from environmental hazards and mechanical damage.
- Microelectronics: Encapsulation adhesives protect microchips and integrated circuits from moisture and contaminants.
- LEDs and Lighting: Epoxy encapsulation enhances the durability and longevity of LED lights by protecting against moisture and mechanical stress.
- Sensors and Actuators: Encapsulation protects sensitive sensors and actuators in harsh environments, ensuring accurate and reliable performance.
- Power Electronics: High-power components such as transformers and capacitors benefit from epoxy encapsulation by improving thermal management and electrical insulation.
Benefits of Using Epoxy Adhesives for Encapsulation
The use of epoxy adhesives for encapsulation offers numerous benefits that enhance the performance and reliability of electronic devices:
- Environmental Protection: Epoxy encapsulation provides a robust barrier against moisture, dust, chemicals, and other contaminants.
- Mechanical Strength: The cured epoxy forms a hard, durable layer that protects components from mechanical stress and impact.
- Electrical Insulation: Epoxy adhesives offer excellent electrical insulation properties, preventing short circuits and electrical failures.
- Thermal Management: Thermally conductive epoxies help dissipate heat from high-power components, preventing overheating and improving efficiency.
- Chemical Resistance: Epoxy encapsulation resists exposure to harsh chemicals, ensuring the longevity of electronic devices in industrial environments.
- Miniaturization: Epoxy adhesives enable the miniaturization of electronic components by providing reliable protection in compact spaces.
Advancements in Epoxy Adhesive Technology
The field of epoxy adhesives for electronics encapsulation is continually evolving, with ongoing research and development efforts to improve performance and expand applications. Some of the recent advancements include:
- Nanotechnology: Incorporating nanoparticles into epoxy formulations enhances thermal conductivity, electrical insulation, and mechanical strength. Nanocomposites offer improved performance without compromising other essential properties.
- Flexible Epoxies: Development of flexible epoxy adhesives that can withstand bending and stretching, making them suitable for flexible electronics and wearable devices.
- Environmentally Friendly Formulations: Advances in green chemistry have led to development of low-VOC (volatile organic compound) and solvent-free epoxy adhesives, reducing environmental impact and improving workplace safety.
- High-Temperature Epoxies: Formulations that can withstand extreme temperatures are being developed for aerospace and automotive electronics applications.
- Smart Epoxies: Incorporating self-healing and sensing capabilities into epoxy adhesives allows for real-time monitoring and repair of electronic components, enhancing reliability and reducing maintenance costs.
Selection Criteria for Epoxy Adhesives in Electronics Encapsulation
Choosing the suitable epoxy adhesive for a specific application requires careful consideration of various factors to ensure optimal performance and reliability. Critical selection criteria include:
- Thermal Properties: Assessing the adhesive’s thermal conductivity and temperature resistance to ensure it can handle the operating conditions of the electronic components.
- Mechanical Properties: Evaluating the adhesive’s hardness, flexibility, and impact resistance to match the mechanical demands of the application.
- Electrical Properties: Considering the adhesive’s electrical insulation or conductivity requirements based on the application’s needs.
- Chemical Resistance: Ensuring the adhesive can withstand exposure to chemicals and environmental contaminants specific to the application.
- Curing Process: Selecting an adhesive with a curing process compatible with the manufacturing workflow and the thermal limitations of the components.
- Environmental Impact: Choosing environmentally friendly formulations that comply with regulations and minimize the ecological footprint.
Challenges in Electronics Encapsulation
Despite the numerous benefits of epoxy encapsulation, some challenges need to be addressed to achieve optimal performance and reliability:
- Thermal Mismatch: Differences in the coefficient of thermal expansion (CTE) between the encapsulant and the electronic components can lead to stress and potential failure during thermal cycling.
- Moisture Absorption: Some epoxy adhesives may absorb moisture over time, affecting their electrical and mechanical properties. Developing moisture-resistant formulations is crucial for long-term reliability.
- Curing Shrinkage: The curing process can cause shrinkage, leading to stress on the encapsulated components. Controlling shrinkage through optimized formulations and curing processes is essential.
- Compatibility: Ensuring compatibility between the epoxy adhesive and the materials used in the electronic components and substrates is vital to prevent adverse reactions and degradation.
- Process Control: Maintaining precise control over the mixing, dispensing, and curing processes is necessary to achieve consistent and reliable encapsulation results.
Case Studies and Real-world Applications
To illustrate the practical applications and benefits of electronics encapsulation epoxy adhesive, let’s explore a few case studies from different industries:
Case Study 1: Automotive Electronics
Electronic components in the automotive industry are subjected to harsh environments, including extreme temperatures, vibrations, and chemical exposure. An automotive manufacturer faced issues with the reliability of its engine control units (ECUs) due to moisture ingress and thermal stress. Switching to a thermally conductive and moisture-resistant epoxy encapsulant significantly improved the durability and performance of the ECUs, resulting in fewer failures and reduced warranty claims.
Case Study 2: Consumer Electronics
A leading manufacturer of wearable fitness trackers encountered problems with water damage and mechanical stress affecting the performance of their devices. By using a flexible epoxy adhesive for encapsulation, they were able to provide a waterproof seal and enhance the durability of the trackers. This led to increased customer satisfaction and a reduction in returns and repairs.
Case Study 3: Renewable Energy
A solar panel manufacturer needed to protect the electronic components in their junction boxes from harsh outdoor conditions, including UV exposure and temperature fluctuations. Implementing a UV-curable epoxy encapsulant with high thermal stability ensured the long-term reliability and performance of the solar panels. This solution contributed to higher energy efficiency and lower maintenance costs.
Future Trends in Electronics Encapsulation Epoxy Adhesive
The future of electronics encapsulation epoxy adhesive looks promising, with several emerging trends that are expected to shape the industry:
- Integration of Advanced Materials: Incorporating advanced materials such as graphene, carbon nanotubes, and boron nitride into epoxy formulations to enhance thermal and electrical properties.
- Smart Manufacturing: Adopting intelligent manufacturing techniques, including automation and robotics, to achieve precise and efficient encapsulation processes.
- Miniaturization and Flexibility: Development of ultra-thin and flexible epoxy adhesives to support the growing trend of miniaturized and flexible electronic devices.
- Sustainability: Increased focus on developing sustainable and biodegradable epoxy formulations to reduce environmental impact and support green electronics manufacturing.
- Enhanced Performance Monitoring: Integrating sensors and self-monitoring capabilities into epoxy encapsulants enables real-time performance monitoring and predictive maintenance.
Electronic encapsulation epoxy adhesive is a critical technology that plays a vital role in ensuring the durability and reliability of modern electronic devices. With advancements in materials science and manufacturing processes, epoxy adhesives continue to evolve, offering enhanced properties and capabilities to meet the demands of diverse electronic applications. From protecting sensitive components in automotive electronics to enabling the miniaturization of wearable devices, epoxy encapsulation plays a crucial role in safeguarding electronic systems from environmental hazards, mechanical stress, and electrical interference.
As industries continue to push the boundaries of innovation, the need for reliable encapsulation solutions will only grow. By staying abreast of the latest developments in epoxy adhesive technology and selecting suitable materials for specific applications, electronics manufacturers can ensure their products’ longevity, performance, and safety.
In conclusion, electronics encapsulation epoxy adhesive represents a cornerstone technology in the ever-expanding world of electronics. Its ability to provide robust protection, enhance performance, and enable innovation makes it indispensable across various industries. As research and development efforts continue to advance, we can expect to see even more sophisticated epoxy formulations that further elevate the reliability and durability of electronic devices, driving progress and innovation in the years to come.
For more about choosing the electronics encapsulation epoxy adhesive:ensuring durability and reliability in modern devices, you can pay a visit to DeepMaterial at https://www.pottingcompound.com/ for more info.
Recent Posts
- The Potting and Encapsulating Compounds Market: An In-Depth Exploration of Trends, Innovations, and Future Prospects
- The Comprehensive Guide to Polyurethane Potting Compound Manufacturers
- The Comprehensive Guide to Epoxy Potting Compound Manufacturers
- The Essential Guide to Potting Materials for Electronics
- The Expanding Horizon of the Mini Silicone Optical Glue Market
- The Comprehensive Guide to PCB Potting Services: Ensuring Reliability in Electronics
- Comprehensive Insights on PCB Encapsulation in Potting Material
- The Vital Role of Industrial Silicone Adhesive Manufacturers in Modern Industry
- The Potting Material Manufacturer: Essential Players in Electronics Protection
- Exploring the Role of Electronic Encapsulation in Potting Material Manufacturing
Tags
Related Posts
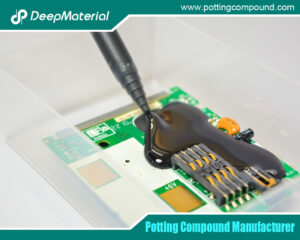
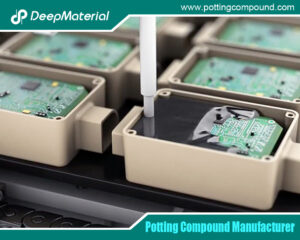
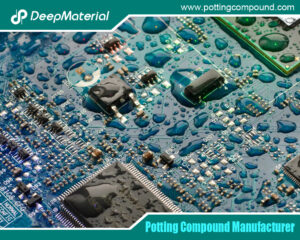
The Comprehensive Guide to Epoxy Potting Compound Manufacturers
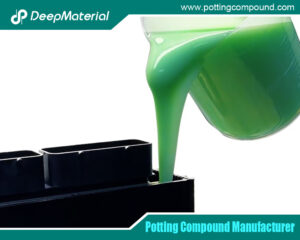
The Essential Guide to Potting Materials for Electronics
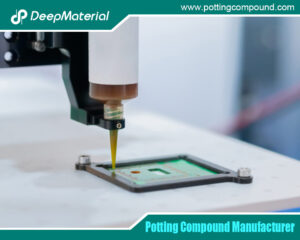
The Expanding Horizon of the Mini Silicone Optical Glue Market
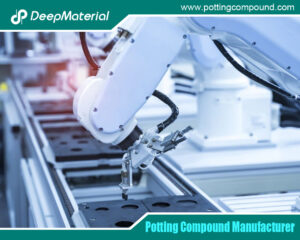