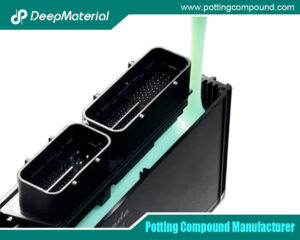
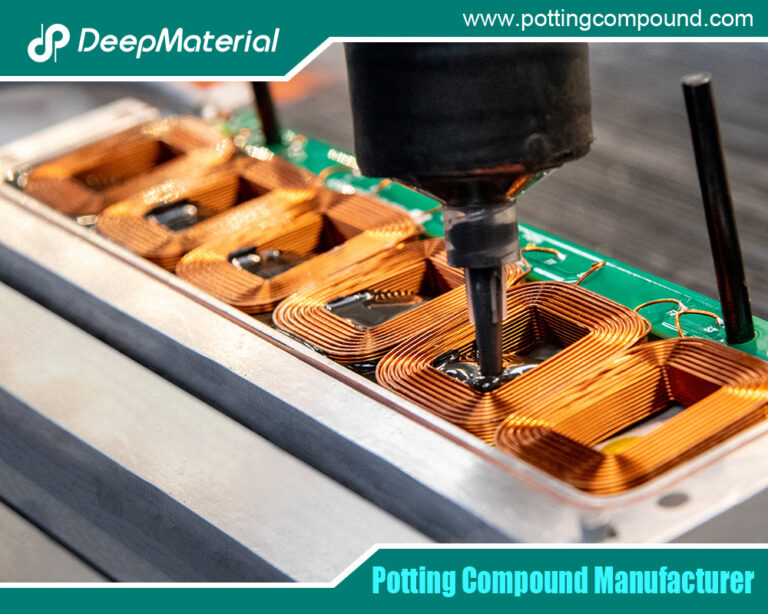
Waterproof Potting Compound: A Comprehensive Guide
- Electronic Potting Material Manufacturer
- July 15, 2025
- Acrylic Conformal Coating, acrylic vs silicone conformal coating, Ceramic Potting Compound, Ceramic Potting Compound Manufacturer, circuit board potting compound, circuit board potting compound china hotsale, conformal coating, conformal coating for pcb, conformal coating market, conformal coating silicone, Connector Potting Compound, deepmaterial potting compound, deepmaterial potting compound manufacturer, electric motor potting compound, electrical potting compound, electronic epoxy encapsulant potting compounds, epoxy potting compound, pcb encapsulation epoxy, polyurethane potting compound, potting compound for electronics, potting compound for pcb, potting compound vs epoxy, potting material for electronic components, silicone potting compound for electronics, UV curing potting compound, uv potting compound, waterproof potting compound, waterproof potting compound manufacturer, waterproof potting compound supplier
Waterproof Potting Compound: A Comprehensive Guide
In today’s technology-driven world, protecting sensitive electronic components from environmental hazards is paramount. One of the most effective solutions for safeguarding electronics is the use of waterproof potting compounds. These specialized materials encase electronic assemblies, providing a robust barrier against moisture, dust, chemicals, and physical stress. From underwater sensors to automotive control units, waterproof potting compounds are critical in ensuring the reliability and longevity of devices across various industries.
The significance of waterproof potting compounds cannot be overstated. Water ingress is one of the leading causes of electronic failure, resulting in costly repairs or replacements. By creating a sealed environment, these compounds protect delicate circuits from corrosion and short-circuiting, even in harsh conditions like marine or outdoor settings. This article explores the fundamentals of waterproof potting compounds, including their properties, types, applications, benefits, and practical considerations. Whether you’re an engineer, manufacturer, or hobbyist, this guide will help you understand why these materials are indispensable and how to choose the right one for your needs.
What is a Waterproof Potting Compound?
A potting compound is a material used to encapsulate electronic components, filling the space around them to provide protection. When the term “waterproof” is added, it refers to compounds specifically designed to prevent water or moisture penetration, making them ideal for environments where exposure to liquids is a concern. Waterproof potting compounds are typically liquid during application, allowing them to flow into intricate spaces, and then cure into a solid or semi-solid state to create a durable seal.
The waterproofing capability is achieved through the chemical composition of the compound, which is often formulated to bond tightly with components and resist water ingress. Common materials used include:
- Epoxy: Known for its hardness and chemical resistance.
- Silicone: Valued for flexibility and wide temperature tolerance.
- Polyurethane: Offers a balance of flexibility and toughness.
These materials are tailored to meet specific requirements, such as thermal conductivity, electrical insulation, or resistance to UV light. By forming a protective cocoon around electronics, waterproof potting compounds ensure functionality in challenging conditions, making them a go-to solution for industries requiring high reliability.
Key Properties of Waterproof Potting Compounds
Waterproof potting compounds are selected based on a combination of properties that make them uniquely suited for protecting electronics. Below are the key characteristics that define their performance:
- Water Resistance: The hallmark feature, measured by standards like IP (Ingress Protection) ratings. For example, an IP68-rated compound ensures complete protection against water immersion.
- Thermal Conductivity: Many compounds dissipate heat generated by electronic components, preventing overheating. Some are formulated with fillers to enhance thermal management.
- Chemical Resistance: These compounds resist exposure to solvents, oils, and acids, which is crucial in industrial or automotive applications.
- Mechanical Strength: They provide structural support, absorbing shocks and vibrations to prevent component damage.
- Electrical Insulation: High dielectric strength ensures no unwanted current flow, protecting circuits from shorting.
- Flexibility: Certain compounds, like silicones, remain flexible after curing, accommodating thermal expansion or movement without cracking.
These properties make waterproof potting compounds versatile, enabling them to meet the stringent demands of applications ranging from consumer electronics to heavy-duty industrial systems.
Types of Waterproof Potting Compounds
Waterproof potting compounds come in several types, each with distinct advantages and limitations. The three most common types are:
- Epoxy-Based Compounds
Epoxy potting compounds are renowned for their exceptional hardness and durability. They offer excellent water and chemical resistance, making them ideal for harsh environments. Epoxies also provide superior mechanical strength and adhesion to various substrates. However, they can be brittle, limiting their use in applications requiring flexibility. Additionally, epoxies may have longer curing times and higher costs.
Pros: High strength, excellent chemical resistance, good thermal conductivity.
Cons: Brittle, less flexible, slower curing.
- Silicone-Based Compounds
Silicone potting compounds are prized for their flexibility and wide temperature range (-50°C to 200°C or more). They remain soft and pliable after curing, making them suitable for applications with thermal expansion or vibration. Silicones are also UV-resistant, ideal for outdoor use. However, they have lower mechanical strength and may not adhere as well to certain surfaces.
Pros: Flexible, wide temperature tolerance, UV resistance.
Cons: Lower strength, higher cost, weaker adhesion.
- Polyurethane-Based Compounds
Polyurethane compounds strike a balance between epoxy’s strength and silicone’s flexibility. They offer good water resistance, toughness, and moderate flexibility, making them versatile for various applications. Polyurethanes cure quickly and are cost-effective, but they may degrade under prolonged UV exposure.
Pros: Balanced properties, fast curing, cost-effective.
Cons: Limited UV resistance, moderate thermal conductivity.
Choosing the right type depends on the specific requirements of the application, such as environmental conditions, mechanical stress, and budget.
Applications of Waterproof Potting Compounds
Waterproof potting compounds are used across a wide range of industries, protecting critical components in demanding environments. Some key applications include:
- Electronics: Printed circuit boards (PCBs), sensors, and connectors are potted to prevent moisture damage in devices like smartphones, wearables, and IoT gadgets.
- Automotive Industry: Potting compounds protect engine control units (ECUs), lighting systems, and sensors from water, oil, and vibrations in vehicles.
- Marine Applications: Underwater sensors, navigation systems, and communication devices rely on waterproof potting to withstand saltwater exposure.
- Outdoor Lighting and Solar Panels: Potting ensures LEDs and solar panel electronics remain functional despite rain, humidity, or temperature fluctuations.
- Medical Devices: Waterproof potting is used in portable diagnostic tools and implantable devices, ensuring reliability in sterile or humid conditions.
These applications highlight the versatility of waterproof potting compounds, which are tailored to meet the unique challenges of each industry.
Benefits of Using Waterproof Potting Compounds
The adoption of waterproof potting compounds offers numerous advantages, making them a preferred choice for protecting electronics:
- Protection Against Moisture and Corrosion: By sealing components, these compounds prevent water ingress, reducing the risk of corrosion and electrical failure.
- Enhanced Durability and Longevity: Potting extends the lifespan of devices by shielding them from environmental stressors like humidity, dust, and chemicals.
- Improved Safety and Reliability: Insulating properties reduce the risk of electrical shorts, enhancing device safety and performance.
- Cost-Effectiveness: While initial costs may be high, potting reduces maintenance and replacement expenses, offering long-term savings.
These benefits make waterproof potting compounds an essential investment for manufacturers seeking to deliver reliable, high-quality products.
Challenges and Considerations
Despite their advantages, waterproof potting compounds come with challenges that must be addressed:
- Cost: High-performance compounds, like silicones, can be expensive, impacting project budgets.
- Curing Time: Some compounds, particularly epoxies, require extended curing periods, slowing production.
- Application Complexity: Proper application requires specialized equipment and skilled labor to ensure void-free encapsulation.
- Environmental Impact: Certain compounds may contain chemicals that pose disposal or recycling challenges.
- Compatibility: Not all compounds are compatible with every component material, risking adhesion or performance issues.
To mitigate these challenges, manufacturers must carefully evaluate their needs and work with suppliers to select suitable materials.
How to Choose the Right Waterproof Potting Compound
Selecting the appropriate waterproof potting compound involves several considerations:
- Environmental Conditions: Assess exposure to water, temperature extremes, UV light, or chemicals.
- Mechanical Requirements: Determine if flexibility or hardness is needed based on vibration or thermal expansion.
- Electrical Properties: Ensure the compound provides adequate insulation for the application.
- Certifications: Look for compounds meeting industry standards, such as UL or RoHS compliance.
- Budget and Scalability: Balance performance with cost, especially for large-scale production.
Consulting with manufacturers or testing samples can help identify the best compound for specific needs, ensuring optimal protection and performance.
Conclusion
Waterproof potting compounds are a cornerstone of modern electronics protection, offering unparalleled defense against moisture, chemicals, and mechanical stress. Their versatility across industries—from automotive to marine—underscores their importance in ensuring device reliability and longevity. By understanding the types, properties, and applications of these compounds, manufacturers and engineers can make informed decisions to safeguard their products.
As technology advances, we can expect innovations in potting compounds, such as eco-friendly formulations and enhanced thermal management. For those looking to protect their electronics, exploring the range of waterproof potting compounds available today is a critical step toward building durable, high-performing devices. Start by consulting with suppliers or testing options to find the perfect solution for your project.
For more about the best waterproof potting compound: a comprehensive guide, you can pay a visit to DeepMaterial at https://www.pottingcompound.com/ for more info.
Recent Posts
- What Are the Core Differences Between Different Conformal Coating Types?
- The Benefits of Conformal Coating for Electronics Products
- Conformal Coating Spray
- UV Curing Potting Compound
- The Ultimate Guide to Electrical Potting Compound and Market Application
- The Top Polyurethane Potting Compound
- Advanced Epoxy Potting Compound for Superior Electronic Protection
- Waterproof Potting Compound: A Comprehensive Guide
- Silicone Potting Compound for Electronics
- Potting Compound vs. Epoxy: A Comprehensive Comparison
Tags
Related Posts
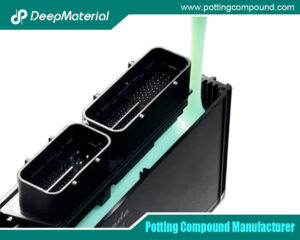
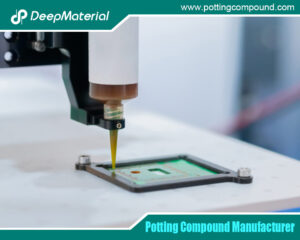
The Benefits of Conformal Coating for Electronics Products
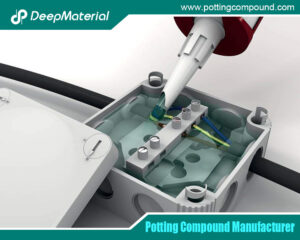
Conformal Coating Spray
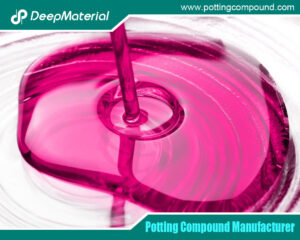
UV Curing Potting Compound
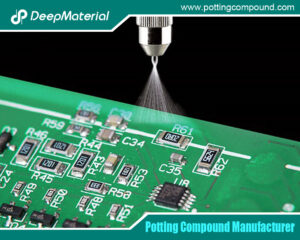
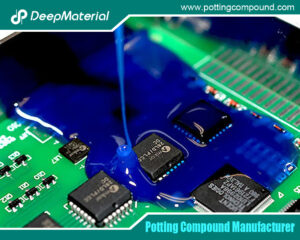