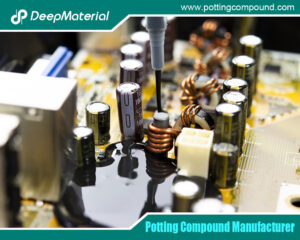
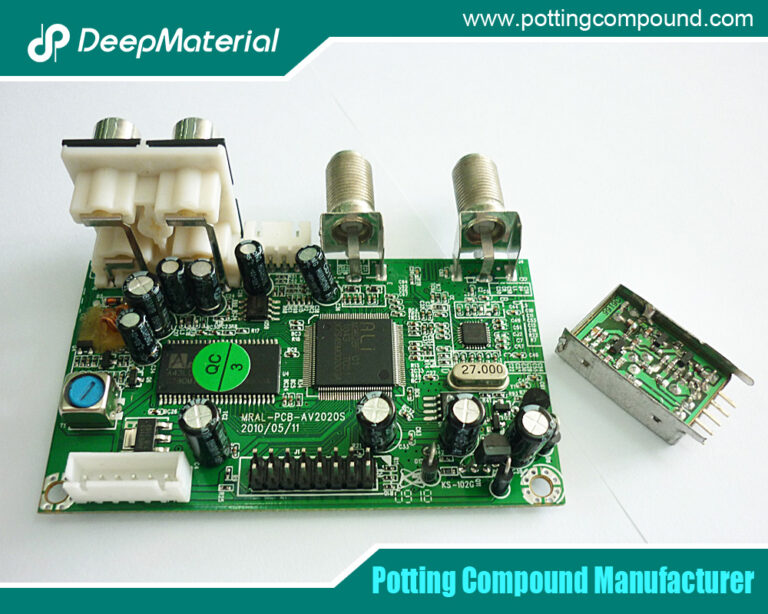
The Versatility of Epoxy Powder Coating in Electrical Insulation
- Electronic Potting Material Manufacturer
- October 8, 2024
- Acrylic Conformal Coating, conformal coating for electronics, conformal coating for pcb, conformal coating for pcb standards, conformal coating material, conformal coating spray, conformal coating types, Connector Potting Compound, Electronic Conformal Coating, electronic potting compound, Epoxy Coating, epoxy coating for electrical insulation, epoxy conformal coating, Epoxy Powder Coating, Epoxy Powder Coating for Electrical, epoxy powder coating for electrical insulation, epoxy powder coating in electrical insulation, Flexible Potting Compound, Industrial Conformal Coating, insulating epoxy coating, LED Potting Compound, pcb conformal coating, PCB Potting Compound, polyurethane potting compound, Silicone Conformal Coating, Silicone Potting Compound, Urethane Conformal Coating, UV Cure Conformal Coating, UV Cure Potting Compound, Waterproof Conformal Coating, waterproof potting compound
The Versatility of Epoxy Powder Coating in Electrical Insulation
Epoxy powder coating has become a cornerstone in electrical and electronic applications, offering robust insulation and protection. This advanced material is widely recognized for its ability to enhance the performance and longevity of electrical components. Epoxy resins in this context span various applications, including adhesives, sealants, coatings, impregnants, moldings, and potting compounds. This article delves into the multifaceted role of epoxy powder coating in electrical insulation, examining its benefits, applications, and future use in the industry.
Understanding Epoxy Powder Coating
What is Epoxy Powder Coating?
Epoxy powder coating is a protective layer applied to electrical components to provide insulation and safeguard against environmental factors. Unlike traditional liquid coatings, powder coatings are used as a dry powder and cured under heat to form a durable finish. This method offers several advantages, particularly in the realm of electrical insulation.
- Composition: Made from epoxy resins and hardeners, creating a robust and resilient finish.
- Application Process:Involves electrostatic powder spraying onto a surface, followed by curing in an oven.
- Properties: Known for its excellent adhesion, chemical resistance, and electrical insulating properties.
Benefits of Epoxy Powder Coating for Electrical Insulation
Epoxy powder coating is a premier choice for electrical insulation because it enhances performance and durability.
- Enhanced Durability:One of the primary advantages of epoxy powder coating is its exceptional durability. This coating forms a robust, protective layer over electrical components, effectively resisting physical wear and tear. The resilient nature of epoxy ensures that components remain safeguarded even under harsh operating conditions.
- Superior Insulation: Epoxy powder coatings are highly effective in providing electrical insulation. They prevent short circuits by properly containing electrical currents within their designated pathways. This superior insulation enhances the safety of electrical systems and contributes to their efficient operation and longevity.
- Corrosion Resistance: Another significant benefit of epoxy powder coating is its corrosion resistance. The coating is a barrier against moisture and chemical exposure, which can otherwise lead to component degradation. By protecting against corrosion, epoxy powder coatings help extend the lifespan of electrical components, reducing the need for frequent replacements and maintenance.
- Environmental Safety: Besides its performance advantages, epoxy powder coating is also environmentally friendly. Unlike many traditional coatings, epoxy powder is free from solvents and volatile organic compounds (VOCs). It makes it a greener choice for industrial applications, aligning with modern sustainability goals and reducing environmental impact.
Applications in Electrical and Electronic Components
Adhesives and Sealants
Epoxy powder coatings are frequently used as adhesives and sealants in electrical assemblies. Their strong bonding properties and resistance to environmental factors make them ideal for:
- Electrical Connections: Ensuring reliable and long-lasting connections between components.
- Sealant Applications: Preventing ingress of moisture and contaminants that could affect electrical performance.
Coatings
Coatings applied via epoxy powder serve to protect and insulate electrical components. It includes:
- Circuit Boards: Providing a protective layer to prevent damage from environmental factors and mechanical stress.
- Wires and Cables:Offering insulation to ensure the safety and reliability of electrical transmission.
Impregnants and Potting Compounds
Epoxy resins are used as impregnants and potting compounds to encapsulate and insulate electrical components, such as:
- Transformers: Filling voids and providing insulation to protect against electrical faults.
- Electronic Assemblies: Ensuring components are secure and insulated from external influences.
Moldings
In molding applications, epoxy powder coating provides:
- Custom Shapes: Forming complex shapes and ensuring uniform insulation across intricate components.
- Mechanical Strength: Enhancing the physical integrity of molded parts used in various electrical applications.
Comparative Analysis
Epoxy Powder Coating vs. Traditional Coatings
When comparing epoxy powder coatings to traditional liquid coatings, several distinctions emerge:
- Application Efficiency: Powder coatings offer a more efficient application process with less waste and quicker curing times.
- Performance: Epoxy powder coatings generally provide better insulation and durability compared to some traditional coatings.
- Environmental Impact: Powder coatings are more environmentally friendly, as they do not release harmful solvents.
Epoxy Powder Coating vs. Other Insulation Materials
Regarding electrical insulation, the choice of materials can significantly affect performance and longevity. Epoxy powder coating stands out among other insulation materials due to its distinct advantages.
- Silicone Insulation: Although silicone offers notable flexibility, epoxy powder coatings surpass its rigidity and chemical resistance. The rigid nature of epoxy coatings makes them highly effective in environments that demand durability and stability. At the same time, silicone’s flexibility may provide a different level of protection against harsh chemicals and environmental conditions.
- Polyurethane Insulation: Polyurethane insulation is often favored for its impact resistance. However, epoxy coatings excel in thermal stability and adherence. While polyurethane might handle physical impacts better, epoxy powder coatings maintain their integrity and insulation properties under extreme temperatures and challenging conditions.
Future Trends and Innovations
The field of epoxy powder coating is continuously evolving, with several advancements shaping its future.
- Nanotechnology:Integrating nanomaterials enhances the insulating properties and overall performance of epoxy powder coatings. These advancements promise greater efficiency and effectiveness in insulation applications, potentially revolutionizing the protection of electrical components.
- Enhanced Formulations: Researchers are developing new epoxy formulations that offer improved flexibility, adhesion, and resistance to extreme conditions. These innovations aim to broaden the range of applications for epoxy coatings and increase their effectiveness in various environments.
Emerging Applications
Epoxy powder coatings are increasingly being adopted in cutting-edge and eco-conscious technologies:
- Smart Electronics: The demand for high-performance insulation in advanced electronics is driving the use of epoxy powder coatings. These coatings provide the necessary protection and reliability for sophisticated electronic devices, which require superior insulation to function optimally.
- Green Technologies: As industries shift towards sustainability, epoxy powder coatings are utilized in eco-friendly technologies. Their environmental benefits align with the industry’s goals for greener, more sustainable practices, making them a popular choice for future-oriented applications.
Conclusion
Epoxy powder coating has firmly established itself as a vital component in electrical insulation, benefiting from enhanced durability and superior insulation to environmental safety. Its applications in adhesives, coatings, impregnants, potting compounds, and moldings highlight its versatility and significance in modern electrical and electronic systems. As technology advances, the future of epoxy powder coatings looks promising, with ongoing innovations set to enhance their performance and expand their applications. This robust material not only meets the demands of current technological needs but also paves the way for future developments in electrical insulation.
For more about choosing the versatility of epoxy powder coating in electrical insulation, you can pay a visit to DeepMaterial at https://www.pottingcompound.com/ for more info.
Recent Posts
- Potting Compound for PCB
- In – depth Analysis of the Curing Characteristics of Electronic Potting Compounds
- A Comprehensive Analysis of the Environmental Performance of Encapsulating Materials: From Regulations to Practices
- A Comprehensive Analysis of PCB Encapsulation Quality Inspection: Innovative Application of Non-Destructive Testing Technologies
- Analysis of the Improvement of the Seismic and Impact Resistance Performance of PCB by Encapsulation
- A Comprehensive Guide to Evaluating the Reliability of Encapsulation Materials for Encapsulated PCBs
- In-depth Analysis of the Reparability of Encapsulation Materials
- A Comprehensive Analysis of Post-Potting PCB Issues and the Repair and Rework of Potting Materials
- A Comprehensive Analysis of the Compatibility between Encapsulation Materials and PCBs: Exploration of Chemical Reactions and Their Impact on Performance
- How to Ensure the Compatibility between Encapsulation Materials and Various Components on PCBs