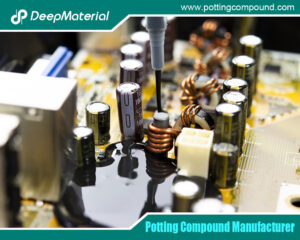
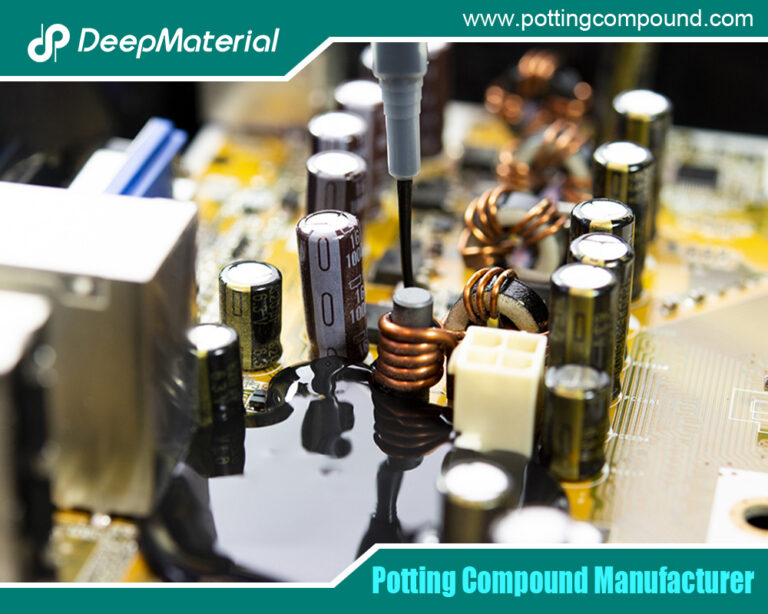
Potting Compound for PCB
- Electronic Potting Material Manufacturer
- June 25, 2025
- Ceramic Potting Compound, Ceramic Potting Compound Manufacturer, circuit board potting, circuit board potting compound, circuit board potting compound china hotsale, circuit board potting compound china OEM, circuit board potting compound factory hotsale, circuit board potting compound hotsale, Connector Potting Compound, deepmaterial potting compound, deepmaterial potting compound manufacturer, electric motor potting compound, electrical potting compound, electronic epoxy encapsulant potting compounds, epoxy potting compound, pcb potting, polyurethane potting compound, polyurethane potting compound for electronics, potting compound, potting compound for electronics, potting compound for pcb, potting compound vs epoxy, potting material for electronic components, potting material for electronics, potting pcb, silicone potting compound for electronics, UV Curable Conformal Coating, UV Cured Epoxy Potting, UV curing potting compound, UV Curing Potting Compounds, waterproof potting compound
Potting Compound for PCB
A potting compound is a liquid or semi-liquid material that is poured or injected over a PCB or electronic assembly, then cured to form a solid, protective layer. The process of potting encases the PCB, shielding its components from external threats while providing electrical insulation and structural support. Unlike conformal coatings, which apply a thin protective film, potting compounds fully encapsulate the assembly, offering superior protection in harsh environments.
Key Functions of Potting Compounds
- Environmental Protection: Shields PCBs from moisture, dust, chemicals, and corrosion.
- Mechanical Stability: Absorbs shock and vibration, preventing damage to delicate components.
- Electrical Insulation: Prevents short circuits and arcing by insulating conductive parts.
- Thermal Management: Dissipates heat or insulates against extreme temperatures.
- Tamper Resistance: Deters unauthorized access or reverse engineering by encasing components.
Potting compounds are essential in industries such as automotive, aerospace, telecommunications, medical devices, and renewable energy, where PCBs face challenging operating conditions.
Types of Potting Compounds for PCBs
Potting compounds come in various formulations, each tailored to specific performance requirements. The main types include:
- Epoxy Potting Compounds
Description: Two-part systems that cure to form a hard, rigid encapsulation.
Properties:
- Excellent chemical resistance and mechanical strength.
- High dielectric strength for electrical insulation.
- Good adhesion to PCB substrates and components.
Advantages:
- Superior protection against moisture, solvents, and abrasion.
- Ideal for high-stress environments like automotive or aerospace.
Disadvantages:
- Limited flexibility, which may stress components during thermal cycling.
- Difficult to remove or repair once cured.
Applications: Engine control units, power supplies, and industrial controllers.
- Example: MG Chemicals’ epoxy compounds offer high thermal conductivity for heat dissipation.
- Silicone Potting Compounds
Description: Flexible, rubber-like materials that remain soft after curing.
Properties:
- Wide temperature range (-50°C to 200°C or higher).
- Excellent flexibility and vibration dampening.
- UV and moisture resistance.
Advantages:
- Accommodates thermal expansion, reducing stress on components.
- Easy to remove for repairs or rework.
Disadvantages:
- Lower mechanical strength and chemical resistance compared to epoxy.
- Higher cost in some formulations.
Applications: LEDs, sensors, and outdoor electronics exposed to weather.
- Example: Dow’s silicone encapsulants provide flexibility for automotive and lighting applications.
- Polyurethane Potting Compounds
Description: Versatile materials that balance flexibility and rigidity.
Properties:
- Good moisture and chemical resistance.
- Moderate dielectric strength and thermal conductivity.
- Customizable hardness after curing.
Advantages:
- Offers a middle ground between epoxy’s rigidity and silicone’s flexibility.
- Cost-effective for many applications.
Disadvantages:
- Limited high-temperature performance compared to silicone.
- May degrade under prolonged UV exposure.
Applications: Consumer electronics, medical devices, and telecommunications equipment.
- Example: Henkel’s polyurethane compounds are used for encapsulating sensitive electronics.
- Acrylic Potting Compounds
Description: Fast-curing materials with moderate protective properties.
Properties:
- Good electrical insulation and adhesion.
- Easy to apply and remove.
Advantages:
- Quick curing times reduce production cycles.
- Cost-effective for less demanding applications.
Disadvantages:
- Lower resistance to chemicals, moisture, and extreme temperatures.
- Limited mechanical strength.
Applications: Low-cost consumer electronics and non-critical assemblies.
- Example: Electrolube’s acrylic compounds suit budget-conscious applications.
- UV-Curable Potting Compounds
- Description: Materials that cure rapidly under UV light, often hybrid formulations.
Properties:
- Fast processing for high-volume production.
- Good adhesion and environmental resistance.
Advantages:
- Speeds up manufacturing with instant curing.
- Precise application for selective encapsulation.
Disadvantages:
- Requires UV equipment, increasing setup costs.
- Limited depth of cure in thick applications.
Applications: Surface-mount electronics and small-scale assemblies.
- Example: Dymax’s UV-curable compounds are ideal for automated production lines.
Each type of potting compound offers unique benefits, and the choice depends on the PCB’s operating environment, performance requirements, and budget.
Benefits of Using Potting Compounds for PCBs
Potting compounds provide a range of advantages that enhance PCB performance and longevity:
- Environmental Protection: Shields against moisture ingress, dust, and corrosive chemicals, extending PCB life in harsh conditions like marine or industrial settings.
Eample: xSilicone potting protects outdoor telecom equipment from rain and humidity.
- Mechanical Durability: Absorbs shock and vibration, critical for automotive or aerospace applications where PCBs face constant movement.
Example: Epoxy potting stabilizes components in vehicle engine control modules.
- Electrical Insulation: Prevents short circuits and arcing, ensuring reliable operation in high-voltage or densely packed circuits.
Example: Polyurethane potting insulates medical device PCBs for patient safety.
- Thermal Management: Conducts or insulates heat, protecting components from overheating or cold-induced brittleness.
Example: Thermally conductive epoxy potting dissipates heat in LED drivers.
- Security and Tamper Resistance: Encases sensitive components, deterring tampering or intellectual property theft.
Example: Epoxy potting protects proprietary circuits in military electronics.
- Improved Reliability: Reduces failure rates by mitigating environmental and mechanical stresses, lowering maintenance costs.
Example: Silicone potting enhances the lifespan of solar inverters in renewable energy systems.
These benefits make potting compounds a critical investment for ensuring PCB reliability in challenging applications.
Applications of Potting Compounds for PCBs
Potting compounds are used across diverse industries to protect PCBs in demanding environments. Key applications include:
- Automotive: Encapsulating engine control units, sensors, and infotainment systems to withstand vibration, heat, and oil exposure.
- Aerospace and Defense: Protecting avionics, radar systems, and communication devices from extreme temperatures, altitude, and shock.
- Telecommunications: Shielding outdoor base stations and routers from moisture, UV radiation, and thermal cycling.
- Medical Devices: Ensuring sterility and reliability in diagnostic equipment, implants, and monitoring devices.
- Renewable Energy: Enhancing durability of solar inverters, wind turbine controllers, and battery management systems in harsh outdoor conditions.
- Consumer Electronics: Protecting wearable devices, smart appliances, and IoT gadgets from dust, sweat, and drops.
- Industrial Automation: Safeguarding PLCs, motor drives, and sensors in factories exposed to chemicals, dust, and vibration.
In each case, the potting compound is selected based on the specific environmental and operational challenges faced by the PCB.
Key Considerations for Selecting a Potting Compound
Choosing the right potting compound requires careful evaluation of the PCB’s requirements and operating conditions. Below are the critical factors to consider:
- Environmental Conditions
- Moisture and Chemicals: Epoxy or polyurethane for high resistance to water and solvents; silicone for humid environments.
- Temperature Range: Silicone for extreme temperatures (-50°C to 200°C); epoxy for moderate ranges.
- UV Exposure: Silicone or UV-curable compounds for outdoor applications.
- Mechanical Requirements
- Vibration and Shock: Silicone or polyurethane for flexibility to absorb mechanical stress.
- Rigidity: Epoxy for applications needing structural support, like heavy industrial equipment.
- Electrical Properties
- Dielectric Strength: Ensure high insulation for high-voltage PCBs (e.g., epoxy or polyurethane).
- Conductivity: Avoid conductive fillers unless grounding is required.
- Thermal Management
- Heat Dissipation: Choose thermally conductive compounds (e.g., epoxy with fillers) for high-power PCBs.
- Insulation: Use silicone for low thermal conductivity in temperature-sensitive applications.
- Processing and Application
- Cure Time: UV-curable for fast production; epoxy for longer curing but higher strength.
- Viscosity: Low viscosity for intricate PCBs; high viscosity for larger assemblies.
- Removal/Repair: Silicone or acrylic for reworkable applications; avoid epoxy for permanent encapsulation.
- Cost and Scalability
- Budget: Acrylic for cost-sensitive projects; silicone or epoxy for high-performance needs.
- Production Volume: UV-curable or automated dispensing systems for high-volume manufacturing.
- Regulatory Compliance
- Standards: Ensure compliance with UL, RoHS, or FDA for specific industries (e.g., medical, automotive).
- Flame Retardancy: Select UL94 V-0 rated compounds for fire safety in consumer electronics.
By aligning these factors with the PCB’s requirements, you can select a potting compound that optimizes performance and cost-effectiveness.
Emerging Trends in Potting Compounds for PCBs
The potting compound industry is evolving to meet the demands of modern electronics. Key trends include:
- Thermally Conductive Materials
Advanced epoxy and silicone formulations with fillers (e.g., alumina, boron nitride) improve heat dissipation for high-power PCBs, such as those in electric vehicles and 5G equipment.
- Eco-Friendly Formulations
Manufacturers are developing RoHS-compliant, low-VOC, and recyclable compounds to align with sustainability goals, reducing environmental impact.
- Smart Encapsulants
Integration of sensors or conductive fillers enables real-time monitoring of PCB health, such as temperature or stress, for predictive maintenance.
- Low-Density Compounds
Lightweight potting materials reduce the weight of encapsulated PCBs, critical for aerospace and portable devices.
- Automation-Friendly Solutions
Low-viscosity and UV-curable compounds support automated dispensing systems, speeding up production in high-volume industries.
These trends reflect the industry’s focus on performance, sustainability, and manufacturing efficiency.
Practical Considerations and Best Practices
To maximize the benefits of potting compounds, follow these best practices:
- Surface Preparation: Clean PCBs thoroughly to ensure strong adhesion and prevent voids.
- Mixing Accuracy: For two-part compounds, follow manufacturer ratios precisely to achieve proper curing.
- Void Prevention: Use vacuum degassing or low-viscosity compounds to eliminate air bubbles during potting.
- Curing Conditions: Maintain recommended temperature and humidity for consistent curing results.
- Testing: Verify encapsulation performance with environmental, electrical, and mechanical tests.
- Safety: Use proper ventilation and PPE when handling potting compounds, especially epoxies.
Conclusion
Potting compounds are essential for protecting PCBs from environmental, mechanical, and electrical stresses, ensuring reliability in industries like automotive, aerospace, and renewable energy. Epoxy, silicone, polyurethane, acrylic, and UV-curable compounds each offer unique benefits, and selecting the right type depends on the PCB’s operating conditions, performance needs, and budget. Leading manufacturers like Henkel, Dow, MG Chemicals, Electrolube, and Dymax provide high-quality solutions tailored to diverse applications.
By evaluating factors such as environmental resistance, mechanical properties, and regulatory compliance, and following best practices for application, users can maximize the performance of potted PCBs. Emerging trends like thermally conductive materials, eco-friendly formulations, and automation-friendly solutions are shaping the future of potting compounds, offering enhanced protection and efficiency. With the right potting compound and manufacturer, PCBs can withstand the toughest challenges, delivering reliable performance for critical electronic systems.
For more about choosing the Top Industrial Electronic Adhesives Suppliers, you can pay a visit to DeepMaterial at https://www.pottingcompound.com/ for more info.
Recent Posts
- Potting Compound for PCB
- In – depth Analysis of the Curing Characteristics of Electronic Potting Compounds
- A Comprehensive Analysis of the Environmental Performance of Encapsulating Materials: From Regulations to Practices
- A Comprehensive Analysis of PCB Encapsulation Quality Inspection: Innovative Application of Non-Destructive Testing Technologies
- Analysis of the Improvement of the Seismic and Impact Resistance Performance of PCB by Encapsulation
- A Comprehensive Guide to Evaluating the Reliability of Encapsulation Materials for Encapsulated PCBs
- In-depth Analysis of the Reparability of Encapsulation Materials
- A Comprehensive Analysis of Post-Potting PCB Issues and the Repair and Rework of Potting Materials
- A Comprehensive Analysis of the Compatibility between Encapsulation Materials and PCBs: Exploration of Chemical Reactions and Their Impact on Performance
- How to Ensure the Compatibility between Encapsulation Materials and Various Components on PCBs