Home > Potting Compound > Polyurethane Potting Compounds
Polyurethane Potting Compounds
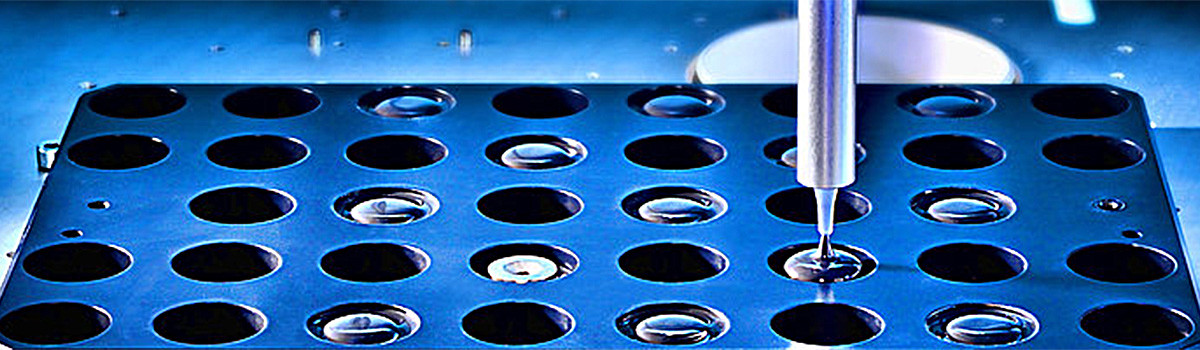
Polyurethane potting compounds have emerged as indispensable materials in various industries, offering exceptional versatility and reliability in electronic encapsulation and protection. As technology advances, the demand for robust and high-performance potting solutions continues to escalate. In this blog post, we delve into the intricacies of polyurethane potting compounds, exploring their applications, benefits, and key considerations.
Table of Contents
ToggleWhat is polyurethane potting compound, and how does it differ from other potting materials?
Choosing the suitable potting material is crucial in electronic encapsulation and protection to ensure durability, reliability, and performance. But what sets polyurethane potting compounds apart from other materials? Let’s delve into this question to uncover polyurethane potting compounds’ unique characteristics and benefits.
Understanding Polyurethane Potting Compound:
- Composition:Polyurethane potting compounds are a type of thermosetting polymer that consists of polyol and isocyanate components. These components react to form a durable and resilient material when cured.
- Versatility:Polyurethane potting compounds exhibit remarkable versatility, making them suitable for various applications across industries such as electronics, automotive, aerospace, and more.
- Properties: One of the distinguishing features of polyurethane potting compounds is their excellent electrical insulation, which makes them ideal for protecting electronic components from moisture, chemicals, and mechanical stress.
- Adhesion:Unlike other potting materials, polyurethane compounds adhere well to various substrates, including metals, plastics, and ceramics, ensuring secure encapsulation and protection of electronic assemblies.
- Flexibility:Polyurethane potting compounds offer flexibility and elasticity, allowing them to accommodate thermal expansion and contraction without compromising the integrity of the encapsulated components.
Differences from Other Potting Materials:
- Epoxy Resins:While epoxy resins are also commonly used for potting applications, polyurethane potting compounds offer superior flexibility and impact resistance, making them more suitable for applications where mechanical stress is a concern.
- Silicone Potting Compounds:Compared to silicone potting compounds, polyurethane potting compounds typically have higher adhesion properties and better resistance to chemicals and solvents, providing enhanced protection in harsh environments.
- Acrylic Resins:Polyurethane potting compounds surpass acrylic resins in toughness and durability, making them a preferred choice for long-term reliability and performance applications.
What are the primary applications of polyurethane potting compounds in electronics?
Polyurethane potting compounds have emerged as indispensable materials in the electronics industry, offering many benefits and applications. Let’s delve into the primary applications of these versatile compounds, which have become synonymous with reliability and performance in electronic devices.
Enhanced Protection:
- Sealing and Encapsulation:Polyurethane potting compounds provide robust sealing and encapsulation solutions, safeguarding electronic components from moisture, dust, chemicals, and mechanical stresses.
- Environmental Protection:They offer excellent resistance to harsh environmental conditions, including temperature extremes, UV exposure, and corrosive atmospheres, ensuring prolonged device durability and reliability.
Improved Performance:
- Thermal Management:These compounds efficiently dissipate heat generated by electronic components, mitigating the risk of overheating and enhancing device performance and longevity.
- Vibration Dampening:Polyurethane potting compounds dampen vibrations and reduce mechanical stress, preventing component displacement or damage, especially in rugged applications or during transportation.
Electrical Insulation:
- Dielectric Properties:Maximizing the safety of electronic components, polyurethane potting compounds provide superior insulation, boasting high dielectric strength and resistance to short circuits and electrical failures.
- Protection Against Arcing:They offer superior arc resistance, which is crucial for applications where electrical arcing poses a potential hazard, such as high-voltage equipment or power distribution systems.
Customization and Versatility:
- Adaptability:Polyurethane potting compounds can be tailored to meet specific application requirements, offering flexibility in terms of viscosity, curing time, and hardness.
- Compatibility:They exhibit compatibility with various substrates, including metals, plastics, and ceramics, facilitating seamless integration into diverse electronic assemblies.
Applications Across Industries:
- Electronics Manufacturing:From consumer electronics to industrial machinery, polyurethane potting compounds find widespread use in the manufacturing of circuit boards, sensors, connectors, and more.
- Automotive Electronics:They play a critical role in automotive electronics, ensuring the reliability and performance of control modules, sensors, and ignition systems in vehicles.
- Renewable Energy:Polyurethane potting compounds contribute to the durability and efficiency of solar panels, wind turbines, and energy storage systems, enabling sustainable energy generation.
How does polyurethane potting enhance the durability and reliability of electronic devices?
In the realm of electronics, durability and reliability are paramount. Enter polyurethane potting compound, a versatile material that protects electronic devices against environmental, mechanical, and electrical threats. Let’s explore how this compound enhances the resilience of electronic devices through six fundamental mechanisms.
Sealing Against Environmental Hazards:
Polyurethane potting compounds create a protective barrier around sensitive electronic components, shielding them from moisture, dust, chemicals, and other environmental contaminants. This sealing action is crucial in extending the lifespan of devices operating in diverse conditions, ranging from industrial settings to outdoor environments.
Mitigating Mechanical Stresses:
Polyurethane potting compounds absorb shocks and vibrations by encapsulating electronic assemblies, reducing the risk of physical damage or component displacement. This dampening effect is particularly beneficial in applications subject to mechanical stresses, such as automotive electronics or portable devices exposed to frequent handling.
Enhancing Thermal Management:
Efficient heat dissipation is essential for maintaining optimal performance and preventing premature failure in electronic devices. Polyurethane potting compounds excel in thermal management, effectively conducting heat away from critical components and dissipating it into the surrounding environment, thus ensuring sustained operation even under high thermal loads.
Safeguarding Against Electrical Failures:
Electrical insulation is paramount in preventing short circuits and electrical malfunctions. Polyurethane potting compounds exhibit high dielectric strength and insulation resistance, effectively isolating conductive elements within electronic assemblies. This insulation capability minimizes the risk of electrical breakdowns, especially in applications exposed to high voltages or fluctuations.
Customized Protection and Adaptability:
One key advantage of polyurethane potting compounds is their versatility. Manufacturers can tailor the properties of these compounds to suit specific application requirements, including viscosity, curing time, and hardness. This customization ensures optimal protection while accommodating the unique needs of different electronic devices and environments.
Ensuring Long-Term Reliability Across Industries:
From consumer electronics to industrial machinery and aerospace systems, polyurethane potting compounds are widely used across diverse industries. Their ability to enhance durability and reliability makes them indispensable in critical applications where operational integrity is non-negotiable. Whether protecting circuit boards in harsh industrial environments or ensuring the longevity of sensors in automotive systems, polyurethane potting compounds play a pivotal role in upholding the performance standards of electronic devices worldwide.
What factors should be considered when selecting a polyurethane potting compound?
Polyurethane potting compounds are widely used in electronic and electrical applications to encapsulate, seal, and protect sensitive components. Choosing the right polyurethane potting compound is essential for guaranteeing peak performance and long-lasting durability in your end product.
Here are the essential factors to consider when making this decision:
Application Requirements:
- Consider the distinct demands of your application, encompassing variables such as variations in temperature, surrounding environmental factors, and the capacity to endure exposure to chemicals.
- Consider factors like flexibility, hardness, and electrical properties required for the intended use.
Physical Properties:
- Evaluate the potting compound’s viscosity and flow characteristics to ensure easy application and complete component coverage.
- Check the cure time and pot life to match the production process requirements and avoid delays or incomplete curing.
Chemical Compatibility:
- Assess the compatibility of the potting compound with materials used in the assembly, including substrates, adhesives, and coatings.
- Ensure resistance to solvents, oils, and other chemicals present in the operating environment to prevent degradation over time.
Thermal Performance:
- Determine the potting compound’s temperature range during operation and choose a formulation with suitable thermal conductivity and stability.
- Look for thermal shock resistance to prevent cracking or delamination under rapid temperature changes.
Electrical Insulation:
- Verify the potting compound’s dielectric strength and insulation properties to maintain electrical integrity and prevent short circuits or leakage currents.
- Consider the presence of any conductive fillers or additives that may affect electrical performance.
Environmental Considerations:
- Assess the impact of factors like humidity, UV exposure, and outdoor conditions on the long-term performance of the potting compound.
- Choose formulations with UV resistance and weather ability for outdoor applications or harsh environments.
Regulatory Compliance:
- Ensure the selected potting compound meets relevant industry standards and regulatory requirements for safety, toxicity, and environmental impact.
- Look for certifications such as UL recognition or RoHS compliance for compatibility with global markets.
Supplier Support and Reliability:
- Partner with a reputable supplier who offers technical support, product customization, and consistent quality assurance.
- Consider availability, lead times, and logistics support to ensure a reliable supply chain.
Can polyurethane potting compounds withstand harsh environmental conditions?
Polyurethane potting compounds are renowned for robustly protecting electronic components in various applications. But can they truly stand up to the rigors of harsh environmental conditions? Let’s delve into this question to uncover the resilience of polyurethane potting compounds:
Understanding Polyurethane Potting Compounds:
- Polyurethane potting compounds are versatile materials used for encapsulating and protecting electronic components.
- They consist of two main components, polyol, and isocyanate, which react to form a tough and durable polymer.
Resilience in Harsh Environments:
- Temperature Extremes:Polyurethane potting compounds exhibit remarkable resistance to temperature extremes, ranging from cold to scorching heat. Capable of enduring temperatures spanning from -40°C to well beyond 150°C, these materials are adeptly suited for both Arctic tundras and scorching desert landscapes.
- Moisture and Humidity:These compounds form a tight seal around electronic components, shielding them from moisture and humidity. This feature prevents corrosion and ensures the longevity of the encapsulated devices, even in highly humid conditions.
- Chemical Exposure:Polyurethane potting compounds resist various chemicals, including oils, fuels, solvents, and acids. This attribute is crucial for applications where electronic devices may come into contact with aggressive chemicals, such as automotive, marine, or industrial settings.
- UV Resistance:Some polyurethane formulations are specially engineered to resist UV degradation, making them suitable for outdoor applications exposed to sunlight. This UV resistance helps maintain encapsulated electronics’s structural integrity and electrical performance over extended periods.
Applications:
- Automotive Electronics: Polyurethane potting compounds are commonly used to protect electronic components in vehicles, where they are exposed to temperature fluctuations, moisture, and various chemicals.
- Aerospace and Defense:In aerospace and defense applications, where reliability is paramount, polyurethane potting compounds provide robust protection against harsh environmental conditions, including vibration, shock, and extreme temperatures.
- Renewable Energy:Electronic components in solar panels, wind turbines, and battery systems are often potted with polyurethane compounds to ensure durability and reliability in outdoor environments.
- Industrial Electronics:From control systems to sensors and transmitters, industrial electronics benefit from the protective properties of polyurethane potting compounds, safeguarding them against harsh operating conditions in factories and plants.
Are there different types of polyurethane potting compounds available?
Polyurethane potting compounds are versatile materials used for encapsulating and protecting electronic components.
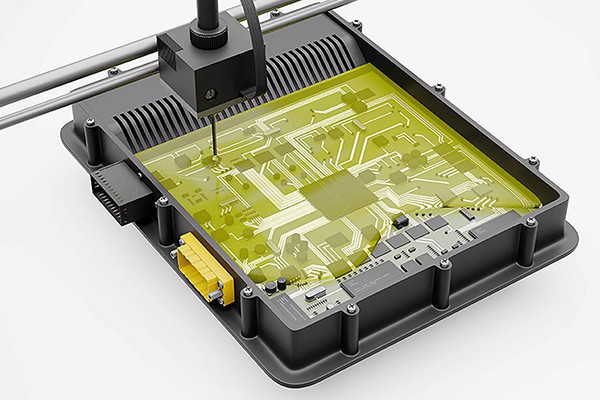
Types of Polyurethane Potting Compounds
Flexible Polyurethane Potting Compounds:
- Designed to provide cushioning and vibration dampening.
- It is ideal for applications where components experience mechanical stress or thermal cycling.
- It is commonly used in automotive, sensor assemblies, and outdoor electronics.
Rigid Polyurethane Potting Compounds:
- Offer superior protection against impact and environmental factors.
- Provide excellent electrical insulation properties.
- Suitable for applications requiring structural support and dimensional stability, such as in power supplies and transformers.
Thermally Conductive Polyurethane Potting Compounds:
- Formulated with additives to enhance thermal conductivity.
- Effective in dissipating heat from sensitive electronic components.
- It is ideal for applications where heat management is critical, such as LED lighting and power electronics.
Optically Clear Polyurethane Potting Compounds:
- Transparent formulations maintain optical clarity even after the curing process is complete.
- Used in applications where visibility of components is necessary, such as LED displays and optical sensors.
- Provide excellent UV resistance and durability.
Factors Influencing Selection
- Environmental Conditions:Consider factors like temperature variations, exposure to moisture, and chemical exposure.
- Mechanical Requirements:Determine the level of flexibility or rigidity needed to protect components from mechanical stress.
- Thermal Management:Evaluate the application’s heat dissipation requirements.
- Electrical Insulation:Ensure adequate electrical insulation properties to prevent short circuits and electrical failures.
- Transparency:If optical clarity is essential, opt for precise formulations.
How does the curing process of polyurethane potting compounds impact their performance?
Polyurethane potting compounds are widely used in various industries for their excellent properties, such as flexibility, durability, and resistance to moisture and chemicals. However, one crucial aspect that significantly impacts their performance is the curing process. In this article, we delve into how the curing process influences polyurethane potting compounds’ performance.
Impact on Mechanical Properties:
The curing process directly affects the mechanical properties of polyurethane potting compounds. Proper curing ensures optimal bonding between molecules, enhancing strength, toughness, and resistance to mechanical stress. Inadequate curing can lead to insufficient cross-linking, compromising the material’s mechanical integrity and durability.
Influence on Electrical Properties:
Their outstanding electrical insulation properties make polyurethane potting compounds a prevalent choice for electronic applications across various industries. The curing process significantly influences these properties. Proper curing ensures uniform distribution of filler materials and minimizes voids, which is crucial for maintaining consistent dielectric strength and insulation resistance. Incomplete curing may lead to the formation of microvoids or weak spots, increasing the risk of electrical failures.
Effect on Chemical Resistance:
The chemical resistance of polyurethane potting compounds is vital for applications exposed to harsh environments or chemical exposure. The curing process is critical in determining the material’s chemical resistance. Properly cured compounds form a dense, impenetrable structure that shields against moisture, solvents, oils, and other corrosive substances. Incomplete curing can result in porous structures, making the material susceptible to chemical ingress and degradation over time.
What are the key advantages of using polyurethane potting compounds over alternatives?
In electronic encapsulation and protection, polyurethane potting compounds have emerged as a leading choice for manufacturers. These compounds revolutionize how sensitive electronic components are safeguarded by offering many advantages over traditional alternatives. Let’s delve into the key benefits that make polyurethane potting compounds the go-to solution in various industries.
Enhanced Protection and Insulation
Polyurethane potting compounds protect against moisture, chemicals, and environmental factors.
- They form a durable barrier around electronic components, shielding them from dust, debris, and corrosion.
- Excellent insulation properties safeguard against electrical failures, ensuring optimal performance even in challenging conditions.
Flexibility and Adaptability
- With their flexible nature, polyurethane potting compounds conform seamlessly to complex shapes and contours of electronic assemblies.
- They accommodate thermal expansions and contractions, reducing stress on delicate components.
- This flexibility extends the lifespan of electronic devices, making them more resilient to mechanical shocks and vibrations.
Optimized Performance
- Polyurethane potting compounds exhibit superior thermal conductivity, efficiently dissipating heat generated by electronic components.
- They maintain stable electrical properties over various temperatures, ensuring consistent performance in diverse environments.
- These compounds minimize signal interference and crosstalk, enhancing the reliability and functionality of electronic systems.
Ease of Application
- In various viscosities, polyurethane potting compounds offer versatility in application methods such as casting, dipping, or dispensing.
- They cure rapidly at room temperature or with heat, facilitating streamlined production processes.
- Minimal shrinkage during curing eliminates voids and ensures complete component encapsulation, enhancing overall protection.
Environmental Sustainability
- Many polyurethane potting compounds, formulated with eco-friendliness, contain minimal volatile organic compounds (VOCs) and hazardous substances, aligning with environmental standards.
- Their longevity and durability contribute to reducing electronic waste by prolonging the lifespan of electronic devices.
- Manufacturers can opt for recyclable or biodegradable formulations, aligning with sustainable practices and regulations.
Cost-Efficiency
- Despite their advanced properties, polyurethane potting compounds offer cost-effective solutions for electronic encapsulation.
- Their long-lasting durability diminishes the necessity for frequent repairs or replacements, ultimately resulting in substantial cost savings over the long term.
- Manufacturers can optimize material usage and production efficiency, further enhancing cost-effectiveness.
Can polyurethane potting compounds be customized for specific applications?
Across diverse industries, polyurethane potting compounds are crucial as versatile materials. They encapsulate electronic components and protect against environmental factors like moisture, chemicals, and mechanical stress.
But can these compounds be tailored to meet the specific needs of different applications? Let’s delve into the customization possibilities of polyurethane potting compounds.
Customization Options:
- Chemical Composition: One primary way to customize polyurethane potting compounds is to alter their chemical composition. Manufacturers can adjust the ingredients to enhance properties like flexibility, adhesion, thermal conductivity, and resistance to specific chemicals.
- Hardness and Flexibility:Polyurethane potting compounds can be formulated to achieve different levels of hardness and flexibility. A higher durometer (Shore hardness) is preferred for applications requiring rigid encapsulation, while softer compounds are suitable for applications where flexibility is crucial.
- Curing Time:Manufacturers can control the curing time of polyurethane potting compounds by adjusting the catalyst concentration or using additives. It allows for customization based on production requirements, whether fast for rapid turnaround or slower for intricate molds.
- Thermal Properties:Customizing thermal conductivity and resistance is vital for applications exposed to extreme temperatures. Polyurethane potting compounds can be tailored to withstand high temperatures or provide better thermal insulation, ensuring optimal performance in diverse environments.
- Environmental Resistance:Tailoring polyurethane potting compounds to resist specific ecological factors such as moisture, solvents, UV radiation, and harsh chemicals ensures longevity and reliability in challenging conditions.
Applications of Customized Polyurethane Potting Compounds:
- Electronics:Safeguarding sensitive electronic components across diverse sectors, such as automotive, aerospace, telecommunications, and consumer electronics, customized potting compounds provide protection against moisture, vibration, and thermal shock.
- Renewable Energy:In solar panels and wind turbines, customized polyurethane potting compounds provide weather resistance and electrical insulation, extending the lifespan and efficiency of renewable energy systems.
- Automotive:Customized potting compounds encapsulate sensors, connectors, and control modules in automotive electronics, ensuring reliable performance under extreme temperatures, vibration, and chemical exposure.
- Medical Devices:Polyurethane potting compounds customized for medical devices offer biocompatibility, sterilization resistance, and protection against bodily fluids, meeting stringent regulatory standards for patient safety.
What precautions should be taken during the handling and application of polyurethane potting compounds?
Polyurethane potting compounds offer a versatile solution for encapsulating electronic components, providing protection from moisture, dust, and other environmental factors. However, working with these compounds requires careful handling and application to ensure safety and effectiveness. Here are some essential precautions to consider:
- Ventilation:Adequate ventilation is crucial when handling polyurethane potting compounds. Work in a well-ventilated area or use exhaust fans to reduce fume exposure.
- Personal Protective Equipment (PPE): When handling polyurethane potting compounds, wear suitable personal protective equipment (PPE) such as gloves, safety goggles, and a respirator. A respirator with organic vapor cartridges helps filter out harmful airborne particles.
- Avoid Skin Contact:Prevent skin contact with uncured polyurethane potting compounds. These materials can cause skin irritation or allergic reactions in some individuals. If skin contact occurs, wash the affected area thoroughly with soap and water. Seek medical attention if irritation persists.
- Temperature and Humidity Control:Maintain recommended temperature and humidity levels during application and curing. Extreme temperatures or high humidity can affect polyurethane potting compounds’ performance and curing process. Follow manufacturer guidelines for optimal conditions.
- Mixing Ratio:Accurately measure and mix the components of the potting compound according to the manufacturer’s instructions. Deviating from the recommended mixing ratio can result in improper curing and compromised performance. Use calibrated dispensing equipment to ensure precision.
- Application Technique:Apply the potting compound evenly and without trapping air bubbles. Proper application techniques, such as vacuum degassing or pressure casting, can help eliminate air pockets and improve the integrity of the encapsulation. Work systematically to cover the components thoroughly.
- Curing Time:Allow sufficient curing time per the product specifications before subjecting the encapsulated components to operational conditions. Rushing the curing process can lead to incomplete curing and reduced effectiveness of the potting compound.
- Storage and Shelf Life:Polyurethane potting compounds should be kept out of direct sunshine and heat sources in a cool, dry location. Proper storage conditions help maintain the integrity and shelf life of the material.
How do temperature fluctuations affect the properties of polyurethane potting compounds?
Temperature fluctuations can significantly impact the properties and performance of polyurethane potting compounds commonly used for encapsulating electronic components. These fluctuations can affect various material aspects, including viscosity, curing time, and mechanical strength.
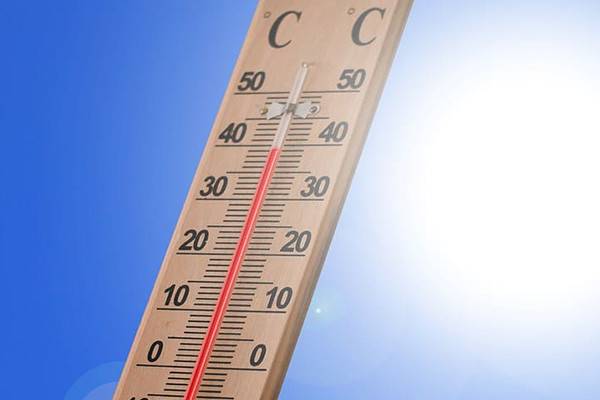
One primary way temperature fluctuations influence polyurethane potting compounds is through changes in viscosity. As temperatures rise, the viscosity of the uncured compound typically decreases, making it easier to handle and apply. Conversely, lower temperatures can cause the compound to become more viscous, potentially making it challenging to dispense and ensure proper electronic component coverage. Maintaining the recommended temperature range during application is critical to achieving optimal viscosity and ensuring uniform encapsulation.
Additionally, temperature fluctuations can impact the curing process of polyurethane potting compounds. These materials typically undergo a chemical reaction to cure, transforming from liquid to solid. Higher temperatures can accelerate the curing process, leading to shorter curing times. Conversely, lower temperatures may slow curing, prolonging the required time for the compound to achieve full strength and durability. Failure to adhere to the recommended curing conditions can result in incomplete curing, compromising the integrity of the encapsulation and potentially exposing electronic components to environmental hazards.
Temperature variations can also impact mechanical attributes like flexibility and tensile strength. Polyurethane potting compounds are designed to provide robust protection for electronic assemblies, with properties tailored to withstand various operating conditions. However, exposure to extreme temperatures can alter these properties, potentially leading to decreased mechanical strength or increased brittleness. It’s essential to consider the anticipated temperature range the encapsulated device will encounter during operation and select a potting compound with suitable thermal stability to ensure long-term performance.
Furthermore, temperature fluctuations can impact the dimensional stability of polyurethane potting compounds. Temperature variations can cause the material to expand or contract, potentially resulting in dimensional changes that affect the fit and functionality of encapsulated components. Selecting a potting compound with a low coefficient of thermal expansion and ensuring proper curing under controlled temperature conditions are crucial steps to mitigate the risk of dimensional instability.
Are there any limitations or drawbacks associated with polyurethane potting compounds?
Polyurethane potting compounds have emerged as versatile solutions in various industries, offering exceptional protection and insulation for electronic components. However, despite their numerous advantages, certain limitations and drawbacks warrant consideration.
Advantages of Polyurethane Potting Compounds:
- Excellent Insulation:Polyurethane potting compounds boast high dielectric strength, making them ideal for insulating sensitive electronic components against environmental factors and electrical interference.
- Chemical Resistance:They exhibit robust resistance to various chemicals, ensuring prolonged durability in harsh operating environments.
- Mechanical Protection: Because they effectively encapsulate components, polyurethane potting compounds provide reliable mechanical protection against vibration, shock, and impact.
Limitations and Drawbacks:
While polyurethane potting compounds offer compelling benefits, they are not without limitations:
- Limited Temperature Range:One significant drawback is their susceptibility to temperature extremes. Polyurethane potting compounds may experience degradation or loss of properties at high and low temperatures, limiting their applicability in extreme environments.
- Hygroscopic Nature:Due to their tendency to be hygroscopic, polyurethane compounds can gradually absorb moisture from their surroundings. This moisture absorption can compromise the insulation properties and lead to electrical failures in the long run.
- Potential for Outgassing: During curing and operation, polyurethane potting compounds may release volatile components, resulting in outgassing. This outgassing can be problematic in applications where cleanliness and contamination control are critical, such as in aerospace or medical devices.
Mitigating Drawbacks:
Despite these limitations, there are strategies to mitigate the drawbacks associated with polyurethane potting compounds:
- Temperature Stabilization:Employing temperature stabilization techniques, such as incorporating thermal additives or selecting formulations with a broader temperature range, can enhance the performance of polyurethane potting compounds in extreme conditions.
- Moisture Barrier Coatings:Applying moisture barrier coatings to the encapsulated components or using moisture-resistant formulations can mitigate the effects of moisture absorption, preserving the integrity of the insulation over time.
- Careful Selection and Testing:Thoroughly evaluating the compatibility of polyurethane potting compounds with specific substrates and conducting rigorous testing under simulated operating conditions can help identify and address potential issues before deployment.
Can polyurethane potting compounds be recycled or disposed of responsibly?
Polyurethane potting compounds have long been favored for their exceptional protection and insulation properties in various industries. However, as sustainability becomes an increasingly pressing concern, questions arise about the end-of-life management of these materials. Can polyurethane potting compounds be recycled, or how can they be disposed of responsibly?
Recycling Polyurethane Potting Compounds:
- Challenges:Polyurethane potting chemicals are challenging to recycle because of their intricate chemical makeup and the difficulty of extracting them from enclosed components.
- Limited Options:Traditional methods such as mechanical or chemical recycling are often impractical or inefficient for polyurethane potting compounds, primarily due to the risk of damaging the encapsulated electronics during the recycling process.
Responsible Disposal Practices:
- Incineration:Incineration is a standard disposal method for polyurethane potting compounds. When adequately incinerated at high temperatures, these compounds can be converted into energy with minimal environmental impact. However, this process requires specialized facilities and careful emission controls to prevent the release of harmful pollutants.
- Landfill Disposal:Disposal is widely available, but it’s generally considered the least environmentally friendly method. Polyurethane potting compounds may take a long time to degrade in landfills, potentially releasing hazardous substances into the soil and groundwater over time.
- Chemical Treatment:Some specialized facilities offer chemical treatment processes to break down polyurethane potting compounds into less harmful byproducts. However, these processes are often costly and may not be readily accessible in all regions.
Promoting Sustainability:
- Development of Eco-Friendly Alternatives:Research and development efforts are underway to create more sustainable alternatives to traditional polyurethane potting compounds. These alternatives aim to maintain polyurethane’s performance benefits while reducing environmental impact and facilitating easier recycling or disposal.
- Education and Awareness:Increasing awareness among manufacturers and consumers about the importance of responsible disposal practices and the environmental impact of polyurethane potting compounds can encourage the adoption of more sustainable approaches.
What role do polyurethane potting compounds play in the automotive industry?
In the intricate world of automotive engineering, durability is paramount. Every component, from the engine to the most miniature sensor, must withstand constant use, extreme temperatures, and harsh environmental conditions. Enter polyurethane potting compounds – unsung heroes in the automotive industry, providing essential protection and reliability.
Protective Shield:
- Polyurethane potting compounds act as a protective shield, encasing sensitive electronic components within the vehicle.
- They form a durable barrier against moisture, chemicals, vibrations, and mechanical shocks, safeguarding critical electronics from external hazards.
Versatile Applications:
Polyurethane potting compounds find application across various automotive components, including:
- Engine control modules
- Transmission sensors
- ABS brake systems
- Airbag sensors
- LED lighting systems
- Onboard entertainment systems
Their versatility allows engineers to customize formulations to meet specific performance requirements, ensuring compatibility with different substrates and operating conditions.
Thermal Management:
- In the automotive realm, temperature fluctuations are inevitable, ranging from scorching heat to cold.
- Polyurethane potting compounds offer excellent thermal conductivity, dissipating heat away from sensitive electronics.
- By maintaining optimal operating temperatures, these compounds prevent overheating and thermal stress, extending critical components’ lifespan.
Mechanical Stability:
- Vibrations and mechanical shocks are common challenges automotive electronics face, particularly in off-road or high-performance vehicles.
- Polyurethane potting compounds provide superior mechanical stability, anchoring components securely in place and dampening vibrations.
- This stability ensures consistent performance under demanding conditions, enhancing the overall durability of automotive systems.
Environmental Resilience:
- From corrosive road salts to aggressive chemicals encountered during maintenance, automotive electronics are exposed to various environmental aggressors.
- Polyurethane potting compounds offer exceptional resistance to chemicals, oils, solvents, and UV radiation, maintaining the integrity of encapsulated components.
- Their resilience against environmental factors ensures reliable performance and minimizes the risk of premature failures in automotive applications.
How do polyurethane potting compounds contribute to the advancement of renewable energy technologies?
Polyurethane potting compounds are pivotal in the evolution of renewable energy technologies. These versatile materials provide crucial protection and insulation for electronic components, ensuring the reliability and longevity of devices used in solar, wind, and other renewable energy systems. Let’s delve into how polyurethane potting compounds contribute to the advancement of renewable energy:
Enhanced Durability:
- Polyurethane potting compounds resist environmental factors such as moisture, temperature fluctuations, and UV radiation.
- They provide a protective barrier against corrosive agents, extending the lifespan of sensitive electronic components in renewable energy systems.
Optimized Performance:
- By encapsulating delicate electronics, polyurethane potting compounds prevent damage from vibrations and mechanical stress, ensuring consistent performance in harsh operating conditions.
- These compounds maintain electrical insulation properties even under extreme temperatures, enhancing the efficiency and reliability of renewable energy devices.
Seamless Integration:
- Polyurethane potting compounds are formulated to flow easily into intricate spaces, precisely encapsulating electronic assemblies.
- Their low viscosity allows for complete component coverage, eliminating voids and air pockets that could compromise the functionality of renewable energy systems.
Environmental Sustainability:
- Many polyurethane potting compounds are formulated with bio-based or recycled materials, aligning with the eco-friendly ethos of renewable energy technologies.
- Their long-lasting protection reduces the need for frequent maintenance or replacement of electronic components, contributing to resource conservation and waste reduction.
Innovative Applications:
- Polyurethane potting compounds enable the miniaturization of electronic devices, facilitating the development of compact and efficient renewable energy systems.
- These materials support electronics integration in challenging environments, expanding the possibilities for renewable energy deployment in remote or harsh locations.
Are there any emerging trends or innovations in the field of polyurethane potting compounds?
Polyurethane potting compounds have long been valued for their reliability and versatility in protecting electronic components. Several new developments and trends are changing the market for polyurethane potting compounds as industries and technology progress. Let’s take a closer look at some of these trends:
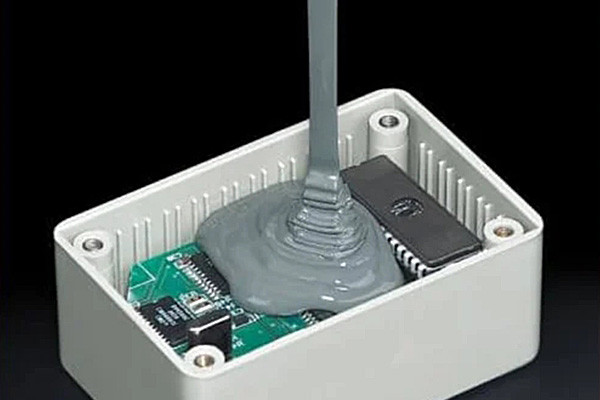
Environmentally Friendly Formulations:
- With growing concerns about sustainability, there is a rising demand for polyurethane potting compounds formulated with bio-based or recycled materials.
- Manufacturers are exploring alternative raw materials and production methods to reduce environmental impact without compromising performance.
Enhanced Thermal Conductivity:
- Better heat management qualities are required for polyurethane potting solutions as electronic devices get smaller and more powerful.
- Innovations in thermal conductive fillers and additives enable the development of compounds that efficiently dissipate heat, ensuring optimal performance and reliability of electronic assemblies.
Ultra-Low Viscosity Compounds:
- Industries such as automotive and aerospace are driving the demand for polyurethane potting compounds with ultra-low viscosity.
- These compounds can penetrate densely packed electronic assemblies more effectively, minimizing voids and improving encapsulation.
Advanced Cure Systems:
- Traditional two-part polyurethane potting compounds require precise mixing and curing conditions. Emerging innovations include one-part systems with moisture-cure or UV-cure capabilities.
- These advanced cure systems offer faster processing times and greater flexibility in manufacturing processes, contributing to increased efficiency and productivity.
Customized Solutions for Specific Applications:
- More and more manufacturers are providing specialized formulations to fit the demands of particular applications and industries.
- From extreme temperature resistance to enhanced chemical compatibility, these specialized polyurethane potting compounds address the diverse needs of industries ranging from renewable energy to medical devices.
What are the cost considerations associated with using polyurethane potting compounds?
Polyurethane potting compounds are versatile materials used in various industries to encapsulate electronic components. While they offer exceptional properties such as excellent electrical insulation, moisture resistance, and mechanical protection, understanding the cost considerations associated with their use is crucial for businesses. Let’s delve into the factors that influence the cost of utilizing polyurethane potting compounds:
Material Cost:
- Polyurethane potting compounds come in various formulations with differing costs based on their specific properties.
- Specialty formulations designed for extreme environments or specific performance requirements may incur higher material costs.
Application Efficiency:
- Proper application techniques and equipment ensure efficient usage of the potting compound, minimizing wastage.
- Training personnel on correct application methods can optimize material usage and reduce overall costs.
Equipment Investment:
- Utilizing polyurethane potting compounds may require initial investment in dispensing equipment such as pumps, mixers, and metering systems.
- While these investments can add to upfront costs, they contribute to consistent and precise application, reducing material waste in the long run.
Labor Costs:
- Labor costs associated with preparing, mixing, and applying polyurethane potting compounds should be factored into the overall cost analysis.
- Efficient workflow management and trained personnel can minimize labor expenses.
Regulatory Compliance:
- Compliance with environmental regulations and safety standards may necessitate additional costs for handling, disposal, or recycling unused or waste material.
- Selecting environmentally friendly formulas or recycling initiatives may have more significant upfront expenses, but they can save money over time and positively impact the environment.
Performance and Durability:
- While initial costs are essential, polyurethane potting compounds’ long-term performance and durability must be considered.
- Investing in high-quality materials with superior protection and longevity can reduce maintenance and replacement costs.
How do manufacturers ensure quality and consistency in polyurethane potting compound production?
Polyurethane potting compounds are crucial in various industries, providing insulation, protection, and stability to electronic components. On the other hand, maintaining strict standards and paying close attention to detail are necessary to produce work of consistently high quality. Here’s how manufacturers ensure top-notch quality and consistency:
Precise Formulation:
- Manufacturers meticulously formulate polyurethane potting compounds, ensuring the right blend of ingredients for desired properties.
- Exact measurements of raw materials such as polyols, isocyanates, additives, and catalysts are crucial for consistent performance.
Quality Raw Materials:
- Selecting high-quality raw materials is paramount to ensure the integrity of the final product.
- Manufacturers source materials from trusted suppliers with proven track records to maintain consistency and reliability.
Tight Quality Control:
- Throughout the whole production process, stringent quality control protocols are implemented.
- Thorough testing procedures assess qualities in terms of their electrical, chemical, and physical aspects to satisfy client requirements and industry standards.
Advanced Mixing Techniques:
- Utilization of state-of-the-art mixing equipment ensures homogeneity and uniformity in the potting compound.
- Automated systems precisely control mixing parameters, minimizing variations and defects.
Temperature and Humidity Control:
- Environmental variables, including humidity and temperature, can significantly impact the characteristics of polyurethane compounds.
- Manufacturers maintain controlled environments to optimize curing and minimize batch-to-batch variability.
Continuous Monitoring and Adjustment:
- Real-time monitoring systems track critical parameters throughout the production process.
- Any deviations from predefined benchmarks trigger immediate adjustments, ensuring consistency and quality.
Robust Quality Assurance:
- Comprehensive quality assurance protocols include batch testing, sample analysis, and performance evaluations.
- Continuous improvement initiatives drive enhancements in processes and product performance.
Compliance with Industry Standards:
- Manufacturers ‘ adherence to industry regulations and standards is non-negotiable.
- Certifications such as ISO and UL demonstrate commitment to quality and reliability.
What are the long-term performance characteristics of polyurethane potting compounds?
Polyurethane potting compounds have emerged as a cornerstone in various industries, offering unparalleled versatility and durability in protecting electronic components. Understanding the long-term performance characteristics of these compounds is crucial for ensuring reliability and functionality in demanding applications.
Durability Under Harsh Conditions
One of the most significant advantages of polyurethane potting compounds is their exceptional durability, even in harsh environmental conditions. These compounds form a robust protective barrier around electronic assemblies, shielding them from moisture, chemicals, vibrations, and thermal cycling. This durability ensures critical components remain operational over extended periods, reducing maintenance costs and downtime.
Thermal Stability
Polyurethane potting compounds exhibit remarkable thermal stability, making them ideal for applications subjected to extreme temperature fluctuations. Whether exposed to high heat or sub-zero conditions, these compounds maintain their structural integrity, preventing thermal stresses from compromising the performance of encapsulated electronics. This thermal resilience ensures consistent operation in environments where temperature variations are common.
Chemical Resistance
In industries where exposure to chemicals is inevitable, the chemical resistance of potting compounds is paramount. Polyurethane potting compounds demonstrate excellent Resistance to various chemicals, including solvents, fuels, oils, and acids. This Resistance protects electronic components from corrosion and maintains their electrical properties, ensuring uninterrupted functionality in chemically aggressive environments.
Mechanical Strength
The mechanical strength of polyurethane potting compounds contributes significantly to the long-term performance of encapsulated electronics. These compounds possess high tensile and flexural strength, effectively absorbing mechanical shocks and vibrations encountered during operation or transportation. By mitigating mechanical stress, polyurethane potting compounds prolong the lifespan of electronic assemblies, enhancing their reliability and robustness.
Aging Resistance
A key consideration for long-term performance is the ability of potting compounds to resist degradation over time. Polyurethane potting compounds exhibit exceptional aging resistance, maintaining their properties and performance characteristics over extended periods.
How can businesses benefit from integrating polyurethane potting compounds into their product development processes?
As businesses strive to create standout products, the integration of advanced materials becomes paramount. One such material that holds immense potential is polyurethane potting compounds. These versatile compounds offer many benefits, making them a valuable asset in product development processes across various industries.
Enhanced Protection and Durability
- Polyurethane potting compounds provide superior protection against moisture, chemicals, and mechanical stresses, safeguarding sensitive electronic components.
- The robust nature of polyurethane enhances the durability of products, ensuring longevity and reliability even in harsh environments.
Improved Performance and Functionality
- By encapsulating electronic assemblies, polyurethane potting compounds prevent damage from vibrations and shocks, improving overall performance.
- These compounds offer excellent thermal conductivity, dissipating heat efficiently and maintaining optimal operating temperatures for electronic devices.
- With customizable formulations, businesses can tailor the properties of polyurethane potting compounds to meet specific application requirements, enhancing functionality and versatility.
Cost-Efficiency and Sustainability
- Polyurethane potting compounds offer long-term protection that minimizes the need for frequent repairs or replacements, which saves businesses money.
- As environmentally friendly options become increasingly important, polyurethane compounds’ recyclability and low VOC (volatile organic compound) emissions align with sustainability goals.
Streamlined Production Processes
- Polyurethane potting compounds can be applied using various methods such as casting, molding, or dispensing, offering flexibility in manufacturing processes.
- Rapid curing formulations enable faster production cycles, reducing time-to-market for new products and enhancing competitiveness.
Flexibility Throughout Sectors
- Polyurethane potting compounds have proven their versatility and effectiveness in various industries, such as consumer electronics, automotive, aerospace, and renewable energy.
- Whether used to seal connectors in automotive electronics or protect solar panel junction boxes, these compounds offer solutions to critical challenges faced by businesses in different sectors.
Conclusion
In conclusion, polyurethane potting compounds stand as pillars of strength in the realm of electronic encapsulation, offering unmatched protection and reliability. As industries evolve and demand grows, the versatility and adaptability of these compounds continue to shine, paving the way for innovation and advancement across various sectors. By understanding their properties, applications, and considerations, businesses can harness the full potential of polyurethane potting compounds to elevate their products and ensure lasting performance in the face of ever-changing challenges.
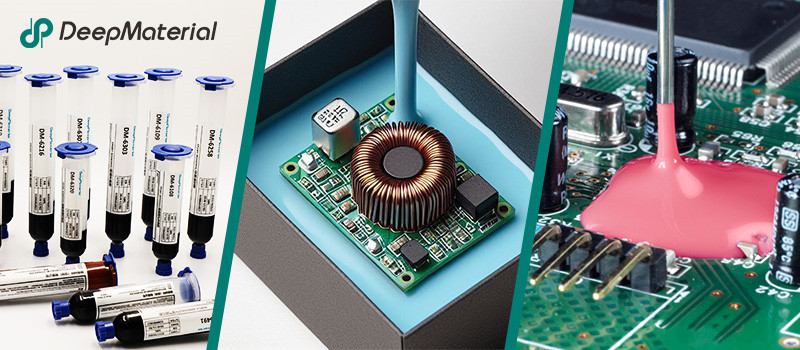
About DeepMaterial
DeepMaterial is a trusted supplier of encapsulant materials that are used in electronics manufacturing worldwide. From chip on board encapsulants such as glob top material to conformal coatings, underfills, low pressure molding, and potting solutions, DeepMaterial offers a full range of circuit board protection materials that effectively protect circuit boards while help reduce costs. More…Deepmaterial is a the manufacturer of epoxy adhesives including hardeners, metalbond, and metal filled resins. Structural, toughened medium viscosity, and non-sag adhesives are also offered. Some adhesives are resistant to thermal shock, chemical, vibration dampening, and impact. Suitable for metals, plastics, wood, and ceramics. Serves electronics, aerospace, automotive, tooling, marine, and construction industries. REACH and RoHS compliant. FDA approved. UL listed. Meets military specifications. We are the one of best adhesive manufacturers in China.
Blogs & News
Potting compounds are at the frontline of electronics assembly, delivering effective protection in challenging environmental conditions while improving mechanical strength and offering high electric insulation. Used within a variety of industries, electrical potting compounds are found within a broad range of consumer electronics, as well as used in applications across the automotive, aerospace, and other industries where electronic assemblies are prevalent.
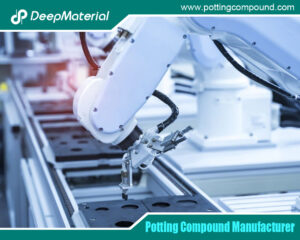
How To Choose Between Potting And Conformal Coating?
Protection of printed circuit boards (PCBs) is most often achieved with either potting or conformal coating. The selection of which method to use depends upon
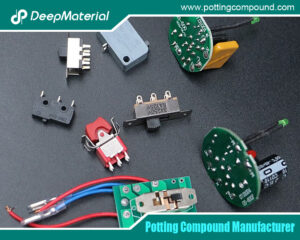
Why are Silicone Potting Compounds Used in Electronics Products?
Potting compounds are one of the key materials used to safeguard sensitive as well as critical electronics components from a variety of threats. Silicone-based potting
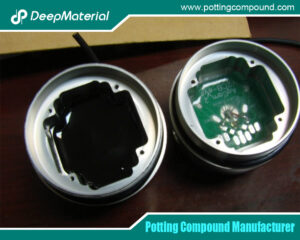
Potting compound for electronics
View Original In electronics, potting may be a process of filling an entire electronic assembly with a solid or gelatinous compound for top voltage assemblies
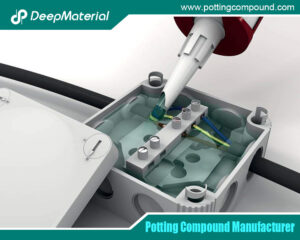
What Is Conformal Coating?
Conformal coatings are protective, non-conductive dielectric layers that are added to a circuit board or electronic device. thermally-conductive-potting The coating “conforms” to the object being
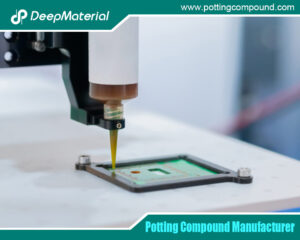
Electronics Potting & Encapsulation
No matter what the specific application or industry, protecting electronic components is crucial for ensuring long-lasting system durability and functionality. Available in various formats including
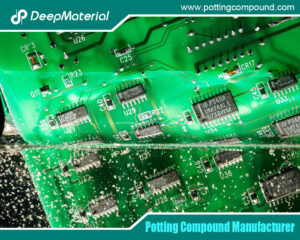
Encapsulation Considerations
If the potting material contains air inclusions or ‘voids’, then it may not be such an effective method of protection. Voids can reduce the insulation