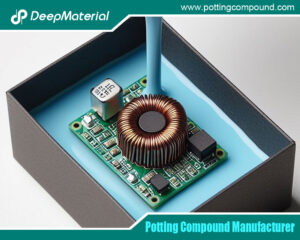
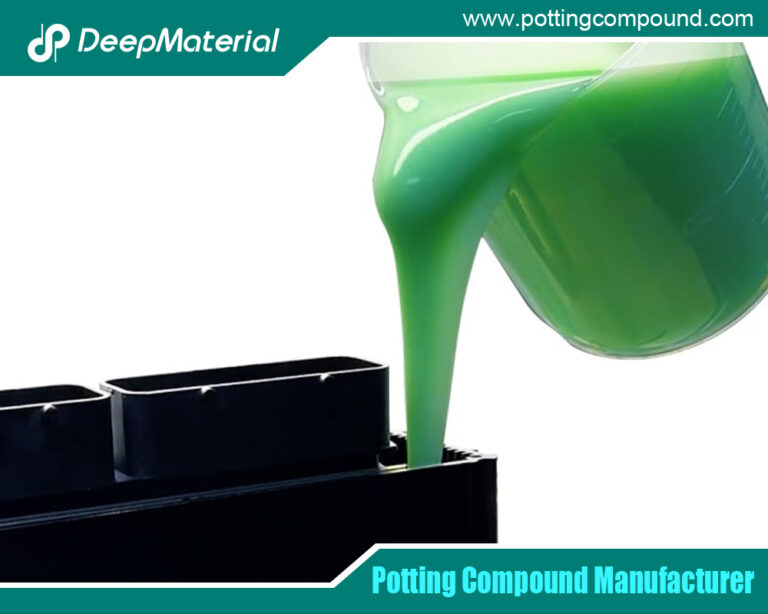
Electronic Potting Material Manufacturer: A Comprehensive Overview
- Electronic Potting Material Manufacturer
- August 16, 2024
- Automotive potting material manufacturers, Benefits of Potting Electronics, circuit board potting, circuit board potting compound, Connector Potting Compound, custom automated electronics potting, customize china electronic potting silicone factories, customize china electronic potting silicone manufacturer, deepmaterial PCB Potting, deepmaterial potting compound, electrical potting compound, electronic encapsulant potting compounds, electronic epoxy encapsulant potting compounds, electronic potting compound, electronic potting material, electronic potting material manufacturer, Electronic Potting Process, electronic potting silicone, electronic potting silicone china fabrication, electronic potting silicone china manufacturing, electronic potting silicone manufacturer, electronic potting silicone manufacturers china, electronic potting silicone products china companies, electronic potting silicone supplier, Epoxy potting material manufacturers, potting material manufacturer, potting material manufacturers
Electronic Potting Material Manufacturer: A Comprehensive Overview
The electronic potting material manufacturing industry plays a critical role in ensuring the reliability and longevity of electronic devices. Potting materials protect sensitive electronic components from environmental hazards, mechanical shock, and electrical interference. This article delves into the intricacies of electronic potting material manufacturing, exploring the materials used, the manufacturing process, applications, and the industry’s future.
Introduction to Potting Materials
What Are Potting Materials?
Potting materials are compounds encapsulating electronic components, protecting them from moisture, dust, chemicals, and mechanical stress. These materials also offer thermal and electrical insulation, enhancing the performance and durability of electronic devices.
Types of Potting Materials
- Epoxy Resins: Known for their excellent adhesion, chemical resistance, and mechanical properties, they are widely used in high-performance applications. They are suitable for harsh environments due to their durability and robustness.
- Polyurethane Resins: These flexible materials provide good moisture resistance and electrical insulation. Polyurethane resins are ideal for applications where components may be subject to mechanical stress or vibration.
- Silicone Resins: Silicone potting materials offer high-temperature resistance and flexibility. They are suitable for applications requiring long-term stability under varying thermal conditions.
- Acrylics: Acrylic potting compounds are known for their fast curing times and clarity. They are often used in applications where visual inspection of components is necessary.
The Manufacturing Process
Raw Material Selection
The first step in manufacturing potting materials is the selection of raw materials. Manufacturers choose the appropriate resins, hardeners, fillers, and additives based on the desired properties of the final product. The selection process involves considering factors such as:
- Thermal conductivity: Important for dissipating heat in high-power applications.
- Electrical insulation: Crucial for preventing short circuits and electrical interference.
- Mechanical properties: Including hardness, flexibility, and impact resistance.
- Chemical resistance: Ensuring the material can withstand exposure to various chemicals.
Formulation and Mixing
Once the raw materials are selected, they are formulated into a specific mixture. This process involves precise measurements and blending to achieve the desired properties. Automated mixing equipment ensures consistency and uniformity in the final product.
Curing and Testing
After mixing, the potting material is subjected to a curing process, which can be either heat or room-temperature-based, depending on the type of resin used. The curing process allows the material to solidify and reach its final properties. Manufacturers conduct rigorous testing to ensure the material meets the required specifications. Tests may include:
- Thermal cycling: To assess the material’s performance under varying temperatures.
- Electrical testing: To verify insulation properties and dielectric strength.
- Mechanical testing: To evaluate hardness, flexibility, and impact resistance.
- Chemical resistance testing: To ensure durability in harsh environments.
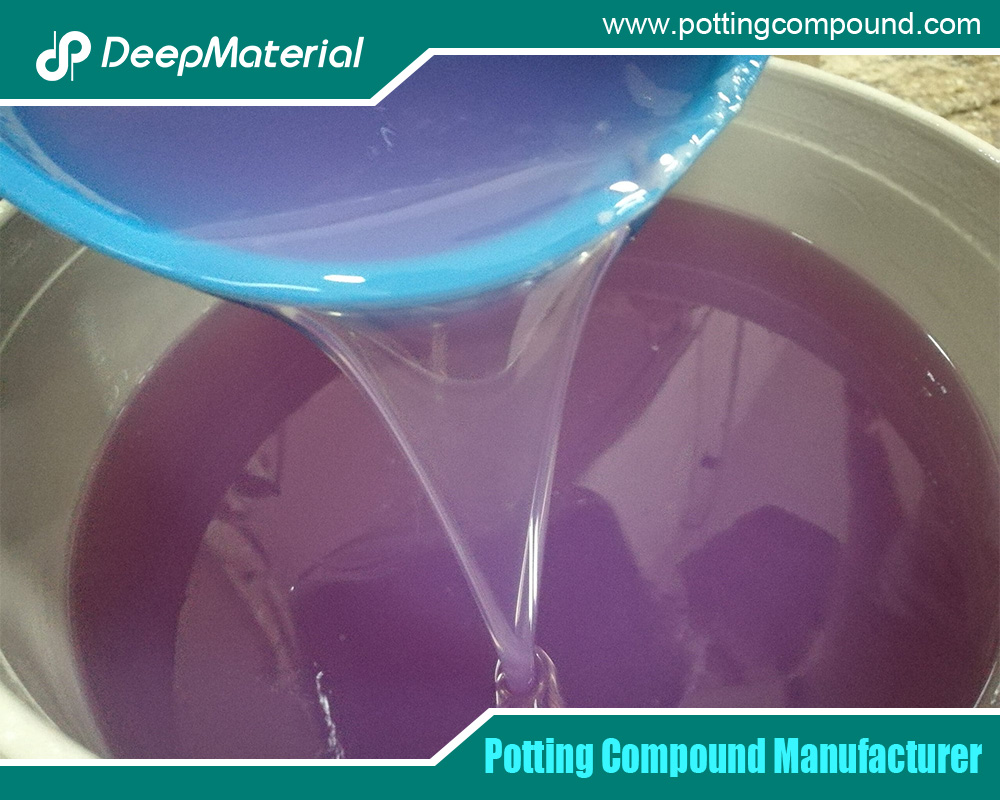
Packaging and Distribution
Once the potting material has passed all quality control tests, it is packaged and prepared for distribution. Packaging protects the material from contamination and degradation during storage and transportation. Manufacturers often provide the material in various forms, such as bulk containers, cartridges, or pre-measured kits, to meet the needs of different customers.
Applications of Potting Materials
Consumer Electronics
Potting materials protect components such as circuit boards, connectors, and sensors in consumer electronics. These materials ensure the devices operate reliably in various environmental conditions, including exposure to moisture, dust, and temperature fluctuations.
Automotive Industry
The automotive industry uses potting materials to protect electronic control units (ECUs), sensors, and vehicle connectors. Potting materials in this sector must withstand harsh conditions such as extreme temperatures, vibration, and exposure to chemicals like oil and fuel.
Aerospace and Defense
In aerospace and defense applications, electronic components must operate reliably under extreme conditions, including high altitudes, temperature extremes, and mechanical shock. Potting materials provide the necessary protection to ensure the functionality and longevity of these critical systems.
Industrial Electronics
Industrial electronics, including automation systems, sensors, and control units, are often exposed to harsh environments. Potting materials protect these components from dust, moisture, chemicals, and mechanical stress, ensuring reliable operation in demanding industrial settings.
Medical Devices
Medical devices require high reliability and protection from environmental factors. Potting materials in this sector must be biocompatible and provide excellent insulation and protection for sensitive electronic components.
Renewable Energy Systems
Renewable energy systems, such as solar panels and wind turbines, rely on potting materials to protect electronic components from environmental factors like UV radiation, moisture, and temperature fluctuations. These materials help ensure the long-term performance and reliability of renewable energy systems.
Challenges and Innovations
Environmental Concerns
One of the significant challenges facing the electronic potting material manufacturing industry is environmental sustainability. Traditional potting materials, such as epoxy and polyurethane resins, are derived from petroleum-based sources and can have negative ecological impacts. Manufacturers are increasingly focusing on developing eco-friendly alternatives and improving the sustainability of their products.
Advances in Material Science
Recent advances in material science have led to the development of new potting materials with enhanced properties. For example, nanotechnology creates materials with improved thermal conductivity and electrical insulation. These innovations are helping to meet the evolving demands of modern electronic devices.
Customization and Specialization
As electronic devices become more specialised, there is a growing need for customised potting solutions. Manufacturers are developing tailored formulations to meet the specific requirements of different applications. This trend towards customization is driving innovation in the industry and enabling manufacturers to offer more targeted and practical solutions.
Automation and Industry 4.0
Automation and Industry 4.0 technologies are revolutionising the manufacturing process for potting materials. Advanced robotics, automated mixing systems, and real-time monitoring are improving the efficiency and consistency of production. These technologies also enable manufacturers to quickly adapt to changing demands and produce high-quality materials with minimal waste.
Future Prospects
Growing Demand for Electronics
The increasing demand for electronic devices across various sectors, including consumer electronics, automotive, aerospace, and industrial applications, is driving the growth of the potting material manufacturing industry. As technology advances, the need for reliable and durable electronic components will only increase, creating new opportunities for manufacturers.
Sustainable and Eco-Friendly Solutions
Environmental sustainability is becoming a key focus for the industry. Manufacturers invest in research and development to create eco-friendly potting materials that reduce environmental impact. These efforts include developing bio-based resins, improving recycling processes, and reducing the use of hazardous chemicals.
Integration of Advanced Technologies
Integrating advanced technologies like nanotechnology, 3D printing, and intelligent materials will drive innovation in potting material manufacturing. These technologies will enable the development of materials with enhanced properties and new capabilities, opening up new applications and markets.
Global Market Expansion
The global market for electronic potting materials is expanding, driven by the growth of the electronics industry in emerging markets. Manufacturers are exploring new opportunities in Asia-Pacific, Latin America, and Africa, where the demand for electronic devices is rapidly increasing.
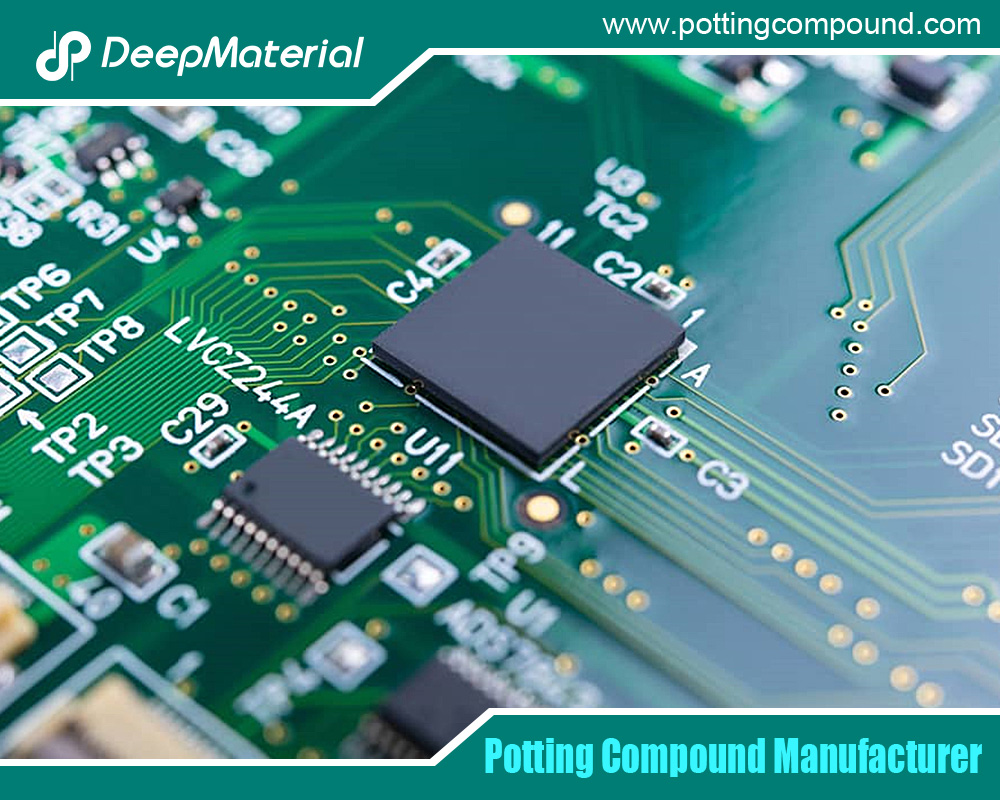
Conclusion
The electronic potting material manufacturing industry plays a vital role in ensuring the reliability and longevity of electronic devices across various sectors. Potting materials protect sensitive electronic components from consumer electronics to aerospace and defense. As technology advances and environmental sustainability becomes a priority, the industry is evolving to meet new challenges and opportunities.
Manufacturers are developing innovative materials, improving production processes, and exploring new markets to stay competitive in a rapidly changing landscape. The future of the electronic potting material manufacturing industry looks promising, with growing demand, technological advancements, and a focus on sustainability driving continued growth and innovation.
For more about choosing the top electronic potting material manufacturer: a comprehensive overview, you can pay a visit to DeepMaterial at https://www.pottingcompound.com/ for more info.
Recent Posts
- Potting Compound vs. Epoxy: A Comprehensive Comparison
- Potting Compound for PCB
- In – depth Analysis of the Curing Characteristics of Electronic Potting Compounds
- A Comprehensive Analysis of the Environmental Performance of Encapsulating Materials: From Regulations to Practices
- A Comprehensive Analysis of PCB Encapsulation Quality Inspection: Innovative Application of Non-Destructive Testing Technologies
- Analysis of the Improvement of the Seismic and Impact Resistance Performance of PCB by Encapsulation
- A Comprehensive Guide to Evaluating the Reliability of Encapsulation Materials for Encapsulated PCBs
- In-depth Analysis of the Reparability of Encapsulation Materials
- A Comprehensive Analysis of Post-Potting PCB Issues and the Repair and Rework of Potting Materials
- A Comprehensive Analysis of the Compatibility between Encapsulation Materials and PCBs: Exploration of Chemical Reactions and Their Impact on Performance