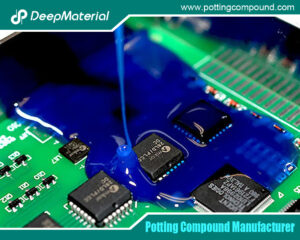
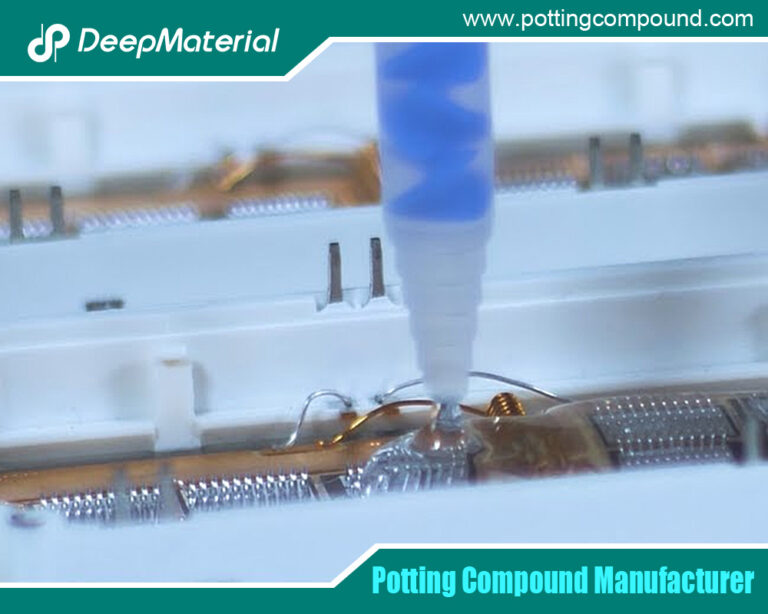
Technical Details on Controlling Parameters such as Temperature, Pressure, and Speed in the Potting Process to Ensure Potting Quality
- Electronic Potting Material Manufacturer
- April 15, 2025
- Automotive potting material manufacturers, Benefits of Potting Electronics, Ceramic Potting Compound, Ceramic Potting Compound Manufacturer, china electronic potting silicone supplier, circuit board potting, circuit board potting compound, circuit board potting compound china hotsale, circuit board potting compound factory wholesale, circuit board potting compounds, conformal coating for electronics, conformal coating spray, conformal coating types, Connector Potting Compound, Connector Potting Process, custom automated electronics potting, electrical potting compound, epoxy potting compound, polyurethane potting compound, potting compound for electronics, potting compound for pcb, potting compound vs epoxy, Potting Process, silicone potting compound for electronics, UV curing potting compound, uv electronic potting compound, uv potting compound, waterproof potting compound
Technical Details on Controlling Parameters such as Temperature, Pressure, and Speed in the Potting Process to Ensure Potting Quality
Potting, as a crucial process in industrial production, is widely applied in numerous fields such as electronics, pharmaceuticals, and automobiles. In the electronics field, it protects electronic components from the external environment, ensuring the stable operation of electronic products. In the pharmaceutical industry, it can guarantee the sterility and stability of drugs. In the automotive manufacturing industry, it plays roles such as sealing, waterproofing, and shockproofing for automotive parts, enhancing the overall performance and reliability of vehicles. The potting quality is directly related to the performance, reliability, and service life of products, and parameters such as temperature, pressure, and speed during the potting process are key factors affecting potting quality. Precisely controlling these parameters has become the core task to ensure potting quality.
Influence of Temperature, Pressure, and Speed on Potting Quality during the Potting Process
Influence of Temperature
- Influence on the Fluidity of Potting Materials: When the temperature rises, the molecular thermal motion of the potting material intensifies, the viscosity decreases, and the fluidity increases. For example, in the electronic potting using epoxy resin, when the temperature increases from 25°C to 40°C, its viscosity may drop by more than half. This enables the potting material to better fill complex and tiny gaps, avoiding incomplete filling. If the temperature is too low, the material’s viscosity is too high, resulting in poor fluidity and difficulty in filling the gaps, leading to potting defects. For instance, when potting LED lights, at low temperatures, the potting adhesive may not completely cover the chip, affecting the performance and lifespan of the LED.
- Influence on the Curing Reaction: An appropriate temperature can make the potting material cure at the expected rate. Taking the two-component polyurethane potting adhesive as an example, curing within the specified temperature range (such as 50 – 60°C) can form a good chemical bond cross-linking structure and obtain ideal physical properties. If the temperature is too high, the curing reaction is too fast, and a large amount of heat may be generated and cannot be dissipated in time, resulting in stress concentration inside the potting material, causing problems such as cracking and deformation. For some electronic component potting, rapid curing at high temperatures will increase the difference in the coefficient of thermal expansion between the potting adhesive and the components, leading to internal stress damage. If the temperature is too low, the curing reaction is slow or even stagnant, prolonging the production cycle and possibly resulting in incomplete curing, making the performance of the potted parts not up to standard. For example, in a low-temperature environment in winter, if no heating measures are taken, some potting adhesives may not cure to the required strength for a long time.
- Influence on the Generation and Elimination of Bubbles: Temperature affects the behavior of bubbles in the potting material. At higher temperatures, the solubility of gas in the potting material decreases, and bubbles are more likely to precipitate. For example, when potting a transformer, if the potting temperature is too high, the gas in the insulating oil is likely to form bubbles. Appropriately increasing the temperature and combining it with operations such as stirring and vacuuming helps the bubbles to escape. Because the increase in temperature makes the gas molecules move more vigorously and more likely to overcome the surface tension and escape. For example, preheating and stirring the potting material before potting can reduce the residual bubbles.
Influence of Pressure
- Influence on the Filling Effect of Potting Materials: Applying a certain pressure can make the potting material quickly and fully fill the target area. When potting the casing of complex electronic products, with the assistance of air pressure or hydraulic pressure, it can ensure that the potting adhesive enters every corner, avoiding a decrease in protective performance due to insufficient filling. If the pressure is insufficient, the potting material is difficult to reach narrow or remote parts, forming potting dead corners and reducing the product’s reliability. If the pressure is too high, it may damage the potted components. For example, when potting a precision electronic chip, excessive pressure may deform the chip pins or damage the internal circuit.
- Influence on the Density and Strength of the Potted Layer: An appropriate pressure can make the molecules of the potting material arrange more closely, improving the density and strength of the potted layer. When manufacturing aerospace parts, applying high pressure to the potting material can enhance its compressive and impact resistance. If the pressure is not appropriate, the potted layer may have a loose structure, reducing its mechanical and sealing performance. For example, if the pressure is too small, there may be voids inside the potted layer, which is likely to be damaged when subjected to vibration or pressure. If the pressure is too high, the potting material is over-compressed, and the internal structure may be damaged, resulting in a decrease in strength instead.
- Influence on Bubble Control: Pressure can change the size and distribution of bubbles. During the vacuum potting process, reducing the pressure makes the bubbles expand and escape, effectively reducing the bubble content. In a non-vacuum environment, appropriately increasing the pressure can compress the bubbles and reduce their impact on potting quality, but the bubbles cannot be completely eliminated. For example, in some common potting scenarios with low requirements for bubbles, the negative impact of bubbles is reduced by making them smaller through pressurization.
Influence of Speed
- Influence on the Uniformity of Potting Materials: Only when the potting speed is moderate can the potting material be evenly distributed during the filling process. Taking the potting of a circuit board as an example, if the speed is too fast, the potting adhesive may accumulate locally or generate turbulence, resulting in inconsistent potting thickness, affecting heat dissipation and protective performance. If the speed is too slow, the previously potted material may partially cure, causing overall uneven potting. For example, during manual potting, unstable operation speed is likely to lead to large differences in potting thickness.
- Influence on Bubble Entrainment: The potting speed is closely related to bubble entrainment. If the speed is too fast, the potting material is likely to entrain air into the potting area and form bubbles. For example, when potting a battery module, rapid potting may cause air to be unable to escape in time, forming bubbles in the potting adhesive, affecting the battery’s performance and safety. If the speed is too slow, although it can reduce bubble entrainment, it may lead to low production efficiency and fail to meet the needs of large-scale production. For example, in some automated potting production lines, a too slow speed will reduce the production capacity.
- Influence on Production Efficiency: A reasonable potting speed is the key to ensuring production efficiency. In large-scale industrial production, increasing the potting speed can increase the number of potted items per unit time and reduce production costs. For example, on an automotive parts production line, using appropriate high-speed potting with automated potting equipment can greatly improve production efficiency. However, if the speed is too fast, it will bring quality risks, and it is necessary to find a balance between quality and efficiency. For example, blindly increasing the speed resulting in unqualified potting quality will instead increase rework costs and time.
Control Methods of Temperature, Pressure, and Speed during the Potting Process
Temperature Control Methods
- Selection and Application of Heating Equipment: Common heating equipment includes hot plates, ovens, heating rods, infrared heaters, etc., each with its applicable scenarios. Hot plates are suitable for preheating potting materials or heating and curing small potted parts. For example, before potting a small electronic module, placing the potting adhesive on a hot plate for preheating can reduce its viscosity. Ovens are suitable for heating and curing batches of potted parts and can provide a uniform and stable temperature environment. For example, in the pharmaceutical industry, the drugs in ampoules are heated in an oven for sterilization and curing after potting. Heating rods are often used to heat the storage containers of potting materials in potting equipment to maintain the material temperature. For example, in a glue dispenser, heating rods are used to keep the potting adhesive fluid. Infrared heaters use infrared radiation for heating, with fast heating speed and high efficiency, and can be used for local heating of large potted parts. For example, when potting the casing of a large transformer, an infrared heater is used to quickly heat the potting area to promote curing.
- Temperature Sensors and Feedback Control Systems: Temperature sensors monitor the temperature during the potting process in real-time, such as thermocouples and thermal resistors, which convert the temperature signal into an electrical signal and transmit it to the controller. The controller compares the preset temperature value with the feedback signal from the sensor and adjusts the power of the heating equipment to maintain the temperature stable. For example, using a PID (Proportional-Integral-Derivative) controller, the heating power is automatically adjusted according to the temperature deviation, so that the potting temperature is precisely controlled within the set range, and the deviation can be controlled within ±1°C.
- Formulation and Optimization of the Temperature Curve: Formulate a temperature curve according to the characteristics of the potting material and product requirements, including stages such as preheating, curing, and cooling. For example, for a certain type of epoxy resin potting adhesive, the preheating stage is to increase the temperature to 40°C at a rate of 5°C/min and maintain it for 15 minutes to make the material flow fully. The curing stage is to increase the temperature to 80°C and maintain it for 60 minutes to complete the curing reaction. The cooling stage is to cool naturally or at a certain rate to prevent internal stress caused by too fast temperature changes. In actual production, optimize the temperature curve through experiments and data analysis. For example, according to the quality inspection results of the potted parts, adjust the temperature and time of each stage to improve potting quality.
Pressure Control Methods
- Selection and Adjustment of the Pressure Source: Pressure sources include air compressors, hydraulic pumps, etc. Air compressors provide air pressure and are often used to apply a relatively low pressure to the potting material. For example, in ordinary electronic potting, an air compressor provides an air pressure of 0.2 – 0.5MPa to assist the filling of the potting adhesive. Hydraulic pumps provide hydraulic pressure and can generate a relatively high pressure, which is suitable for scenarios with high requirements for the density and strength of the potted layer. For example, when potting aerospace parts, a hydraulic pump is used to provide a hydraulic pressure of 1 – 5MPa to make the potting material fill tightly. Adjust the output pressure of the pressure source through pressure reducing valves, overflow valves, etc. to meet different potting needs. For example, use a pressure reducing valve to adjust the high-pressure gas output by the air compressor to an appropriate pressure for potting.
- Pressure Sensors and Closed-Loop Control Systems: Pressure sensors monitor the pressure during the potting process in real-time, such as strain gauge pressure sensors and capacitive pressure sensors, which convert the pressure signal into an electrical signal and transmit it to the controller. The controller compares the preset pressure value with the feedback signal from the sensor and adjusts the output of the pressure source or controls the valve opening to maintain the pressure stable, forming a closed-loop control system. For example, in a vacuum potting device, the vacuum degree is monitored by a pressure sensor, and the controller adjusts the pumping rate of the vacuum pump to keep the vacuum degree at the set value, with a deviation controllable within ±0.01MPa.
- Formulation and Implementation of the Pressure Control Strategy: Formulate a pressure control strategy according to the potting process and product requirements. In the initial stage of potting, use a relatively low pressure to make the potting material fill slowly to avoid impacting the potted components. As the filling progresses, gradually increase the pressure to fully compact the potting material. In the later stage of potting, maintain an appropriate pressure to complete the curing. For example, when potting the motor winding, apply a pressure of 0.1MPa in the initial stage, increase the pressure to 0.3MPa when the filling reaches 80%, and maintain a pressure of 0.2MPa during the curing stage. During the implementation process, strictly control the pressure change according to the strategy to ensure potting quality.
Speed Control Methods
- Selection of Potting Equipment and Parameter Setting: Potting equipment includes manual glue guns, semi-automatic glue dispensers, and fully automatic glue dispensers, etc., and different equipment has different speed control capabilities. Manual glue guns have their speed controlled manually by the operator and are suitable for small batches and potting with low precision requirements. Semi-automatic glue dispensers control the potting speed by adjusting the air pressure or motor speed, and their speed stability is better than that of manual glue guns. Fully automatic glue dispensers use precise motors and control systems and can accurately control the potting speed and dosage, which are suitable for large-scale and high-precision potting production. For example, in the potting of mobile phone motherboards, a fully automatic glue dispenser can control the potting speed within the range of 1 – 10mm/s. Set the parameters of the potting equipment according to the potting process requirements, such as adjusting the pump speed and valve opening of the glue dispenser to achieve the control of the potting speed.
- Flow Sensors and Speed Regulation Systems: Flow sensors monitor the flow of potting materials in real-time, such as electromagnetic flowmeters and gear flowmeters, etc., which convert the flow signal into an electrical signal and transmit it to the controller. The controller calculates the current potting speed according to the preset speed value and the feedback signal from the flow sensor and adjusts the driving device of the potting equipment (such as motor speed, cylinder stroke, etc.) to adjust the potting speed, keeping the potting speed stable. For example, when potting a capacitor, the flow of the potting adhesive is monitored by a flow sensor, and the controller adjusts the motor speed of the glue dispenser to ensure a constant potting speed.
- Planning and Adjustment of the Speed Curve: Plan the speed curve according to the shape, size, and process requirements of the potted product. For potted parts with simple shapes, uniform speed potting can be adopted. For potted parts with complex shapes or special requirements, a variable speed potting curve needs to be planned. For example, when potting an electronic component with a special-shaped groove, reduce the potting speed at the groove part to ensure the filling quality, and appropriately increase the speed at other parts to improve production efficiency. In actual production, adjust and optimize the speed curve according to the potting quality inspection results and production efficiency requirements.
Potting Quality Inspection and Evaluation
Common Potting Quality Defects and Analysis
- Bubble Problems: The causes of bubbles include air mixed in the potting material, too fast potting speed, improper control of temperature and pressure, etc. Bubbles will reduce the strength of the potted layer, affect the sealing performance and heat dissipation effect. For example, in electronic potting, bubbles may cause local overheating of electronic components and shorten their service life. Reduce the generation of bubbles by optimizing the potting process, such as controlling the potting speed, performing vacuum degassing treatment, and reasonably adjusting the temperature and pressure.
- Insufficient or Excessive Potting: Insufficient potting may be caused by poor fluidity of the potting material, insufficient pressure, too slow potting speed, etc., which will make the protected object insufficiently protected. Excessive potting may cause material waste and product appearance defects. For example, in pharmaceutical packaging potting, excessive potting may affect the tightness of the medicine and the integrity of the packaging. By precisely controlling the parameters of the potting process, such as adjusting the potting speed, pressure, and material flow, and regularly calibrating the potting equipment, problems of insufficient or excessive potting can be avoided.
- Poor Curing: Poor curing may be caused by insufficient temperature, time, improper proportion of the curing agent, or quality problems of the potting material, which will reduce the mechanical and chemical stability of the potted parts. For example, in the potting of automotive parts, poor curing may cause the parts to loosen or fall off during use. Ensure the curing effect by strictly controlling the curing temperature, time, and the proportion of the curing agent, as well as conducting quality inspections on the potting material.
- Cracking of the Potted Layer: The cracking of the potted layer may be caused by a large difference in the coefficient of thermal expansion between the potting material and the potted object, excessive internal stress during the curing process, too fast temperature change, etc., which will reduce the protective performance and structural strength of the potted parts. For example, in the potting of outdoor electronic products, the cracking of the potted layer will make the electronic products vulnerable to environmental erosion. Prevent the cracking of the potted layer by selecting a suitable potting material, optimizing the curing process, and controlling the temperature change rate.
Potting Quality Inspection Methods
- Appearance Inspection: Observe the appearance of the potted parts with the naked eye or with the help of tools such as magnifying glasses and microscopes, and check for defects such as bubbles, insufficient potting, excessive potting, uneven surfaces, and cracking. It is the most basic and commonly used inspection method, which can be carried out in real-time on the production line to promptly detect obvious quality problems.
- Sealing Inspection: For potted parts with sealing requirements, use methods such as pressure testing, vacuum testing, and helium mass spectrometry leak detection to detect the sealing performance. In pressure testing, a certain pressure of gas is charged into the potted part, and whether there is gas leakage is observed. In vacuum testing, the potted part is placed in a vacuum environment, and whether there is gas escape is observed. Helium mass spectrometry leak detection uses the high diffusivity and low residue of helium to detect tiny leaks and is often used in occasions with extremely high requirements for sealing performance, such as the detection of potted parts for aerospace and medical equipment.
- Hardness Inspection: Use a hardness tester to detect the hardness of the potted layer to determine whether the curing effect meets the requirements. Different potting materials and application scenarios have different requirements for hardness. For example, the hardness of electronic potting adhesives is generally between Shore A 30 – 80. By detecting the hardness, the curing degree and performance of the potting material can be evaluated.
- Tensile Strength and Shear Strength Inspection: Use a tensile testing machine and a shear testing machine to detect the tensile strength and shear strength between the potted layer and the potted object to evaluate the bonding performance between the potted layer and the potted object.
For more about choosing the top technical details on controlling parameters such as temperature, pressure, and speed in the potting process to ensure potting quality, you can pay a visit to DeepMaterial at https://www.pottingcompound.com/ for more info.
Recent Posts
- The Top Polyurethane Potting Compound
- Advanced Epoxy Potting Compound for Superior Electronic Protection
- Waterproof Potting Compound: A Comprehensive Guide
- Silicone Potting Compound for Electronics
- Potting Compound vs. Epoxy: A Comprehensive Comparison
- Potting Compound for PCB
- In – depth Analysis of the Curing Characteristics of Electronic Potting Compounds
- A Comprehensive Analysis of the Environmental Performance of Encapsulating Materials: From Regulations to Practices
- A Comprehensive Analysis of PCB Encapsulation Quality Inspection: Innovative Application of Non-Destructive Testing Technologies
- Analysis of the Improvement of the Seismic and Impact Resistance Performance of PCB by Encapsulation
Tags
Related Posts
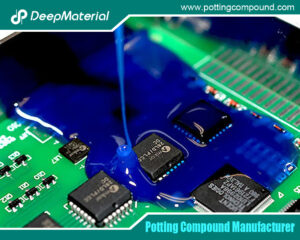
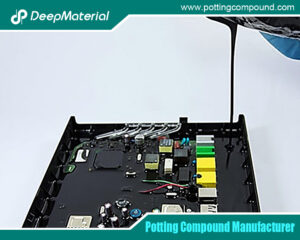
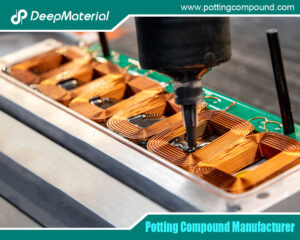
Waterproof Potting Compound: A Comprehensive Guide
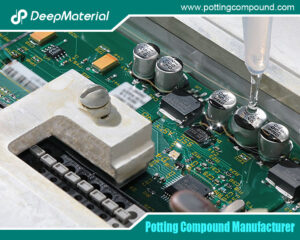
Silicone Potting Compound for Electronics
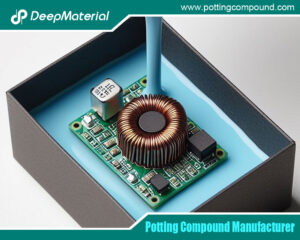
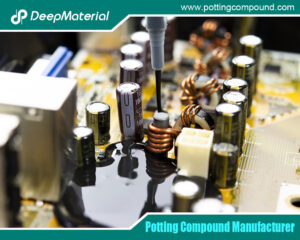