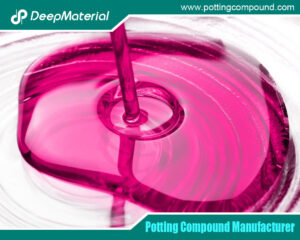
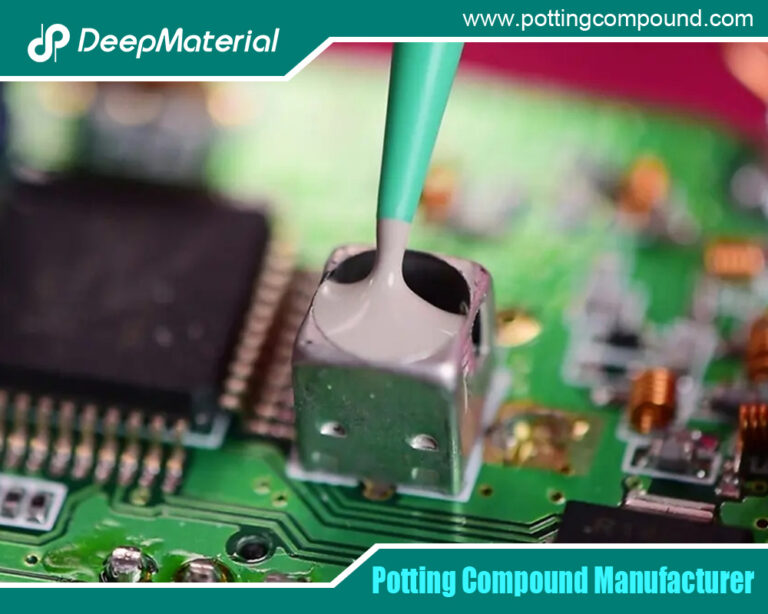
In-depth Analysis of the Reparability of Encapsulation Materials
- Electronic Potting Material Manufacturer
- May 15, 2025
- conformal coating for electronics, conformal coating for pcb, conformal coating for pcb standards, conformal coating material, conformal coating silicone, conformal coating spray, conformal coating types, conformal coating waterproof, electrical potting compound, electronic board level underfill and encapsulation material market, electronic epoxy encapsulant potting compounds, encapsulation material manufacturer, encapsulation material supplier, encapsulation materials, epoxy encapsulation electronic components, epoxy encapsulation led, epoxy encapsulation meaning, epoxy encapsulation molding compound, epoxy potting compound, epoxy resin encapsulation, pcb encapsulation epoxy, polyurethane potting compound, potting and encapsulation material, potting and encapsulation material china, potting and encapsulation material manufacturer, potting compound for electronics, potting compound for pcb, potting compound vs epoxy, silicone potting compound for electronics, UV curing potting compound, waterproof potting compound
In-depth Analysis of the Reparability of Encapsulation Materials
Encapsulation materials are widely used in modern industry. Their function is to protect internal electronic components, mechanical parts, etc., from external environments such as moisture, dust, chemical substances, and mechanical stress, thereby improving the reliability and stability of products. However, due to various reasons, products after encapsulation may encounter problems such as electrical performance failures and damage to the encapsulation materials themselves. At this time, the reparability of the encapsulation materials becomes extremely crucial. Reparable encapsulation materials can not only reduce production costs but also reduce product downtime and improve production efficiency, which has an important impact on the economic benefits of enterprises and the market competitiveness of products.
Common Problems of Encapsulation Materials and Preliminary Judgment of Their Reparability
Problems Related to Electrical Performance
- Short Circuit: When conductive impurities such as metal debris and solder beads are mixed into the encapsulation material, or improper operation during the encapsulation process causes accidental connection between component pins, a short circuit may occur. A short circuit has a great impact on the reparability of the encapsulation material because it is necessary to accurately locate the short-circuit point, which often requires disassembling part of the encapsulation material, increasing the difficulty of repair. If the short circuit is caused by impurities inside the encapsulation material, it may be necessary to completely remove the encapsulation material and re-encapsulate it; if the short-circuit point is on the surface and easy to handle, the problem can be solved by repairing the encapsulation material locally.
- Open Circuit: The shrinkage stress during the curing of the encapsulation material and the difference in thermal expansion and contraction caused by temperature changes may cause component pins to break or circuits to crack, resulting in an open circuit. For an open circuit problem, if the breakpoint position can be determined and the breakpoint is easy to operate on, it can be solved by repairing the circuit or pins and then re-encapsulating. In this case, the reparability of the encapsulation material is relatively good; however, if the breakpoint is difficult to locate or is in a complex structure, the repair difficulty increases, and the reparability decreases.
Physical Damage to the Encapsulation Material
- Cracking: Insufficient flexibility of the encapsulation material, too fast curing speed, mechanical impact, or drastic temperature changes may all lead to cracking. When the cracking is minor and can be detected in a timely manner, it can be repaired by filling the cracks and re-curing the encapsulation material, and the reparability is relatively high; but for severe cracking, it may be necessary to remove most of the encapsulation material and re-encapsulate it, and the repair process is complex.
- Debonding: Incomplete surface cleaning before encapsulation or a mismatch between the encapsulation material and the material of the object being encapsulated will cause the encapsulation material to debond from the PCB or components. When the debonding area is small, the encapsulation material can be re-fixed by reprocessing the surface and applying an adhesive; when the debonding is severe, the entire encapsulation material needs to be replaced, and the reparability depends on the specific situation.
- Residual Bubbles: Air introduced during the stirring process, high environmental humidity during encapsulation, and other reasons will cause bubbles to be generated inside the encapsulation material. A small number of bubbles have little impact on the reparability and can be made to escape by heating and other methods; a large number of bubbles may affect the performance of the encapsulation material, and it is necessary to remove it and re-encapsulate.
Factors Affecting the Reparability of Encapsulation Materials
Types of Encapsulation Materials
- Epoxy Resin: Epoxy resin encapsulation materials have high strength, high insulation, and good chemical corrosion resistance. However, after curing, they have high hardness and brittleness, and it is difficult to remove them during repair. Usually, they need to be softened by heating at a high temperature or dissolved with a special solvent. This process may cause damage to the surrounding components, and the reparability is relatively low. For example, in electronic devices, when there is a problem with the epoxy resin-encapsulated circuit board, removing the encapsulation material may cause component pins to break or solder joints to become desoldered.
- Silicone: Silicone encapsulation materials have good flexibility, excellent high and low-temperature resistance performance, and good adhesion to a variety of materials. They are relatively easy to remove and can be removed by a combination of heating and softening with the assistance of a solvent, causing less damage to the surrounding components, and the reparability is relatively high. For example, in the encapsulation of automotive electronic sensors, when there is a problem with the silicone encapsulation material, it is easier to perform repair operations.
- Polyurethane: Polyurethane encapsulation materials have good comprehensive performance, with a certain degree of flexibility and wear resistance. Their repair difficulty is between that of epoxy resin and silicone, and they can be removed by a combination of heating and mechanical removal. However, during the removal process, attention should be paid to their adhesion to the object being encapsulated to avoid damaging the components.
Degree of Curing
The higher the degree of curing of the encapsulation material, the greater its hardness, and the more difficult it is to repair. Completely cured encapsulation materials require stronger external force, higher temperature, or more effective solvents to be removed; partially cured encapsulation materials are relatively easier to handle and can be further cured by appropriate methods or softened to a certain extent for repair. In the production process, if a problem is found in the encapsulation material during the partial curing stage, measures should be taken in a timely manner. At this time, the success rate of repair is relatively high and the cost is relatively low.
Application Scenarios and Environments
- Electronics Field: The internal space of electronic devices is compact, and the components are precise, which requires extremely high precision and protection of components during the repair process of the encapsulation material. During the repair process, any minor mistake may cause damage to the components and affect the performance of the device, which increases the difficulty of repairing the encapsulation material and reduces its reparability. For example, the repair of the encapsulation material of a mobile phone motherboard requires operation in a very small space, which has strict requirements for technology and equipment.
- Automotive Field: The working environment of automobiles is complex, and the encapsulation material has to withstand various factors such as high temperature, vibration, and humidity. When repairing the encapsulation material of an automobile, not only should the performance of the repaired material meet the requirements of the harsh working environment of the automobile be considered, but also whether the repair process will affect the normal operation of other components of the automobile should be taken into account. This also poses a challenge to the reparability of the encapsulation material.
- Aerospace Field: Aerospace equipment has extremely high requirements for reliability. Once there is a problem with the encapsulation material, the repair process must go through strict testing and verification to ensure that the performance after repair is consistent with or close to the original performance. Due to the particularity of aerospace equipment, the repair of its encapsulation material is difficult, and the reparability is relatively low. In many cases, it is more inclined to replace the entire component.
Repair Methods of Encapsulation Materials and the Embodiment of Reparability
Heating and Softening Removal Method
- Operation Process: Use equipment such as a hot air gun and a heating table to heat the encapsulation material to soften it, and then use tools such as a scraper and tweezers to remove it. For different types of encapsulation materials, the heating temperatures are different. For example, epoxy resin encapsulation materials usually need to be heated to 300 – 400°C, and silicone encapsulation materials need to be heated to 200 – 300°C.
- Embodiment of Reparability: This method is applicable to most encapsulation materials, but it needs to be used with caution for the encapsulation materials around components that are sensitive to temperature. If the operation is proper, the encapsulation material can be removed well for repair, and the reparability is relatively high; but if the heating is improper, it may damage the components, resulting in the inability to repair.
Solvent Dissolution Method
- Operation Process: Select appropriate solvents, such as organic solvents like acetone and toluene, to dissolve the encapsulation material. Drop the solvent on the surface of the encapsulation material to make it penetrate and dissolve the encapsulation material, and then use tools to remove the dissolved substances.
- Embodiment of Reparability: The solvent dissolution method has a good effect on some encapsulation materials such as silicone, and can remove the encapsulation material under relatively mild conditions, causing less impact on the surrounding components, and the reparability is relatively high. However, attention should be paid to the corrosiveness of the solvent to the PCB, components, etc. If the solvent is not selected properly or used in excessive amounts, it may damage other components and reduce the reparability.
Mechanical Removal Method
- Operation Process: Directly use tools such as tweezers, scrapers, and long-nose pliers to remove the encapsulation material by physical external force. For relatively thin and less adhesive encapsulation materials, they can be directly scraped off with a scraper; for the encapsulation material covering component pins, it can be carefully crushed and removed with long-nose pliers.
- Embodiment of Reparability: The mechanical removal method is simple and direct, but it is easy to cause physical damage to components and circuits. When the adhesion between the encapsulation material and the components is not tight and the operation space is large, the reparability is relatively good; if the encapsulation material is closely combined with the components and the operation space is narrow, using this method may cause damage to the components, and the reparability is reduced.
Local Repair Method
- Operation Process: When there are only local problems with the encapsulation material, such as small-area cracking and debonding, handle the local area. For the cracked area, first clean the crack, then fill it with new encapsulation material and cure it; for the debonded area, reprocess the surface and then apply an adhesive to fix it.
- Embodiment of Reparability: The local repair method is highly targeted and has little impact on the overall encapsulation structure, and the reparability is high. It can effectively save repair costs and time, especially suitable for the repair of small-range problems.
Significance of Detection and Verification after Repair for Reparability
Appearance Inspection
Observe whether the surface of the repaired encapsulation material is flat and smooth, and whether there are defects such as cracks, bubbles, and holes, as well as whether the combination between the encapsulation material and the components and PCB is tight by the naked eye or under a microscope. Appearance inspection can intuitively find the problems that may occur during the repair process. If there are obvious defects in the appearance, it may be necessary to repair it again, which is directly related to the final effect of the repair of the encapsulation material and its reparability.
Electrical Performance Test
Use equipment such as a multimeter and an oscilloscope to test the electrical performance after repair, such as resistance, capacitance, and signal transmission, etc., to see if they are normal. The electrical performance test is a key indicator for judging whether the repair is successful. If the electrical performance does not meet the requirements, it indicates that the repair has not achieved the expected effect, and the reparability is in question, and it is necessary to further investigate the problem and repair it again.
Reliability Test
Simulate the actual use environment through aging tests, vibration tests, high and low-temperature cycle tests, etc., and detect the performance stability and reliability of the repaired encapsulation material under different conditions. The reliability test can verify whether the repaired encapsulation material can work stably and continuously in the actual application. Only by passing the reliability test can it be proved that the repair of the encapsulation material is successful, and the reparability is effectively verified.
Case Analysis
Case of Repairing Encapsulation Material of an Electronic Device
The encapsulation material of an electronic device cracked due to external impact, causing the internal components to be affected by moisture and short-circuited. The heating and softening removal method was used to remove the cracked part of the encapsulation material, then the affected components were cleaned, and re-encapsulation was carried out. After appearance inspection, electrical performance test, and reliability test, the device returned to normal operation, proving that in this case, the encapsulation material is reparable, and the repair method is effective.
Case of Repairing Encapsulation Material of an Automotive Sensor
The encapsulation material of an automotive sensor debonded due to long-term operation in a high-temperature environment, affecting the performance of the sensor. The local repair method was used, the surface was reprocessed, and a high-temperature-resistant adhesive was applied to re-fix the encapsulation material. After a series of tests simulating the working environment of the automobile, the performance of the sensor was stable, indicating that for the problem of the encapsulation material of this automotive sensor, the adopted repair method is feasible, and the encapsulation material is reparable.
Conclusion and Prospect
The reparability of encapsulation materials is affected by various factors. There are differences in the reparability of different types of encapsulation materials, and the selection of repair methods and the operation process are crucial to the repair effect. Through effective detection and verification means, it can be ensured that the repaired encapsulation materials meet the use requirements. In the future, with the development of materials science and manufacturing technology, it is expected to develop more easily repairable encapsulation materials. At the same time, repair technologies will continue to innovate and improve, improving the efficiency and success rate of repairing encapsulation materials, reducing production costs, and promoting the development of related industries. In practical applications, according to the specific problems and application scenarios of the encapsulation materials, various factors should be comprehensively considered, and the most suitable repair method should be selected to give full play to the advantages of the reparability of the encapsulation materials.
For more about the in-depth analysis of the reparability of encapsulation materials, you can pay a visit to DeepMaterial at https://www.pottingcompound.com/ for more info.
Recent Posts
- UV Curing Potting Compound
- The Ultimate Guide to Electrical Potting Compound and Market Application
- The Top Polyurethane Potting Compound
- Advanced Epoxy Potting Compound for Superior Electronic Protection
- Waterproof Potting Compound: A Comprehensive Guide
- Silicone Potting Compound for Electronics
- Potting Compound vs. Epoxy: A Comprehensive Comparison
- Potting Compound for PCB
- In – depth Analysis of the Curing Characteristics of Electronic Potting Compounds
- A Comprehensive Analysis of the Environmental Performance of Encapsulating Materials: From Regulations to Practices
Tags
Related Posts
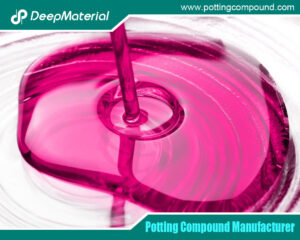
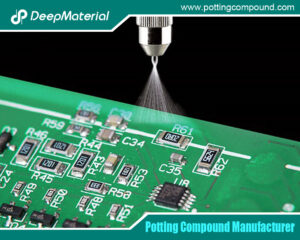
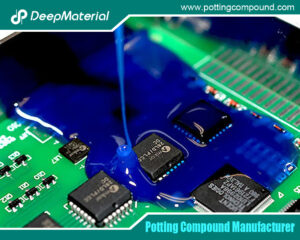
The Top Polyurethane Potting Compound
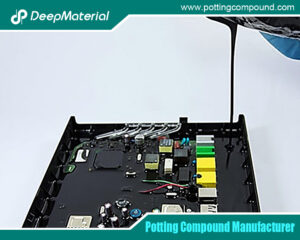
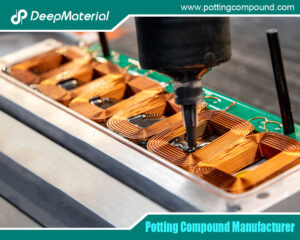
Waterproof Potting Compound: A Comprehensive Guide
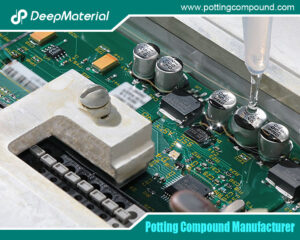