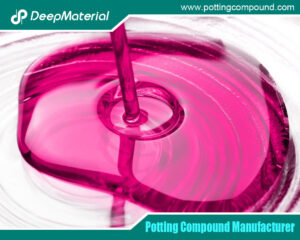
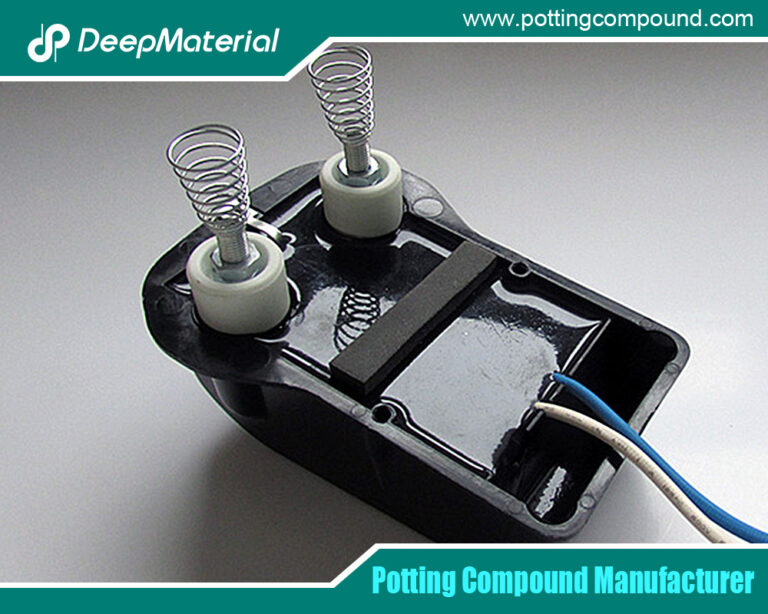
How to Ensure the Compatibility between Encapsulation Materials and Various Components on PCBs
- Electronic Potting Material Manufacturer
- May 6, 2025
- Automotive potting material manufacturers, Benefits of Potting Electronics, Ceramic Potting Compound, Ceramic Potting Compound Manufacturer, china electronic potting silicone manufacturer, china electronic potting silicone supplier, circuit board potting, circuit board potting compound, circuit board potting compounds, conformal coating, conformal coating market, conformal coating material, Connector Potting Compound, Connector Potting Process, custom automated electronics potting, deepmaterial potting compound, electric motor potting compound, electronic board level underfill and encapsulation material market, encapsulation material manufacturer, encapsulation materials, epoxy encapsulation, epoxy encapsulation electronic components, epoxy encapsulation for photovolatics, epoxy encapsulation led, epoxy encapsulation molding compound, epoxy resin encapsulation, epoxy resin encapsulation solar panels, potting and encapsulation material, potting and encapsulation material manufacturer, potting compound
How to Ensure the Compatibility between Encapsulation Materials and Various Components on PCBs
In electronic devices, the printed circuit board (PCB) carries various components, and the stability of its performance is crucial for the overall operation of the device. As a key medium for protecting PCBs and components, the compatibility between encapsulation materials and various components, coatings, and substrate materials on the PCB directly affects the reliability, stability, and service life of electronic devices. Therefore, ensuring the compatibility of encapsulation materials has become an important issue in the field of electronic manufacturing.
Overview of Encapsulation Materials and Compatibility
The Role of Encapsulation Materials
Encapsulation materials in electronic devices are like a strong “armor”, playing multiple key roles. It can effectively improve the insulation between internal components and circuits, providing strong support for the miniaturization and lightweight of devices. This is just like creating a safe insulation space for precision electronic components, allowing them to work stably in a compact environment. At the same time, it prevents the direct exposure of components and circuits, greatly improving the waterproof, dustproof, and moisture-proof performance of the devices, which is like holding an umbrella for electronic devices to protect them from the erosion of harsh external environments. In fields with extremely high requirements for the reliability of electronic devices, such as automobiles and aerospace, these functions of encapsulation materials are particularly important, ensuring the stable operation of devices in complex environments.
The Significance of Compatibility
Compatibility is the cornerstone of the application of encapsulation materials. Once the compatibility between the encapsulation material and the components on the PCB is poor, it is like laying a hidden danger at the foundation of a building, which may lead to a series of serious problems. For example, it will cause the encapsulation material to fail to closely adhere to the components and substrates, resulting in gaps and bubbles. These tiny defects are like hidden time bombs, which will reduce the protection effect, making electronic devices vulnerable to the intrusion of moisture, dust, etc. It may also cause chemical reactions, corroding the components and substrates, like a slow poison, gradually weakening the performance of electronic devices and shortening their service life. According to relevant research statistics, electronic device failures caused by compatibility issues account for a considerable proportion among all failure reasons, which fully highlights the importance and urgency of ensuring compatibility.
Analysis of Key Components on PCBs
Characteristics of Various Components
- Resistors: Resistors are important components for regulating current and voltage in electronic devices. Common resistors include carbon film resistors, metal film resistors, etc. Carbon film resistors have a lower cost, but their accuracy is relatively not high; metal film resistors have higher accuracy and good stability. Different types of resistors have differences in materials and structures, which makes their interactions with encapsulation materials different. For example, certain encapsulation materials may chemically react with the carbon film layer of carbon film resistors, affecting the resistance value stability of the resistors.
- Capacitors: Capacitors can store and release charges, playing key roles such as filtering and coupling in circuits. Electrolytic capacitors have the characteristic of large capacitance, but their positive electrodes are usually metal foils, and the electrolyte is likely to react with certain encapsulation materials, resulting in problems such as leakage, affecting their performance and service life. Ceramic capacitors, on the other hand, have the advantages of good high-frequency characteristics and high stability. However, there may be differences in the thermal expansion coefficients between their ceramic materials and encapsulation materials. When the temperature changes, stress is likely to be generated, causing the capacitors to crack or the encapsulation materials to crack.
- Integrated Circuits (ICs): ICs are the core components of electronic devices, highly integrating numerous electronic components and having extremely strict requirements for the working environment. The pins of ICs are usually made of metal materials. When in contact with encapsulation materials, they may be electrochemically corroded, leading to pin breakage or poor contact, and then causing the entire IC to fail. Moreover, the passivation layer on the surface of the IC chip also needs to be compatible with the encapsulation material, otherwise it may affect the electrical performance of the chip.
Types and Functions of Coatings
- Three-proof Paint Coatings: Three-proof paint coatings are mainly used to protect PCBs from the erosion of moisture, dust, and chemical substances, just like putting an invisible protective suit on the PCB. It has good insulation performance and moisture-proof performance, which can effectively extend the service life of the PCB. Common three-proof paints include acrylic, silicone, and polyurethane types. The compatibility between different types of three-proof paints and encapsulation materials also varies. For example, acrylic three-proof paints may chemically react with certain epoxy resin encapsulation materials, causing the coating to fail.
- Solder Mask Layer: The main function of the solder mask layer is to prevent the solder from flowing where soldering is not required, ensuring the accuracy and reliability of soldering. It is like a precise “solder navigator”. The solder mask layer is usually composed of organic resin and pigments. When in contact with encapsulation materials, it is necessary to ensure that the two will not dissolve each other or undergo chemical reactions, so as not to affect the performance of the solder mask layer and then the soldering quality of the PCB.
Characteristics of Substrate Materials
- Common Substrate Materials: Currently, common substrate materials for PCBs include phenolic paper-based laminates, epoxy glass cloth laminates (FR-4), etc. Phenolic paper-based laminates have a lower cost, but their mechanical and electrical properties are relatively poor, and their water absorption is relatively high. When combined with encapsulation materials, the presence of water may affect the compatibility between the two. FR-4 is one of the most widely used substrate materials, having good mechanical properties, electrical properties, and dimensional stability. However, its thermal expansion coefficient may not match well with certain encapsulation materials. When the temperature changes greatly, it is likely to cause the encapsulation material to separate from the substrate.
- The Influence of Substrate Materials on Compatibility: The surface roughness, chemical composition, and thermal expansion coefficient of substrate materials will all have an important impact on the compatibility of encapsulation materials. For substrates with a large surface roughness, it is difficult for the encapsulation material to be completely wetted, and it is easy to form bubbles and gaps. Substrates with different chemical compositions may chemically react with the encapsulation material, reducing the compatibility. For substrates and encapsulation materials with a large difference in thermal expansion coefficient, thermal stress will be generated during the temperature cycle process, causing the interface to crack and damaging the protection effect.
Key Factors Affecting Compatibility
Matching of Chemical Properties
- Chemical Composition of Encapsulation Materials: Common encapsulation materials mainly include epoxy resins, polyurethanes, silicone, etc. Epoxy resins have excellent mechanical properties and adhesive properties, and the hardness after curing is relatively high, but their temperature resistance is relatively limited. Polyurethane encapsulation materials have good flexibility and low-temperature resistance, and have good adhesion to a variety of materials, but they may degrade in a high-temperature environment. Silicone encapsulation materials have excellent high-temperature resistance, weather resistance, and electrical insulation performance, but their adhesive strength is relatively low. Different chemical compositions determine the chemical activity and reaction characteristics of the encapsulation material, which are closely related to the compatibility with components on the PCB.
- The Possibility of Chemical Reactions with Components: If the chemical properties of the encapsulation material do not match those of the components, coatings, or substrate materials, a chemical reaction may occur. For example, certain acidic encapsulation materials may corrode metal components, causing their surfaces to oxidize and rust. Alkaline encapsulation materials may react with the ceramic materials of ceramic capacitors, damaging their structure and performance. When selecting an encapsulation material, it is necessary to fully consider its chemical compatibility with various components on the PCB to avoid potential chemical reactions.
Matching of Physical Properties
- Thermal Expansion Coefficient: The thermal expansion coefficient is an important indicator for measuring the dimensional change of materials when the temperature changes. If the thermal expansion coefficients of the encapsulation material and the components on the PCB do not match, during the temperature cycle process, due to the different expansion and contraction degrees of different materials, thermal stress will be generated. Under the long-term action of this thermal stress, it may cause the interface between the encapsulation material and the components to crack, reducing the protection effect and even damaging the components. For example, when an electronic device cools down suddenly after working in a high-temperature environment, the encapsulation material and the substrate with a large difference in thermal expansion coefficient may separate due to inconsistent contraction.
- Hardness and Flexibility: The hardness and flexibility of the encapsulation material also need to match the components on the PCB. If the encapsulation material is too hard, it may damage the fragile components when subjected to external impact, just like a hard shell may crush the internal egg during a collision. If the encapsulation material is too soft, it may not provide sufficient mechanical support, causing the components to shift in a vibration environment, affecting the normal connection of the circuit. Therefore, it is necessary to select an encapsulation material with appropriate hardness and flexibility according to the specific application scenarios and the characteristics of the components.
Influence of Process Factors
- The Influence of the Encapsulation Process on Compatibility: Different links in the encapsulation process, such as mixing, pouring, and curing, will all have an impact on the compatibility between the encapsulation material and the components. During the mixing process, if the stirring is not uniform, it may cause the performance of the encapsulation material to be inconsistent, affecting its bonding with the components. When pouring, if the fluidity of the encapsulation material is poor, it may not be able to completely fill the gaps between the components, forming voids and bubbles. During the curing process, if the curing temperature and time are not controlled properly, it may cause the encapsulation material to be incompletely cured or generate internal stress, reducing the compatibility.
- The Importance of Curing Conditions: Curing conditions are key factors in the encapsulation process. Different encapsulation materials have different curing requirements, including curing temperature, curing time, and curing method. For example, epoxy resin encapsulation materials usually need to be cured by heating at a certain temperature. If the curing temperature is too high or the time is too long, it may cause the encapsulation material to change color and its performance to decline, and the compatibility with the components becomes poor. Some silicone encapsulation materials can be cured at room temperature, but the curing speed is relatively slow. It is necessary to control the humidity and temperature of the curing environment to ensure the curing effect and compatibility.
Testing and Evaluation Methods for Compatibility
Laboratory Testing Methods
- Thermal Cycle Testing: Thermal cycle testing simulates the temperature changes experienced by electronic devices during actual use. The encapsulated PCB samples are repeatedly cycled between high and low temperature environments. By observing the appearance changes of the samples during the thermal cycle process, such as whether there are cracks, bubbles, delamination, etc., and testing the changes in their electrical performance, the thermal compatibility between the encapsulation material and the components can be evaluated. Generally, the temperature range and the number of cycles of the thermal cycle test will be determined according to the actual use environment and requirements of the electronic device. For example, automotive electronic devices may need to be tested under a wider temperature range and more cycles.
- Wet Heat Testing: Wet heat testing is mainly used to evaluate the compatibility between the encapsulation material and the components in a high-temperature and high-humidity environment. Place the samples in an environmental chamber with a specific temperature and humidity for a certain period of time. During the test, regularly check the appearance of the samples and detect their electrical performance indicators such as insulation resistance and dielectric constant. If the compatibility between the encapsulation material and the components is poor, under the wet heat environment, water penetration may occur, leading to problems such as component corrosion and short circuits. The compatibility can be judged by the changes in these performance indicators.
- Chemical Corrosion Testing: Chemical corrosion testing is to expose the encapsulated samples to specific chemical reagents, observe whether the encapsulation material and the components undergo chemical reactions, and the degree of the reaction. Commonly used chemical reagents include acid, alkali, and salt solutions, which are selected according to the chemical substances that the electronic device may come into contact with. For example, for electronic devices used in a chemical environment, chemical corrosion tests for acid and alkali resistance may be required. By detecting the corrosion situation and performance changes on the surface of the samples, the chemical compatibility of the encapsulation material can be evaluated.
Actual Application Testing
- Small Batch Trial Production: Before mass production, small batch trial production is an effective actual application testing method. Through small batch trial production, the compatibility between the encapsulation material and the PCB components can be tested in a real production environment, and potential problems can be discovered. During the trial production process, conduct a comprehensive inspection of the products, including appearance inspection, electrical performance testing, reliability testing, etc., collect data and analyze it, and adjust and optimize the encapsulation material or production process according to the test results.
- Long-term Reliability Monitoring: Conduct long-term reliability monitoring on the products of trial production, simulate various conditions in the actual use of the products, and track their performance changes. The products can be placed in different environments, such as high temperature, low temperature, humidity, vibration, etc., and their various performance indicators can be regularly detected. The time span of long-term reliability monitoring may be as long as several months or even years. Through the analysis of the monitoring data, the long-term compatibility between the encapsulation material and the components can be evaluated, providing a reliable basis for the design and production of the products.
Effective Strategies for Ensuring Compatibility
Selection of Encapsulation Materials
- Select Encapsulation Materials According to Component Characteristics: When selecting an encapsulation material, fully consider the characteristics of various components on the PCB. For components with high requirements for high-temperature resistance, such as power devices, silicone encapsulation materials with good high-temperature resistance should be selected. For components that require good adhesive performance, such as ceramic capacitors, epoxy resin encapsulation materials may be a better choice. For devices that work in a low-temperature environment, the low-temperature resistance of polyurethane encapsulation materials can meet the requirements. In addition, factors such as the electrical performance and chemical stability of the encapsulation material also need to be considered. After a comprehensive evaluation, select the most suitable encapsulation material.
- Refer to the Material Compatibility Database: There are now many professional material compatibility databases, which collect a large amount of compatibility information between different encapsulation materials and various components, coatings, and substrate materials. When selecting an encapsulation material, these databases can be referred to understand the compatibility of different material combinations and avoid selecting material combinations with known poor compatibility. At the same time, with the continuous development of materials science and the emergence of new encapsulation materials, the database will also be continuously updated, providing the latest compatibility references for electronic manufacturing enterprises.
Process Optimization
- Improve Encapsulation Process Parameters: Through experiments and data analysis, optimize the encapsulation process parameters. For example, adjust the mixing ratio of the encapsulation material to ensure that each component is fully mixed and improve the performance stability of the encapsulation material. Optimize the pouring temperature and speed to enable the encapsulation material to better fill the gaps between the components and reduce the generation of bubbles and voids. Precisely control the curing temperature and time to ensure that the encapsulation material is completely cured and avoid generating internal stress due to over-curing. Different encapsulation materials and product structures may require different process parameters, which need to be adjusted according to the actual situation.
- Introduce Advanced Encapsulation Equipment: Advanced encapsulation equipment can more precisely control the encapsulation process and improve the encapsulation quality and consistency. For example, the use of automated encapsulation equipment can achieve precise measurement and mixing, reducing the influence of human factors. The use of vacuum encapsulation equipment can extract bubbles during the encapsulation process and improve the adhesion between the encapsulation material and the components. The introduction of advanced encapsulation equipment can not only improve production efficiency but also effectively improve the compatibility between the encapsulation material and the PCB components and enhance the reliability of the products.
Quality Control
- Establish a Strict Quality Inspection System: During the production process, establish a strict quality inspection system to comprehensively inspect the encapsulation material and the encapsulated products. When inspecting the incoming encapsulation materials, detect whether their various performance indicators meet the requirements. During the encapsulation process, monitor the encapsulation quality in real time, such as checking the filling situation of the encapsulation material and whether there are bubbles. After the encapsulation is completed, conduct appearance inspection, electrical performance testing, reliability testing, etc. on the products to ensure that the product quality meets the standards. Only through strict quality inspection can compatibility issues be found and solved in a timely manner, ensuring the quality and reliability of the products.
- Randomly Inspect Raw Materials and Finished Products: In addition to comprehensive inspection, regular random inspections should also be carried out on raw materials and finished products. Random inspections can discover potential problems in the production process and take timely measures for improvement. For the raw materials of the encapsulation material, randomly inspect whether their chemical composition and physical properties are stable. For finished products, randomly inspect their performance under various environmental conditions, such as high temperature, low temperature, humidity, etc. Through random inspections, product quality can be effectively controlled, and the compatibility between the encapsulation material and the PCB components can always be maintained in a good state.
The compatibility between the encapsulation material and various components, coatings, and substrate materials on the PCB is the key to ensuring the stable performance and long-term reliable operation of electronic devices. By deeply understanding the characteristics of components on the PCB, the factors affecting compatibility, adopting scientific testing and evaluation methods, and effective strategies for ensuring compatibility, electronic manufacturing enterprises can improve product quality, reduce failure rates, meet the market demand for high-performance electronic devices, and stand in the fierce market competition.
For more about how to ensure the compatibility between encapsulation materials and various components on PCBs, you can pay a visit to DeepMaterial at https://www.pottingcompound.com/ for more info.
Recent Posts
- UV Curing Potting Compound
- The Ultimate Guide to Electrical Potting Compound and Market Application
- The Top Polyurethane Potting Compound
- Advanced Epoxy Potting Compound for Superior Electronic Protection
- Waterproof Potting Compound: A Comprehensive Guide
- Silicone Potting Compound for Electronics
- Potting Compound vs. Epoxy: A Comprehensive Comparison
- Potting Compound for PCB
- In – depth Analysis of the Curing Characteristics of Electronic Potting Compounds
- A Comprehensive Analysis of the Environmental Performance of Encapsulating Materials: From Regulations to Practices
Tags
Related Posts
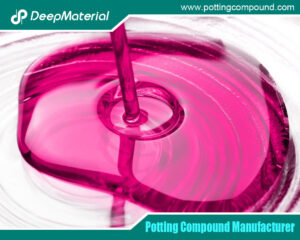
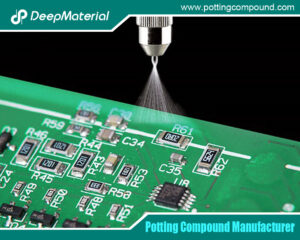
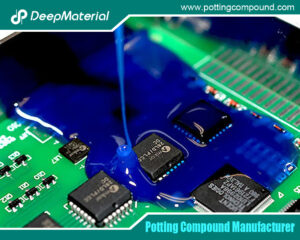
The Top Polyurethane Potting Compound
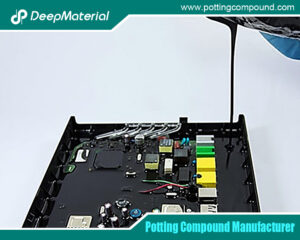
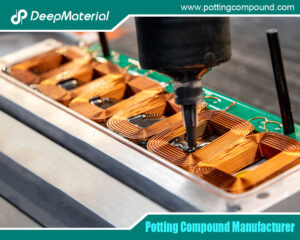
Waterproof Potting Compound: A Comprehensive Guide
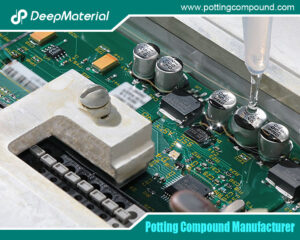