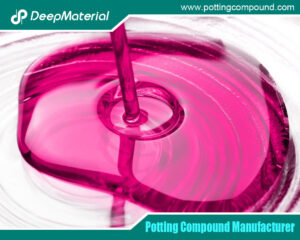
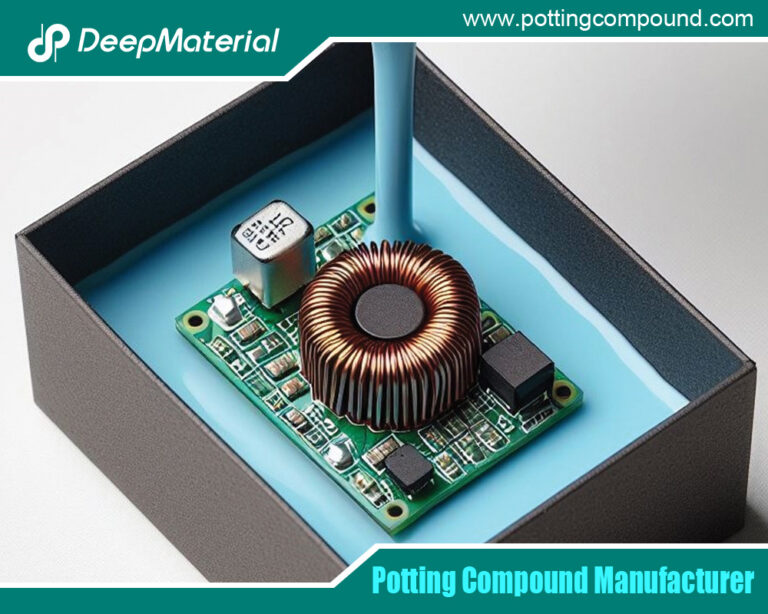
Potting Compound vs. Epoxy: A Comprehensive Comparison
- Electronic Potting Material Manufacturer
- July 2, 2025
- Automotive potting material manufacturers, Benefits of Potting Electronics, Ceramic Potting Compound, Ceramic Potting Compound Manufacturer, circuit board potting, circuit board potting compound, conformal coating for electronics, conformal coating for pcb, conformal coating for pcb standards, conformal coating material, conformal coating pcb, conformal coating process, conformal coating silicone, conformal coating types, conformal coating waterproof, Connector Potting Compound, custom automated electronics potting, electrical potting compound, electronic epoxy encapsulant potting compounds, epoxy encapsulation molding compound, epoxy potting compound, pcb encapsulation epoxy, pcb potting, polyurethane potting compound, polyurethane potting compound for electronics, potting and encapsulation, potting and encapsulation material, potting compound for electronics, potting compound for pcb, potting compound vs epoxy, potting compounds and epoxy, potting material for electronic components, potting material for electronics, potting pcb, silicone potting compound for electronics, UV Curable Conformal Coating, UV Cured Epoxy Potting, UV Curing Encapsulants, UV curing potting compound, UV Curing Potting Compounds, waterproof potting compound
Potting Compound vs. Epoxy: A Comprehensive Comparison
In the world of electronics, manufacturing, and material encapsulation, two terms frequently come up: potting compounds and epoxy. These materials play a critical role in protecting components, ensuring durability, and enhancing performance in a wide range of applications, from automotive electronics to aerospace systems. While potting compounds and epoxies are often discussed interchangeably, they are not identical. Understanding their differences, advantages, and limitations is essential for engineers, designers, and hobbyists alike. This article delves into a detailed comparison of potting compounds and epoxy, exploring their properties, applications, and key considerations to help you make informed decisions.
What Are Potting Compounds?
Potting compounds are materials used to encase or encapsulate electronic components, protecting them from environmental factors such as moisture, dust, vibration, and thermal stress. The process of “potting” involves filling an electronic assembly or housing with a liquid compound that hardens to form a protective barrier. Potting compounds are designed to provide insulation, mechanical stability, and resistance to harsh conditions, making them indispensable in industries like electronics, automotive, aerospace, and telecommunications.
Potting compounds come in various formulations, including epoxy, silicone, polyurethane, and acrylic-based materials. Each type offers unique properties tailored to specific applications. For instance, silicone potting compounds are known for their flexibility and high-temperature resistance, while polyurethane compounds excel in shock absorption and moisture resistance. The choice of potting compound depends on the application’s requirements, such as operating temperature, chemical exposure, or mechanical stress.
What Is Epoxy?
Epoxy is a type of thermosetting polymer formed by mixing a resin and a hardener, which undergo a chemical reaction to create a strong, durable material. Epoxies are widely used in adhesives, coatings, composites, and, notably, as a potting material for electronic encapsulation. In the context of potting, epoxy serves as one of the many types of potting compounds available, valued for its excellent adhesion, chemical resistance, and mechanical strength.
Epoxy’s versatility makes it a go-to choice for applications requiring robust protection. It is commonly used to encase circuit boards, transformers, and sensors, providing a rigid, protective shell that shields components from environmental damage. Epoxy potting compounds are particularly popular in industries where durability and resistance to harsh chemicals or high temperatures are critical.
Key Properties: Potting Compounds vs. Epoxy
To understand the differences between potting compounds and epoxy, it’s essential to examine their properties. Since epoxy is a subset of potting compounds, we’ll compare epoxy-based potting compounds with other types of potting compounds, such as silicone, polyurethane, and acrylic.
- Mechanical Strength
- Epoxy: Epoxy potting compounds are renowned for their high mechanical strength and rigidity. Once cured, epoxy forms a hard, durable shell that provides excellent protection against physical stress, impact, and vibration. This makes it ideal for applications where components must withstand rough handling or mechanical shock.
- Other Potting Compounds: Polyurethane potting compounds offer more flexibility than epoxy, making them better suited for applications where components are subject to repeated flexing or thermal expansion. Silicone potting compounds are even more flexible and elastic, providing superior shock absorption but less rigidity than epoxy. Acrylic potting compounds, while less common, are lightweight but lack the mechanical strength of epoxy or polyurethane.
- Thermal Conductivity
- Epoxy: Epoxy potting compounds can be formulated with fillers to enhance thermal conductivity, making them suitable for applications requiring heat dissipation, such as in power electronics. However, standard epoxies have moderate thermal conductivity compared to specialized compounds.
- Other Potting Compounds: Silicone potting compounds typically offer better thermal conductivity and can operate in a wider temperature range (-50°C to 200°C or higher) compared to epoxy (typically -40°C to 150°C). Polyurethane compounds have lower thermal conductivity but are often used in applications where flexibility is more critical than heat dissipation.
- Chemical and Moisture Resistance
- Epoxy: Epoxy excels in chemical resistance, making it ideal for environments exposed to oils, solvents, or corrosive substances. It also provides excellent moisture resistance, protecting electronic components from humidity and water ingress.
- Other Potting Compounds: Polyurethane potting compounds are highly resistant to moisture and are often used in outdoor or marine applications. Silicone compounds also offer excellent moisture resistance and perform well in humid environments. Acrylics, while less resistant to chemicals, are suitable for less demanding environments.
- Electrical Insulation
- Epoxy: Epoxy potting compounds have excellent dielectric properties, making them ideal for insulating electronic components and preventing electrical shorts. They are commonly used in high-voltage applications.
- Other Potting Compounds: Silicone and polyurethane compounds also provide strong electrical insulation, with silicone being particularly effective in high-temperature environments. Acrylics offer good insulation but may not perform as well in extreme conditions.
- Cure Time and Processing
- Epoxy: Epoxy typically requires a longer curing time, ranging from a few hours to a full day, depending on the formulation and curing conditions. It can be cured at room temperature or with heat to accelerate the process.
- Other Potting Compounds: Polyurethane compounds generally cure faster than epoxy, often within a few hours. Silicone compounds also cure relatively quickly, and some formulations can be UV-cured for rapid processing. Acrylics have the fastest curing times but may require specific conditions, such as UV exposure.
Applications: Where Each Shines
Both potting compounds and epoxy have distinct applications based on their properties. Below are some common use cases for each.
Epoxy Potting Compounds
- Electronics Manufacturing: Epoxy is widely used to encapsulate printed circuit boards (PCBs), transformers, and sensors, providing robust protection against moisture, chemicals, and mechanical stress.
- Automotive Electronics: In automotive systems, epoxy potting compounds protect control modules and sensors from high temperatures, vibrations, and exposure to automotive fluids.
- Aerospace: Epoxy’s high strength and chemical resistance make it suitable for aerospace applications, such as encapsulating avionics components exposed to extreme conditions.
- Industrial Equipment: Epoxy is used in heavy-duty industrial equipment where components must withstand harsh chemicals, high voltages, or mechanical wear.
Other Potting Compounds
- Silicone Potting Compounds: These are ideal for applications requiring flexibility and high-temperature resistance, such as LED lighting, outdoor electronics, and medical devices. Silicone’s elasticity makes it suitable for components that experience thermal cycling or mechanical stress.
- Polyurethane Potting Compounds: Polyurethane is commonly used in automotive, marine, and outdoor applications due to its flexibility and excellent moisture resistance. It is ideal for encapsulating components in environments with frequent temperature changes or exposure to water.
- Acrylic Potting Compounds: Acrylics are less common but are used in applications where lightweight materials and fast curing are needed, such as in consumer electronics or low-cost assemblies.
Advantages and Disadvantages
Epoxy Potting Compounds
Advantages:
- High Strength: Epoxy provides a rigid, durable encapsulation that protects against impact and vibration.
- Chemical Resistance: Excellent resistance to solvents, oils, and corrosive substances.
- Adhesion: Strong bonding to a wide range of substrates, ensuring a secure encapsulation.
- Electrical Insulation: Superior dielectric properties for high-voltage applications.
Disadvantages:
- Rigidity: Epoxy’s hardness can be a drawback in applications requiring flexibility or thermal expansion.
- Cure Time: Longer curing times compared to other compounds may slow down production.
- Thermal Limitations: Epoxy has a narrower operating temperature range compared to silicone.
Other Potting Compounds
Advantages:
- Flexibility (Polyurethane and Silicone): These materials accommodate thermal expansion and mechanical stress, making them ideal for dynamic environments.
- High-Temperature Performance (Silicone): Silicone compounds can operate in extreme temperatures, surpassing epoxy’s capabilities.
- Fast Curing (Acrylics and Polyurethane): Faster processing times improve manufacturing efficiency.
- Moisture Resistance (Polyurethane): Polyurethane excels in humid or wet environments.
Disadvantages:
- Lower Strength (Silicone and Polyurethane): These materials may not provide the same level of mechanical protection as epoxy.
- Cost (Silicone): Silicone potting compounds can be more expensive than epoxy or polyurethane.
- Limited Chemical Resistance (Acrylics): Acrylics are less suitable for harsh chemical environments.
Key Considerations for Choosing Between Potting Compounds and Epoxy
When deciding between epoxy and other potting compounds, several factors should guide your decision:
- Environmental Conditions: Consider the operating environment of your application. If components are exposed to high temperatures or thermal cycling, silicone may be the better choice. For chemical exposure, epoxy is often preferred.
- Mechanical Requirements: If rigidity and strength are critical, epoxy is ideal. For applications requiring flexibility or shock absorption, polyurethane or silicone is more suitable.
- Processing Constraints: Evaluate curing time and manufacturing requirements. Acrylics and polyurethane offer faster curing, which can streamline production, while epoxy may require more time or heat.
- Cost: Epoxy and polyurethane are generally more cost-effective than silicone, which can be a deciding factor for budget-conscious projects.
- Electrical Performance: For high-voltage applications, epoxy and silicone provide excellent insulation, but the choice may depend on other factors like temperature or flexibility.
Practical Examples
To illustrate the differences, consider two scenarios:
- Scenario 1: Automotive Sensor: An automotive sensor must withstand vibrations, temperature fluctuations, and exposure to automotive fluids. Epoxy might be chosen for its chemical resistance and durability, but polyurethane could be a better option if flexibility is needed to accommodate thermal expansion.
- Scenario 2: Outdoor LED Lighting: LED lights exposed to rain, UV radiation, and extreme temperatures benefit from silicone potting compounds due to their flexibility, moisture resistance, and high-temperature performance.
Conclusion
Potting compounds and epoxy both serve critical roles in protecting electronic components, but they cater to different needs based on their properties. Epoxy, as a type of potting compound, excels in applications requiring high strength, chemical resistance, and electrical insulation. However, other potting compounds like silicone, polyurethane, and acrylic offer unique advantages, such as flexibility, faster curing, or high-temperature performance, making them better suited for specific applications.
When choosing between potting compounds and epoxy, carefully assess the environmental, mechanical, and electrical requirements of your project. By understanding the strengths and limitations of each material, you can select the best solution to ensure the longevity and reliability of your components. Whether you opt for the robust protection of epoxy or the versatile performance of other potting compounds, the right choice will enhance the durability and functionality of your application.
For more about choosing the potting compound vs. epoxy: a comprehensive comparison, you can pay a visit to DeepMaterial at https://www.pottingcompound.com/ for more info.
Recent Posts
- UV Curing Potting Compound
- The Ultimate Guide to Electrical Potting Compound and Market Application
- The Top Polyurethane Potting Compound
- Advanced Epoxy Potting Compound for Superior Electronic Protection
- Waterproof Potting Compound: A Comprehensive Guide
- Silicone Potting Compound for Electronics
- Potting Compound vs. Epoxy: A Comprehensive Comparison
- Potting Compound for PCB
- In – depth Analysis of the Curing Characteristics of Electronic Potting Compounds
- A Comprehensive Analysis of the Environmental Performance of Encapsulating Materials: From Regulations to Practices
Tags
Related Posts
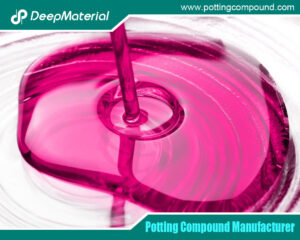
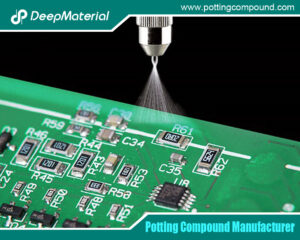
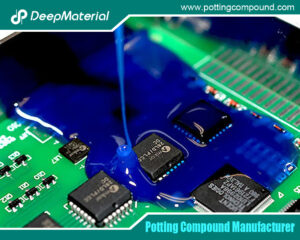
The Top Polyurethane Potting Compound
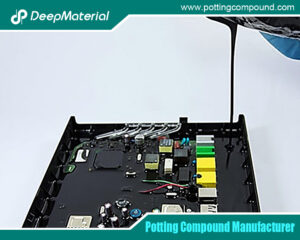
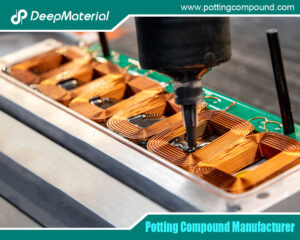
Waterproof Potting Compound: A Comprehensive Guide
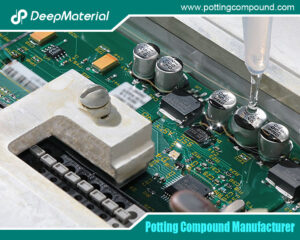