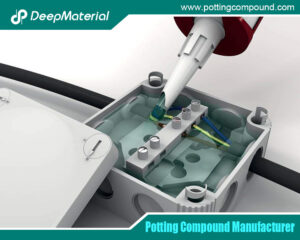
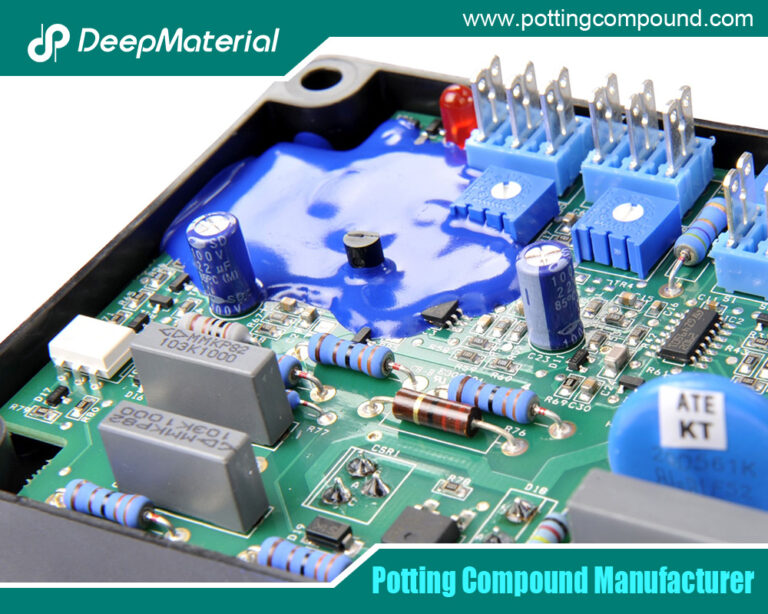
Influence of Encapsulation Thickness on the Heat Dissipation Performance and Electrical Insulation Performance of PCB
- Electronic Potting Material Manufacturer
- April 22, 2025
- circuit board encapsulation, conformal coating for electronics, conformal coating for pcb, conformal coating material, conformal coating spray, Electrical Component Encapsulation, electrical encapsulation, electronic board level underfill and encapsulation material market, electronic encapsulation, electronic encapsulation china hotsale, Electronic Encapsulation in Potting Material Manufacturing, electronic encapsulation manufacturer, Electronic Encapsulation Methods, Electronic encapsulation process, electronic encapsulation supplier, electronic encapsulation supplier china wholesale, Encapsulation for PCB, encapsulation lcd, epoxy encapsulation, epoxy encapsulation electronic components, epoxy encapsulation for photovolatics and oleds, epoxy encapsulation led, epoxy encapsulation meaning, epoxy encapsulation molding compound, epoxy potting compound, led encapsulation epoxy, potting and encapsulation, potting compound for electronics, potting compound for pcb, silicone potting compound for electronics, waterproof potting compound
Influence of Encapsulation Thickness on the Heat Dissipation Performance and Electrical Insulation Performance of PCB
In the design and manufacturing of electronic devices, the performance of the printed circuit board (PCB) is of vital importance. Encapsulation, as an important means to protect the PCB and electronic components, the selection of its encapsulation thickness is directly related to the heat dissipation performance and electrical insulation performance of the PCB, which in turn affects the stability, reliability and service life of the entire electronic device. This article will deeply explore the specific impacts of the encapsulation thickness on these two aspects of the PCB performance.
Overview of Encapsulation Materials and Encapsulation Processes
Encapsulation refers to filling the liquid encapsulation material around the PCB and electronic components, and forming a tight protective layer after curing. Common encapsulation materials include epoxy resin, silicone, polyurethane, etc. Epoxy resin encapsulation materials have good mechanical strength and insulation performance; silicone encapsulation materials are resistant to high temperatures and have good flexibility; polyurethane encapsulation materials have excellent impact resistance. Encapsulation processes include room temperature encapsulation and heating encapsulation, etc. During the encapsulation process, parameters such as the fluidity and curing time of the encapsulation material need to be controlled to ensure the quality of the encapsulation.
Influence of Encapsulation Thickness on Heat Dissipation Performance
I. Relationship between Heat Conduction Principle and Encapsulation Thickness
From the basic principle of heat conduction, heat transfer follows Fourier’s law, that is, the heat passing through a certain cross-section per unit time is proportional to the area of this cross-section, the temperature gradient and the thermal conductivity of the material. For PCB encapsulation, the encapsulation material acts as a medium for heat transfer. When the encapsulation thickness is relatively thin, the path for heat to transfer from the electronic components to the encapsulation material and then dissipate is relatively short. Take an electronic component with a power of P as an example. Assuming that the heat generated by it is Q, under the same other conditions, a thin encapsulation layer enables the heat to be conducted to the surrounding environment more quickly. This is because the thermal resistance is proportional to the thickness of the material and inversely proportional to the thermal conductivity. Reducing the encapsulation thickness reduces the thermal resistance, making it easier for the heat to transfer. For example, in some small electronic devices, using a relatively thin encapsulation thickness (such as 1 – 2mm) can effectively conduct the heat generated by the chip out quickly, ensuring that the chip works at a lower temperature.
II. Hindrance to Heat Dissipation Caused by Thick Encapsulation Layer
However, when the encapsulation thickness is too large, the situation is the opposite. A thick encapsulation layer will increase the thermal resistance and hinder the heat transfer. On the one hand, the thermal conductivity of the encapsulation material itself is relatively low compared to materials such as metals. Even if the encapsulation material has a certain thermal conductivity, with the increase of the thickness, the heat will encounter greater resistance when transferring inside the encapsulation material, resulting in the accumulation of heat in the encapsulation layer. On the other hand, an excessively thick encapsulation layer may make the heat transfer path longer and more complex, which is not conducive to the rapid and effective dissipation of heat. For example, in some large industrial power supply devices, if the encapsulation thickness reaches more than 10mm, it will be found that the temperature of the electronic components increases significantly. This is because the excessively thick encapsulation layer seriously hinders the heat dissipation and affects the normal operation of the device.
III. Consideration Factors for the Optimal Encapsulation Thickness
Determining the optimal encapsulation thickness requires comprehensive consideration of multiple factors. Firstly, it is the power and heat generation of the electronic components. Components with higher power and greater heat generation require a thinner encapsulation layer to ensure good heat dissipation. Secondly, it is the thermal conductivity of the encapsulation material. Encapsulation materials with high thermal conductivity can appropriately increase the encapsulation thickness without significantly affecting the heat dissipation effect. In addition, the operating environment temperature and heat dissipation method of the device are also very important. If the device operates in a high-temperature environment or relies on natural heat dissipation, then the encapsulation thickness should be minimized as much as possible; while if efficient heat dissipation methods such as forced air cooling or liquid cooling are used, the limitation of the encapsulation thickness can be appropriately relaxed.
Influence of Encapsulation Thickness on Electrical Insulation Performance
I. Insulation Principle and the Role of Thickness
The basic principle of electrical insulation is to use insulating materials to prevent the leakage of current. The encapsulation material plays the role of isolating electronic components and circuits with different potentials in the PCB. Increasing the encapsulation thickness can provide a greater insulation distance, thereby improving the insulation performance. According to the relevant theory of electrical insulation, under a certain electric field strength, the breakdown voltage of the insulating material is proportional to the thickness. For example, in a high-voltage circuit board, appropriately increasing the encapsulation thickness (such as 5 – 8mm) can effectively improve its ability to withstand high voltages and prevent the occurrence of electrical breakdown phenomena.
II. Insulation Risks of an Excessively Thin Encapsulation Layer
When the encapsulation thickness is too thin, there are greater electrical insulation risks. On the one hand, a thin encapsulation layer may not be able to completely cover the gaps between electronic components and circuits, resulting in the easy occurrence of electric leakage phenomena under harsh environments such as high voltage or humidity. On the other hand, an excessively thin encapsulation layer, during long-term use, due to the influence of environmental factors (such as temperature changes, humidity, chemical erosion, etc.), its insulation performance may gradually decline, increasing the possibility of electrical failures. For example, in some outdoor electronic devices, if the encapsulation thickness is less than 1mm, after a period of exposure to wind, rain and sunlight, the insulation performance may decline, leading to problems such as device short circuits.
III. Balance between Encapsulation Thickness and Insulation Performance
Although increasing the encapsulation thickness is beneficial to improving the insulation performance, it cannot be increased without limit. In addition to the heat dissipation problems mentioned above, an excessively thick encapsulation layer will also increase the cost, weight and volume, bringing inconvenience to the design and use of the device. Therefore, in practical applications, it is necessary to find a balance between the encapsulation thickness and the insulation performance. This requires comprehensive consideration of multiple factors such as the operating voltage of the PCB, the operating environment and the cost. For example, for general consumer electronic products with relatively low operating voltages, under the premise of ensuring the insulation performance, the encapsulation thickness can be appropriately reduced to reduce the cost and volume.
Case Analysis and Data Support
I. Case of PCB Encapsulation in a Certain Communication Device
During the research and development of a certain communication device, the optimization research on the encapsulation thickness of the PCB was carried out. The power amplifier in this device is the main heat-generating component. Initially, an encapsulation thickness of 5mm was used. Although the insulation performance was good, after the device ran for a long time, the temperature of the power amplifier was too high, resulting in unstable signal transmission. Through thermal simulation analysis and actual testing, after reducing the encapsulation thickness to 2mm, the temperature of the power amplifier decreased significantly, and the heat dissipation performance was improved. At the same time, through the test of the insulation performance, it was found that it still could meet the insulation requirements of the device, ensuring the stable operation of the device.
II. Data Comparison Explanation
Through experimental tests, the data on the heat dissipation performance and electrical insulation performance of the PCB under different encapsulation thicknesses were obtained. In terms of heat dissipation performance, when the encapsulation thickness increased from 1mm to 5mm, the operating temperature of the electronic components increased by 15°C, and the thermal resistance increased by 0.5°C/W; in terms of electrical insulation performance, when the encapsulation thickness increased from 2mm to 4mm, the breakdown voltage increased by 500V. These data intuitively show the influence of the encapsulation thickness on the heat dissipation performance and electrical insulation performance of the PCB.
The encapsulation thickness has a significant influence on the heat dissipation performance and electrical insulation performance of the PCB. In the design and manufacturing process, it is necessary to fully consider the specific needs of the electronic device, comprehensively balance the two aspects of heat dissipation and insulation, and select an appropriate encapsulation thickness to ensure the stable and reliable performance of the PCB and improve the overall quality and service life of the electronic device. In the future, with the continuous development of electronic technology, the research on encapsulation materials and encapsulation processes will also continue to deepen, and it is expected to develop new encapsulation solutions that can not only meet the requirements of good heat dissipation but also ensure excellent insulation performance.
For more about influence of encapsulation thickness on the heat dissipation performance and electrical insulation performance of PCB, you can pay a visit to DeepMaterial at https://www.pottingcompound.com/ for more info.
Recent Posts
- Conformal Coating Spray
- UV Curing Potting Compound
- The Ultimate Guide to Electrical Potting Compound and Market Application
- The Top Polyurethane Potting Compound
- Advanced Epoxy Potting Compound for Superior Electronic Protection
- Waterproof Potting Compound: A Comprehensive Guide
- Silicone Potting Compound for Electronics
- Potting Compound vs. Epoxy: A Comprehensive Comparison
- Potting Compound for PCB
- In – depth Analysis of the Curing Characteristics of Electronic Potting Compounds
Tags
Related Posts
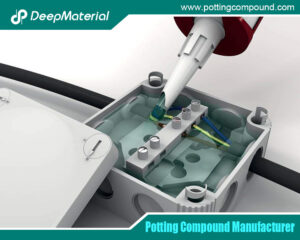
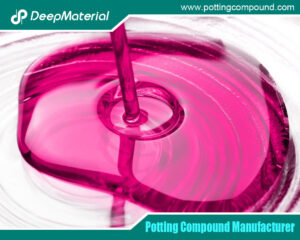
UV Curing Potting Compound
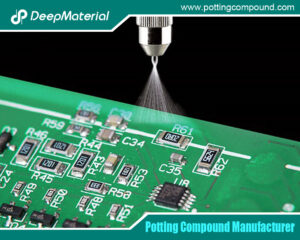
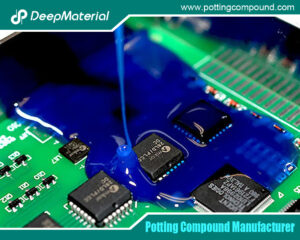
The Top Polyurethane Potting Compound
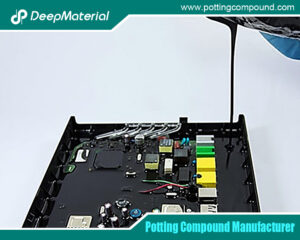
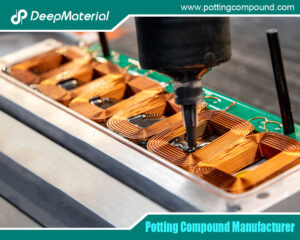